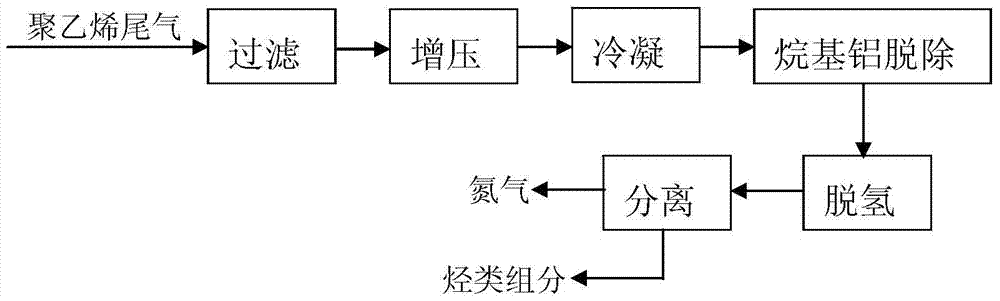
本發(fā)明涉及聚乙烯生產(chǎn)裝置的尾氣回收技術(shù)領(lǐng)域,更具體地講,本發(fā)明涉及一種回收聚乙烯裝置尾氣中烴類組分和氮?dú)獾姆椒ê脱b置。
背景技術(shù):在聚乙烯的生產(chǎn)過(guò)程中,通常會(huì)從聚合反應(yīng)器和聚乙烯粉料脫氣倉(cāng)中排放出大量的由包括未聚合的乙烯和共聚單體(丙烯、丁烯、己烯等)等的烴類組分、誘導(dǎo)冷凝劑(異戊烷、己烷等)、氫氣和脫氣倉(cāng)的吹掃氮?dú)馑旌隙傻木垡蚁┭b置尾氣?;厥站垡蚁┭b置尾氣中的烴類組分和氮?dú)獾葰怏w,對(duì)于聚乙烯裝置的節(jié)能降耗而言意義重大。現(xiàn)有的回收聚乙烯裝置尾氣的方法通常包括加壓冷凝、膜分離和變壓吸附等步驟,從而能夠?qū)崿F(xiàn)烴類組分的有效回收,其中,烴類組分的回收率可達(dá)到99%以上。但是,采用現(xiàn)有技術(shù)中上述方法回收的氮?dú)庵芯袣錃猓绻麑⒒厥盏牡獨(dú)夥祷刂撩摎鈧}(cāng)循環(huán)使用,則可能會(huì)形成倉(cāng)內(nèi)的氫氣積累而造成嚴(yán)重的安全隱患。因此,亟需提供一種能夠從聚乙烯裝置尾氣中同時(shí)回收烴類組分以及氫氣含量極低的氮?dú)獾姆椒ê脱b置。
技術(shù)實(shí)現(xiàn)要素:針對(duì)上述現(xiàn)有技術(shù)中存在的問(wèn)題和不足,本發(fā)明的目的在于提供一種能夠從聚乙烯裝置尾氣中同時(shí)回收烴類組分和氮?dú)獾姆椒ê脱b置,從而實(shí)現(xiàn)氮?dú)饣厥章蚀笥?9%且烴類組分回收率達(dá)到近100%的近零排放效果。為了實(shí)現(xiàn)上述目的,本發(fā)明的一方面提供了一種回收聚乙烯裝置尾氣中烴類組分和氮?dú)獾姆椒ǎ龇椒òㄒ韵虏襟E:A、使聚乙烯裝置尾氣經(jīng)過(guò)催化脫氫反應(yīng)器進(jìn)行脫氫處理;B、使脫氫處理后的聚乙烯裝置尾氣經(jīng)過(guò)變壓吸附分離單元進(jìn)行烴類組分和氮?dú)獾姆蛛x處理,回收得到彼此分離的烴類組分和氫氣含量為0.001~0.5mol%的氮?dú)?。根?jù)本發(fā)明的回收聚乙烯裝置尾氣中烴類組分和氮?dú)獾姆椒ǖ囊粋€(gè)實(shí)施例,所述方法還包括在步驟A之前進(jìn)行的利用過(guò)濾單元去除聚乙烯裝置尾氣中的固體顆粒和液滴的過(guò)濾步驟。根據(jù)本發(fā)明的回收聚乙烯裝置尾氣中烴類組分和氮?dú)獾姆椒ǖ囊粋€(gè)實(shí)施例,所述方法還包括在所述過(guò)濾步驟之后且在步驟A之前進(jìn)行的利用增壓?jiǎn)卧獙⒕垡蚁┭b置尾氣增壓至0.2~2MPa的增壓步驟。根據(jù)本發(fā)明的回收聚乙烯裝置尾氣中烴類組分和氮?dú)獾姆椒ǖ囊粋€(gè)實(shí)施例,所述方法還包括在所述增壓步驟之后且在步驟A之前進(jìn)行的利用低溫冷凝單元回收聚乙烯裝置尾氣中的誘導(dǎo)冷凝劑和高沸點(diǎn)烴類組分的低溫冷凝步驟,其中,冷凝溫度為-30~2℃。