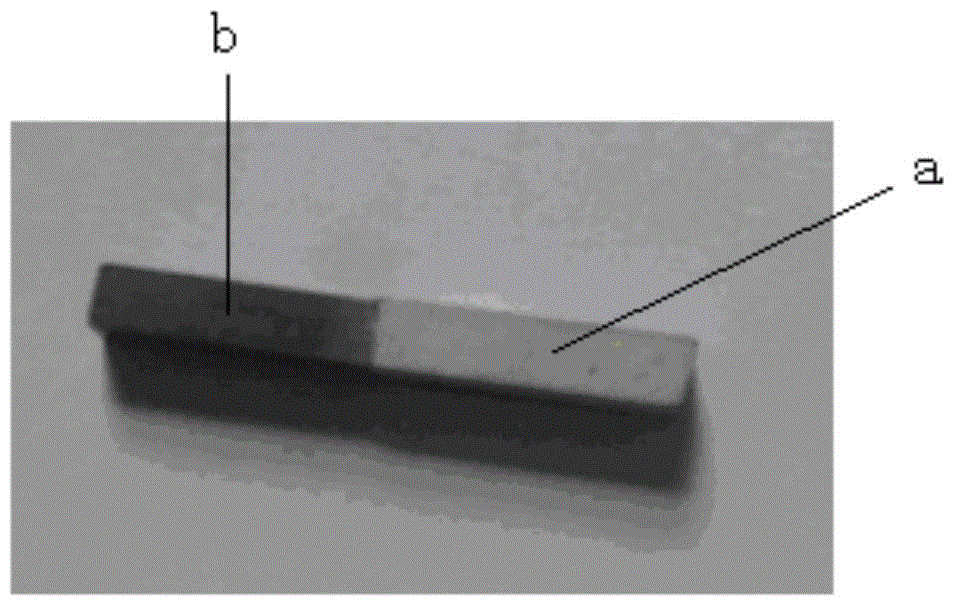
一種Co-Cr-Mo合金/氧化鋯陶瓷復(fù)合材料及其制備方法技術(shù)領(lǐng)域本發(fā)明涉及一種Co-Cr-Mo合金/氧化鋯陶瓷復(fù)合材料及其制備方法;屬于復(fù)合材料制備技術(shù)領(lǐng)域。
背景技術(shù):Co-Cr-Mo合金由于其具有優(yōu)異的力學(xué)性能和生物相容性能,故其適用于制造體內(nèi)承載條件苛刻的長期植入件,但在人工關(guān)節(jié)置換手術(shù)中,由于聚四氟乙烯髖臼和Co-Cr-Mo合金金屬股骨頭之間的機(jī)械磨損和腐蝕,產(chǎn)生的合金碎屑容易在關(guān)節(jié)腔內(nèi)積累,從而引起有害的組織反應(yīng)和過敏反應(yīng)進(jìn)而導(dǎo)致人體炎癥、植入體松動等不良現(xiàn)象,因此限制了Co-Cr-Mo合金在生物種植體中的應(yīng)用。相比金屬,氧化鋯陶瓷與內(nèi)襯的摩擦因數(shù)更小,研究結(jié)果表明氧化鋯陶瓷與聚四氟乙烯間的磨損率比Co-Cr-Mo合金與聚四氟乙烯的磨損率低20倍,同時(shí)氧化鋯由于具有高強(qiáng)度、高韌性和高表面光潔度且無毒耐腐蝕,化學(xué)性能穩(wěn)定的特點(diǎn),被認(rèn)為是制備高載荷條件下人工關(guān)節(jié)球頭的理想替代材料,因此這種Co-Cr-Mo合金-氧化鋯陶瓷復(fù)合關(guān)節(jié)假體成為了研究最多的關(guān)節(jié)置換材料。目前主要生產(chǎn)工藝是利用等離子噴涂或者激光熔覆在Co-Cr-Mo合金球頭上制備一層氧化鋯陶瓷薄膜,但這種方法涂層跟基體的結(jié)合強(qiáng)度不夠,容易導(dǎo)致涂層剝落,甚至完全剝落,剝落的氧化鋯陶瓷碎屑也容易在關(guān)節(jié)腔內(nèi)積累,從而引起有害的組織反應(yīng)和過敏反應(yīng)進(jìn)而導(dǎo)致人體炎癥、植入體松動等不良現(xiàn)象。而直接制備氧化鋯陶瓷球頭不存在這一問題,但需要解決Co-Cr-Mo合金人工關(guān)節(jié)柄和氧化鋯陶瓷球頭的連接。目前,人們已經(jīng)開始招手研究采用共燒結(jié)制備陶瓷/金屬復(fù)合材料的技術(shù),但其存在所得成品界面結(jié)合強(qiáng)度低、共燒結(jié)界面變形、樣品極易開裂、成品率低等問題,如采用共燒結(jié)技術(shù)制備氧化鋯/316L不銹鋼復(fù)合材料時(shí),其加入1-2wt%的粘接劑;所得成品的成品率低,極易出現(xiàn)共燒結(jié)界面變形、樣品極易開裂的情況,即使得到了成品,其成品的界面結(jié)合強(qiáng)度僅僅約為20Mpa;采用共燒結(jié)技術(shù)制備氧化鋯/Ni-Cr合金復(fù)合材料時(shí),其加入1-2wt%的粘接劑;所得成品的成品率低,極易出現(xiàn)共燒結(jié)界面變形、樣品極易開裂的情況,即使得到了成品,其成品的界面結(jié)合強(qiáng)度僅僅約為25Mpa。到目前為止,人們還沒有通過共燒結(jié)技術(shù),得到界面結(jié)合強(qiáng)度高、成品率高的氧化鋯/Co-Cr-Mo合金復(fù)合材料。
