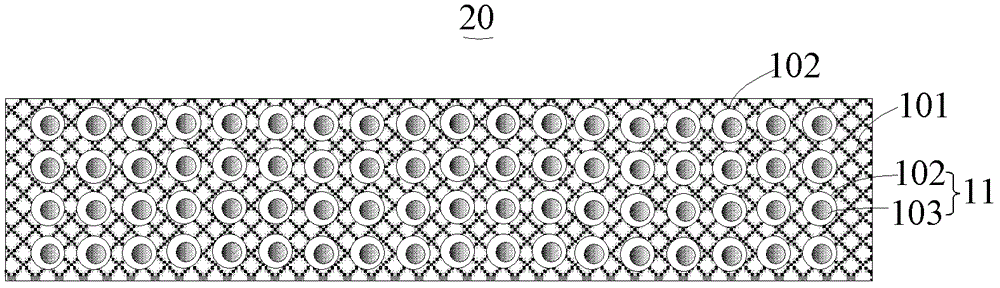
本發(fā)明涉及復(fù)合材料領(lǐng)域,尤其涉及一種基于復(fù)合材料的介質(zhì)基板及其制造方法。
背景技術(shù):在通訊系統(tǒng)中,電子元器件的尺寸逐步向著高功效、多功能及小尺寸方向發(fā)展,這對高頻材料的性能提出更高的需求?,F(xiàn)代電子信息產(chǎn)品特別是微波射頻器件的高速發(fā)展,集成度極大的提高及數(shù)字化、高頻化、多功能化等應(yīng)用要求已經(jīng)向一般的PTFE高頻板及制造工藝提出了挑戰(zhàn)。目前市場上的高頻材料主要有PTFE基板、熱固性PPO、交聯(lián)聚丁二烯基板和環(huán)氧樹脂復(fù)合基板。其介電常數(shù)、介電損耗及可加工性能三者匹配的需求已經(jīng)非常迫切。有機復(fù)合基板材料一般是將無機氧化物陶瓷顆粒均勻分散到有機高分子材料中來制造復(fù)合材料基板。無機氧化物具有較高的介電常數(shù),有機高分子材料具有很好的成型性和可加工性能,結(jié)合上述兩者的優(yōu)點,就可得到介電常數(shù)在較高范圍、同時可加工性能良好的復(fù)合材料。因選取的原材料的限制,現(xiàn)有的有機高分子-氧化物陶瓷復(fù)合材料不能獲得較高的介電常數(shù),介電損耗也較大。然而,常見的高介電有機高分子-氧化物陶瓷復(fù)合材料通常由環(huán)氧樹脂、酚醛樹脂、聚四氟乙烯等介電常數(shù)較低、損耗較大的高分子材料與介電常數(shù)較大、但損耗也較高的鐵電陶瓷顆粒組成。為了保證材料的可加工性,樹脂的含量不能太低,即是高介電常數(shù)的鐵電陶瓷的含量不能太高,這就導(dǎo)致復(fù)合材料的介電常數(shù)不高。同時,高分子材料組分和鐵電陶瓷材料組分的高損耗也會致使復(fù)合材料的較高的損耗。
技術(shù)實現(xiàn)要素:基于此,為了解決現(xiàn)有復(fù)合材料及基于復(fù)合材料介質(zhì)基板的介電常數(shù)不高而且損耗較高的技術(shù)問題,因此提供一種基于復(fù)合材料的介質(zhì)基板。同時,本發(fā)明還提供一種介質(zhì)基板的制造方法。一種基于復(fù)合材料的介質(zhì)基板包括第一導(dǎo)電箔和依附于所述第一導(dǎo)電箔上的復(fù)合材料,所述復(fù)合材料包括母體材料、高介電常數(shù)的金屬微粒及包裹所述高介電常數(shù)的金屬微粒的有機高分子材料;所述金屬微粒和有機高分子材料形成核殼結(jié)構(gòu),所述母體材料和有機高分子材料互不相溶;所述核殼結(jié)構(gòu)離散地分布嵌入在所述母體材料中,其中所述高介電常數(shù)的金屬微粒的粒徑在0.1um-2um之間。進一步地,所述母體材料為高分子材料,選用環(huán)氧樹脂、聚烯烴、聚丙烯酸酯類、聚硅氧烷類及其共聚物或共混物中的任意一種。進一步地,所述金屬微粒包括由單一金屬材料、金屬化合物或至少一種金屬材料的合金材料制得。進一步地,所述介電常數(shù)的金屬微粒表面上涂覆有活性劑,有機高分子材料通過化學(xué)鍵或氫鍵等吸附在表面活性劑上以形成所述核殼結(jié)構(gòu)。進一步地,所述有機高分子材料選用聚苯乙烯(PS)或者聚甲基丙烯酸甲酯(PMMA)中的任意一種。進一步地,所述介質(zhì)基板還包括第二導(dǎo)電箔;所述復(fù)合材料位于第一導(dǎo)電箔和第二導(dǎo)電箔之間,其中第一導(dǎo)電箔和第二導(dǎo)電箔選銅、銀或者金中的任意材料制得。一種介質(zhì)基板的制造方法包括如下步驟:b.將金屬微粒表面包裹有機高分子材料,形成核殼結(jié)構(gòu);c.