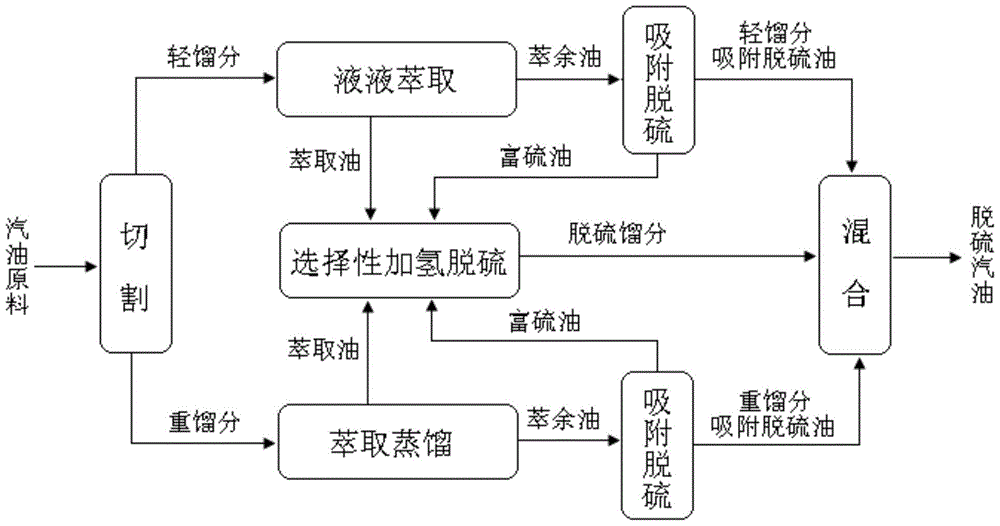
本發(fā)明涉及一種汽油脫硫方法,特別是涉及一種汽油深度脫硫方法。
背景技術(shù):隨著人們對(duì)環(huán)境保護(hù)的日益重視,世界各國(guó)的新環(huán)保法規(guī)對(duì)汽油質(zhì)量的要求愈加嚴(yán)格。例如,我國(guó)于2017年1月1日即將實(shí)施的國(guó)V車用汽油標(biāo)準(zhǔn)將要求烯烴含量在25%以下,硫含量在10ppm以下;美國(guó)環(huán)保局(EPA)規(guī)定汽油的硫限值為30ppm(TierIl);歐洲要求汽油的硫含量應(yīng)當(dāng)?shù)陀?0ppm(歐IV排放標(biāo)準(zhǔn))。因此,必須對(duì)汽油進(jìn)行深度脫硫才可能達(dá)到相關(guān)要求。吸附脫硫在脫除汽油原料中硫化物的同時(shí)對(duì)汽油產(chǎn)品辛烷值的影響較小,因此是較具潛力的脫硫方法之一,目前也有較多報(bào)道。例如,由Black&VeatchPritchardInc.與AlcoaIndustrialChemicals聯(lián)合開(kāi)發(fā)的IRVAD技術(shù)采用多級(jí)流化床吸附方式,使用氧化鋁基質(zhì)選擇性固體吸附劑處理液體烴類,在吸附過(guò)程中,吸附劑逆流與液體烴類相接觸,使用過(guò)的吸附劑逆向與再生熱氣流(例如氫氣)反應(yīng)得以再生。該技術(shù)的脫硫率可達(dá)90%以上,然而該吸附劑選擇性不高,吸附硫容有限,并且再生過(guò)程相對(duì)復(fù)雜。Phillips石油公司研發(fā)的S-Zorb工藝是在臨氫的條件下采用一種特定的吸附劑進(jìn)行脫硫,該吸附劑以氧化鋅、二氧化硅、氧化鋁作為載體并且負(fù)載Co、Ni、Cu等金屬組分,其能夠吸附硫化物中的硫原子,使之保留在吸附劑上,而硫化物的烴結(jié)構(gòu)部分則被釋放回工藝物流中,從而實(shí)現(xiàn)脫硫過(guò)程。該工藝在反應(yīng)過(guò)程中不產(chǎn)生H2S,從而避免了H2S與烯烴再次反應(yīng)生成硫醇。然而,該脫硫技術(shù)工藝操作條件相對(duì)苛刻,脫硫反應(yīng)的溫度為343-413℃,壓力為2.5-2.9MPa。盡管上述吸附脫硫方法能夠減小汽油產(chǎn)品辛烷值的損失,然而操作相對(duì)復(fù)雜,并且脫硫深度不夠,通常難以將汽油脫硫至10ppm以下。此外,由于汽油成分相對(duì)復(fù)雜,并且某些成分會(huì)在吸附脫硫過(guò)程中產(chǎn)生競(jìng)爭(zhēng)吸附,從而造成吸附脫硫效率降低、吸附劑使用壽命縮短等缺陷。加氫脫硫是脫除汽油中硫化物最為有效的方法。并且,為了避免加氫脫硫過(guò)程中汽油中的烯烴等成分被飽和而導(dǎo)致辛烷值損失,工業(yè)上通常先對(duì)汽油原料進(jìn)行蒸餾,從而將其切割為兩個(gè)以上餾分,其中對(duì)輕餾分以非加氫脫硫方式進(jìn)行脫硫,從而避免辛烷值損失;對(duì)重餾分通常以選擇性加氫脫硫方式進(jìn)行脫硫,從而實(shí)現(xiàn)深度脫硫。例如,石油化工科學(xué)研究院于2001年開(kāi)發(fā)的FCC汽油選擇性加氫脫硫工藝(RSDS-Ⅰ),先在90℃的切割溫度下將FCC汽油切割成輕、重餾分,然后對(duì)輕餾分進(jìn)行堿抽提脫硫醇,并采用主催化劑RSDS-Ⅰ和保護(hù)劑RGO-2對(duì)重餾分進(jìn)行選擇性加氫脫硫;而在對(duì)上述工藝進(jìn)行改進(jìn)的第二代FCC汽油選擇性加氫脫硫技術(shù)(RSDS-Ⅱ)將切、重餾分的切割點(diǎn)降至70℃,并且在重餾分選擇性加氫脫硫部分采用第二代加氫催化劑RSDS-21、RSDS-22。法國(guó)石油研究院(IFP)Axens公司開(kāi)發(fā)的Prime-G+工藝,采用全餾分預(yù)加氫、輕重汽油切割和重餾分選擇性加氫脫硫的工藝流程,其根據(jù)硫含量的目標(biāo)值將切割溫度設(shè)為93-149℃,并且在全餾分預(yù)加氫過(guò)程中,采用HR845催化劑將輕硫化物與二烯烴作用形成高沸點(diǎn)的硫化物,因此烯烴沒(méi)有被飽和;此外,在重餾分選擇性加氫脫硫中采用HR806和HR841兩種催化劑進(jìn)行,操作更加靈活。中國(guó)石化撫順石油化工研究院開(kāi)發(fā)的OCT-M工藝在90℃的切割溫度下將FCC汽油切割為輕、重兩個(gè)餾分,其中對(duì)輕餾分進(jìn)行脫硫醇,對(duì)重餾分采用FGH-20/FGH-11組合催化劑進(jìn)行選擇性加氫脫硫。