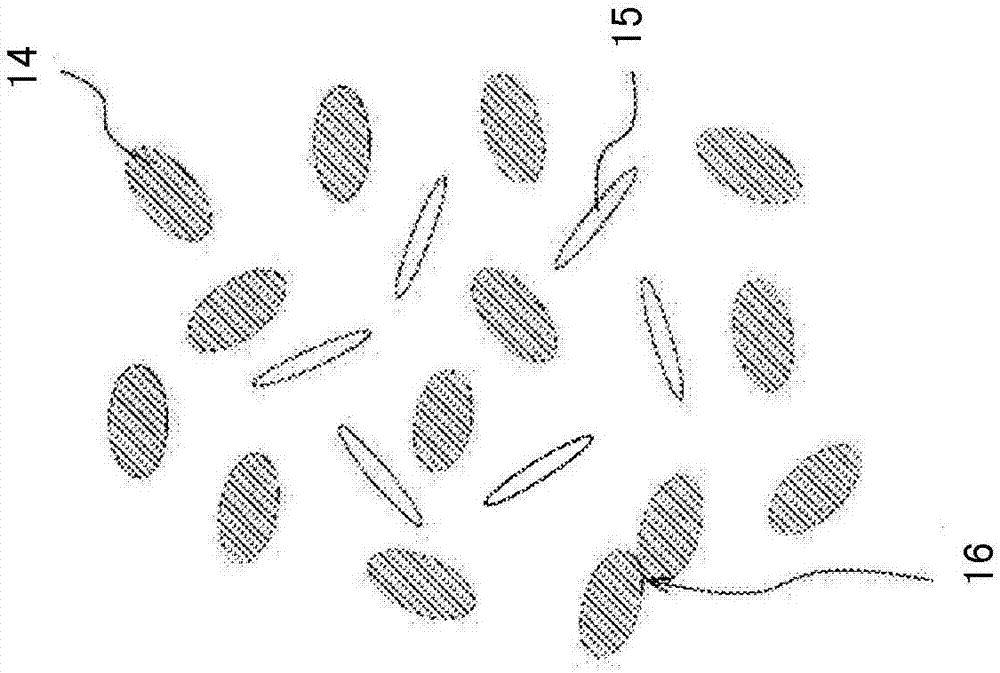
本發(fā)明涉及用于各種工業(yè)機(jī)械的往復(fù)滑動部的滑動部件。
背景技術(shù):
:迄今使用的是添加了石墨作為潤滑成分的銅系滑動部件。例如,jp2000-309807a中記載,在被覆有銅合金層的銅系滑動部件中,通過向銅合金層中添加75~900μm的大粒徑石墨,銅合金層中石墨粉末的數(shù)量減少,銅合金形成網(wǎng)絡(luò),籍此能夠得到比以往添加了小粒徑石墨的銅合金的強(qiáng)度更高的滑動部件。另外,jp2002-285262a中記載,在被覆有銅合金層的銅系滑動部件中,通過使銅合金層中含有作為潤滑成分的bi或石墨等固體潤滑劑,石墨等固體潤滑劑被bi包圍而作為共存相分散在燒結(jié)銅合金中,籍此提高滑動部件的強(qiáng)度。技術(shù)實(shí)現(xiàn)要素:在上述現(xiàn)有技術(shù)專利文獻(xiàn)的銅系滑動部件中,如圖4a所示,銅合金等金屬部24形成網(wǎng)絡(luò),固體潤滑劑25以被該金屬部包圍的島狀形態(tài)分散在金屬中。于是,在將上述現(xiàn)有技術(shù)專利文獻(xiàn)的銅系滑動部件適用于往復(fù)滑動部的場合下,首先,在進(jìn)行往復(fù)滑動的對象部件27的滑動方向改變的瞬間,對象部件的表面與銅系滑動部件的滑動面之間的相對速度成為0。此時(shí),銅系滑動部件的滑動層僅從對象部件受到與滑動層厚度方向平行的負(fù)荷。隨后,如圖4b所示,在從對象部件27的運(yùn)動開始的瞬間至轉(zhuǎn)變成動摩擦狀態(tài)(銅系滑動部件的滑動面與對象部件之間的兩個(gè)表面間發(fā)生滑動(滑行)的狀態(tài))的這段時(shí)間內(nèi),銅系滑動部件的滑動層23由于沿對象部件的運(yùn)動方向(箭頭方向)的負(fù)荷而發(fā)生彈性形變,在兩個(gè)表面間不發(fā)生滑動(滑行)。在該場合下,用于使銅系滑動部件的滑動面與對象部件之間的兩個(gè)表面間發(fā)生滑動(滑行)的力(起動力)也包括滑動層的彈性形變所需要的力。從而,在像上述現(xiàn)有技術(shù)專利文獻(xiàn)所述那樣的滑動層的銅合金24形成網(wǎng)絡(luò)的場合(圖4a)下,由于形變?nèi)菀讉鞑ブ零~合金的整個(gè)網(wǎng)絡(luò),因此滑動層23的彈性形變量變大,從而使起動力變大。換言之,銅系滑動部件的滑動面與對象部件之間的靜摩擦系數(shù)變大。因此,在銅系滑動部件的滑動面與對象部件之間的兩個(gè)表面間發(fā)生滑動(滑行)的瞬間,對這兩個(gè)表面施加了大摩擦力,容易在滑動層23的表面上引起磨耗。本發(fā)明是鑒于上述情況而完成的發(fā)明,其目的在于提供一種與對象部件之間的靜摩擦系數(shù)低、適合在往復(fù)滑動部中使用的滑動部件。