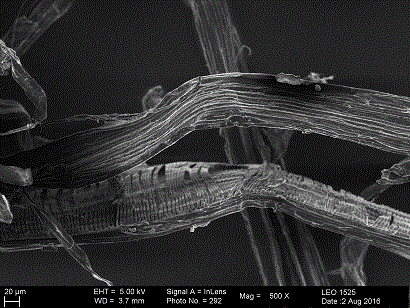
本發(fā)明屬于新型天然纖維材料領(lǐng)域,具體涉及天然纖維的提取、制備工藝,特別涉及蓮纖維的制備工藝。
背景技術(shù):
:由于人們對(duì)健康和環(huán)保越來越多的關(guān)注,綠色安全、環(huán)境友好型紡織面料的需求逐年增加。天然植物纖維具有健康安全、資源可再生、易降解等特性,因此為公認(rèn)的綠色環(huán)保材料。天然植物纖維材料親水性好、不起球、抗靜電、舒適透氣,是倍受青睞的服裝面料。目前,棉、麻、竹等天然植物纖維的生產(chǎn)已經(jīng)非常成熟。蓮又稱荷、芙蕖等,在中國、緬甸、泰國等亞洲種植廣泛,目前,主要作為食用、藥用、觀賞等。每年都有大量的蓮桿作為農(nóng)業(yè)廢棄物處理,造成資源的極大浪費(fèi)。蓮纖維是新型天然植物纖維,在藕和蓮葉桿中含量較多。蓮纖維織物穿著舒適、吸濕透氣,是理想的夏季面料。緬甸是最早使用蓮纖維制作服飾的國家之一,當(dāng)?shù)刂饕ㄟ^手工方式從蓮葉桿中提取天然蓮纖維用于制作佛教袈裟等宗教用品。有研究通過生物發(fā)酵,堿煮等方法與傳統(tǒng)手工抽取相結(jié)合,成功提取出蓮纖維,但生產(chǎn)效率比直接手工抽取纖維并無明顯提高。也有研究將干蓮桿生物浸泡脫膠后,采用手工方式分離纖維和表皮,然后采用堿煮對(duì)纖維脫膠處理,制得細(xì)度為25dtex左右的精制蓮纖維,其制備的纖維在形貌和性能上和手工抽取的蓮纖維有較大差異。綜上所述,目前蓮纖維的生產(chǎn)工藝主要存在纖維質(zhì)量參差不齊、性狀差異大、生產(chǎn)勞動(dòng)強(qiáng)度大、人工成本高等問題。直接手工抽取或者生物發(fā)酵、堿煮預(yù)處理后再手工抽取兩種方法雖然可以很好的分離蓮桿表皮,但是生產(chǎn)效率較低。通過堿煮脫膠生產(chǎn)蓮纖維,獲得的蓮纖維粗糙,性能較差,并且手工剝離表皮的方式仍然不利于提高生產(chǎn)效率。本發(fā)明設(shè)計(jì)的聯(lián)合法制備蓮纖維工藝,處理蓮桿的過程中,通過化學(xué)、機(jī)械等方式,在超聲波輔助下,即除去果膠、木質(zhì)素等雜質(zhì),又有效的破壞并去除了表皮組織,得到較純的蓮纖維。該工藝無需人工抽取纖維和分離表皮,有利于提高生產(chǎn)效率,縮短生產(chǎn)周期。技術(shù)實(shí)現(xiàn)要素:本發(fā)明的目的是提供一種聯(lián)合法制備蓮纖維工藝,所述制備工藝有效分離去除果膠、表皮雜質(zhì),溶解去除纖維中所含過多木質(zhì)素,提高蓮纖維制備效率,并獲得具有較好可紡性能的蓮纖維。本發(fā)明的技術(shù)方案:本發(fā)明提供一種聯(lián)合法制備蓮纖維的新方法,采用強(qiáng)堿,亞氯酸鹽、冰乙酸,輔以機(jī)械設(shè)備處理蓮桿,處理過程分別在油浴或超聲波環(huán)境中進(jìn)行。蓮桿經(jīng)過化學(xué)除雜、表皮處理、粗纖維處理、機(jī)械分離、洗滌過濾、上油開松工序獲得蓮纖維。所述蓮桿包括蓮葉桿、蓮花桿、藕中的至少一種。優(yōu)選的,所述蓮桿為蓮葉桿。所述強(qiáng)堿為氫氧化鈉、氫氧化鉀、氫氧化鋇中的至少一種。