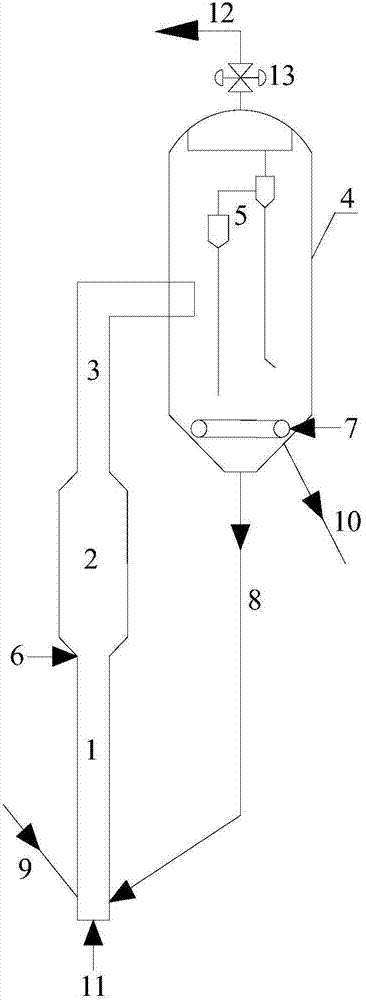
本發(fā)明涉及一種結(jié)焦催化劑的再生方法和系統(tǒng)。
背景技術(shù):
:重質(zhì)油催化裂化反應(yīng)生成液化氣和汽油等富氫組分的同時(shí),還生成一部分氫含量相對(duì)低的焦炭。焦炭沉積在催化劑上使催化劑的活性和選擇性大幅度下降。采用高溫氧化再生方法,將催化劑上的焦炭通過(guò)燃燒的方法除掉,以恢復(fù)催化劑的活性和選擇性,這一過(guò)程稱為催化劑的再生。常規(guī)催化劑再生方法是在鼓泡流化床或湍動(dòng)流化床內(nèi)通入空氣并采用單段再生方式進(jìn)行再生,在這種低線速、氣固全返混的流化床內(nèi),氣體和固體接觸效率低,催化劑再生速度慢,從而導(dǎo)致再生器催化劑藏量過(guò)大,燒焦強(qiáng)度低,約為100kg(焦炭量)/[h(單位時(shí)間)·t(催化劑藏量)],催化劑的再生效果差,進(jìn)入反應(yīng)器的再生催化劑含碳量為0.2重%。單段再生的另一個(gè)缺點(diǎn)是再生器的設(shè)備直徑很大,設(shè)備的固定投資較大。隨著分子篩催化劑在催化裂化裝置上廣泛的使用,尤其是usy型分子篩催化劑的使用,再生催化劑上的殘余的碳含量和再生方式對(duì)恢復(fù)催化劑的活性及選擇性影響很大。因此,有效降低再生過(guò)程中催化劑藏量和改善催化劑再生效果成為催化劑再生技術(shù)開(kāi)發(fā)的方向。從上世紀(jì)七十年代以來(lái),國(guó)內(nèi)外各種強(qiáng)化再生技術(shù)不斷發(fā)展,其中一方面是在工藝上采用高溫、高氣速?gòu)?qiáng)化燒焦技術(shù),如燒焦罐式再生器;另一方面是改善傳統(tǒng)催化劑全混型流化床再生器,如兩段再生器等。這些再生器的燒焦強(qiáng)度比常規(guī)單段再生器高1-2倍,但其結(jié)構(gòu)和操作都比較復(fù)雜。為了進(jìn)一步提高燒焦強(qiáng)度,簡(jiǎn)化設(shè)備結(jié)構(gòu)和操作,適應(yīng)重油催化裂化技術(shù)的發(fā)展, 國(guó)外開(kāi)發(fā)了全管道燒焦技術(shù),即提升管再生技術(shù)。中國(guó)專利cn1210762a公開(kāi)了一種分子篩催化劑高效再生工藝技術(shù),主要包括:待生催化劑在第一根再生管再生后進(jìn)入外置旋風(fēng)分離器組,經(jīng)料腿進(jìn)入第二根再生管;從第二根再生管外置旋風(fēng)分離器組料腿直接進(jìn)入外取熱器,經(jīng)底部再斜管進(jìn)入提升管反應(yīng)器。燒焦時(shí)間在10秒以下,燒焦強(qiáng)度是現(xiàn)有技術(shù)的10倍左右。但該工藝過(guò)程中分子篩催化劑再生操作條件非??量?,不利于催化劑活性或選擇性的恢復(fù)。中國(guó)專利cn2169473y公開(kāi)了一種催化裂化提升管燒焦再生器,技術(shù)特點(diǎn)在于提升管再生器上設(shè)有多段空氣進(jìn)氣口進(jìn)行待生催化劑再生,強(qiáng)化了待生催化劑的燒焦再生過(guò)程,其結(jié)構(gòu)簡(jiǎn)單,操作方便。美國(guó)專利usp4514285公開(kāi)了一種下行管和稀相提升管再生的催化裂化反應(yīng)系統(tǒng)。