根據(jù)本發(fā)明的回收聚乙烯裝置尾氣中烴類組分和氮?dú)獾姆椒ǖ囊粋€(gè)實(shí)施例,所述方法還包括在所述低溫冷凝步驟之后且在步驟A之前進(jìn)行的利用烷基鋁脫除塔脫除聚乙烯裝置尾氣中的烷基鋁的脫除步驟,其中,所述烷基鋁脫除塔中裝填有活性炭。根據(jù)本發(fā)明的回收聚乙烯裝置尾氣中烴類組分和氮?dú)獾姆椒ǖ囊粋€(gè)實(shí)施例,所述催化脫氫反應(yīng)器中裝填的催化劑為含貴金屬的脫氫催化劑或含非貴金屬的脫氫催化劑,其中,脫氫處理的反應(yīng)溫度為50~300℃。根據(jù)本發(fā)明的回收聚乙烯裝置尾氣中烴類組分和氮?dú)獾姆椒ǖ囊粋€(gè)實(shí)施例,所述含貴金屬的脫氫催化劑為含鈀、鉑、金和銀中至少一種的脫氫催化劑,所述含非貴金屬的脫氫催化劑為含錳、銅和鎳中至少一種的脫氫催化劑。根據(jù)本發(fā)明的回收聚乙烯裝置尾氣中烴類組分和氮?dú)獾姆椒ǖ囊粋€(gè)實(shí)施例,所述變壓吸附分離單元包括2個(gè)或2個(gè)以上的吸附塔,所述吸附塔中裝填有為活性炭、活性氧化鋁、硅膠和分子篩中的一種或多種的吸附劑。根據(jù)本發(fā)明的回收聚乙烯裝置尾氣中烴類組分和氮?dú)獾姆椒ǖ囊粋€(gè)實(shí)施例,所述變壓吸附分離單元中的分離處理至少包括吸附步驟、逆放步驟和抽空步驟,所述吸附步驟的壓力大于0.15MPa,所述逆放步驟的壓力大于0.1Mpa,所述抽空步驟的壓力為0.001~0.06MPa,其中,使脫氫處理后的聚乙烯裝置尾氣冷卻至20~60℃后再進(jìn)入變壓吸附分離單元中。本發(fā)明的另一方面提供了一種回收聚乙烯裝置尾氣中烴類組分和氮?dú)獾难b置,所述裝置包括通過(guò)管道順次連接的催化脫氫反應(yīng)器和變壓吸附分離單元,其中,所述聚乙烯裝置尾氣依次經(jīng)過(guò)催化脫氫反應(yīng)器和變壓吸附分離單元回收得到彼此分離的烴類組分和氫氣含量為0.001~0.5mol%的氮?dú)狻8鶕?jù)本發(fā)明的回收聚乙烯裝置尾氣中烴類組分和氮?dú)獾难b置的一個(gè)實(shí)施例,所述裝置還包括設(shè)置在催化脫氫反應(yīng)器之前的過(guò)濾單元,所述過(guò)濾單元用于去除聚乙烯裝置尾氣中的固體顆粒和液滴。根據(jù)本發(fā)明的回收聚乙烯裝置尾氣中烴類組分和氮?dú)獾难b置的一個(gè)實(shí)施例,所述裝置還包括設(shè)置在所述過(guò)濾單元之后且在催化脫氫反應(yīng)器之前的增壓?jiǎn)卧?,所述增壓?jiǎn)卧糜趯?duì)聚乙烯裝置尾氣進(jìn)行增壓。根據(jù)本發(fā)明的回收聚乙烯裝置尾氣中烴類組分和氮?dú)獾难b置的一個(gè)實(shí)施例,所述裝置還包括設(shè)置在所述增壓?jiǎn)卧笄以诖呋摎浞磻?yīng)器之前的低溫冷凝單元,所述低溫冷凝單元用于回收聚乙烯裝置尾氣中的誘導(dǎo)冷凝劑和高沸點(diǎn)烴類組分。根據(jù)本發(fā)明的回收聚乙烯裝置尾氣中烴類組分和氮?dú)獾难b置的一個(gè)實(shí)施例,所述裝置還包括設(shè)置在所述低溫冷凝單元之后且在催化脫氫反應(yīng)器之前的烷基鋁脫除塔,所述烷基鋁脫除塔用于脫除聚乙烯裝置尾氣中的烷基鋁,其中,所述烷基鋁脫除塔中裝填有活性炭。根據(jù)本發(fā)明的回收聚乙烯裝置尾氣中烴類組分和氮?dú)獾难b置的一個(gè)實(shí)施例,所述催化脫氫反應(yīng)器中裝填的催化劑為含貴金屬的脫氫催化劑或含非貴金屬的脫氫催化劑。