將上述核殼結(jié)構(gòu)和母體材料溶液按照一定比例進行混合配制成粘度溶液;d.提供第一導(dǎo)電箔,將粘度溶液涂布在第一導(dǎo)電箔上;e.烘干和固化上述粘度溶液。進一步地,所述制造方法還包括如下步驟:g.將覆第一導(dǎo)電箔介質(zhì)基板與第二導(dǎo)電箔壓合。進一步地,所述制造方法b步驟還包括如下步驟:在高介電常數(shù)陶的金屬微粒表面上涂覆有活性劑將高介電常數(shù)的金屬微粒表面改性,然后有機高分子材料通過化學(xué)鍵或氫鍵等吸附在表面活性劑上。一種介質(zhì)基板的制造方法包括如下步驟:H.提供金屬微粒;I.將金屬微粒表面包裹有機高分子材料,形成核殼結(jié)構(gòu);J.將上述核殼結(jié)構(gòu)和母體材料溶液按照一定比例進行混合配制成粘度溶液;K.提供第一導(dǎo)電箔,將粘度溶液涂布在第一導(dǎo)電箔上;L.烘干和固化上述粘度溶液。進一步地,所述制造方法還包括如下步驟:M.將覆第一導(dǎo)電箔介質(zhì)基板與第二導(dǎo)電箔壓合。進一步地,所述制造方法I步驟還包括如下步驟:在高介電常數(shù)的金屬微粒表面上涂覆有活性劑將金屬微粒表面改性,然后有機高分子材料通過化學(xué)鍵或氫鍵等吸附在表面活性劑上。通過采用上述高介電常數(shù)、低損耗的復(fù)合材料加工工藝以及基于上述復(fù)合材料,且與相對單純陶瓷粉體加入到高分子母體材料中相比,本發(fā)明以高介電常數(shù)的金屬微粒為核、有機高分子膜為外殼的核殼結(jié)構(gòu),將上述核殼結(jié)構(gòu)和母體材料溶液按照一定比例進行混合配制成粘度溶液;然后烘干和固化所述粘度溶液使得所述核殼結(jié)構(gòu)無規(guī)則離散地分布嵌入在所述母體材料中,這樣形成的復(fù)合材料及基于復(fù)合材料的介質(zhì)基板的損耗可降低50%以上。制得介質(zhì)基板才滿足現(xiàn)有電子設(shè)備的需求。附圖說明圖1是本發(fā)明的高介電常數(shù)、低損耗復(fù)合材料一實施方式的示意圖;圖2是本發(fā)明的高介電常數(shù)、低損耗復(fù)合材料另一實施方式的示意圖;圖3為基于圖1所示復(fù)合材料加工成單面銅箔的介質(zhì)基板一實施方式的示意圖;圖4為基于圖1所示復(fù)合材料加工成雙面銅箔的介質(zhì)基板另一實施方式的示意圖;圖5為本復(fù)合材料中核殼結(jié)構(gòu)形成過程示意圖;圖6為本發(fā)明的高介電常數(shù)、低損耗復(fù)合材料的制造工藝流程圖;圖7為圖4所示介質(zhì)基板制造的一實施方式工藝流程圖;圖8為圖4所示介質(zhì)基板制造的另一實施方式工藝流程圖。具體實施方式現(xiàn)在詳細參考附圖中描述的實施例。為了全面理解本發(fā)明,在以下詳細描述中提到了眾多具體細節(jié)。但是本領(lǐng)域技術(shù)人員應(yīng)該理解,本發(fā)明可以無需這些具體細節(jié)而實現(xiàn)。在其他實施方式中,不詳細描述公知的方法。過程、組件和電路,以免不必要地使實施例模糊。請參考圖1,為本發(fā)明高介電常數(shù)、低損耗的復(fù)合材料一實施方式的示意圖。所述復(fù)合材料10包括母體材料101、高介電常數(shù)的金屬微粒103及包裹所述高介電常數(shù)的金屬微粒103的有機高分子材料102。所述高介電常數(shù)的金屬微粒103和有機高分子材料102形成核殼結(jié)構(gòu)11,所述核殼結(jié)構(gòu)11無規(guī)則離散地分布嵌入在所述母體材料101中。所述復(fù)合材料10在未烘干和固化之前為一定粘度的高分子溶液。在本發(fā)明中,所述金屬微粒103包括由單一金屬材料、金屬化合物或至少一種金屬材料的合金材料制得。