催化劑通過(guò)稀相提升管再生后,在再生脫氣罐中脫除煙氣、提高催化劑密度并形成催化劑密相床層后,通過(guò)催化劑分布板進(jìn)入下行反應(yīng)管,原料油通過(guò)進(jìn)料分配環(huán)管經(jīng)多條管徑噴入下行反應(yīng)器,與自由下落過(guò)程中的催化劑接觸并進(jìn)行催化裂化反應(yīng)。這種下行管反應(yīng)器由于原料油和催化劑初始接觸時(shí)催化劑的密度較低,油劑接觸效率不理想,因而原料轉(zhuǎn)化率較低。中國(guó)專利cn2205827y公開(kāi)了一種兩段串聯(lián)提升管燒焦再生器,兩段提升管再生器可在不同溫度下操作,并分別引入燒焦用空氣。失活催化劑先在第一段提升管再生器中脫去全部碳?xì)浠衔锖筒糠址e碳,再進(jìn)入第二段提升管再生器,進(jìn)一步降低催化劑的殘?zhí)己?。兩段再生器可以分別進(jìn)入空氣,控制不同操作氣速與溫度,避免單一管道燒焦時(shí)操作彈性小的缺點(diǎn)。全部再生用空氣一次性進(jìn)入時(shí),入口氣速過(guò)高,大量冷空氣引入,可能將因入口溫度降低導(dǎo)致“熄火”現(xiàn)象,若引入空氣量減少,降低入口氣速,則將因供氧不足導(dǎo)致燒焦反應(yīng)不完全。采用兩段串聯(lián)提升管燒焦再生,可以大幅度提高第二段再生器的操作溫度,提高燒焦強(qiáng)度且無(wú)水熱失活現(xiàn)象之慮。高速流化系統(tǒng)的返混程度比密相流化床中少得多。在提升管再生器中,可用比密相流化床中少的空氣將催化劑上的積碳燒至較低水平。事實(shí)上,密相流化床燒焦反應(yīng)程度僅為理論焦炭燃燒程度的大約10%,而提升管再生器可達(dá)到近100%。這種高效率正是提升管再生器進(jìn)行成功操作所要求的。綜上所述,不管是密相流化床再生器,燒焦罐式再生器,還是提升管式再生器,無(wú)不例外的采用空氣或多段空氣作為再生氣體,造成燒焦效率有限、焦炭起燃困難等結(jié)果。從催化裂化再生技術(shù)的發(fā)展來(lái)看,一直追求實(shí)現(xiàn)再生催化劑活性的最大程度恢復(fù),以實(shí)現(xiàn)烴類的最大轉(zhuǎn)化能力。但催化劑的活性是一個(gè)宏觀的轉(zhuǎn)化率的概念表述,并沒(méi)有體現(xiàn)目的產(chǎn)品選擇性的追求。譬如,再生時(shí)可以實(shí)現(xiàn)再生催化劑活性恢復(fù)最高,但該再生催化劑在參與反應(yīng)時(shí)可能由于其高活性而導(dǎo)致高的焦炭和干氣產(chǎn)率,這是不希望看到的。因此再生時(shí)需要追求催化劑活性恢復(fù)的一種均勻性,或者說(shuō)實(shí)現(xiàn)再生催化劑上酸性的一種均勻分布,從而實(shí)現(xiàn)低的焦炭和干氣產(chǎn)率、高的目的產(chǎn)品選擇性。因此,有必要開(kāi)發(fā)一種結(jié)焦催化劑的快速再生方法。技術(shù)實(shí)現(xiàn)要素:本發(fā)明的目的是提供一種結(jié)焦催化劑的再生方法和系統(tǒng),利用該系統(tǒng)的方法能夠大幅度提高燒焦效率,提高再生催化劑的催化裂化選擇性,并能夠在相同燒焦催化劑處理量下,減少再生器尺寸。