海順德開(kāi)發(fā)出的HDDO系列脫雙烯烴催化劑、HDOS系列深度加氫脫硫催化劑、HDMS系列脫硫醇催化劑以及相應(yīng)的FCC汽油選擇性加氫脫硫工藝(CDOS),先將FCC汽油在較低溫度、臨氫條件下進(jìn)行脫二烯烴反應(yīng),然后將FCC汽油切割為輕、重兩個(gè)組分,并對(duì)重餾分進(jìn)行深度加氫脫硫,加氫后的重餾分與輕餾分調(diào)和而得到低硫清潔汽油。上述方法對(duì)汽油原料的切割溫度普遍較高,切割所形成的輕餾分中硫含量相對(duì)較大,僅依靠脫硫醇等非加氫脫硫方式難以使輕餾分的硫含量降至10ppm以下,在生產(chǎn)硫含量小于10ppm的汽油產(chǎn)品時(shí),大部分輕餾分仍需要加氫脫硫,因而全餾分汽油的辛烷值損失量較高(例如高達(dá)3.0-4.0)。此外,盡管上述加氫脫硫方式能夠使汽油的硫含量大大降低,然而存在投資和操作費(fèi)用高,在脫除硫化物的同時(shí)使大量的烯烴被飽和,既增加了氫耗,也使汽油的辛烷值大幅降低。因此,期待一種在實(shí)現(xiàn)深度脫硫的同時(shí)減小汽油產(chǎn)品辛烷值損失的汽油脫硫方法。
技術(shù)實(shí)現(xiàn)要素:本發(fā)明提供一種汽油深度脫硫方法,用于解決現(xiàn)有技術(shù)中的脫硫方法操作復(fù)雜,并且難以同時(shí)實(shí)現(xiàn)深度脫硫和減小辛烷值損失等技術(shù)缺陷。本發(fā)明提供一種汽油深度脫硫方法,包括如下步驟:將汽油原料切割為輕餾分和重餾分;對(duì)所述輕餾分進(jìn)行液液萃取,得到含有烯烴的輕餾分萃余油和含有硫化物及芳烴的輕餾分萃取油;對(duì)所述重餾分進(jìn)行萃取蒸餾,得到含有烯烴的重餾分萃余油和含有硫化物及芳烴的重餾分萃取油;對(duì)所述輕餾分萃取油和重餾分萃取油進(jìn)行選擇性加氫脫硫,得到脫硫餾分;將所述輕餾分萃余油、重餾分萃余油和脫硫餾分混合,得到脫硫汽油;其中,所述輕餾分與重餾分的切割溫度為80-120℃。在本發(fā)明中,所述汽油原料可以為催化裂化汽油等。所述切割是將汽油原料按照餾程從低到高切割為輕、重兩個(gè)餾分;可以采用本領(lǐng)域常規(guī)方法進(jìn)行所述切割,例如蒸餾等。進(jìn)一步地,所述輕餾分與重餾分的切割溫度為90-110℃。經(jīng)研究發(fā)現(xiàn):催化裂化汽油中硫化物的分布具有以下特點(diǎn):1、碳五以下(沸點(diǎn)通常<40℃)的餾分中,主要含有硫醇硫;2、碳六(沸點(diǎn)通常為40-80℃)餾分中主要含有噻吩硫;3、碳七(沸點(diǎn)通常為70-110℃)餾分中主要含有甲基噻吩硫;4、碳七以上的餾分中的硫化物以烷基噻吩和硫醚硫?yàn)橹??;谝陨涎芯?,本發(fā)明人采用特定的切割溫度將汽油原料切割為輕餾分和重餾分;其中:1、上述輕餾分中含有大量的烯烴,并且含有部分芳烴、烷烴及環(huán)烷烴,硫化物主要為噻吩、甲基噻吩、烷基噻吩等;針對(duì)上述輕餾分中的噻吩和甲基噻吩,本發(fā)明采用液液萃取方式可容易地進(jìn)行脫除,而對(duì)于上述輕餾分中某些與烴的抽提選擇性較低且沸點(diǎn)較高的硫化物,液液萃取時(shí)溶劑再生所需溫度較高,會(huì)導(dǎo)致硫化物與烯烴生膠加重,因此不易實(shí)現(xiàn)這些硫化物的脫除。鑒于此,本發(fā)明對(duì)液液萃取后的萃取油進(jìn)行選擇性加氫脫硫,從而實(shí)現(xiàn)深度脫硫;同時(shí),由于液液萃取過(guò)程已將輕餾分中的硫化物和大部分芳烴萃取出來(lái)從而與烷烴、烯烴和環(huán)烷烴分離,因此在后續(xù)選擇性加氫脫硫時(shí)輕餾分中的烯烴不會(huì)被飽和,從而可以避免汽油產(chǎn)品的辛烷值損失,并且還能大幅度降低總的脫硫負(fù)荷。2、上述重餾分中烯烴含量較低而芳烴和硫化物含量較高,因此本發(fā)明先采用萃取蒸餾將重餾分中的烯烴分離出來(lái),隨后對(duì)分離了烯烴的重餾分進(jìn)行選擇性加氫脫硫,既可以滿足深度脫硫,同時(shí)還能夠避免汽油產(chǎn)品的辛烷值損失?;谏鲜鲅芯砍晒岢霰景l(fā)明,其在實(shí)現(xiàn)深度脫硫的同時(shí)還能夠顯著減小汽油產(chǎn)品辛烷值損失。在本發(fā)明中,液液萃取的目的是通過(guò)有機(jī)溶劑將輕餾分中的烯烴、烷烴、環(huán)烷烴等成分與硫化物、大部分芳烴及環(huán)烯等其它成分分離,從而避免烯烴等不飽和烴在后續(xù)選擇性加氫脫硫過(guò)程中被飽和而造成汽油產(chǎn)品辛烷值降低。