為了實(shí)現(xiàn)上述目的,本發(fā)明的滑動部件包含鋼背層和該鋼背層上的具有滑動面的滑動層,所述滑動層由20~40體積%的石墨和其余部分的銅合金構(gòu)成,所述銅合金含有1~15質(zhì)量%的sn,其余部分由銅和不可避免的雜質(zhì)構(gòu)成,所述滑動層包含以被所述石墨包圍的海島結(jié)構(gòu)的形態(tài)分散在銅合金基質(zhì)中的島狀銅合金部,所述島狀銅合金部包含與所述滑動面平行的方向上的長度為25~500μm的島狀銅合金部,與所述滑動面平行的方向上的長度為25~500μm的島狀銅合金部相對于所述滑動層的比例為5~40體積%。通過這種構(gòu)成,能夠得到與對象部件之間的靜摩擦系數(shù)低、適合在往復(fù)滑動部中使用的滑動部件。根據(jù)本發(fā)明的一具體例,與所述滑動面平行的方向上的長度為25~500μm的島狀銅合金部中縱橫比為1.2~5的島狀銅合金部的比例可在50體積%以上,所述縱橫比定義為與所述滑動面平行的方向上的長度x和與所述滑動面垂直的方向上的長度y之比(x/y)。通過使與所述滑動面平行的方向上的長度為25~500μm的島狀銅合金部中縱橫比為1.2~5的島狀銅合金部比例在50體積%以上,能夠進(jìn)一步降低滑動部件與對象部件之間的靜摩擦系數(shù)。這是由于島狀銅合金部的顆粒的形狀在與滑動面平行的方向上具有稍長的各向異性。即,由于對象部件在與滑動部件的滑動面水平的方向上進(jìn)行往復(fù)滑動,因此島狀銅合金部在與滑動面平行的方向上為稍長的形狀使得島狀銅合金部與石墨之間容易發(fā)生滑動。因此,與對象部件之間的靜摩擦系數(shù)降低。本發(fā)明的一具體例中,可使銅合金含有1~15質(zhì)量%的ni、0.01~0.5質(zhì)量%的p中的至少一種以上。即使銅合金中含有這些元素,也能夠由滑動層中的島狀銅合金部充分發(fā)揮出降低與對象部件之間靜摩擦系數(shù)的效果。此外,也可以使銅合金還含有1~10質(zhì)量%的pb和bi中的至少一種以上。pb、bi是潤滑成分,且具有降低滑動層進(jìn)行動摩擦?xí)r動摩擦系數(shù)的效果,但如果pb和bi中的至少一種以上的含量小于1質(zhì)量%,則該效果不充分。而如果pb和bi中的至少一種以上的含量超過10質(zhì)量%,則滑動層會變脆。本發(fā)明的一具體例中,銅合金還可包含最多5質(zhì)量%的mo2c這樣的硬質(zhì)粒子。下面,參照所附的示意圖對本發(fā)明的構(gòu)成及其多種優(yōu)點(diǎn)進(jìn)行詳細(xì)說明。展示附圖的目的僅在于例示非限定性的實(shí)施例。附圖的簡要說明圖1是顯示本發(fā)明一例的包含島狀銅合金部的滑動部件的示意圖。圖2a~c是用于對本發(fā)明滑動部件的滑動層的制造工序中島狀銅合金部的形成進(jìn)行說明的圖,圖2a顯示了散布層(散布時(shí))的剖面,圖2b顯示了一次燒結(jié)后的燒結(jié)層的剖面,圖2c顯示了軋制后的燒結(jié)層的剖面。圖3a~c是散布時(shí)空孔率少的場合下的與圖2a~c相對應(yīng)的圖,圖3a顯示了散布層(散布時(shí))的剖面,圖3b顯示了一次燒結(jié)后的燒結(jié)層的剖面,圖3c顯示了軋制后的燒結(jié)層的剖面。圖4a和4b是對添加了以往固體潤滑劑的滑動部件的摩擦發(fā)生機(jī)理進(jìn)行說明的圖。發(fā)明詳述本發(fā)明一具體例的滑動部件1示于圖1?;瑒硬考?