所述單一金屬材料包括但不限于銅、鎳、錮、鉛、鋅、銻、汞、鎘、鋁、鎂、鈣、鉀、金、銀、銅、鍶、鋇和鉍。金屬化合物是指由至少一種金屬元素與其他任意元素發(fā)生相互化學(xué)作用而形成一種具有金屬特性的物質(zhì),如三氧化二鋁等。合金材料是指由至少一種金屬元素與其他任意元素混合而形成一種具有金屬特性的物質(zhì)。所述母體材料101為高分子材料,包括但不限于環(huán)氧樹脂、聚烯烴、聚丙烯酸酯類、聚硅氧烷類及其共聚物或共混物。在本實施方式中,通過采用高介電陶瓷材料磨制成所述高介電常數(shù)的金屬微粒103,每一高介電常數(shù)的金屬微粒103的粒徑在0.05um-4um之間,其中較優(yōu)選地高介電常數(shù)的金屬微粒103的粒徑0.1um-2um之間。請參閱圖5,為了使在高介電常數(shù)的金屬微粒103表面形成有機高分子材料102,首先在高介電常數(shù)的金屬微粒103表面上涂覆有活性劑104將高介電常數(shù)的金屬微粒103表面改性,然后有機高分子材料102通過化學(xué)鍵或氫鍵等吸附在表面活性劑104上。所述有機高分子材料102可以選用各種與母體材料101不相溶的有機高分子材料,在加工過程中,應(yīng)該根據(jù)不同工藝選擇不同相應(yīng)的材料。在本實施方式中,有機高分子材料102選用聚苯乙烯(PS)或者聚甲基丙烯酸甲酯(PMMA)。請參考圖2,是本發(fā)明的高介電常數(shù)、低損耗復(fù)合材料另一實施方式的示意圖。所述核殼結(jié)構(gòu)11離散且均勻地分布嵌入在所述母體材料101中。所述復(fù)合材料10在未烘干和固化之前為一定粘度的高分子溶液。請參考圖3,為基于所述復(fù)合材料加工成介質(zhì)基板一實施方式的示意圖。所述介質(zhì)基板8包括一導(dǎo)電箔13和依附于所述導(dǎo)電箔13上的復(fù)合材料10。在本實施方式中,所述導(dǎo)電箔13優(yōu)選銅箔。在其他實施方式中,所述導(dǎo)電箔13選擇銀箔或者金箔。在在本發(fā)明所述介質(zhì)基板8也稱之為層壓板,可以進一步應(yīng)用于天線基板、PCB板、覆銅基板、芯片載體件或類似應(yīng)用件。請參考圖4,為基于所述復(fù)合材料加工成介質(zhì)基板另一實施方式的示意圖。所述介質(zhì)基板8包括第一導(dǎo)電箔11、第二導(dǎo)電箔13和夾于所述第一導(dǎo)電箔11和第二導(dǎo)電箔13的復(fù)合材料10。在本實施方式中,所述第一導(dǎo)電箔11和第二導(dǎo)電箔13優(yōu)選銅箔。在其他實施方式中,所述第一導(dǎo)電箔11和第二導(dǎo)電箔13銀箔或金箔。下面介紹上述高介電常數(shù)、低損耗復(fù)合材料及基于高介電常數(shù)、低損耗復(fù)合材料技術(shù)制造介質(zhì)基板:請參閱圖6,為本發(fā)明的高介電常數(shù)、低損耗復(fù)合材料的制造工藝流程圖。所述復(fù)合材料加工流程如下:步驟21:將高介電常金屬加工成金屬微粒。在該步驟中,通過將高介電金屬磨制成所述高介電常數(shù)的金屬微粒,每一高介電常數(shù)的金屬微粒的粒徑在0.05um-4um之間,其中較優(yōu)選地高介電常數(shù)的金屬微粒的粒徑0.1um-2um之間。在本發(fā)明中,所述金屬微粒103包括由單一金屬材料、金屬化合物或至少一種金屬材料的合金材料制得。所述單一金屬材料包括但不限于銅、鎳、錮、鉛、鋅、銻、汞、鎘、鋁、鎂、鈣、鉀、金、銀、銅、鍶、鋇和鉍。金屬化合物是指由至少一種金屬元素與其他任意元素發(fā)生相互化學(xué)作用而形成一種具有金屬特性的物質(zhì),如三氧化二鋁等。