本領(lǐng)域技術(shù)人員可以根據(jù)該目的來(lái)選擇適宜的有機(jī)溶劑和液液萃取工藝。在一實(shí)施方式中,所述液液萃取包括:使所述輕餾分從抽提塔中下部進(jìn)入,有機(jī)溶劑從抽提塔頂部進(jìn)入,并且從抽提塔底部回流裝置注入C5烷烴;其中,控制抽提塔塔頂溫度為55-100℃,塔底溫度為40-80℃,塔頂絕對(duì)壓力為0.2-0.7MPa,所述有機(jī)溶劑與輕餾分進(jìn)料比(體積比)為1.0-5.0,C5烷烴與輕餾分進(jìn)料比(體積比)為0.1-0.5;收集抽提塔塔頂流出物,得到含有烯烴的輕餾分萃余物;收集抽提塔塔底流出物,得到含有硫化物及芳烴的輕餾分萃取物;對(duì)所述輕餾分萃余物進(jìn)行水洗,得到含有烯烴的輕餾分萃余油;對(duì)所述輕餾分萃取物中的有機(jī)溶劑和C5烷烴進(jìn)行分離,得到含有硫化物及芳烴的輕餾分萃取油。其中,所述有機(jī)溶劑可以選自二甘醇、三甘醇、四甘醇、二甲亞砜、環(huán)丁砜、N-甲酰嗎啉、N-甲基吡咯烷酮、聚乙二醇和碳酸丙烯酯中的一種或多種,進(jìn)一步為三甘醇、四甘醇和環(huán)丁砜中的一種或多種;控制所述有機(jī)溶劑的含水量(即水的重量含量)<1.0%是有利的,進(jìn)一步可以為0.6-0.8%。在本發(fā)明中,加入所述C5烷烴是為了增加分離效率;在一實(shí)施方式中,C5烷烴可選自正戊烷和異戊烷中的一種或兩種。進(jìn)一步地,控制抽提塔塔頂溫度為65-80℃,塔底溫度為50-60℃,塔頂絕對(duì)壓力為0.5-0.6MPa,所述有機(jī)溶劑與輕餾分進(jìn)料比為2.0-3.0,C5烷烴與輕餾分進(jìn)料比為0.2-0.3。此外,對(duì)所述輕餾分萃余物進(jìn)行水洗的目的是去除其中的有機(jī)溶劑;在進(jìn)行所述水洗時(shí),可以控制水的用量(基于輕餾分萃余物的量)為1-10%,例如為2-4%。在一實(shí)施方式中,對(duì)所述輕餾分萃取物中的有機(jī)溶劑和C5烷烴進(jìn)行分離,可以包括:使所述輕餾分萃取物進(jìn)入抽提蒸餾塔頂部,收集抽提蒸餾塔頂部流出物,回收得到C5烷烴,收集抽提蒸餾塔塔底流出物,得到含有輕富硫組分(含有硫化物、芳烴、環(huán)稀)、有機(jī)溶劑和水的第一混合物;其中,控制抽提蒸餾塔絕對(duì)壓力為0.15-0.3MPa,抽提蒸餾塔塔底溫度為150-180℃;使所述第一混合物進(jìn)入回收塔中部,收集回收塔塔頂流出物,得到含有輕富硫組分和水的第二混合物,收集回收塔塔底流出物,回收得到有機(jī)溶劑;其中,控制回收塔絕對(duì)壓力為0.015-0.05MPa,回收塔塔底溫度為130-180℃;將所述第二混合物冷凝后進(jìn)行油水分離,得到水和含有硫化物及芳烴的輕餾分萃取油(即輕富硫組分)。進(jìn)一步地,回收得到的C5烷烴經(jīng)冷凝后可返回至所述抽提塔底部回流裝置進(jìn)行循環(huán)利用;得到的水一部分可返回所述回收塔塔頂,另一部分用于對(duì)所述輕餾分萃余物的水洗;回收得到的有機(jī)溶劑經(jīng)換熱后可返回所述抽提塔頂部循環(huán)使用。進(jìn)一步地;抽提蒸餾塔絕對(duì)壓力可以為0.2MPa,抽提蒸餾塔塔底溫度可以為160℃;回收塔絕對(duì)壓力可以為0.035-0.045MPa,回收塔塔底溫度可以為165-175℃。在本發(fā)明中,萃取蒸餾的目的是通過(guò)有機(jī)溶劑將重餾分中的烯烴、烷烴、環(huán)烷烴等成分與硫化物、大部分芳烴及環(huán)烯等其它成分分離,從而避免烯烴等不飽和烴在后續(xù)選擇性加氫脫硫過(guò)程中被飽和而造成汽油產(chǎn)品辛烷值降低;此外,在萃取蒸餾中,還能夠利用蒸餾來(lái)實(shí)現(xiàn)不同組分的分離。本領(lǐng)域技術(shù)人員可以根據(jù)該目的來(lái)選擇適宜的有機(jī)溶劑和萃取蒸餾工藝。在一實(shí)施方式中,所述萃取蒸餾包括:使所述重餾分從萃取蒸餾塔中下部進(jìn)入,有機(jī)溶劑從萃取蒸餾塔上部進(jìn)入;其中,控制萃取蒸餾塔的理論塔板數(shù)為25-45,塔頂溫度為70-110℃,塔底溫度為150-190℃,塔頂絕對(duì)壓力為0.1-0.5MPa,有機(jī)溶劑與重餾分的進(jìn)料比(即體積比)為1.0-5.0,回流比為0.1-4.0;收集萃取蒸餾塔塔頂流出物,得到含有烯烴的重餾分萃余物;收集萃取蒸餾塔塔底流出物,得到含有硫化物及芳烴的重餾分萃取物;對(duì)所述重餾分萃余物進(jìn)行水洗,得到含有烯烴的重餾分萃余油;對(duì)所述重餾分萃取物中的有機(jī)溶劑進(jìn)行分離,得到含有硫化物及芳烴的重餾分萃取油。