技術(shù)實(shí)現(xiàn)要素:本發(fā)明針對現(xiàn)有技術(shù)存在的不足之處,提供一種界面結(jié)合強(qiáng)度高、成品率高的Co-Cr-Mo合金/氧化鋯陶瓷復(fù)合材料及其制備方法。本發(fā)明一種Co-Cr-Mo合金/氧化鋯陶瓷復(fù)合材料,包括Co-Cr-Mo合金部分、氧化鋯陶瓷部分,所述氧化鋯陶瓷部分通過界面結(jié)合層與Co-Cr-Mo合金部分構(gòu)成一個整體,所述Co-Cr-Mo合金部分的孔隙率為8-20%、優(yōu)選為10-14%、進(jìn)一步優(yōu)選為10-12%;所述氧化鋯陶瓷部分的孔隙率為2%-7%、優(yōu)選為2%-5%、進(jìn)一步優(yōu)選為2%-3%;所述界面結(jié)合層的結(jié)合強(qiáng)度為30-40Mpa。本發(fā)明一種Co-Cr-Mo合金/氧化鋯陶瓷復(fù)合材料,所述界面結(jié)合處存在元素的交互擴(kuò)散區(qū),其厚度為1-5um。本發(fā)明一種Co-Cr-Mo合金/氧化鋯陶瓷復(fù)合材料,所述Co-Cr-Mo合金部分為Co-Cr-Mo合金人工關(guān)節(jié)柄;所述氧化鋯陶瓷部分為與Co-Cr-Mo合金人工關(guān)節(jié)柄配套的球頭。本發(fā)明一種Co-Cr-Mo合金/氧化鋯陶瓷復(fù)合材料的制備方法,包括下述步驟:步驟一配料取平均粒徑16~35μm的Co-Cr-Mo合金粉末為原料A,按原料A總質(zhì)量的8%~15%配取石蠟,并將所配取的原料A與石蠟混合均勻,得到混合物A;石蠟除了起到粘結(jié)的作用外,最主要的目的是調(diào)節(jié)Co-Cr-Mo合金燒結(jié)時(shí)的孔隙率,從而調(diào)節(jié)Co-Cr-Mo合金的燒結(jié)收縮行為;取平均粒徑45~65μm的ZrO2粉末為原料B,按原料B總質(zhì)量的0.05%~0.2%配取石蠟,并將所配取的原料B與石蠟混合均勻,得到混合物B;步驟二成型將混合物A、混合B放入壓腔中壓制成型,得到一端為混合物A,另一端為混合物B的整體壓坯;壓制時(shí),控制壓力為300-600Mpa;步驟三燒結(jié)在真空條件下,對步驟二所得壓坯進(jìn)行燒結(jié),燒結(jié)完成后,隨爐冷卻至室溫,得到Co-Cr-Mo合金/氧化鋯陶瓷復(fù)合材料;燒結(jié)時(shí),控制升溫速率為2-5℃/min、進(jìn)一步優(yōu)選為5℃/min,控制燒結(jié)溫度為1300℃-1500℃、優(yōu)選為1300℃-1450℃、進(jìn)一步優(yōu)選為1450℃。本發(fā)明一種Co-Cr-Mo合金/氧化鋯陶瓷復(fù)合材料的制備方法,步驟一中,混合物A中,石蠟的質(zhì)量為原料A質(zhì)量的8-10%。