為了實(shí)現(xiàn)上述目的,本發(fā)明提供一種結(jié)焦催化劑的再生方法,該方法包括:將結(jié)焦催化劑從提升管再生器底部送入提升管再生器中,并由下至上交替地與至少一股富氧氣體和至少一股含氧氣體接觸并進(jìn)行再生,得到再生催化劑;其中,所述提升管再生器設(shè)置有至少一段包括細(xì)管段和粗管段的再生段,且所述再生段中粗管段位于所述細(xì)管段的上方,所述富氧氣體從細(xì)管段 的下部送入所述提升管再生器中,所述含氧氣體從粗管段的下部送入所述提升管再生器中;所述富氧氣體的氧氣體積含量大于21體%,所述含氧氣體為選自氧氣、空氣和煙氣中的至少一種。優(yōu)選地,所述富氧氣體的氧氣含量在31體%以上。優(yōu)選地,所述富氧氣體為純氧。優(yōu)選地,所述再生的條件包括:再生溫度為450-700℃,再生時(shí)間為5-15秒,耗風(fēng)指標(biāo)為1-4nm3/千克焦炭,所述再生催化劑的碳含量為0-10重%。優(yōu)選地,該方法還包括:將所述結(jié)焦催化劑與至少部分所述再生催化劑混合后再進(jìn)行所述再生,和/或?qū)⑺鼋Y(jié)焦催化劑與至少部分所述再生催化劑換熱后再進(jìn)行所述再生。優(yōu)選地,所述結(jié)焦催化劑與所述再生催化劑的混合質(zhì)量比為1:(1-5)。優(yōu)選地,所述結(jié)焦催化劑中的催化劑為微球催化劑,所述微球催化劑為催化裂化催化劑、吸附脫硫催化劑、脫氫催化劑、甲醇制烯烴催化劑或甲醇制汽油催化劑。優(yōu)選地,將結(jié)焦催化劑依次與一股富氧氣體和一股含氧氣體接觸并進(jìn)行再生,得到再生催化劑;其中,所述提升管再生器設(shè)置有一段再生段。本發(fā)明還提供一種結(jié)焦催化劑的再生系統(tǒng),其中,該再生系統(tǒng)包括提升管再生器,所述提升管再生器設(shè)置有至少一段包括細(xì)管段和粗管段的再生段,且所述再生段中粗管段位于所述細(xì)管段的上方,所述細(xì)管段的下部設(shè)置有富氧氣體入口,所述粗管段的下部設(shè)置有含氧氣體入口,所述提升管再生器的底部設(shè)置有結(jié)焦催化劑入口,所述提升管再生器的頂部設(shè)置有再生催化劑出口。優(yōu)選地,所述粗管段與所述細(xì)管段的內(nèi)徑之比為(1.2-5):1,長(zhǎng)度之比為(0.5-2):1。優(yōu)選地,所述再生段設(shè)置為一段,所述提升管再生器還包括位于所述再 生段下方的預(yù)提升段和位于所述再生段上方的出口段,所述預(yù)提升段的高度占提升管再生器高度的5-20%,所述細(xì)管段的高度占提升管再生器高度的10-30%,所述粗管段的高度占提升管再生器高度的30-60%,所述出口段的高度占提升管再生器高度的大于零至20%。優(yōu)選地,所述再生系統(tǒng)還包括位于所述提升管再生器上方且與所述提升管再生器的再生催化劑出口連通的密相床緩沖器。優(yōu)選地,所述密相床緩沖器設(shè)置有換熱催化劑出口;所述換熱催化劑出口與所述提升管再生器的結(jié)焦催化劑入口直接連通,或與用于使再生催化劑和結(jié)焦催化劑換熱的換熱器連通。優(yōu)選地,所述密相床緩沖器內(nèi)設(shè)置有氣固分離裝置,所述氣固分離裝置為選自偏流彈道式分離器、臥式旋風(fēng)分離器、立式旋風(fēng)分離器、金屬燒結(jié)過(guò)濾器、回流分離器和彎管分離器中的至少一種。