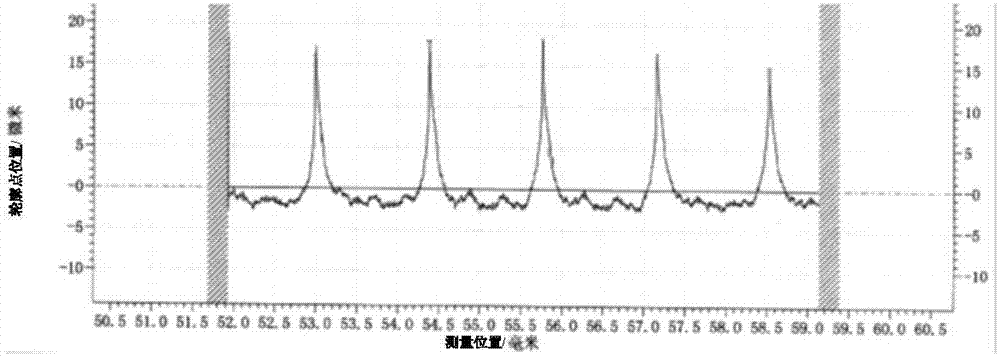
本實用新型涉及一種內(nèi)徑車刀。
背景技術(shù):
:軸承套圈的質(zhì)量對軸承的性能、壽命等均有較大的影響,因此對套圈的加工有較高要求。套圈的內(nèi)徑面采用車加工的方式,現(xiàn)有技術(shù)中,若要保證套圈的質(zhì)量,一般需要先利用粗加工刀具對其進行粗加工,后利用精加工刀具對其進行精加工,最后得到符合要求的零件。前期設備的投入較大,且其中涉及到多個流程,粗加工、精加工不能同步進行,加工成本高、效率低。技術(shù)實現(xiàn)要素:本實用新型要解決的技術(shù)問題是為了克服現(xiàn)有技術(shù)的內(nèi)徑面加工成本高、效率低的缺陷,提供一種能夠同時用于粗加工、精加工的內(nèi)徑車刀。本實用新型是通過下述技術(shù)方案來解決上述技術(shù)問題:一種內(nèi)徑車刀,其包括有刀柄以及與所述刀柄相連的刀頭,其特點在于,所述刀頭為球頭,所述球頭設有一刀刃,所述刀刃的第一端位于所述球頭遠離所述刀柄的端部的一側(cè),所述刀刃的第二端位于所述球頭靠近所述刀柄的位置。較佳地,所述刀刃由若干段相連的圓弧組成。較佳地,相鄰的兩所述圓弧相切,且若干段所述圓弧的半徑相同??梢愿鶕?jù)待加工工件的材質(zhì)、加工要求等選擇上述圓弧的半徑。較佳地,相鄰的兩所述圓弧相切,且若干段所述圓弧的半徑不同??梢愿鶕?jù)待加工工件的材質(zhì)、加工要求等對上述圓弧的半徑進行變化。較佳地,若干段所述圓弧的半徑從所述第一端至所述第二端逐漸變大。較佳地,所述刀柄為圓棒,所述球頭的球心位于所述圓棒的軸線上,所述圓棒與所述球頭之間設有一頸部,所述頸部的直徑小于所述球頭的直徑。采用上述設置,圓棒距球頭刀刃一定距離,可以避免對車削加工造成干擾。較佳地,所述球頭的球心到所述刀刃所在的平面的距離小于所述球頭的半徑的50%。上述距離過大,會導致刀刃所在平面截球頭所得的截面過小,不利于內(nèi)徑車刀的使用。具體的距離可以根據(jù)待加工工件的材質(zhì)、加工要求等進行選擇。較佳地,所述圓棒的軸線與所述刀刃所在的平面的夾角小于45°。上述夾角不宜過大,否則會導致切削阻力過大。具體的夾角可以根據(jù)待加工工件的材質(zhì)、加工要求等進行選擇。較佳地,所述圓棒的直徑大于所述球頭的直徑。采用上述設置,內(nèi)徑車刀的原材料可為圓棒料,球頭的加工要求高,刀柄的加工要求低,一般球頭的加工量大于刀柄的加工量。較佳地,所述內(nèi)徑車刀為碳化鎢車刀或陶瓷車刀。上述碳化鎢車刀、陶瓷車刀具有硬度高、耐磨性好的特點,上述內(nèi)徑車刀也可由其他市售可得的材料制成,具體的材料可根據(jù)待加工工件的材質(zhì)、加工要求等進行選擇。在符合本領(lǐng)域常識的基礎(chǔ)上,上述各優(yōu)選條件,可任意組合,即得本實用新型各較佳實例。