本發(fā)明一種Co-Cr-Mo合金/氧化鋯陶瓷復(fù)合材料的制備方法,步驟一中,混合物B中,石蠟的質(zhì)量為原料B質(zhì)量的0.05%~0.2%。本發(fā)明本發(fā)明一種Co-Cr-Mo合金/氧化鋯陶瓷復(fù)合材料的制備方法,步驟一中所述Co-Cr-Mo合金粉末以質(zhì)量百分比包括下述組分:Cr26%-30%;Mo5%-7%;余量為Co。本發(fā)明一種Co-Cr-Mo合金/氧化鋯陶瓷復(fù)合材料的制備方法,步驟二中,壓制成型時(shí),采用單向壓制的方法制備壓坯,為了方便操作,一般在往壓腔中加粉前,會用一個很薄的隔板將壓腔分為C、D兩部分,然后將混合物A加入C部分,將混合物B加入D部分,震實(shí),并使得震實(shí)后的混合物A與混合物B處于同一水平位置,抽出隔板施壓,得到坯體,所述隔板與壓腔底部接觸;或先將混合物A加入壓腔中,震實(shí),然后再將混合物B加入壓腔中,壓制得到坯體;或先將混合物B加入壓腔中,震實(shí),然后再將混合物A加入壓腔中,壓制得到坯體。本發(fā)明一種Co-Cr-Mo合金/氧化鋯陶瓷復(fù)合材料的制備方法,步驟三中,所述真空條件的壓強(qiáng)≤10-1Pa。本發(fā)明一種Co-Cr-Mo合金/氧化鋯陶瓷復(fù)合材料的制備方法,步驟三中,在燒結(jié)溫度下保溫1-3小時(shí)、優(yōu)選為2小時(shí)。原理和優(yōu)勢本發(fā)明通過嚴(yán)格限定原料粉末的組分和粒度,通過對不同原料加入不同質(zhì)量的石蠟,在合理的壓制壓力以及燒結(jié)程序下,實(shí)現(xiàn)了Co-Cr-Mo合金與氧化鋯陶瓷完美結(jié)合,得到了界面結(jié)合層的結(jié)合強(qiáng)度為30-40Mpa的Co-Cr-Mo合金/氧化鋯陶瓷復(fù)合材料。本發(fā)明通過往粒度為16~35μm的Co-Cr-Mo合金粉末中加入8-15%的石蠟,通過往45~65μm的ZrO2粉末加入0.05%-0.2%的石蠟,通過合理的壓制壓力與燒結(jié),得到界面結(jié)合良好的復(fù)合材料。本發(fā)明控制合金端和陶瓷端的粒度以及孔隙率,調(diào)整兩端燒結(jié)行為,為避免燒結(jié)升溫、保溫過程中出現(xiàn)明顯的界面變形和材料開裂提供了必要條件。通過將石蠟按不同的用量加入合金粉末與陶瓷粉末中,尤其是當(dāng)8-15%的石蠟加入合金粉末中,0.05%-0.2%加入ZrO2粉末中,在燒結(jié)加熱前期,通過控制升溫速率,使得合金粉末中的石蠟以一個合理的速度分解并被排除坯體中,從而使得坯體的合金端出現(xiàn)適當(dāng)?shù)目紫堵?。由于合金的熱膨脹系?shù)要大于陶瓷的熱膨脹系數(shù),所以必須選用粒度較大的ZrO2粉末,該尺寸的ZrO2粉末加入0.05%-0.2%的石蠟以便于成型,在壓力為300-600Mpa壓制后,在本發(fā)明燒結(jié)前期能減少由于熱膨脹差異導(dǎo)致復(fù)合材料沿界面開裂的可能。