與現(xiàn)有的再生方法和系統(tǒng)相比,本發(fā)明的主要優(yōu)點(diǎn)在于:1、本發(fā)明方法很好地解決了提升管再生器中結(jié)焦催化劑燒焦起燃難的問(wèn)題,可以使結(jié)焦催化劑快速再生,再生催化劑活性分布更均勻,從而降低催化裂化副產(chǎn)物焦炭和干氣產(chǎn)率;2、本發(fā)明方法可以大幅度降低裝置催化劑藏量尤其是再生器的藏量,大大減小靜設(shè)備和動(dòng)設(shè)備的尺寸,減少投資,減少占地面積;3、由于再生系統(tǒng)中氧氣濃度高,從而使燒焦效率大幅度提高,再生時(shí)間縮短,減少催化劑的破碎、磨損,提高了催化劑的使用壽命和效率;4、本發(fā)明方法將富氧氣體和含氧氣體分別從提升管再生器的不同位置送入提升管再生器中,一方面可以方便結(jié)焦催化劑的起燃,另一方面可以節(jié)約富氧氣體,并且還可以利用粗管段和細(xì)管段對(duì)燒焦再生的溫度、壓力和線速等進(jìn)行穩(wěn)定控制。本發(fā)明的其他特征和優(yōu)點(diǎn)將在隨后的具體實(shí)施方式部分予以詳細(xì)說(shuō)明。附圖說(shuō)明附圖是用來(lái)提供對(duì)本發(fā)明的進(jìn)一步理解,并且構(gòu)成說(shuō)明書(shū)的一部分,與下面的具體實(shí)施方式一起用于解釋本發(fā)明,但并不構(gòu)成對(duì)本發(fā)明的限制。在附圖中:圖1是本發(fā)明方法的一種具體實(shí)施方式的流程示意圖,也是本發(fā)明系統(tǒng)的一種具體實(shí)施方式的結(jié)構(gòu)示意圖;圖2是本發(fā)明方法的另一種具體實(shí)施方式的流程示意圖,也是本發(fā)明系統(tǒng)的另一種具體實(shí)施方式的結(jié)構(gòu)示意圖。附圖標(biāo)記說(shuō)明1細(xì)管段2粗管段3出口段4密相床緩沖器5氣固分離裝置6管線7管線8管線9管線10管線11管線12管線13雙動(dòng)滑閥具體實(shí)施方式以下結(jié)合附圖對(duì)本發(fā)明的具體實(shí)施方式進(jìn)行詳細(xì)說(shuō)明。應(yīng)當(dāng)理解的是,此處所描述的具體實(shí)施方式僅用于說(shuō)明和解釋本發(fā)明,并不用于限制本發(fā)明。本發(fā)明提供一種結(jié)焦催化劑的再生方法,該方法包括:將結(jié)焦催化劑從提升管再生器底部送入提升管再生器中,并由下至上交替地與至少一股富氧氣體和至少一股含氧氣體接觸并進(jìn)行再生,得到再生催化劑;其中,所述提升管再生器設(shè)置有至少一段包括細(xì)管段和粗管段的再生段,且所述再生段中粗管段位于所述細(xì)管段的上方,所述富氧氣體從細(xì)管段的下部送入所述提升 管再生器中,所述含氧氣體從粗管段的下部送入所述提升管再生器中;所述富氧氣體的氧氣體積含量大于21體%,優(yōu)選在31體%以上,更優(yōu)選為純氧,所述含氧氣體為選自氧氣、空氣和煙氣中的至少一種。發(fā)明人通過(guò)試驗(yàn)得出,在結(jié)焦催化劑燒焦再生過(guò)程中,再生氣氛中氧氣體積分?jǐn)?shù)越高,結(jié)焦催化劑上的焦炭劇烈燃燒點(diǎn)越低。因此,在保證不損壞催化劑基質(zhì)和活性組分結(jié)構(gòu)的前提下,可以盡量使用氧氣體積分?jǐn)?shù)較高的再生氣氛,進(jìn)行結(jié)焦催化劑的燒焦反應(yīng),甚至可以是純氧,即100%氧氣。根據(jù)本發(fā)明,所述富氧氣體可以是主要成分為氧氣和二氧化碳的再生氣體,也可以包括其它成分;所述的純氧是指100體%的氧氣,可以含有不可避免的雜質(zhì);所述含氧氣體的氧氣含量一般小于富氧氣體,如有需要氧氣含量也可以大于或等于富氧氣體,例如,均為純氧。