在背層2上具有滑動層3,滑動層1包含銅合金4和石墨5。銅合金4包含銅合金基質(zhì)41和以被石墨5包圍的海島結(jié)構(gòu)的形態(tài)分散在銅合金基質(zhì)41中的島狀銅合金部42。與滑動面6平行的方向上的長度為25~500μm的島狀銅合金部42相對于滑動層3的比例為5~40體積%。如果是該比例,則能夠降低與對象部件(未圖示)之間的靜摩擦系數(shù)。這推測是由于以下機(jī)理而達(dá)成的。在將本發(fā)明的滑動部件1適用于往復(fù)滑動部的場合下,首先,在進(jìn)行往復(fù)滑動的對象部件的滑動方向改變的瞬間,對象部件的表面與滑動部件1的滑動面6之間的相對速度成為0。隨后,在從對象部件的運(yùn)動開始的瞬間至轉(zhuǎn)變?yōu)閯幽Σ翣顟B(tài)(滑動部件1的滑動面6與對象部件之間的兩個(gè)表面間發(fā)生滑動(滑行)的狀態(tài))的這段時(shí)間內(nèi),滑動部件1的滑動層3受到沿對象部件的運(yùn)動方向上的負(fù)荷,但如圖1所示,由于島狀銅合金部42的周圍被石墨5包圍,因此與石墨5的界面處發(fā)生滑動,所以島狀銅合金部42本身僅發(fā)生微小的彈性形變。另外,即使島狀銅合金部42發(fā)生微小的彈性形變,其也會被周圍的石墨6阻斷,不會傳播至其它島狀銅合金部42和島狀銅合金部以外的形態(tài)的銅合金基質(zhì)41(部分形成了網(wǎng)絡(luò)的銅合金部分)處。此外,存在于銅合金基質(zhì)41之間的島狀銅合金部42及其周圍的石墨6能夠抑制銅合金基質(zhì)41內(nèi)的彈性形變。因此,滑動層3的彈性形變量變小,滑動層3上所施加的起動時(shí)的摩擦力變小。換言之,本發(fā)明的滑動部件1的滑動層3與對象部件之間的靜摩擦系數(shù)降低。此外,與滑動面6平行的方向上的長度為25~500μm的島狀銅合金部42相對于滑動層3的比例為5~40體積%,如果該比例小于5體積%,則降低滑動層3的彈性形變量的效果不充分,與對象部件之間的靜摩擦系數(shù)變大。而在島狀銅合金部42的比例大于40體積%的場合下,下文所述的一次燒結(jié)后的燒結(jié)層的強(qiáng)度會變得過低,因此燒結(jié)層會在軋制時(shí)破損,無法制作本發(fā)明的滑動部件。此外,滑動部件1的滑動層3中所包含的島狀銅合金部42不僅包含與滑動面平行的方向上的長度為25~500μm的島狀銅合金部,還可以少量(相對于滑動層在5體積%以下)包含與滑動面平行的方向上的長度小于25μm的島狀銅合金部或者長度大于500μm的島狀銅合金部。此外,島狀銅合金部42相對于滑動層3的體積比例難以直接測定,但可通過測定島狀銅合金部42的面積相對于與滑動面6垂直的方向上滑動層3的剖面結(jié)構(gòu)中滑動層3的面積的比例來確定。另外,本發(fā)明中,島狀銅合金部42的與滑動面6平行的方向上的長度是指當(dāng)沿著滑動方向觀察與滑動面6垂直的方向上滑動層3的剖面組織時(shí)島狀銅合金部42的與滑動面平行的方向上的長度。另外,石墨5作為潤滑成分包含在滑動層中,而且,也與以被石墨5包圍的海島結(jié)構(gòu)的形態(tài)分散在滑動層中的島狀銅合金部42的形成有關(guān)。