燒結(jié)后期,由于石蠟基本排除坯體,此時(shí)合金端與陶瓷端均開始出現(xiàn)閉孔現(xiàn)象,此時(shí)必須嚴(yán)格控制燒結(jié)的溫度和時(shí)間,一旦溫度過高、時(shí)間過長,將導(dǎo)致合金端大量孔隙消失,那么在后續(xù)降溫時(shí),有可能出現(xiàn)界面變形甚至沿界面開裂的現(xiàn)象出現(xiàn)。一旦時(shí)間過短、溫度過低則會導(dǎo)致界面擴(kuò)散層的厚度太低,從而嚴(yán)重影響界面結(jié)合強(qiáng)度。本發(fā)明燒結(jié)后的冷卻過程中,由于不同孔隙度的Co-Cr-Mo合金,其燒結(jié)收縮行為不同,高孔隙度的Co-Cr-Mo合金收縮較慢,同時(shí)ZrO2收縮速率比Co-Cr-Mo合金小。所以本發(fā)明通過嚴(yán)格控制原料粉末的組分和粒度,通過對不同原料加入不同質(zhì)量的石蠟,在合理的壓制壓力以及合理的燒結(jié)條件參數(shù),保證了Co-Cr-Mo合金的孔隙度,從而使得降溫過程中Co-Cr-Mo合金的收縮率與ZrO2收縮行為相近,減少了界面應(yīng)力,從而得到了界面結(jié)合強(qiáng)度高的Co-Cr-Mo合金/氧化鋯復(fù)合材料。本發(fā)明在燒結(jié)過程中Co-Cr-Mo合金/ZrO2界面兩端元素相互擴(kuò)散,形成一個2-5微米的元素梯度變化區(qū)域,避免了界面處元素濃度突變,增加了界面結(jié)合強(qiáng)度。總之,本發(fā)明通過各參數(shù)的協(xié)同作用,尤其是巧妙的利用了石蠟含量為6-15%的Co-Cr-Mo合金的燒結(jié)收縮率與氧化鋯陶瓷的燒結(jié)收縮率相近的特性,通過合理的配比與工藝條件參數(shù)的控制,得到了界面結(jié)合層的結(jié)合強(qiáng)度為30-40Mpa的Co-Cr-Mo合金/氧化鋯陶瓷復(fù)合材料。附圖說明附圖1為本發(fā)明所得產(chǎn)品的示意圖,附圖2為本發(fā)明實(shí)施例1所制備的樣品照片;b為Co-Cr-Mo合金部分,a為氧化鋯陶瓷部分;附圖3為實(shí)施例1所得樣品界面的能譜分析圖,左端為Co-Cr-Mo合金,右端為氧化鋯陶瓷;圖3中左端為Co-Cr-Mo合金,右端為氧化鋯陶瓷;從圖3中可以看出從圖中可以看出界面處氧和鋯元素已經(jīng)擴(kuò)散到Co-Cr-Mo合金中。具體實(shí)施方式本發(fā)明實(shí)施例中成品金屬端的孔隙率是通過下述方法測得的;在相同的條件下,制得純金屬粉末的壓坯并燒結(jié),最后測量所的燒結(jié)成品的孔隙率,即為該條件下,所的復(fù)合材料金屬端的孔隙率;在相同的條件下,制得純氧化鋯的壓坯并燒結(jié),最后測量所的燒結(jié)成品的孔隙率,即為該條件下,所的復(fù)合材料氧化鋯端的孔隙率。實(shí)施例1步驟一配料取平均粒徑16μm的Co-Cr-Mo合金粉末為原料A,按原料A總質(zhì)量的9%配取石蠟,并將所配取的原料A與石蠟混合均勻,得到混合物A;原料A中Cr:28wt%、Mo:6wt%、Co:余量wt%;取平均粒徑45μm的ZrO2粉末為原料B,按原料B總質(zhì)量的0.1%配取石蠟,并將所配取的原料B與石蠟混合均勻,得到混合物B;步驟二成型用單向壓制的方法制備式樣,壓制壓力為300MPa。