在上述萃取蒸餾條件下,重餾分中的烯烴與芳烴的分離程度可達(dá)到90%以上,分離效果好。其中,重餾分與有機(jī)溶劑在萃取蒸餾塔中經(jīng)多級(jí)逆流接觸,重餾分從萃取蒸餾塔頂部流出時(shí)部分硫化物、大部分芳烴及環(huán)烯等成分被萃取脫除,從而形成含有烯烴、烷烴、環(huán)烷烴等成分的重餾分萃余物,重餾分萃余物經(jīng)冷凝器冷凝后,一部分回流,以維持萃取蒸餾塔塔內(nèi)的熱量平衡,并保證萃取蒸餾的穩(wěn)定進(jìn)行以及產(chǎn)品的分離精度,其中回流比(即用于回流的重餾分萃余物與餾出的重餾分萃余物之間的體積比)為0.1-4.0;萃取了重餾分中的硫化物和芳烴的溶劑從塔底流出,形成重餾分萃取物,其中含有重富硫組分(包括硫化物、芳烴、環(huán)烯等)、水和溶劑。在上述萃取蒸餾中,所述有機(jī)溶劑可以選自二甘醇、三甘醇、四甘醇、二甲亞砜、環(huán)丁砜、N-甲酰嗎啉、N-甲基吡咯烷酮、聚乙二醇和碳酸丙烯酯中的一種或多種,進(jìn)一步為三甘醇、四甘醇和環(huán)丁砜中的一種或多種,例如三甘醇與環(huán)丁砜的混合溶劑,其中環(huán)丁砜與三甘醇的體積比可以為(6-9):(4-1);控制所述有機(jī)溶劑的含水量(即水的重量含量)<1.0%是有利的,進(jìn)一步可以為0.6-0.8%。進(jìn)一步地,所述萃取蒸餾塔的理論塔板數(shù)為30-35,塔頂溫度為80-100℃,塔底溫度為160-180℃,塔頂絕對(duì)壓力為0.3-0.4MPa,有機(jī)溶劑與重餾分的進(jìn)料比為2.0-3.0,回流比為0.2-2.0。此外,對(duì)所述重餾分萃余物進(jìn)行水洗的目的是去除其中的有機(jī)溶劑;在水洗時(shí),可以控制水的用量(基于重餾分萃余物的量)為1-10%,例如為2-4%。在一實(shí)施方式中,對(duì)所述重餾分萃取物中的有機(jī)溶劑進(jìn)行分離,可以包括:使所述重餾分萃取物從溶劑回收塔中上部進(jìn)入,蒸汽(水蒸汽)從溶劑回收塔下部進(jìn)入;其中,所述溶劑回收塔的理論塔板數(shù)為10-30,塔頂溫度為50-100℃,塔底溫度為150-200℃,塔頂絕對(duì)壓力為0.03-0.07MPa,蒸汽與重餾分萃取物的進(jìn)料比(即質(zhì)量比)為(0.1-0.5):100,回流比為0.2-4.0。在上述溶劑回收塔中,重富硫組分與溶劑得到分離,其中溶劑從塔底流出后可進(jìn)入萃取蒸餾塔中進(jìn)行循環(huán)利用;重富硫組分和蒸汽從塔頂流出,經(jīng)冷凝后,采用常規(guī)方式(例如抽真空)脫水,得到含有硫化物及芳烴的重餾分萃取油(即重富硫組分),重餾分萃取油隨后進(jìn)行選擇性加氫脫硫,一部分脫除的水用于回流,以維持溶劑回收塔塔內(nèi)的熱量平衡,保證分離過(guò)程穩(wěn)定進(jìn)行,其中回流比(即用于回流的水與餾出的水之間的體積比)為0.2-4.0,其余的水用于對(duì)重餾分萃余物的水洗。進(jìn)一步地,所述溶劑回收塔的理論塔板數(shù)為15-25,塔頂溫度為60-80℃,塔底溫度為165-185℃,塔頂絕對(duì)壓力為0.04-0.06MPa,蒸汽與重餾分萃取物的進(jìn)料比為(0.3-0.4):100,回流比為0.5-2.0。在一實(shí)施方式中,所述萃取蒸餾可以包括:使重餾分從萃取蒸餾塔中下部進(jìn)入,有機(jī)溶劑從萃取蒸餾塔上部進(jìn)入,萃取蒸餾塔塔頂流出物形成含有烯烴的重餾分萃余物,萃取蒸餾塔塔底流出物形成含有硫化物及芳烴的重餾分萃取物;使上述重餾分萃余物進(jìn)入水洗塔中進(jìn)行水洗,得到含有烯烴的重餾分萃余油;使上述重餾分萃取物從溶劑回收塔中上部進(jìn)入,蒸汽從溶劑回收塔下部進(jìn)入,溶劑回收塔塔底流出物形成有機(jī)溶劑,溶劑回收塔塔頂流出物形成重富硫組分和水的混合物;使上述混合物進(jìn)入富硫油罐中進(jìn)行分離,形成含有硫化物及芳烴的重餾分萃取油(即重富硫組分)和水,形成的水一部分返回至溶劑回收塔,另一部分返回至水洗塔。進(jìn)一步地,可以使水洗塔塔底出水進(jìn)入水汽提塔塔頂進(jìn)行汽提,水汽提塔塔頂流出物(即從水中所汽提出的微量有機(jī)物)隨后可進(jìn)入回流罐進(jìn)行分離,水汽提塔塔底流出物(即含溶劑的水)隨后可進(jìn)入溶劑回收塔塔底進(jìn)行溶劑回收。水汽提塔底部通常設(shè)有重沸器,其產(chǎn)生的汽提蒸汽可作為溶劑回收塔的蒸汽來(lái)源。在回流罐中,有機(jī)物與水可通過(guò)常規(guī)方式進(jìn)行分離(例如抽真空),分離出的有機(jī)物隨后進(jìn)入萃取蒸餾塔塔底,分離出的水可與水洗塔塔底出水合并后進(jìn)入水汽提塔塔頂進(jìn)行汽提。