如果滑動層3中石墨5的含量小于20體積%,則以被石墨5包圍的形態(tài)分散在滑動層3中的島狀銅合金部42的形成變得不充分。而如果滑動層3中石墨5的含量大于40體積%,則滑動層3會變脆。另外,滑動層3中的銅合金含有1~15質(zhì)量%的sn。sn具有提高銅合金強(qiáng)度的效果,如果sn的含量小于1質(zhì)量%,則該效果不充分。而如果sn的含量大于15質(zhì)量%,則銅合金會變脆。銅合金還可含有以下中的至少一種:1~15質(zhì)量%的ni、0.01~0.5質(zhì)量%的p、1~10質(zhì)量%的pb和bi中的一種或兩種,還可含有最多5質(zhì)量%的mo2c等硬質(zhì)粒子。下面,參照圖2a~c和圖3a~c對本發(fā)明一具體例的滑動部件進(jìn)行說明。本具體例的滑動部件的滑動層的制造工序按照粉末制作、粉末混合、散布、一次燒結(jié)、一次軋制,二次燒結(jié)的順序進(jìn)行。首先,利用水霧化法(水アトマイズ法)制作平均粒徑d50為25~50μm的銅合金粉末。平均粒徑d50是指利用激光衍射·散射方式進(jìn)行的粒度分布測試中累計(jì)體積50%的粒徑。另外,利用水霧化法制成的粉末是異形粉(非球形形狀的粉末)。然后,用常規(guī)的混合機(jī)對上述銅合金粉末14和扁平形狀的鱗片狀石墨粉末15(日本石墨工業(yè)株式會社(日本黒鉛工業(yè)(株))制造)進(jìn)行混合。該鱗片狀石墨粉末15中,粒徑為45~75μm的粉末占全體石墨粉末的60質(zhì)量%以上,且最大粒徑在300μm以下。此外,鱗片狀石墨粉末的粒徑利用篩來測定。另外,鱗片狀石墨粉末的粒徑是指扁平形狀的粒子的最長部分的尺寸。此時(shí),銅合金粉末14與鱗片狀石墨粉末15的混合粉末的空孔率(空孔率:1-ad/td,ad:表觀密度(g/cm3),td:理論密度(g/cm3))為60~76%。然后,將該混合粉末散布在帶鋼(鋼背層)上,形成散布層。散布層的空孔率維持所述混合粉末的空孔率(60~76%,圖2a)。此外,背層不限于鋼,也可以由銅合金或其它金屬制成。另外,背層也可以由鋼和被覆在鋼表面上的銅或銅合金構(gòu)成。在散布工序之后進(jìn)行一次燒結(jié)工序。在一次燒結(jié)工序中,為了維持散布時(shí)散布層的空孔率,需要在比銅合金中產(chǎn)生液相的溫度(熔點(diǎn))低50℃以上的溫度下進(jìn)行燒結(jié)。籍此,能夠防止銅合金中產(chǎn)生液相。例如,在對含有10質(zhì)量%的錫的銅合金進(jìn)行燒結(jié)的場合下,在700~740℃下進(jìn)行燒結(jié)。然后,在對銅合金開始加熱而到達(dá)燒結(jié)溫度之后,在該燒結(jié)溫度下保持2~10分鐘,隨后進(jìn)行冷卻。另外,在一次燒結(jié)工序中,燒結(jié)至收縮率(收縮率:1-燒結(jié)層厚度(mm)/散布層厚度(mm))達(dá)到3~10%。在像這樣燒結(jié)至一次燒結(jié)時(shí)的收縮率達(dá)到3~10%的場合下,燒結(jié)層的空孔率達(dá)到55~75%(圖2b)。