試樣為抗彎樣,尺寸長為42mm,寬為6mm,厚為4mm。制備壓制前,在上述模具的中部加入金屬薄片,在薄片兩側(cè)裝填混合物A和混合物B;步驟三燒結(jié)將壓坯試樣在真空度為10-3Pa的真空燒結(jié)爐中,以每分鐘5℃的升溫速率,在1400℃下保溫2小時(shí)進(jìn)行燒結(jié),然后隨爐冷卻至室溫。得到成品,檢測成品的力學(xué)性能,得到燒結(jié)試樣的界面結(jié)合強(qiáng)度達(dá)到35.06MPa。所得成品中金屬端的孔隙率為15.5%、陶瓷端的孔隙率為4%。實(shí)施例2步驟一配料取平均粒徑35μm的Co-Cr-Mo合金粉末為原料A,按原料A總質(zhì)量的8%配取石蠟,并將所配取的原料A與石蠟混合均勻,得到混合物A;原料A中Cr:28wt%、Mo:6wt%、Co:余量wt%;取平均粒徑65μm的ZrO2粉末為原料B,按原料B總質(zhì)量的0.1%配取石蠟,并將所配取的原料B與石蠟混合均勻,得到混合物B;步驟二成型用單向壓制的方法制備式樣,壓制壓力為600MPa。試樣為抗彎樣,尺寸長為42mm,寬為6mm,厚為4mm。制備壓制前,在上述模具的中部加入金屬薄片,在薄片兩側(cè)裝填混合物A和混合物B;步驟三燒結(jié)將壓坯試樣在真空度為10-1Pa的真空燒結(jié)爐中,以每分鐘2℃的升溫速率,在1300℃下保溫3小時(shí)進(jìn)行燒結(jié),然后隨爐冷卻至室溫。得到成品,檢測成品的力學(xué)性能,得到燒結(jié)試樣的界面結(jié)合強(qiáng)度達(dá)到30.1MPa。所得成品中金屬端的孔隙率為9%、陶瓷端的孔隙率為5%。實(shí)施例3步驟一配料取平均粒徑25μm的Co-Cr-Mo合金粉末為原料A,按原料A總質(zhì)量的15%配取石蠟,并將所配取的原料A與石蠟混合均勻,得到混合物A;原料A中Cr:28wt%、Mo:6wt%、Co:余量wt%;取平均粒徑50μm的ZrO2粉末為原料B,按原料B總質(zhì)量的0.1%配取石蠟,并將所配取的原料B與石蠟混合均勻,得到混合物B;步驟二成型用單向壓制的方法制備式樣,壓制壓力為400MPa。試樣為抗彎樣,尺寸長為42mm,寬為6mm,厚為4mm。制備壓制前,在上述模具的中部加入金屬薄片,在薄片兩側(cè)裝填混合物A和混合物B;步驟三燒結(jié)將壓坯試樣在真空度為10-2Pa的真空燒結(jié)爐中,以每分鐘2℃的升溫速率,在1450℃下保溫1.5小時(shí)進(jìn)行燒結(jié),然后隨爐冷卻至室溫。得到成品,檢測成品的力學(xué)性能,得到燒結(jié)試樣的界面結(jié)合強(qiáng)度達(dá)到31.2MPa。所得成品中金屬端的孔隙率為19%、陶瓷端的孔隙率為3.5%。