本實用新型的積極進步效果在于:本實用新型公開的內(nèi)徑車刀設有球頭結(jié)構(gòu),刀刃位于球頭,靠近第一端的刀刃可用作粗加工刀刃,與粗加工刀刃緊鄰的、更靠近第二端的刀刃可用作精加工刀刃;可以將粗加工、精加工在單個刀具上完成,簡化加工流程、節(jié)省加工成本、提高加工效率。附圖說明圖1為本實用新型較佳實施例的內(nèi)徑車刀對工件進行車削加工時的示意圖。圖2為現(xiàn)有技術(shù)的粗加工刀具加工后的樣本一的內(nèi)徑面表面粗糙度輪廓坐標圖。圖3為現(xiàn)有技術(shù)的粗加工刀具加工后的樣本二的內(nèi)徑面表面粗糙度輪廓坐標圖。圖4為現(xiàn)有技術(shù)的粗加工刀具加工后的樣本三的內(nèi)徑面表面粗糙度輪廓坐標圖。圖5為現(xiàn)有技術(shù)的精加工刀具加工后的樣本一的內(nèi)徑面表面粗糙度輪廓坐標圖。圖6為現(xiàn)有技術(shù)的精加工刀具加工后的樣本二的內(nèi)徑面表面粗糙度輪廓坐標圖。圖7為現(xiàn)有技術(shù)的精加工刀具加工后的樣本三的內(nèi)徑面表面粗糙度輪廓坐標圖。圖8為本實用新型較佳實施例的內(nèi)徑車刀加工后的樣本一的內(nèi)徑面表面粗糙度輪廓坐標圖。圖9為本實用新型較佳實施例的內(nèi)徑車刀加工后的樣本二的內(nèi)徑面表面粗糙度輪廓坐標圖。圖10為本實用新型較佳實施例的內(nèi)徑車刀加工后的樣本三的內(nèi)徑面表面粗糙度輪廓坐標圖。附圖標記說明:10:內(nèi)徑車刀11:刀柄12:刀頭13:刀刃14:頸部15:錐面20:工件21:內(nèi)徑面30:車刀前進方向具體實施方式下面舉個較佳實施例,并結(jié)合附圖來更清楚完整地說明本實用新型。如圖1所示,一種內(nèi)徑車刀10,其包括有刀柄11以及與刀柄11相連的刀頭12,刀頭12為球頭,球頭設有一刀刃13,刀刃13的第一端位于球頭遠離刀柄11的端部的一側(cè),刀刃13的第二端位于球頭靠近刀柄11的位置。刀刃13由若干段相連的圓弧組成。本實施例中,相鄰的兩圓弧相切,且若干段圓弧的半徑相同。另一實施例中,相鄰的兩圓弧可相切,且若干段圓弧的半徑可不同。不同半徑的圓弧可通過對球頭表面不同程度的研磨實現(xiàn)。再一實施例中,若干段圓弧的半徑可從第一端至第二端逐漸變大。刀柄11為圓棒,球頭的球心位于圓棒的軸線上,圓棒與球頭之間設有一頸部14,頸部14的直徑小于球頭的直徑。圓棒的直徑大于球頭的直徑。圓棒與頸部14之間可通過一錐面15連接,錐面15與圓棒的外周面的夾角為30°。其他實施例中,錐面15與圓棒的外周面的夾角也可設置成其他角度。球頭的球心到刀刃13所在的平面的距離小于球頭的半徑的50%。圓棒的軸線與刀刃13所在的平面的夾角小于45°。本實施例中,內(nèi)徑車刀10為碳化鎢車刀。其他實施例中,內(nèi)徑車刀10也可為其他硬質(zhì)合金車刀,或陶瓷車刀或由其他市售可得的材料制成。