而如果在銅合金中產(chǎn)生液相的燒結(jié)溫度下進(jìn)行燒結(jié),則燒結(jié)層的空孔率降低,一次燒結(jié)時(shí)的收縮率會大于10%。于是,如果對一次燒結(jié)時(shí)收縮率大于10%時(shí)的燒結(jié)層的剖面進(jìn)行測定,則會發(fā)現(xiàn)與圖3b所示的組織同樣地大量形成銅合金粉末14之間的頸部,結(jié)果是燒結(jié)層(滑動層)中島狀銅合金部42的形成量減少。而如果一次燒結(jié)時(shí)的收縮率小于3%,則燒結(jié)層的強(qiáng)度過低,燒結(jié)層會在下文所述的軋制時(shí)破損。一次燒結(jié)工序之后,用軋制機(jī)進(jìn)行使燒結(jié)層致密化的軋制工序。圖2c的箭頭顯示了軋制時(shí)的力的方向19。在軋制前的燒結(jié)層的空孔率為55~75%的場合(圖2b)下,軋制時(shí)的擠壓余地(日文:潰し代)(軋制前具有空孔的燒結(jié)層的厚度與軋制后空孔消除而致密化了的燒結(jié)層的厚度之差)大。因此,如圖2c所示,軋制后鱗片狀石墨粉末15長軸的方向齊整。而且,在一次燒結(jié)工序中,如圖2b所示,銅合金粉末14之間形成頸部17的情況少,因此在之后的軋制工序中,鱗片狀石墨粉末15進(jìn)入銅合金粉末14之間的間隙中,在形成網(wǎng)絡(luò)的銅合金41中大量形成被鱗片狀石墨粉末15包圍的島狀銅合金部42。而在散布層的空孔率小于60%的場合(圖3a)下,燒結(jié)層的空孔率也降低,銅合金粉末之間相互接觸的部分16也多。于是,在軋制前的燒結(jié)層的空孔率小于55%的場合下,軋制時(shí)的擠壓余地小(圖3b)。因此,如圖3c所示,軋制后鱗片狀石墨粉末15長軸的方向18不齊整。而且,在一次燒結(jié)工序中,如圖3b所示,銅合金粉末14之間形成頸部17的情況多,因此在之后的軋制工序中,鱗片狀石墨粉末15無法進(jìn)入銅合金粉末14之間的網(wǎng)絡(luò)41’的間隙中,幾乎不形成被鱗片狀石墨粉末15包圍的島狀銅合金部42。在軋制工序(一次軋制工序)之后進(jìn)行二次燒結(jié)工序,在該二次燒結(jié)工序中,以與一次燒結(jié)工序相同的條件進(jìn)行燒結(jié),根據(jù)需要進(jìn)行二次軋制工序。關(guān)于銅合金粉末,如果使用平均粒徑d50小于25μm的粉末,則一次燒結(jié)后的燒結(jié)層的空孔率會變得大于75%,從而燒結(jié)層的強(qiáng)度會降低,燒結(jié)層在軋制時(shí)會破損。而如果銅合金粉末的平均粒徑d50大于50μm,則一次燒結(jié)后的燒結(jié)層的空孔率變得小于55%,從而幾乎不形成被鱗片狀石墨粉末包圍的島狀銅合金部。如圖2c所示,在一次燒結(jié)后的燒結(jié)層的空孔率為55~75%且軋制時(shí)擠壓余地大的場合下,鱗片狀石墨15粉末的長軸的方向18聚攏,而如果使用粒徑小的鱗片狀石墨粉末,則與粒徑大的鱗片狀石墨粉末相比,長軸的方向難以聚攏。因此,鱗片狀石墨粉末的粒徑越小,對被鱗片狀石墨粉末包圍的島狀銅合金部42的形成的幫助也越小。