合金材料是指由至少一種金屬元素與其他任意元素混合而形成一種具有金屬特性的物質(zhì)。步驟23:將金屬微粒表面包裹有機高分子材料,形成核殼結(jié)構(gòu)。在本實施方式中,首先在高介電常數(shù)陶的金屬微粒表面上涂覆有活性劑將高介電常數(shù)的金屬微粒表面改性,然后有機高分子材料通過化學(xué)鍵或氫鍵等吸附在表面活性劑上以形成核殼結(jié)構(gòu)。步驟25:將上述核殼結(jié)構(gòu)和母體材料溶液按照一定比例進行混合配制成粘度溶液。核殼結(jié)構(gòu)和母體材料溶液按照比例進行混合并進行攪拌均勻,使之成為粘度的液體。在本實施方式中,所述母體材料為高分子材料,包括但不限于環(huán)氧樹脂、聚烯烴、聚丙烯酸酯類、聚硅氧烷類及其共聚物或共混物,且在未通過烘干或固化手段,所述母體材料液體狀態(tài)。步驟27:烘干和固化上述粘度溶液形成本發(fā)明的高介電常數(shù)、低損耗的復(fù)合材料。在本實施方式中,在烘干、固化過程的溫度控制50~100℃之間;而其烘干、固化采用業(yè)界常用方法及設(shè)備。請參閱圖8,為本發(fā)明介質(zhì)基板制造的一實施方式工藝流程圖。所述介質(zhì)基板加工流程如下:步驟31:將高介電常金屬加工成金屬微粒。在該步驟中,通過將高介電金屬磨制成所述高介電常數(shù)的金屬微粒,每一高介電常數(shù)的金屬微粒的粒徑在0.05um-4um之間,其中較優(yōu)選地高介電常數(shù)的金屬微粒的粒徑0.1um-2um之間。其中在本發(fā)明中,所述金屬微粒103包括由單一金屬材料、金屬化合物或至少一種金屬材料的合金材料制得。所述單一金屬材料包括但不限于銅、鎳、錮、鉛、鋅、銻、汞、鎘、鋁、鎂、鈣、鉀、金、銀、銅、鍶、鋇和鉍。金屬化合物是指由至少一種金屬元素與其他任意元素發(fā)生相互化學(xué)作用而形成一種具有金屬特性的物質(zhì),如三氧化二鋁等。合金材料是指由至少一種金屬元素與其他任意元素混合而形成一種具有金屬特性的物質(zhì)。步驟33:將金屬微粒表面包裹有機高分子材料,形成核殼結(jié)構(gòu)。在本實施方式中,首先在高介電常數(shù)陶的金屬微粒表面上涂覆有活性劑將高介電常數(shù)的金屬微粒表面改性,然后有機高分子材料通過化學(xué)鍵或氫鍵等吸附在表面活性劑上以形成核殼結(jié)構(gòu)。步驟35:將上述核殼結(jié)構(gòu)和母體材料溶液按照一定比例進行混合配制成粘度溶液。核殼結(jié)構(gòu)和母體材料溶液按照比例進行混合并進行攪拌均勻,使之成為粘度溶液。在本實施方式中,所述母體材料為高分子材料,包括但不限于環(huán)氧樹脂、聚烯烴、聚丙烯酸酯類、聚硅氧烷類及其共聚物或共混物,且在未通過烘干或固化手段,所述母體材料液體狀態(tài)。步驟37:提供第一導(dǎo)電箔,將粘度溶液涂布在第一導(dǎo)電箔上。在本實施方式中,所述第一導(dǎo)電箔11選銅箔,然后業(yè)界常用溶液涂布方法及設(shè)備將粘度溶液涂布在銅箔一表面上。在其他實施方式中,所述第一導(dǎo)電箔11可選用銀箔或金箔。步驟38:烘干和固化上述粘度溶液形成單面覆導(dǎo)電箔介質(zhì)基板。在本實施方式中,在烘干、固化過程的溫度控制50~100℃之間;而其烘干、固化采用業(yè)界常用方法及設(shè)備。步驟39:將覆第一導(dǎo)電箔介質(zhì)基板與第二導(dǎo)電箔壓合,形成雙面覆導(dǎo)電箔的介質(zhì)基板。所述第一導(dǎo)電箔介質(zhì)基板指將第一導(dǎo)電箔上復(fù)合材料烘干和固化形成單面覆導(dǎo)電箔介質(zhì)基板。請參閱圖8,為本發(fā)明介質(zhì)基板制造的另一實施方式工藝流程圖。