本內(nèi)徑車刀10可以使用簡易的工具磨床進行研磨制作,易于標準化大量制造,制作人員不需具備特殊操作技巧或經(jīng)驗,可以降低人工成本。使用鈍化后可經(jīng)過簡易的研磨方式進行刀刃再生,再生后刀具擁有相同的切削能力,可降低刀具成本。再次參照圖1,使用時,內(nèi)徑車刀10安裝于固定架,固定架的滑動臺前進時會帶動車刀一并沿車刀前進方向30前進,靠近第一端的刀刃13用作粗加工刀刃,其先與待加工工件20接觸,進行大切削量的粗加工,將內(nèi)徑面21的不平整材料或氧化皮膜切除,并在工件20上形成粗加工內(nèi)徑面;與粗加工刀刃緊鄰的、更靠近第二端的刀刃13用作精加工刀刃,粗加工刀刃經(jīng)過后,精加工刀刃會與粗加工內(nèi)徑面接觸,進行小切削量的精加工,降低粗加工內(nèi)徑面的表面粗糙度及加工紋路深度,形成符合要求的精加工內(nèi)徑面。用粗加工刀具、精加工刀具以及本實施例的內(nèi)徑車刀對軸承套圈進行加工(其他加工條件均保持一致),并分別選取三個樣本,所測得表面粗糙度結(jié)果示意圖分別如圖2-4、圖5-7、如8-10所示,具體數(shù)據(jù)分別如下表1、表2、表3所示。其中Ra為輪廓的算術(shù)平均偏差,Rt為輪廓的總高度,表中它們的單位均為μm。表1粗加工刀具加工后的內(nèi)徑面表面粗糙度測量結(jié)果數(shù)據(jù)測量值樣本1樣本2樣本3平均值Ra2.20622.30172.44002.3160Rt21.074822.549520.532821.3857表2精加工刀具加工后的內(nèi)徑面表面粗糙度測量結(jié)果數(shù)據(jù)測量值樣本1樣本2樣本3平均值Ra1.48591.39991.47261.4528Rt7.66647.23768.43687.7803表3本實施例的內(nèi)徑車刀加工后的內(nèi)徑面表面粗糙度測量結(jié)果數(shù)據(jù)測量值樣本1樣本2樣本3平均值Ra1.46711.42231.45431.4479Rt11.271310.22479.902510.4661以上數(shù)據(jù)證明,本實施例的內(nèi)徑車刀加工后的內(nèi)徑面Ra可以達到單獨精加工的標準,Rt相比單獨精加工略有所欠缺,但比之粗加工結(jié)果已經(jīng)有很大的改善,故本內(nèi)徑車刀將粗加工、精加工結(jié)合在一起,能夠在保證質(zhì)量的前提下提高加工效率。雖然以上描述了本實用新型的具體實施方式,但是本領(lǐng)域的技術(shù)人員應當理解,這僅是舉例說明,本實用新型的保護范圍是由所附權(quán)利要求書限定的。本領(lǐng)域的技術(shù)人員在不背離本實用新型的原理和實質(zhì)的前提下,可以對這些實施方式做出多種變更或修改,但這些變更和修改均落入本實用新型的保護范圍。當前第1頁1 2 3