此外,可以使溶劑回收塔塔底的一部分有機(jī)溶劑作為水汽提塔塔底重沸器的熱源,然后與萃取蒸餾塔塔底的萃取物換熱,再返回至萃取蒸餾塔塔頂;另一部分有機(jī)溶劑可進(jìn)入溶劑再生塔中部,同時(shí)水汽提塔塔底產(chǎn)生的蒸汽進(jìn)入溶劑再生塔底部對(duì)溶劑進(jìn)行水蒸汽蒸餾,溶劑再生塔塔頂流出物進(jìn)入溶劑回收塔塔底。上述方式不僅能夠?qū)τ袡C(jī)溶劑進(jìn)行循環(huán)利用,還能夠保證整個(gè)系統(tǒng)循環(huán)溶劑的使用性能,同時(shí)有利于節(jié)約資源和能源。在本發(fā)明中,可以采用本領(lǐng)域的常規(guī)方法進(jìn)行所述選擇性加氫脫硫,例如S-zorb、RSDS、OCT-M、Prime-G+、CODS等選擇性脫硫方法或其他選擇性深度脫硫方法,也可以為上述方法中的兩種以上方法的組合。在一實(shí)施方式中,可以將所述輕餾分萃取油和重餾分萃取油合并后與氫氣在選擇性加氫脫硫催化劑的作用下進(jìn)行所述選擇性加氫脫硫;其中,控制所述選擇性加氫脫硫的溫度為200-300℃,壓力為1.5-2.5MPa,體積空速為1-5h-1,氫油體積比為400-600。本發(fā)明對(duì)所述選擇性加氫脫硫催化劑不作嚴(yán)格限定,可以為本領(lǐng)域常規(guī)的催化劑。在一實(shí)施方式中,所述選擇性加氫脫硫催化劑可以是公開(kāi)號(hào)為CN104673376A的中國(guó)專利中所公開(kāi)的催化劑。具體地,所述選擇性加氫脫硫催化劑可以由載體負(fù)載活性金屬成分而得到;其中,所述載體可以為分子篩(例如X型、Y型或ZSM-5型)或金屬氧化物(例如三氧化二鋁),所述活性金屬可以包括Co和Mo,Co和Mo在所述載體上的總負(fù)載量可以為5-20%。更進(jìn)一步地,載體上負(fù)載的Co與Mo的質(zhì)量比為(0.2-0.6):1。本發(fā)明的汽油深度脫硫方法,還可以進(jìn)一步對(duì)所述輕餾分萃余油和重餾分萃余油進(jìn)行吸附脫硫。具體地,可以分別對(duì)所述輕餾分萃余油和重餾分萃余油進(jìn)行吸附脫硫,也可以將所述輕餾分萃余油和重餾分萃余油合并為混合油后對(duì)所述混合油進(jìn)行吸附脫硫。在一實(shí)施方式中,本發(fā)明的汽油深度脫硫方法可以包括:對(duì)所述輕餾分萃余油進(jìn)行吸附脫硫,得到輕餾分吸附脫硫油和輕餾分富硫油;對(duì)所述重餾分萃余油進(jìn)行吸附脫硫,得到重餾分吸附脫硫油和重餾分富硫油;將所述輕餾分吸附脫硫油、重餾分吸附脫硫油和所述脫硫餾分混合,得到脫硫汽油。具體地,可以利用脫硫吸附劑進(jìn)行所述吸附脫硫,本發(fā)明對(duì)所采用的脫硫吸附劑不作嚴(yán)格限定,可以為本領(lǐng)域常規(guī)的脫硫吸附劑。在一實(shí)施方式中,所述脫硫吸附劑可以是公開(kāi)號(hào)為CN104667861A的中國(guó)專利中所公開(kāi)的脫硫吸附劑。具體地,所述脫硫吸附劑由分別經(jīng)堿處理的分子篩和活性炭作為復(fù)合載體負(fù)載活性金屬成分而得到;其中,所述活性金屬選自周期表IA、VIII、IB、IIB和VIB族中的一種或多種元素,所述活性金屬在復(fù)合載體上的負(fù)載量為2-30%,優(yōu)選為5-25%,進(jìn)一步優(yōu)選為5-20%。進(jìn)一步地,所述復(fù)合載體中,分子篩與活性炭的質(zhì)量比為(20-80):(80-20),優(yōu)選為(20-60):(80-40);其中,分子篩的類型可以為X型、Y型或ZSM-5型,本發(fā)明對(duì)所采用X型和ZSM-5型分子篩以及活性炭無(wú)嚴(yán)格限制,活性炭的比表面通常可為1000m2/g左右;所述Y型分子篩的骨架硅鋁原子比不小于3.0(XRD法測(cè)定)。此外,所述活性金屬選自Ni、Fe、Ag、Co、Mo、Zn和K中的至少2種。其中,Ni在復(fù)合載體上的負(fù)載量可為10-30%;Fe在復(fù)合載體上的負(fù)載量可為5-15%;Ag在復(fù)合載體上的負(fù)載量可為5-10%;Co在復(fù)合載體上的負(fù)載量可為5-10%;Mo在復(fù)合載體上的負(fù)載量可為5-10%;Zn在復(fù)合載體上的負(fù)載量可為5-15%;K在復(fù)合載體上的負(fù)載量可為5-15%。該負(fù)載量為每種活性金屬各自在復(fù)合載體上的負(fù)載量。進(jìn)一步地,所述活性金屬在復(fù)合載體上的負(fù)載量為2-30%,優(yōu)選為5-25%,進(jìn)一步優(yōu)選為5-20%。