根據(jù)本發(fā)明的回收聚乙烯裝置尾氣中烴類組分和氮?dú)獾难b置的一個(gè)實(shí)施例,所述含貴金屬的脫氫催化劑為含鈀、鉑、金和銀中至少一種的脫氫催化劑,所述含非貴金屬的脫氫催化劑為含錳、銅和鎳中至少一種的脫氫催化劑。根據(jù)本發(fā)明的回收聚乙烯裝置尾氣中烴類組分和氮?dú)獾难b置的一個(gè)實(shí)施例,所述變壓吸附分離單元包括2個(gè)或2個(gè)以上的吸附塔,所述吸附塔中裝填有為活性炭、活性氧化鋁、硅膠和分子篩中的一種或多種的吸附劑。本發(fā)明具體利用了催化脫氫與變壓吸附相結(jié)合的技術(shù)從聚乙烯裝置尾氣中同時(shí)回收烴類組分和氮?dú)獾姆椒?,將尾氣中的烴類組分和誘導(dǎo)冷凝劑濃縮回收利用,同時(shí)脫除掉尾氣中含有的氫氣,從而使得回收后的烴類組分和氮?dú)饽軌蚍謩e返回至聚乙烯裝置中循環(huán)使用,達(dá)到零排放和全回收聚乙烯裝置尾氣中烴類組分和氮?dú)獾哪康?。附圖說(shuō)明圖1示出了根據(jù)本發(fā)明示例性實(shí)施例的回收聚乙烯裝置尾氣中烴類組分和氮?dú)獾难b置的結(jié)構(gòu)框圖。圖2示出了根據(jù)本發(fā)明示例性實(shí)施例的回收聚乙烯裝置尾氣中烴類組分和氮?dú)獾姆椒ǖ牧鞒炭驁D。具體實(shí)施方式在下文中,將結(jié)合附圖詳細(xì)說(shuō)明本發(fā)明的回收聚乙烯裝置尾氣中烴類組分和氮?dú)獾姆椒ê脱b置。根據(jù)本發(fā)明,所述聚乙烯裝置尾氣是指在聚乙烯的正常生產(chǎn)過(guò)程中從聚合反應(yīng)器和聚乙烯粉料脫氣倉(cāng)中排放出的由包括未聚合的乙烯和共聚單體(丙烯、丁烯、己烯等)等的烴類組分、誘導(dǎo)冷凝劑(異戊烷、己烷等)、氫氣和脫氣倉(cāng)的吹掃氮?dú)馑旌隙傻臍怏w。本發(fā)明的目的是提供一種能夠同時(shí)有效回收聚乙烯裝置尾氣中的烴類組分和氮?dú)獠⑦M(jìn)行循環(huán)利用的方法和裝置,其中,所回收的氮?dú)庵袣錃夂繛?.001~0.5mol%,從而避免了氮?dú)饣厥帐褂脮r(shí)可能產(chǎn)生的安全隱患。下面先對(duì)本發(fā)明的回收聚乙烯裝置尾氣中烴類組分和氮?dú)獾姆椒ㄟM(jìn)行具體說(shuō)明。根據(jù)本發(fā)明,所述回收聚乙烯裝置尾氣中烴類組分和氮?dú)獾姆椒òㄒ韵虏襟E:A、使聚乙烯裝置尾氣經(jīng)過(guò)催化脫氫反應(yīng)器進(jìn)行脫氫處理;B、使脫氫處理后的聚乙烯裝置尾氣經(jīng)過(guò)變壓吸附分離單元進(jìn)行烴類組分和氮?dú)獾姆蛛x處理,回收得到彼此分離的烴類組分和氫氣含量為0.001~0.5mol%的氮?dú)?。在上述步驟中,先將聚乙烯裝置尾氣進(jìn)行催化脫氫處理,是為了能夠預(yù)先脫除掉聚乙烯裝置尾氣中的氫氣,便于進(jìn)行后續(xù)的分離處理并獲得較為純凈的氮?dú)?;然后將脫氫處理后的聚乙烯裝置尾氣進(jìn)行變壓吸附分離處理,是為了能夠同時(shí)得到分離后的烴類組分和氮?dú)?。根?jù)本發(fā)明的優(yōu)選實(shí)施例,將所得烴類組分分離后進(jìn)行分別的回收利用,將所得氮?dú)夥祷刂辆垡蚁┑纳a(chǎn)過(guò)程中作為吹掃氣體在脫氣倉(cāng)中使用,但本發(fā)明不限于此。