優(yōu)選的,所述強(qiáng)堿為氫氧化鈉或氫氧化鉀。所述的聯(lián)合法制備蓮纖維工藝,所述亞氯酸鹽為亞氯酸鈉、亞氯酸鈣、亞氯酸鉀中的至少一種。聯(lián)合法制備蓮纖維工藝具體步驟如下:a、蓮桿清洗,曬干,剪為相同長度;b、加入強(qiáng)堿、硅酸鈉、三聚磷酸鈉處理蓮桿;c、將步驟b所得樣品通過機(jī)械擠壓分離出粗纖維和蓮桿表皮,多次洗滌,并用孔徑為2mm的篩子過濾,重復(fù)該步操作,直至濾液中性,且無沉淀,收集粗蓮纖維和表皮混合樣品;d、將步驟c中的粗蓮纖維和蓮桿表皮混合樣品用亞氯酸鹽、冰乙酸處理,破壞表皮組織,且從粗蓮纖維的維管束中分離出蓮纖維;e、將步驟d中得到的樣品用蒸餾水浸泡洗滌至中性,反復(fù)機(jī)械擠壓樣品,使表皮破壞為碎屑,用孔徑為2mm篩子沖洗過濾,洗去碎屑,獲得純蓮纖維樣品;f、將e中獲得樣品干燥、上油、開松,獲得蓮纖維。優(yōu)選的,上述步驟b中,具體實(shí)施方法為:配置0~25g/L的強(qiáng)堿溶液,加入2~4g/L硅酸鈉、1~3g/L三聚磷酸鈉,加入蓮桿,在一定溫度下反應(yīng)一定時(shí)間。步驟d中,具體步驟為:稱取4~12g亞氯酸鹽,加入1200~2000mL蒸餾水溶解得亞氯酸鹽溶液,加入步驟c得到的粗蓮纖維和表皮混合樣品6~14g,加入2~8mL冰乙酸,在一定溫度下反應(yīng)一定時(shí)間。步驟b、d中,反應(yīng)過程選擇在油浴中進(jìn)行,步驟b中,反應(yīng)溫度為70~100℃,反應(yīng)時(shí)間為1~6h。步驟d中,反應(yīng)溫度為60~80℃,反應(yīng)時(shí)間為1~4h。步驟b、d中,反應(yīng)過程在超聲波環(huán)境下進(jìn)行,步驟b中,反應(yīng)溫度為60~80℃,反應(yīng)時(shí)間為20~60min,功率為100~160W。步驟d中,反應(yīng)溫度為60~80℃,反應(yīng)時(shí)間為20~80min,功率為100~160W。本發(fā)明的有益效果:(1)聯(lián)合法制備蓮纖維工藝使用化學(xué)試劑價(jià)格低廉,工藝流程簡(jiǎn)單易操作,生產(chǎn)周期短,人工成本低,具有工業(yè)化前景;(2)聯(lián)合法制備蓮纖維工藝有效除去雜質(zhì)(果膠、木質(zhì)素、蓮桿表皮等),除雜率為85%以上,并且成功從維管束組織中獲得直徑為3um~6um的蓮纖維;(3)聯(lián)合法制備蓮纖維工藝有效的除去蓮桿表皮,無需人工分離,提高生產(chǎn)效率,縮短了生產(chǎn)周期;(4)工藝過程中,結(jié)合超聲波,對(duì)雜質(zhì)去除、纖維提取有促進(jìn)作用,為蓮纖維提取工藝提供新的技術(shù)途徑。附圖說明圖1為聯(lián)合法制備蓮纖維法獲得蓮纖維樣品。由圖可見,該方法獲得蓮纖維潔白柔軟,外觀形貌類似棉纖維。圖2為強(qiáng)堿處理后獲得纖維樣品的掃描電鏡圖。由圖2可見,堿處理后的粗蓮纖維樣品中含有維管束組織,蓮纖維被包裹在里面。樣品表面也含有較多的雜質(zhì)。圖3為亞氯酸鹽、冰乙酸處理后獲得蓮纖維樣品的掃描電鏡圖(放大5000倍)。由圖3可見,經(jīng)過亞氯酸鹽處理后的纖維樣品多以多根纖維組成扁平復(fù)絲結(jié)構(gòu)出現(xiàn),并含有部分單纖維,單根蓮纖維的直徑4um左右,纖維表面雜質(zhì)少。