在復(fù)合載體上負(fù)載兩種以上活性金屬時(shí),所述負(fù)載量為活性金屬的總負(fù)載量。在一實(shí)施方式中,所述活性金屬為K和Ni;進(jìn)一步地,K在復(fù)合載體上的負(fù)載量為5-15%,Ni在復(fù)合載體上的負(fù)載量為10-25%;更進(jìn)一步地,復(fù)合載體上負(fù)載的K與Ni的質(zhì)量比為(0.2-0.5):1。在另一實(shí)施方式中,所述活性金屬為Zn和Fe;進(jìn)一步地,Zn在復(fù)合載體上的負(fù)載量為5-15%,F(xiàn)e在復(fù)合載體上的負(fù)載量為8-15%;更進(jìn)一步地,復(fù)合載體上負(fù)載的Zn與Fe的質(zhì)量比為(0.5-1):1。上述脫硫吸附劑可參照公開(kāi)號(hào)為CN104667861A的中國(guó)專利中所公開(kāi)的方法進(jìn)行制備和再生。進(jìn)一步地,所述吸附脫硫是利用固定床常壓進(jìn)行,并且控制吸附脫硫的溫度為20-100℃,輕餾分萃余油或重餾分萃余油的流速為0.3-1mL/min。本發(fā)明的吸附脫硫?qū)p餾分萃余油和重餾分萃余油進(jìn)行,由于各萃余油中排除了芳烴,因此可以有效避免芳烴在吸附脫硫過(guò)程中所引起的競(jìng)爭(zhēng)吸附,脫硫效率可高達(dá)100%,并且還能夠延長(zhǎng)吸附劑的使用壽命。此外,還可以進(jìn)一步對(duì)所述輕餾分富硫油和重餾分富硫油進(jìn)行選擇性加氫脫硫,例如可以將所述輕餾分富硫油和重餾分富硫油與所述輕餾分萃取油和重餾分萃取油合并后進(jìn)行選擇性加氫脫硫。本發(fā)明的實(shí)施,至少具有以下優(yōu)勢(shì):1、本發(fā)明的汽油深度脫硫方法,基于對(duì)汽油原料中硫、烯烴和芳烴等組成分布的研究,先在特定的切割溫度下將汽油原料切割為輕餾分和重餾分,隨后對(duì)輕餾分進(jìn)行液液萃取,對(duì)重餾分進(jìn)行萃取蒸餾,在部分脫硫的同時(shí)使烯烴等成分從各餾分中分離,在后續(xù)對(duì)各餾分中其它成分進(jìn)行選擇性加氫脫硫過(guò)程中不僅不會(huì)造成辛烷值的大量損失,還能大幅度地降低總的脫硫負(fù)荷。2、本發(fā)明的汽油深度脫硫方法,不僅按照切割溫度將汽油原料切割為輕餾分和重餾分,還結(jié)合輕餾分和重餾分各自的成分特點(diǎn)對(duì)其組分進(jìn)行劃分,并對(duì)劃分后的各個(gè)組分進(jìn)行有針對(duì)性地脫硫,整個(gè)脫硫過(guò)程更加精細(xì)和高效。3、本發(fā)明的汽油深度脫硫方法,通過(guò)優(yōu)化萃取蒸餾工藝,從而能夠使重餾分中的烯烴與芳烴高度分離,分離度可達(dá)90%以上;并且,烯烴與芳烴的分離還有利于避免在后續(xù)吸附脫硫過(guò)程中所引起的競(jìng)爭(zhēng)吸附,吸附脫硫效率可高達(dá)100%,吸附劑的使用壽命大大延長(zhǎng)。4、本發(fā)明的汽油深度脫硫方法所生產(chǎn)的脫硫汽油中含硫量達(dá)到10ppm以下,辛烷值不僅幾乎未損失甚至略有提高,此外產(chǎn)品收率>95%,脫硫汽油產(chǎn)品的品質(zhì)高。附圖說(shuō)明圖1為本發(fā)明實(shí)施例1的汽油深度脫硫方法的工藝流程圖;圖2為本發(fā)明實(shí)施例2的汽油深度脫硫方法的工藝流程圖;圖3為本發(fā)明一實(shí)施例的汽油深度脫硫方法中萃取蒸餾的工藝流程圖。具體實(shí)施方式為使本發(fā)明的目的、技術(shù)方案和優(yōu)點(diǎn)更加清楚,下面將結(jié)合本發(fā)明的附圖和實(shí)施例,對(duì)本發(fā)明實(shí)施例中的技術(shù)方案進(jìn)行清楚、完整地描述,顯然,所描述的實(shí)施例是本發(fā)明一部分實(shí)施例,而不是全部的實(shí)施例?;诒景l(fā)明中的實(shí)施例,本領(lǐng)域普通技術(shù)人員在沒(méi)有做出創(chuàng)造性勞動(dòng)前提下所獲得的所有其他實(shí)施例,都屬于本發(fā)明保護(hù)的范圍。實(shí)施例11、制備選擇性加氫脫硫催化劑先采用CoSO4溶液對(duì)ZSM-5型分子篩(載體)進(jìn)行等體積浸漬,經(jīng)洗滌、干燥和焙燒后,再采用(NH4)6Mo7O24.4H2O的水溶液對(duì)已浸漬CoSO4溶液的ZSM-5型分子篩進(jìn)行等體積浸漬,經(jīng)洗滌、干燥和焙燒后,制得選擇性加氫脫硫催化劑。