根據(jù)本發(fā)明,再生是本領(lǐng)域技術(shù)人員所熟知的,本發(fā)明不再贅述,所述再生的條件可以包括:再生溫度可以為450-700℃,優(yōu)選為550-680℃,再生時(shí)間可以為5-15秒,優(yōu)選為6-12秒,耗風(fēng)指標(biāo)可以為1-4nm3/千克焦炭,優(yōu)選為2-4nm3/千克焦炭,所述再生催化劑的碳含量可以為0-10重%,優(yōu)選為0.4-1.0重%,例如碳含量可以低于0.2重%,也可以高于1重%,只要能夠滿足后續(xù)反應(yīng)需求而不影響反應(yīng)的活性和選擇性即可。其中所述的耗風(fēng)指標(biāo)包括所有再生氣體,即既包括含氧氣體也包括富氧氣體,也可以包括通入再生器中用于再生的其它氣體。含氧氣體與富氧氣體的體積之比本發(fā)明并沒(méi)有限制,只要能夠使結(jié)焦催化劑恢復(fù)活性、控制再生溫度以及催化劑的線速等即可。根據(jù)本發(fā)明,由于提升管再生器的線速較高,一般為2-20米/秒,因此可以在提升管再生器出口處設(shè)置密相床緩沖器對(duì)再生催化劑進(jìn)行緩沖處理,一方面可以將提升管再生器出來(lái)的再生催化劑的線速降低,方便后面輸送,另一方面,還可以繼續(xù)在密相床緩沖器中通入再生氣體進(jìn)行進(jìn)一步地再生。 因此,密相床緩沖器中緩沖處理的條件可以為:緩沖流化氣體可以為選自惰性氣體、水蒸氣、氧氣、空氣和煙氣中的至少一種,緩沖處理的時(shí)間可以為10-600秒,緩沖器的溫度可以根據(jù)實(shí)際需要進(jìn)行控制,例如可以采用取熱介質(zhì)進(jìn)行取熱。根據(jù)本發(fā)明,為了提高結(jié)焦催化劑的溫度,方便結(jié)焦催化劑的起燃,該方法還可以包括:將所述結(jié)焦催化劑與至少部分所述再生催化劑混合后再進(jìn)行所述再生,和/或?qū)⑺鼋Y(jié)焦催化劑與至少部分所述再生催化劑換熱后再進(jìn)行所述再生,其中,所述結(jié)焦催化劑與所述再生催化劑的混合質(zhì)量比可以為1:(1-5)。本發(fā)明的方法可以適用于多種結(jié)焦催化劑進(jìn)行再生,一般來(lái)說(shuō),所述結(jié)焦催化劑中的催化劑為微球催化劑,所述微球催化劑可以為催化裂化催化劑、吸附脫硫催化劑、脫氫催化劑、甲醇制烯烴催化劑或甲醇制汽油催化劑。本發(fā)明的一種優(yōu)選具體實(shí)施方式,將結(jié)焦催化劑依次與一股富氧氣體和一股含氧氣體接觸并進(jìn)行再生,得到再生催化劑;其中,所述提升管再生器設(shè)置有一段再生段,在細(xì)管段內(nèi)形成第一再生區(qū),在粗管段內(nèi)形成第二再生區(qū)。本發(fā)明還提供一種結(jié)焦催化劑的再生系統(tǒng),其中,該再生系統(tǒng)包括提升管再生器,所述提升管再生器設(shè)置有至少一段包括細(xì)管段和粗管段的再生段,且所述再生段中粗管段位于所述細(xì)管段的上方,所述細(xì)管段的下部設(shè)置有富氧氣體入口,所述粗管段的下部設(shè)置有含氧氣體入口,所述提升管再生器的底部設(shè)置有結(jié)焦催化劑入口,所述提升管再生器的頂部設(shè)置有再生催化劑出口。根據(jù)本發(fā)明,所述富氧氣體入口和含氧氣體入口可以采用徑向或切向結(jié)構(gòu)與提升管再生器本體連接,優(yōu)選采用切向結(jié)構(gòu);采用切向結(jié)構(gòu)時(shí)氣體入口氣速一般控制在10~20米/秒左右,切向引入氣體,可以使提升管再生器內(nèi) 氣固兩相處于旋流狀態(tài),有利于燒焦反應(yīng)的進(jìn)行。