實(shí)施例4步驟一配料取平均粒徑28μm的Co-Cr-Mo合金粉末為原料A,按原料A總質(zhì)量的10%配取石蠟,并將所配取的原料A與石蠟混合均勻,得到混合物A;原料A中Cr:28wt%、Mo:6wt%、Co:余量wt%;取平均粒徑55μm的ZrO2粉末為原料B,按原料B總質(zhì)量的0.1%配取石蠟,并將所配取的原料B與石蠟混合均勻,得到混合物B;步驟二成型用單向壓制的方法制備式樣,壓制壓力為450MPa。試樣為抗彎樣,尺寸長為42mm,寬為6mm,厚為4mm。制備壓制前,在上述模具的中部加入金屬薄片,在薄片兩側(cè)裝填混合物A和混合物B;步驟三燒結(jié)將壓坯試樣在真空度為10-2Pa的真空燒結(jié)爐中,以每分鐘2℃的升溫速率,在1450℃下保溫2小時(shí)進(jìn)行燒結(jié),然后隨爐冷卻至室溫。得到成品,檢測成品的力學(xué)性能,得到燒結(jié)試樣的界面結(jié)合強(qiáng)度達(dá)到38.5MPa。所得成品中金屬端的孔隙率為14.5%、陶瓷端的孔隙率為6%。實(shí)施例5步驟一配料取平均粒徑16μm的Co-Cr-Mo合金粉末為原料A,按原料A總質(zhì)量的8%配取石蠟,并將所配取的原料A與石蠟混合均勻,得到混合物A;原料A中Cr:28wt%、Mo:6wt%、Co:余量wt%;取平均粒徑65μm的ZrO2粉末為原料B,按原料B總質(zhì)量的0.1%配取石蠟,并將所配取的原料B與石蠟混合均勻,得到混合物B;步驟二成型用單向壓制的方法制備式樣,壓制壓力為450MPa。試樣為抗彎樣,尺寸長為42mm,寬為6mm,厚為4mm。制備壓制前,在上述模具的中部加入金屬薄片,在薄片兩側(cè)裝填混合物A和混合物B;步驟三燒結(jié)將壓坯試樣在真空度為10-2Pa的真空燒結(jié)爐中,以每分鐘2℃的升溫速率,在1400℃下保溫2小時(shí)進(jìn)行燒結(jié),然后隨爐冷卻至室溫。得到成品,檢測成品的力學(xué)性能,得到燒結(jié)試樣的界面結(jié)合強(qiáng)度達(dá)到32MPa。所得成品中金屬端的孔隙率為12.5%、陶瓷端的孔隙率為3.5%。對比例1取平均粒徑16μm的Co-Cr-Mo合金粉末為原料A,按原料A總質(zhì)量的2%配取石蠟,并將所配取的原料A與石蠟混合均勻,得到混合物A;原料A中Cr:28wt%、Mo:6wt%、Co:余量wt%;其他條件完全和實(shí)施例1一致,得到成品后檢測成品的力學(xué)性能,得到燒結(jié)試樣的界面結(jié)合強(qiáng)度達(dá)到15.6MPa。所得成品中金屬端的孔隙率為5.6%、陶瓷端的孔隙率為3.8%。對比例2取平均粒徑65μm的Co-Cr-Mo合金粉末為原料A,按原料A總質(zhì)量的1.5%配取石蠟,并將所配取的原料A與石蠟混合均勻,得到混合物A;取平均粒徑35μm的ZrO2粉末為原料B,按原料B總質(zhì)量的0.2%配取石蠟,并將所配取的原料B與石蠟混合均勻,得到混合物B;其他條件完全和實(shí)施例2一致,得到成品后檢測成品的力學(xué)性能,得到燒結(jié)試樣的界面結(jié)合強(qiáng)度達(dá)到12.7MPa。所得成品中金屬端的孔隙率為4.8%、陶瓷端的孔隙率為5.8%。