上述制備的選擇性加氫脫硫催化劑的總比表面為168m2/g左右,總孔體積為0.378mL/g左右,Co在載體上的負(fù)載量約為7%,Mo在載體上的負(fù)載量約為10%,載體上負(fù)載的Co與Mo的質(zhì)量比為0.7:1。2、汽油脫硫以大慶常壓重油經(jīng)過(guò)催化裂化生產(chǎn)出的催化汽油為原料(其組成見(jiàn)表1),對(duì)該汽油原料進(jìn)行脫硫的工藝流程如圖1和圖3所示。2.1汽油原料切割將上述汽油原料切割為輕餾分和重餾分,其中輕、重餾分的切割溫度為100℃,即:輕餾分為<100℃的餾分,重餾分為>100℃的餾分。2.2液液萃取使輕餾分從抽提塔中下部進(jìn)入,環(huán)丁砜(有機(jī)溶劑)從抽提塔頂部進(jìn)入,并且從抽提塔底部回流裝置注入異戊烷(C5烷烴),控制抽提塔塔頂溫度為65℃,塔底溫度為50℃,塔頂絕對(duì)壓力為0.5MPa,環(huán)丁砜與輕餾分進(jìn)料比為2.0,異戊烷與輕餾分進(jìn)料比為0.2;收集抽提塔塔頂流出物,得到含有烯烴的輕餾分萃余物;收集抽提塔塔底流出物,得到含有硫化物及芳烴的輕餾分萃取物。上述輕餾分萃余物隨后進(jìn)入水洗塔進(jìn)行水洗以去除其中的有機(jī)溶劑,水洗塔塔頂流出物形成含有烯烴的輕餾分萃余油,水洗塔塔底流出物形成水(水洗水);在進(jìn)行水洗時(shí),控制水的用量(基于輕餾分萃余物的量)為3%左右。上述輕餾分萃取物隨后進(jìn)入抽提蒸餾塔頂部,控制抽提蒸餾塔絕對(duì)壓力為0.2MPa,抽提蒸餾塔塔底溫度為160℃,收集抽提蒸餾塔頂部流出物,回收得到C5烷烴,收集抽提蒸餾塔塔底流出物,得到含有輕富硫組分(含有硫化物、芳烴、環(huán)稀及少量的水)、有機(jī)溶劑和水的第一混合物。回收得到的C5烷烴經(jīng)冷凝后可返回至抽提塔底部回流裝置進(jìn)行循環(huán)利用。使上述第一混合物進(jìn)入回收塔中部,控制回收塔絕對(duì)壓力為0.035MPa,回收塔塔底溫度為165℃,收集回收塔塔頂流出物,得到含有輕富硫組分和水的第二混合物,收集回收塔塔底流出物,回收得到有機(jī)溶劑。回收得到的有機(jī)溶劑經(jīng)換熱后可返回抽提塔頂部循環(huán)使用。將上述第二混合物冷凝后進(jìn)行油水分離,得到水和含有硫化物及芳烴的輕餾分萃取油(即輕富硫組分)。得到的水一部分可返回回收塔塔頂,另一部分可用于對(duì)輕餾分萃余物的水洗。2.3萃取蒸餾萃取蒸餾的工藝流程如圖3所示,具體包括:使上述重餾分從萃取蒸餾塔101中下部進(jìn)入,有機(jī)溶劑從萃取蒸餾塔101上部進(jìn)入,重餾分與有機(jī)溶劑在萃取蒸餾塔101中經(jīng)多級(jí)逆流接觸,進(jìn)行脫硫脫芳烴;其中,有機(jī)溶劑為由環(huán)丁砜和三甘醇混合而成的復(fù)合溶劑,復(fù)合溶劑中環(huán)丁砜與三甘醇的體積比為8:2,復(fù)合溶劑的含水量<1.0%,萃取蒸餾塔101理論塔板數(shù)為35,并且萃取蒸餾塔101塔頂溫度為75℃左右,塔底溫度為160℃左右,塔頂絕對(duì)壓力為0.3MPa左右,有機(jī)溶劑與重餾分的進(jìn)料比為3.0左右。經(jīng)脫硫脫芳烴的汽油餾分從萃取蒸餾塔101塔頂引出,得到含有烯烴的重餾分萃余物,重餾分萃余物一部分回流,其中回流比為0.6左右;而萃取了硫化物和芳烴的富溶劑從萃取蒸餾塔101的底部引出,得到重餾分萃取物,其含有重富硫組分(包括硫化物、芳烴、環(huán)烯等)、水和有機(jī)溶劑。在萃取蒸餾塔101中,烯烴與芳烴的分離度達(dá)到90%。上述重餾分萃余物隨后進(jìn)入水洗塔102進(jìn)行水洗以去除其中的有機(jī)溶劑,水洗塔塔頂流出物形成含有烯烴的重餾分萃余油,水洗塔102塔底流出物形成水(水洗水);在進(jìn)行水洗時(shí),控制水的用量(基于重餾分萃余物的量)為3%左右。上述重餾分萃取物隨后進(jìn)入溶劑回收塔103的中部,同時(shí)來(lái)自水汽提塔105的汽提蒸汽進(jìn)入到溶劑回收塔103下部進(jìn)行低真空度的減壓蒸餾操作,以降低塔底溫度,溶劑回收塔103塔底流出物形成有機(jī)溶劑,其含水量為0.6-0.65%,塔頂流出物形成重富硫組分和水的混合物;其中,溶劑回收塔103的理論塔板數(shù)為20,塔頂溫度為70℃左右,塔底溫度為165℃左右,塔頂絕對(duì)壓力為0.04Mpa左右,蒸汽與重餾分萃取物的進(jìn)料比為0.3:100左右。溶劑回收塔103塔頂流出物通過(guò)冷凝器冷凝后進(jìn)入富硫油罐104,對(duì)富硫油罐104抽真空,使重富硫組分和水得到分離,分離出的重富硫組分形成含有硫化物及芳烴的重餾分萃取油,隨后進(jìn)入選擇性加氫脫硫單元進(jìn)行選擇性加氫脫硫,分離出的水一部分返回至溶劑回收塔103頂部進(jìn)行回流,其中回流比為0.8左右,另一部分則返回至水洗塔102中用于重餾分萃余物的水洗。