根據(jù)本發(fā)明,設(shè)置粗管段和細(xì)管段是為了控制再生時(shí)提升管再生器的溫度、壓力和線速等,本發(fā)明所述粗管段與所述細(xì)管段的內(nèi)徑之比可以為(1.2-5):1,優(yōu)選為(2-4):1,長(zhǎng)度之比為(0.5-2):1,本領(lǐng)域技術(shù)人員也可以根據(jù)實(shí)際情況進(jìn)行設(shè)置。一種具體實(shí)施方式,所述再生段設(shè)置為一段,所述提升管再生器還包括位于所述再生段下方的預(yù)提升段和位于所述再生段上方的出口段,所述出口段內(nèi)設(shè)置有出口區(qū),所述預(yù)提升段的高度占提升管再生器高度的5-20%,所述細(xì)管段的高度占提升管再生器高度的10-30%,所述粗管段的高度占提升管再生器高度的30-60%,所述出口段的高度占提升管再生器高度的大于零至20%。所述預(yù)提升段、粗管段、細(xì)管段和出口段的總高度可以為15-60米,預(yù)提升段的內(nèi)徑可以為0.2-5米,出口段內(nèi)徑與細(xì)管段的內(nèi)徑之比可以為(0.8-1.5):1,所述提升管再生器可以與所述預(yù)提升段和/或出口段同軸(如圖1所示),也可以不同軸(如圖2所示),所述粗管段和細(xì)管段結(jié)合部位可以為圓臺(tái),該圓臺(tái)縱剖面等腰梯形的頂角可以為30~80°,粗管段與出口段結(jié)合部位也可以為圓臺(tái),該圓臺(tái)縱剖面等腰梯形的底角可以為45~85°。根據(jù)本發(fā)明,所述再生系統(tǒng)還可以包括位于所述提升管再生器上方且與所述提升管再生器的再生催化劑出口連通的密相床緩沖器,密相床緩沖器一方面可以用于降低再生催化劑的線速,使再生催化劑容易通過(guò)管線進(jìn)入反應(yīng)器中用于反應(yīng),另一方面,密相床緩沖器內(nèi)可以設(shè)置有氣固分離裝置,使再生煙氣和再生催化劑分離,氣固分離裝置是本領(lǐng)域技術(shù)人員熟知的,例如,可以為選自偏流彈道式分離器、臥式旋風(fēng)分離器、立式旋風(fēng)分離器、金屬燒結(jié)過(guò)濾器、回流分離器和彎管分離器中的至少一種。由于待生的結(jié)焦催化劑的溫度較低,要在一般的再生時(shí)間(2~15秒)內(nèi)在提升管再生器中燒去結(jié)焦催化劑上的炭是比較困難的。因此,一種具體 實(shí)施方式,密相床緩沖器可以設(shè)置有換熱催化劑出口;所述換熱催化劑出口可以與所述提升管再生器的結(jié)焦催化劑入口直接連通,或可以與用于使再生催化劑和結(jié)焦催化劑換熱的換熱器連通,例如,可以采用一個(gè)熱的再循環(huán)閥,使從密相床緩沖器引出的熱催化劑循環(huán)回到再生器底部。一般,通過(guò)此再循環(huán)閥的催化劑質(zhì)量與通過(guò)控制提升管再生器結(jié)焦催化劑送入量的待生滑閥的催化劑質(zhì)量之比至少為1:1,最好大于2:1,以便使提升管再生器中的溫度提高到足以完全再生,可以想象的是,與結(jié)焦催化劑一起進(jìn)入提升管再生器的可以是結(jié)焦催化劑和再生催化劑的混合催化劑。