但是由于聚乙烯裝置尾氣中還存在諸如雜質(zhì)、誘導(dǎo)冷凝劑、烷基鋁等物質(zhì),所以為了獲得更純凈的產(chǎn)品并實(shí)現(xiàn)更好的分離回收效果,本發(fā)明的回收方法中還可以包括其他的優(yōu)化步驟。具體地,圖2示出了根據(jù)本發(fā)明示例性實(shí)施例的回收聚乙烯裝置尾氣中烴類組分和氮?dú)獾姆椒ǖ牧鞒炭驁D。如圖2所示,根據(jù)本發(fā)明的示例性實(shí)施例,所述方法還包括在步驟A之前進(jìn)行的利用過(guò)濾單元去除聚乙烯裝置尾氣中的固體顆粒和液滴的過(guò)濾步驟,從而能夠保證后續(xù)單元的穩(wěn)定運(yùn)行;所述方法還包括在過(guò)濾步驟之后且在步驟A之前進(jìn)行的利用增壓?jiǎn)卧獙⒕垡蚁┭b置尾氣增壓至0.2~2MPa的增壓步驟,其中,增壓?jiǎn)卧梢詾閴嚎s機(jī)或鼓風(fēng)機(jī),增壓的步驟可以縮小管道通徑并降低投資,有利于冷凝回收高沸點(diǎn)烴類組分;所述方法還包括在增壓步驟之后且在步驟A之前進(jìn)行的利用低溫冷凝單元回收聚乙烯裝置尾氣中的誘導(dǎo)冷凝劑和高沸點(diǎn)烴類組分的低溫冷凝步驟,其中冷凝溫度為-30~2℃;所述方法還包括在低溫冷凝步驟之后且在步驟A之前進(jìn)行的利用烷基鋁脫除塔脫除聚乙烯裝置尾氣中的烷基鋁的脫除步驟,其中,烷基鋁脫除塔中裝填有活性炭,脫除尾氣中可能含有的烷基鋁可以保證脫氫單元長(zhǎng)時(shí)間的穩(wěn)定運(yùn)行。但本發(fā)明不限于此,操作人員可以根據(jù)需要增加或刪除上述優(yōu)化步驟中的任一個(gè)。根據(jù)本發(fā)明,上述催化脫氫反應(yīng)器中裝填的催化劑為含貴金屬的脫氫催化劑或含非貴金屬的脫氫催化劑,其中,脫氫處理的反應(yīng)溫度為50~300℃。其中,含貴金屬的脫氫催化劑可以為含鈀、鉑、金和銀中至少一種的脫氫催化劑,含非貴金屬的脫氫催化劑可以為含錳、銅和鎳中至少一種的脫氫催化劑。其中,氫氣在催化脫氫反應(yīng)器中且在脫氫催化劑的作用下與乙烯反應(yīng)生成乙烷而被脫除,脫除氫氣之后的聚乙烯裝置尾氣則可進(jìn)入后續(xù)的吸附分離處理階段。上述變壓吸附分離單元包括2個(gè)或2個(gè)以上的吸附塔,當(dāng)然其可以還包括如配套的程控閥、管道、PLC控制器和真空泵等輔助設(shè)備。優(yōu)選地,將脫氫處理之后的聚乙烯裝置尾氣冷卻至20~60℃,冷卻的目的是保證變壓吸附分離單元的穩(wěn)定運(yùn)行。之后再進(jìn)入變壓吸附分離單元進(jìn)行分離處理,可以采用自然冷卻的方式,也可以采用換熱器和冷卻器進(jìn)行強(qiáng)制冷卻的方式。其中,吸附塔中裝填有為活性炭、活性氧化鋁、硅膠和分子篩中的一種或多種的吸附劑,吸附劑可以實(shí)現(xiàn)對(duì)乙烯、乙烷等烴類組分的選擇性吸附,而氮?dú)鈩t從吸附塔塔頂?shù)臍怏w出口被分離出來(lái)。之后,可以利用真空泵降壓將吸附在吸附劑上的烴類組分脫吸附而獲得烴類組分的產(chǎn)品,繼而再去乙烯分離裝置回收乙烯、丙烯等產(chǎn)品,乙烷等飽和烴類組分也可以作為乙烯裂解爐的原料,烴類組分也...