另外,如果使滑動層3中所包含的鱗片狀石墨5的量保持不變,則鱗片狀石墨粉末15的粒徑越大,該粉末的個(gè)數(shù)就會減少,被鱗片狀石墨粉末15包圍的島狀銅合金部42就越難形成。如此,在鱗片狀石墨的粒徑過小的場合或過大的場合下,被鱗片狀石墨粉末包圍的島狀銅合金部42都難以形成。具體而言,粒徑小于45μm的鱗片狀石墨粉末對被鱗片狀石墨粉末包圍的島狀銅合金部的形成的幫助小,粒徑大于75μm的鱗片狀石墨粉末對被鱗片狀石墨粉末包圍的島狀銅合金部的形成的幫助也小。所以,如果不使用含有60%以上的粒徑在45~75μm范圍內(nèi)的粉末的鱗片狀石墨粉末15,則被鱗片狀石墨粉末15包圍的島狀銅合金部42就無法形成。另外,由上述理由可知,在含有最大粒徑大于300μm的鱗片狀石墨粉末的場合下,被鱗片狀石墨粉末15包圍的島狀銅合金部42也變得難以形成。實(shí)施例下面,制作本發(fā)明的實(shí)施例1~14以及比較例1~6,測定它們的銅合金部的形態(tài),并進(jìn)行往復(fù)滑動試驗(yàn)。實(shí)施例1~14以及比較例1~6的成分、銅合金部的形態(tài)、往復(fù)滑動試驗(yàn)中的靜摩擦系數(shù)的測定結(jié)果示于表1。表1滑動部件的剖面測定中,沿著與滑動面垂直的方向切斷,對2.3mm×0.7mm范圍內(nèi)的組成像(倍率:50倍)進(jìn)行攝影。對所得到的組成像使用常用圖像分析方法(分析軟件:image-proplus(版本:4.5);プラネトロン株式會社((株)プラネトロン)制造)測定與滑動面平行的方向上的長度為25~500μm的島狀銅合金部的面積之和,算出與滑動面平行的方向上的長度為25~500μm的島狀銅合金部在滑動層的總面積中所占的比例。此外,對該面積的比例使用6個(gè)視野(6個(gè)不同的任意剖面)的組成像來計(jì)算它們的平均值。該結(jié)果示于表1的“25~500μm的島狀銅合金部(體積%)”一欄。另外,縱橫比按照以下方式求出:對所得到的組成像使用上述分析軟件,測定以滑動層的厚度方向上的長度為y軸、以與之垂直的方向上的長度為x軸時(shí)各島狀銅合金部的y軸方向上的長度(y)和x軸方向上的長度(x),算出各自的長度之比(x/y)。從其中測定縱橫比為1.2~5的島狀銅合金部的面積之和,算出縱橫比為1.2~5的島狀銅合金部在與滑動面平行的方向上的長度為25~500μm的島狀銅合金部的總面積中所占的比例。該結(jié)果示于表1的“縱橫比:1.2~5(體積%)”一欄。此外,往復(fù)滑動試驗(yàn)以表2中所示的條件來實(shí)施。靜摩擦系數(shù)的測定方法是:測定滑動方向剛改變后的摩擦系數(shù),重復(fù)測定4小時(shí),求出其平均值。另外,往復(fù)滑動試驗(yàn)中的摩擦系數(shù)的測定是以滑動方向改變時(shí)摩擦系數(shù)的峰值作為靜摩擦系數(shù)來測定的。此外,試驗(yàn)時(shí)間為4小時(shí),但在磨耗量大于50μm的場合下,判斷為異常磨耗而終止試驗(yàn)。