對比例3步驟一配料取平均粒徑10μm的Co-Cr-Mo合金粉末為原料A,按原料A總質(zhì)量的20%配取石蠟,并將所配取的原料A與石蠟混合均勻,得到混合物A;原料A中Cr:27wt%、Mo:6wt%、Co:余量wt%;取平均粒徑50μm的ZrO2粉末為原料B,按原料B總質(zhì)量的0.2%配取石蠟,并將所配取的原料B與石蠟混合均勻,得到混合物B;步驟二成型用單向壓制的方法制備式樣,壓制壓力為700MPa。試樣為抗彎樣,尺寸長為42mm,寬為6mm,厚為4mm。制備壓制前,在上述模具的中部加入金屬薄片,在薄片兩側(cè)裝填混合物A和混合物B;步驟三燒結(jié)將壓坯試樣在真空度為10-2Pa的真空燒結(jié)爐中,以每分鐘10℃的升溫速率,在1650℃下保溫4小時(shí)進(jìn)行燒結(jié),然后隨爐冷卻至室溫。得到明顯變形且存在裂紋的殘次品,根本無法進(jìn)行力學(xué)性能數(shù)據(jù)的檢測。對比4步驟一配料取平均粒徑70μm的Co-Cr-Mo合金粉末為原料A,按原料A總質(zhì)量的0.5%配取石蠟,并將所配取的原料A與石蠟混合均勻,得到混合物A;原料A中Cr:27wt%、Mo:6wt%、Co:余量wt%;取平均粒徑70μm的ZrO2粉末為原料B,按原料B總質(zhì)量的0.2%配取石蠟,并將所配取的原料B與石蠟混合均勻,得到混合物B;步驟二成型用單向壓制的方法制備式樣,壓制壓力為100MPa。試樣為抗彎樣,尺寸長為42mm,寬為6mm,厚為4mm。制備壓制前,在上述模具的中部加入金屬薄片,在薄片兩側(cè)裝填混合物A和混合物B;步驟三燒結(jié)將壓坯試樣在真空度為10-2Pa的真空燒結(jié)爐中,以每分鐘1℃的升溫速率,在1000℃下保溫4小時(shí)進(jìn)行燒結(jié),然后隨爐冷卻至室溫。得到成品后檢測成品的力學(xué)性能,得到燒結(jié)試樣的界面結(jié)合強(qiáng)度達(dá)到13.2MPa。所得成品中金屬端的孔隙率為3.6%、陶瓷端的孔隙率為7.8%。對比例5步驟一配料取平均粒徑35μm的Co-Cr-Mo合金粉末為原料A,按原料A總質(zhì)量的6%配取石蠟,并將所配取的原料A與石蠟混合均勻,得到混合物A;原料A中Cr:28wt%、Mo:6wt%、Co:余量wt%;取平均粒徑65μm的ZrO2粉末為原料B,按原料B總質(zhì)量的0.1%配取石蠟,并將所配取的原料B與石蠟混合均勻,得到混合物B;步驟二成型用單向壓制的方法制備式樣,壓制壓力為600MPa。試樣為抗彎樣,尺寸長為42mm,寬為6mm,厚為4mm。制備壓制前,在上述模具的中部加入金屬薄片,在薄片兩側(cè)裝填混合物A和混合物B;步驟三燒結(jié)將壓坯試樣在真空度為10-1Pa的真空燒結(jié)爐中,以每分鐘2℃的升溫速率,在1100℃下保溫3小時(shí)進(jìn)行燒結(jié),然后隨爐冷卻至室溫。得到成品,檢測成品的力學(xué)性能,得到燒結(jié)試樣的界面結(jié)合強(qiáng)度達(dá)到18.5MPa。所得成品中金屬端的孔隙率為9%、陶瓷端的孔隙率為5%。