圖4為本發(fā)明實(shí)施例1所制備的蓮纖維的一次拉伸曲線。具體實(shí)施方式本發(fā)明提供一種聯(lián)合法制備蓮纖維工藝,為了使本發(fā)明的技術(shù)方案更加明確,下面結(jié)合具體的實(shí)施例對(duì)本方案作進(jìn)一步的說明。本發(fā)明提供一種聯(lián)合法制備蓮纖維的新方法,采用強(qiáng)堿,亞氯酸鹽、冰乙酸,輔以機(jī)械設(shè)備處理蓮桿,處理過程分別在油浴或超聲波環(huán)境中進(jìn)行。蓮桿經(jīng)過化學(xué)除雜、表皮處理、粗纖維處理、機(jī)械分離、洗滌過濾、上油開松工序獲得蓮纖維。所述蓮桿包括蓮葉桿、蓮花桿、藕中的至少一種。優(yōu)選的,所述蓮桿為蓮葉桿。因?yàn)樯徣~桿產(chǎn)量多,且目前作為農(nóng)田廢棄物處理,選擇蓮葉桿可以節(jié)約資源,變廢為寶。所述強(qiáng)堿為氫氧化鈉、氫氧化鉀、氫氧化鋇中的至少一種。優(yōu)選的,所述強(qiáng)堿為氫氧化鈉或氫氧化鉀。所述的聯(lián)合法制備蓮纖維工藝,所述亞氯酸鹽為亞氯酸鈉、亞氯酸鈣、亞氯酸鉀中的至少一種。聯(lián)合法制備蓮纖維工藝具體步驟如下:a、蓮桿清洗,曬干,剪為相同長度;b、加入強(qiáng)堿、硅酸鈉、三聚磷酸鈉處理蓮桿;c、將步驟b所得樣品通過機(jī)械擠壓分離出粗纖維和蓮桿表皮,多次洗滌,并用孔徑為2mm的篩子過濾,重復(fù)該步操作,直至濾液中性,且無沉淀,收集粗蓮纖維和表皮混合樣品;d、將步驟c中的粗蓮纖維和蓮桿表皮混合樣品用亞氯酸鹽、冰乙酸處理,破壞表皮組織,且從粗蓮纖維的維管束中分離出蓮纖維;e、將步驟d中得到的樣品用蒸餾水浸泡洗滌至中性,反復(fù)機(jī)械擠壓樣品,使表皮破壞為碎屑,用孔徑為2mm篩子沖洗過濾,洗去碎屑,獲得純蓮纖維樣品;f、將e中獲得樣品干燥、上油、開松,獲得蓮纖維。優(yōu)選的,上述步驟b中,具體實(shí)施方法為:配置0~25g/L的強(qiáng)堿溶液,加入2~4g/L硅酸鈉、1~3g/L三聚磷酸鈉,加入蓮桿,在一定溫度下反應(yīng)一定時(shí)間。步驟d中,具體步驟為:稱取4~12g亞氯酸鹽,加入1200~2000mL蒸餾水溶解得亞氯酸鹽溶液,加入步驟c得到的粗蓮纖維和表皮混合樣品6~14g,加入2~8mL冰乙酸,在一定溫度下反應(yīng)一定時(shí)間。步驟b、d中,反應(yīng)過程在油浴中反應(yīng),步驟b中,反應(yīng)溫度為70~100℃,反應(yīng)時(shí)間為1~6h。步驟d中,反應(yīng)溫度為60~80℃,反應(yīng)時(shí)間為1~4h。步驟b、d中,反應(yīng)過程在超聲波環(huán)境下進(jìn)行,步驟b中,反應(yīng)溫度為60~80℃,反應(yīng)時(shí)間為20~60min,功率為100~160W。步驟d中,反應(yīng)溫度為60~80℃,反應(yīng)時(shí)間為20~80min,功率為100~160W。本發(fā)明制備具有較好可紡性的精制蓮纖維,其外觀形貌見圖1,蓮纖維外觀潔白,柔軟蓬松。下面通過實(shí)施例對(duì)本發(fā)明進(jìn)行具體描述,有必要指出的是實(shí)施例只用于對(duì)本發(fā)明的進(jìn)一步說明,不能理解為對(duì)本發(fā)明保護(hù)范圍的限制,該