表2滑動速度0.5米/分鐘試驗(yàn)時(shí)間4小時(shí)滑動環(huán)境干燥試驗(yàn)溫度室溫試驗(yàn)負(fù)荷10n對象材料s55c實(shí)施例1~3、6~12中,使用常規(guī)的混合機(jī)將利用水霧化法制成的平均粒徑d50為35μm的異形狀銅合金粉末與粒徑在45~75μm范圍內(nèi)的粉末占80質(zhì)量%且最大粒徑在106~150μm范圍內(nèi)的鱗片狀石墨粉末混合成表1的成分比,制成混合粉末。銅合金粉末含有sn,實(shí)施例8~12還含有ni、p、pb、bi中的一種或多種,實(shí)施例12還含有mo2c。然后,在帶鋼(鋼背層)上散布混合粉末而形成散布層,在700~740℃的燒結(jié)溫度下進(jìn)行一次燒結(jié),形成燒結(jié)層。接著,進(jìn)行使燒結(jié)層致密化的軋制和在700~740℃的燒結(jié)溫度下的二次燒結(jié),制成滑動部件。此外,表1的“石墨45~75μm(質(zhì)量%)”一欄中給出作為原材料的鱗片狀石墨粉末中粒徑在45~75μm范圍內(nèi)的粉末所占的質(zhì)量比例,“散布層的空孔率(%)”一欄中給出散布層的空孔率,“收縮率(%)”一欄中給出一次燒結(jié)工序中的收縮率(收縮率:1—一次燒結(jié)后的燒結(jié)層厚(mm)/散布層厚(mm)),“燒結(jié)層的空孔率(%)”一欄中給出一次燒結(jié)后的燒結(jié)層的空孔率。實(shí)施例4中,除了使用利用水霧化法制成的平均粒徑d50為50μm的異形狀銅合金粉末作為銅合金粉末以外,按照與實(shí)施例1相同的方式進(jìn)行制作。實(shí)施例5中,除了使用粒徑在45~75μm范圍內(nèi)的粉末占60質(zhì)量%且最大粒徑在106~150μm范圍內(nèi)的鱗片狀石墨粉末作為鱗片狀石墨粉末以外,按照與實(shí)施例1相同的方式進(jìn)行制作。實(shí)施例13中,除了使用利用水霧化法制成的平均粒徑d50為25μm的異形狀銅合金粉末作為銅合金粉末以外,按照與實(shí)施例1相同的方式進(jìn)行制作。實(shí)施例14中,除了使用粒徑在45~75μm范圍內(nèi)的粉末占95質(zhì)量%且最大粒徑在106~150μm范圍內(nèi)的鱗片狀石墨粉末作為鱗片狀石墨粉末以外,按照與實(shí)施例1相同的方式進(jìn)行制作。實(shí)施例1~11、13、14的結(jié)果是形成了5~40體積%的與滑動面平行的方向上的長度為25~500μm的島狀銅合金部,靜摩擦系數(shù)低。而且,在實(shí)施例3、13、14中,通過將燒結(jié)層的空孔率(散布層的空孔率)控制在較高水平,形成了較多的與滑動面平行的方向上的長度為25~500μm的島狀銅合金部。特別是在實(shí)施例3中,通過將燒結(jié)層的空孔率(散布層的空孔率)控制在較高水平,形成了比例為40體積%的最多的與滑動面平行的方向上的長度為25~500μm的島狀銅合金部。這樣的實(shí)施例3、13、14中得到了在與滑動面平行的方向上的長度為25~500μm的島狀銅合金部中縱橫比為1.2~5的島狀銅合金部為50體積%以上那么多、靜摩擦系數(shù)特別低的結(jié)果。實(shí)施例12按照與實(shí)施例1相同的方式進(jìn)行制作,但在粉末混合工序中同時(shí)還添加硬質(zhì)粒子(mo2c)而混合。