另一種實(shí)施方式,結(jié)焦催化劑進(jìn)入提升管再生器之前,先在一定容量的容器或管道里與顆粒溫度遠(yuǎn)高于結(jié)焦催化劑的再生催化劑直接換熱或間接換熱,以使結(jié)焦催化劑的顆粒溫度升高至550℃以上,最好能達(dá)到580℃以上;然后將結(jié)焦催化劑再流入提升管再生器與富氧氣體接觸,進(jìn)行燒焦再生。一種進(jìn)一步的具體實(shí)施方式,可以將一定量的新鮮催化劑引入上述容器或管道里,與任意碳含量的催化劑混合換熱或老化后,再進(jìn)入提升管再生器燒焦再生。下面將通過(guò)具體實(shí)施方式來(lái)進(jìn)一步說(shuō)明本發(fā)明,但是本發(fā)明并不因此而受到任何限制。如圖1或圖2所示,結(jié)焦催化劑經(jīng)過(guò)管線9(待生斜管)進(jìn)入非等徑提升管再生器底部,將富氧氣體由管線11通入非等徑提升管再生器底部與結(jié)焦催化劑接觸并在細(xì)管段1內(nèi)的第一再生區(qū)中燒焦再生,再生生成的煙氣和含碳量降低的不完全再生催化劑上行,在粗管段2內(nèi)的第二再生區(qū)中與從管線6通入的含氧氣體繼續(xù)反應(yīng),得到的適合再次反應(yīng)的再生催化劑和煙氣通過(guò)出口段3,經(jīng)氣固分離裝置5進(jìn)行氣固分離,再生催化劑進(jìn)入密相床緩沖器4,從管線7通入含氧氣體至密相床緩沖器4底部,煙氣經(jīng)過(guò)雙動(dòng)滑閥13和管線12進(jìn)入后續(xù)處理系統(tǒng);密相床緩沖器4中的再生催化劑分為兩部分,一部分通過(guò)管線8返回非等徑提升管再生器的底部與結(jié)焦催化劑混合,另一 部分經(jīng)管線10返回反應(yīng)器與預(yù)提升介質(zhì)接觸并與原料油反應(yīng)。下面將通過(guò)實(shí)施例來(lái)進(jìn)一步說(shuō)明本發(fā)明,但本發(fā)明并不因此而受到任何限制。本發(fā)明實(shí)施例和對(duì)比例中所使用的原料油為減壓渣油,其性質(zhì)列于表1。本發(fā)明實(shí)施例和對(duì)比例中所使用的催化劑為催化裂化催化劑,由中國(guó)石油化工股份有限公司催化劑齊魯分公司生產(chǎn),商品編號(hào)為mlc-500,性質(zhì)列于表2。本發(fā)明實(shí)施例和對(duì)比例中氣體產(chǎn)物收集完成由agilent6890gc(tcd檢測(cè)器)分析干氣和液化氣產(chǎn)率,液體產(chǎn)品采用氣相色譜的模擬蒸餾進(jìn)行測(cè)定,結(jié)焦催化劑和再生催化劑卸出后在multiea2000碳硫分析儀上進(jìn)行焦炭含量分析(采用ripp106-90測(cè)試方法進(jìn)行測(cè)試)。實(shí)施例1-2實(shí)施例1-2在如圖1所示的裝置上進(jìn)行,其中細(xì)管段的內(nèi)徑為5厘米,長(zhǎng)度為60厘米,粗管段的內(nèi)徑為15厘米,長(zhǎng)度為60厘米,密相床緩沖器的內(nèi)徑為50厘米,長(zhǎng)度為100厘米,密相床緩沖器內(nèi)設(shè)置有金屬燒結(jié)過(guò)濾器分離再生催化劑和再生煙氣。按照本發(fā)明所提出的再生方法對(duì)結(jié)焦催化劑進(jìn)行快速再生,在粗管段和細(xì)管段的底部分別通入純氧。催化劑在提升管再生器的停留再生時(shí)間為8秒,在密相床緩沖器通入空氣,催化劑的平均停留時(shí)間為60秒。再生后的再生催化劑進(jìn)入反應(yīng)器,與表1所列的原料油接觸,進(jìn)行催化裂化反應(yīng),具體再生條件、反應(yīng)條件和產(chǎn)品收率均列于表3。