技術(shù)領(lǐng)域:
的技術(shù)人員可以根據(jù)本發(fā)明作出一些非本質(zhì)的改進(jìn)和調(diào)整。實(shí)施例1稱取20g干蓮桿,整理成5cm長的小段。配制1L濃度為20g/L的氫氧化鈉溶液,加入3g硅酸鈉和2g三聚磷酸鈉。在90℃油浴4h。反應(yīng)完成后取出樣品,用蒸餾水洗滌3次,然后用蒸餾水浸泡3h。取出樣品,通過機(jī)械擠壓作用,洗去蓮桿纖維與表皮間的組織,用孔徑2mm篩子沖洗去除沉淀等雜質(zhì),重復(fù)該操作,直至濾液為中性,濾液中沉淀基本消失為止,樣品在60℃烘干24h。將樣品稱重,按照每克樣品12g亞氯酸鈉、6mL冰乙酸加入藥品,加入蒸餾水,密封容器,在70℃油浴3h。將樣品用蒸餾水洗滌至中性,通過機(jī)械擠壓作用,壓碎表皮組織,用孔徑2mm的篩子沖洗去掉碎屑,留下蓮纖維樣品,在60℃烘干24h。用上油劑上油,開松,制備得到蓮纖維。表1樣品的雜質(zhì)去除率,在堿液處理后,雜質(zhì)去除率達(dá)到60.29%,通過亞氯酸鹽處理后,雜質(zhì)去除率達(dá)到91.56%。圖2和圖3分別為亞氯酸鹽處理前后,被維管束包裹的蓮纖維和已經(jīng)從維管束中分離出來的蓮纖維掃描電鏡圖。從圖中可以看出,亞氯酸鹽處理后,蓮桿中的雜質(zhì),包括果膠、表皮等被有效去除,維管束組織被破壞并從中成功分離出單根蓮纖維或者多根蓮纖維的復(fù)絲結(jié)構(gòu)。圖4為蓮纖維的應(yīng)力應(yīng)變曲線,可以從圖得出蓮纖維屬于脆性斷裂,無屈服出現(xiàn),力學(xué)特征近似棉、麻等天然纖維。表1傳統(tǒng)加熱方式樣品雜質(zhì)去除率樣品強(qiáng)堿處理樣品(%)亞氯酸鹽處理樣品(%)除雜率60.2991.56實(shí)施例2稱取20g干蓮桿,整理成5cm長的小段。配制1L濃度為20g/L的氫氧化鈉溶液,加入3g硅酸鈉和2g三聚磷酸鈉。設(shè)置超聲波功率為140W,在70℃超聲30min。反應(yīng)完成后取出樣品,用蒸餾水洗滌3次,然后用蒸餾水浸泡3h。取出樣品,通過機(jī)械擠壓作用,洗去蓮桿纖維與表皮間的組織,用孔徑2mm篩子沖洗去除沉淀等雜質(zhì),重復(fù)該操作,直至濾液為中性,濾液中沉淀基本消失為止,樣品在60℃烘干24h。將樣品稱重,按照每克樣品12g亞氯酸鈉、6mL冰乙酸加入藥品,加入蒸餾水,密封容器,設(shè)置超聲波功率為140W,60℃水浴加熱20min。將樣品用蒸餾水洗滌至中性,通過機(jī)械擠壓作用,壓碎表皮組織,用孔徑2mm的篩子沖洗去掉碎屑,留下蓮纖維樣品,在60℃烘干24h。用上油劑上油,開松,制備獲得蓮纖維。表2是相同反應(yīng)條件下,超聲波處理樣品的雜質(zhì)去除率,堿處理后,樣品的雜質(zhì)去除率為43.09%,經(jīng)過亞氯酸鹽脫木質(zhì)素、去表皮后,雜質(zhì)去除率達(dá)到89.20%。表2超聲波條件下樣品的雜質(zhì)去除率樣品堿處理樣品(%)亞氯酸鹽處理樣品(%)雜質(zhì)去除率43.0989.20當(dāng)前第1頁1 2 3