硬質(zhì)粒子的成分量添加至表1所示的量。即使添加了硬質(zhì)粒子也得到了與實(shí)施例1相同的結(jié)果。比較例1中,除了使用與實(shí)施例1相同的鱗片狀石墨粉末、使滑動層中的石墨含量為15體積%以外,按照與實(shí)施例1相同的方式進(jìn)行制作。在該比較例1中,由于滑動層中的石墨含量為15體積%那么少,銅合金被鱗片狀石墨粉末包圍的比例變低。因此,導(dǎo)致滑動層中幾乎未形成被石墨包圍的島狀銅合金部、靜摩擦系數(shù)高于實(shí)施例1的結(jié)果。比較例2中,除了使用粒徑在45~75μm范圍內(nèi)的粉末占50質(zhì)量%且粒徑在75~300μm范圍內(nèi)的粉末占50質(zhì)量%的鱗片狀石墨粉末作為鱗片狀石墨粉末以外,按照與實(shí)施例1相同的方式進(jìn)行制作。該比較例2中,由于只含有50質(zhì)量%的粒徑在45~75μm范圍內(nèi)的鱗片狀石墨粉末,鱗片狀石墨粉末的個(gè)數(shù)少,銅合金難以被鱗片狀石墨粉末包圍。因此,導(dǎo)致滑動層中幾乎未形成被石墨包圍的島狀銅合金部、靜摩擦系數(shù)高于實(shí)施例1的結(jié)果。比較例3中,除了使用利用水霧化法制成的平均粒徑d50為55μm的異形狀銅合金粉末作為銅合金粉末以外,按照與實(shí)施例1相同的方式進(jìn)行制作。該比較例3中,由于銅合金粉末的平均粒徑d50為55μm那么大,散布層的空孔率變低,燒結(jié)層的空孔率也變低。因此,導(dǎo)致滑動層中幾乎未形成被石墨包圍的島狀銅合金部、靜摩擦系數(shù)高于實(shí)施例1的結(jié)果。比較例4中,除了使用利用氣霧化法制成的平均粒徑d50為35μm的銅合金粉末作為銅合金粉末以外,按照與實(shí)施例1相同的方式進(jìn)行制作。在使用氣霧化法制作銅合金粉末的場合下,該粉末成為球狀。該比較例3中,由于使用了球狀的銅合金粉末,散布層的空孔率變低,燒結(jié)層的空孔率也變低。因此,導(dǎo)致滑動層中幾乎未形成被石墨包圍的島狀銅合金部、靜摩擦系數(shù)高于實(shí)施例1的結(jié)果。比較例5中,除了在一部分銅合金成為液相的850℃的燒結(jié)溫度下進(jìn)行燒結(jié)以外,按照與實(shí)施例1相同的方式進(jìn)行制作。在該比較例5中,散布層的空孔率為67%,但一次燒結(jié)時(shí)產(chǎn)生銅合金的液相,燒結(jié)層的空孔率降低至51%。因此,導(dǎo)致滑動層中幾乎未形成被石墨包圍的島狀銅合金部、靜摩擦系數(shù)高于實(shí)施例1的結(jié)果。在比較例6中,除了使用銅粉末與錫粉末的混合粉末作為銅合金粉末以外,按照與實(shí)施例1相同的方式進(jìn)行制作。在該比較例5中,在一次燒結(jié)時(shí)的升溫過程中,首先,錫粉末變成液相,一部分銅粉末由于錫的液相而液相化,燒結(jié)層的空孔率降低至51%。因此,導(dǎo)致滑動層中幾乎未形成被石墨包圍的島狀銅合金部、靜摩擦系數(shù)高于實(shí)施例1的結(jié)果。當(dāng)前第1頁12