所述介質(zhì)基板加工流程如下:步驟41:將高介電常金屬加工成金屬微粒。在該步驟中,通過將高介電金屬磨制成所述高介電常數(shù)的金屬微粒,每一高介電常數(shù)的金屬微粒的粒徑在0.05um-4um之間,其中較優(yōu)選地高介電常數(shù)的金屬微粒的粒徑0.1um-2um之間。在本發(fā)明中,所述金屬微粒103包括由單一金屬材料、金屬化合物或至少一種金屬材料的合金材料制得。所述單一金屬材料包括但不限于銅、鎳、錮、鉛、鋅、銻、汞、鎘、鋁、鎂、鈣、鉀、金、銀、銅、鍶、鋇和鉍。金屬化合物是指由至少一種金屬元素與其他任意元素發(fā)生相互化學(xué)作用而形成一種具有金屬特性的物質(zhì),如三氧化二鋁等。合金材料是指由至少一種金屬元素與其他任意元素混合而形成一種具有金屬特性的物質(zhì)。步驟43:將金屬微粒表面包裹有機高分子材料,形成核殼結(jié)構(gòu)。在本實施方式中,首先在高介電常數(shù)陶的金屬微粒表面上涂覆有活性劑將高介電常數(shù)的金屬微粒表面改性,然后有機高分子材料通過化學(xué)鍵或氫鍵等吸附在表面活性劑上以形成核殼結(jié)構(gòu)。步驟45:將上述核殼結(jié)構(gòu)和母體材料溶液按照一定比例進行混合配制成粘度溶液。核殼結(jié)構(gòu)和母體材料溶液按照比例進行混合并進行攪拌均勻,使之成為粘度溶液。在本實施方式中,所述母體材料為高分子材料,包括但不限于環(huán)氧樹脂、聚烯烴、聚丙烯酸酯類、聚硅氧烷類及其共聚物或共混物,且在未通過烘干或固化手段,所述母體材料液體狀態(tài)。步驟47:提供第一導(dǎo)電箔,將粘度溶液涂布在第一導(dǎo)電箔上。在本實施方式中,所述第一導(dǎo)電箔11選銅箔,然后業(yè)界常用溶液涂布方法及設(shè)備將粘度溶液涂布在銅箔一表面上。在其他實施方式中,所述第一導(dǎo)電箔11可選用銀箔或金箔。步驟48:烘干和固化上述粘度溶液形成單面覆導(dǎo)電箔介質(zhì)基板。在本實施方式中,在烘干、固化過程的溫度控制50~100℃之間;而其烘干、固化采用業(yè)界常用方法及設(shè)備。步驟49:將覆第一導(dǎo)電箔介質(zhì)基板與第二導(dǎo)電箔壓合,形成雙面覆導(dǎo)電箔的介質(zhì)基板。所述覆第一導(dǎo)電箔介質(zhì)基板指將第一導(dǎo)電箔上復(fù)合材料烘干和固化形成單面覆導(dǎo)電箔介質(zhì)基板。雙面覆導(dǎo)電箔的介質(zhì)基板是指將所述覆第一導(dǎo)電箔介質(zhì)基板與第二導(dǎo)電箔壓合形成雙面覆導(dǎo)電箔的介質(zhì)基板。通過采用上述高介電常數(shù)、低損耗的復(fù)合材料加工工藝以及基于上述復(fù)合材料,且與相對單純陶瓷粉體加入到高分子母體材料中相比,本發(fā)明以高介電常數(shù)的金屬微粒為核、有機高分子膜為外殼的核殼結(jié)構(gòu),將上述核殼結(jié)構(gòu)和母體材料溶液按照一定比例進行混合配制成粘度溶液;然后烘干和固化所述粘度溶液使得所述核殼結(jié)構(gòu)無規(guī)則離散地分布嵌入在所述母體材料中,這樣形成的復(fù)合材料及基于復(fù)合材料的介質(zhì)基板的損耗可降低50%以上。制得介質(zhì)基板才滿足現(xiàn)有電子設(shè)備的需求。上面結(jié)合附圖對本發(fā)明的實施例進行了描述,但是本發(fā)明并不局限于上述的具體實施方式,上述的具體實施方式僅僅是示意性的,而不是限制性的,本領(lǐng)域的普通技術(shù)人員在本發(fā)明的啟示下,在不脫離本發(fā)明宗旨和權(quán)利要求所保護的范圍情況下,還可做出很多形式,這些均屬于本發(fā)明的保護之內(nèi)。