對(duì)比例對(duì)比例在燒焦罐型式密相床催化裂化裝置上進(jìn)行,燒焦罐和密相床的內(nèi)徑與本發(fā)明不同,燒焦罐的內(nèi)徑為40厘米,長(zhǎng)度為60厘米,密相床層的內(nèi) 徑為200厘米,長(zhǎng)度為400厘米。按照常規(guī)的空氣再生方法對(duì)與實(shí)施例相同的結(jié)焦催化劑進(jìn)行再生,燒焦罐和密相床層分別通入空氣。催化劑在燒焦罐的停留時(shí)間為60秒,在密相床層的平均停留時(shí)間為6分鐘。再生后的催化劑進(jìn)入反應(yīng)器,與表1所列的原料油接觸,進(jìn)行催化裂化反應(yīng),具體再生條件、反應(yīng)條件和產(chǎn)品收率均列于表3。從表3的結(jié)果對(duì)比可以看出,與對(duì)比例相比,實(shí)施例1在再生器和密相床尺寸大幅度減小,裝置總藏量大幅度減少,耗風(fēng)指標(biāo)明顯降低的前提下,采用本發(fā)明的再生方法,再生催化劑上炭含量降低較多,產(chǎn)品分布好,干氣產(chǎn)率和焦炭產(chǎn)率選擇性較好。另外,若控制實(shí)施例2的再生條件,使實(shí)施例2所得再生催化劑含碳量與對(duì)比例相同,從產(chǎn)品收率可以看出,產(chǎn)品分布好,干氣產(chǎn)率和焦炭產(chǎn)率選擇性也較好,這是因?yàn)椴捎帽景l(fā)明的再生方法,再生催化劑活性分布更均勻。表1為本發(fā)明實(shí)施例和對(duì)比例所使用的原料油原料油名稱減壓渣油密度(20℃),千克/米3933.0運(yùn)動(dòng)粘度,毫米2/秒100℃65殘?zhí)恐?,重?.0凝點(diǎn),℃35總氮,重%0.31硫,重%0.25碳,重%86.91氫,重%12.50金屬含量,ppm鎳8.8釩2.0鐵1.8銅<0.1鈉0.3餾程,℃hk(初餾點(diǎn))38010%45230%51550%56770%619kk(終餾點(diǎn))/表2為本發(fā)明實(shí)施例和對(duì)比例所使用的催化劑催化劑商品編號(hào)mlc-500化學(xué)組成,重%氧化鋁50.3氧化鈉0.320表觀密度,kg/m3800孔體積,ml/g0.35比表面積,m2/g210磨損指數(shù),重%·時(shí)-11.7篩分組成,重%0~40微米12.140~80微米49.5>80微米38.4表3為本發(fā)明實(shí)施例和對(duì)比例的再生條件、反應(yīng)條件和產(chǎn)品收率實(shí)施例1實(shí)施例2對(duì)比例催化裂化反應(yīng)單元提升管出口溫度,℃500500500催化劑/原料重量比666反應(yīng)時(shí)間,秒333水蒸汽/原料重量比0.050.050.05再生單元裝置催化劑總藏量,噸0.50.55再生氣體氧氣氧氣空氣再生溫度,℃670670670耗風(fēng)指標(biāo),nm3/kg32.813.5結(jié)焦催化劑碳含量,重%1.11.051.2再生催化劑碳含量,重%0.040.120.12產(chǎn)品收率干氣產(chǎn)率,重%3.02.63.6液化氣產(chǎn)率,重%15.014.314.8汽油產(chǎn)率,重%42.843.041.5柴油產(chǎn)率,重%25.326.525.0重油產(chǎn)率,重%5.05.05.4焦炭產(chǎn)率,重%8.98.69.7當(dāng)前第1頁(yè)12