水洗塔102塔底出水進(jìn)入水汽提塔105塔頂進(jìn)行汽提,從而分離水中的微量有機(jī)物,水汽提塔105塔頂流出物隨后進(jìn)入回流罐106進(jìn)行分離,水汽提塔105塔底流出物(即含溶劑的水)隨后進(jìn)入溶劑回收塔103塔底進(jìn)行溶劑回收。水汽提塔105底部通常設(shè)有重沸器,其產(chǎn)生的汽提蒸汽可作為溶劑回收塔103的蒸汽來(lái)源。對(duì)回流罐106進(jìn)行抽真空,使有機(jī)物與水得到分離,分離出的有機(jī)物隨后進(jìn)入萃取蒸餾塔101塔底,分離出的水與水洗塔102塔底流出的水合并后進(jìn)入水汽提塔105塔頂進(jìn)行汽提。溶劑回收塔103塔底流出的有機(jī)溶劑中的一部分先作為水汽提塔105塔底重沸器的熱源,然后與萃取蒸餾塔101塔底的萃取物換熱,再返回至萃取蒸餾塔101塔頂,從而完成有機(jī)溶劑的循環(huán);另一部分則進(jìn)入溶劑再生塔107中部,同時(shí)水汽提塔105塔底產(chǎn)生的蒸汽進(jìn)入溶劑再生塔107底部,對(duì)有機(jī)溶劑進(jìn)行減壓水蒸汽蒸餾,溶劑蒸汽和水蒸氣從溶劑再生塔107塔頂流出后進(jìn)入溶劑回收塔103塔底,溶劑再生塔107塔底不定期排渣,以去除溶劑降解物,保障系統(tǒng)循環(huán)溶劑的使用性能。2.4選擇性加氫脫硫?qū)⑸鲜鲚p餾分萃取油和重餾分萃取油合并后,與氫氣在上述選擇性加氫脫硫催化劑的作用下進(jìn)行選擇性加氫脫硫;其中,控制控制反應(yīng)溫度為260℃,反應(yīng)壓力為1.8MPa,體積空速3.0h-1,氫油體積比(即氫氣與由輕餾分萃取油和重餾分萃取油形成的混合油的體積比)為500,得到脫硫餾分。2.5混合將上述輕餾分萃余油、重餾分萃余油和脫硫餾分混合,得到脫硫汽油,其收率為96%,組成見(jiàn)表1。實(shí)施例2本實(shí)施例在實(shí)施例1的基礎(chǔ)上進(jìn)行改進(jìn),其中不同的是:對(duì)實(shí)施例1的輕餾分萃余油進(jìn)行吸附脫硫,得到輕餾分吸附脫硫油和輕餾分富硫油;并且對(duì)實(shí)施例1的重餾分萃余油進(jìn)行吸附脫硫,得到重餾分吸附脫硫油和重餾分富硫油。隨后,將輕餾分富硫油、重餾分富硫油與實(shí)施例1的輕餾分萃取油和重餾分萃取油合并后進(jìn)行選擇性加氫脫硫,得到脫硫餾分,其工藝流程如圖2所示。利用脫硫吸附劑進(jìn)行上述吸附脫硫,脫硫吸附劑由分別經(jīng)堿處理的ZSM-5型分子篩和活性炭作為復(fù)合載體負(fù)載活性金屬成分而得到;其中,分子篩與活性炭的質(zhì)量比為1:1,活性金屬為K和Ni,K在復(fù)合載體上的負(fù)載量約為5%,Ni在復(fù)合載體上的負(fù)載量約為10%,復(fù)合載體上負(fù)載的K與Ni的質(zhì)量比為0.5:1。經(jīng)檢測(cè),上述脫硫吸附劑的硫容為0.514,壽命長(zhǎng)達(dá)8-9h,吸附脫硫效率達(dá)到100%;其中,硫容為1g脫硫吸附劑將汽油原料中的總含硫量降至10ppmw以下時(shí)所脫除的總硫量(以克計(jì)),即硫容為0.514時(shí),代表1g脫硫吸附劑將汽油原料中的總含硫量降至10ppmw以下時(shí)所脫除的總硫量為0.514g。將上述脫硫吸附劑填裝于固定床反應(yīng)器中,在溫度為30℃以及常壓條件下,以0.5mL/min的流速分別對(duì)輕餾分萃余油和重餾分萃余油進(jìn)行吸附脫硫,得到輕餾分吸附脫硫油和重餾分吸附脫硫油;在吸附脫硫后,采用150℃的水蒸氣吹掃吸附脫硫后的脫硫吸附劑3h進(jìn)行洗滌,分別收取輕餾分富硫油和重餾分富硫油,并將該輕餾分富硫油和重餾分富硫油與實(shí)施例1的輕餾分萃取油和重餾分萃取油合并后進(jìn)行選擇性加氫脫硫,得到脫硫餾分。將輕餾分吸附脫硫油、重餾分吸附脫硫油和脫硫餾分混合,得到脫硫汽油,其收率為96%,組成見(jiàn)表1。實(shí)施例3除萃取蒸餾中,萃取蒸餾塔理論塔板數(shù)為25,萃取蒸餾塔塔頂溫度為80℃左右,塔底溫度為150℃左右,塔頂絕對(duì)壓力為0.2MPa左右,有機(jī)溶劑與重餾分的進(jìn)料比為0.5左右,此時(shí)萃取蒸餾塔中烯烴與芳烴的分離度達(dá)到80%左右;吸附脫硫中,脫硫吸附劑的壽命為3.4h,吸附脫硫效率達(dá)到84%左右之外,其余均與實(shí)施例2相同,得到脫硫汽油,其收率為94%,組成見(jiàn)表1。實(shí)施例41、制備選擇性加氫脫硫催化劑按照實(shí)施例1方法制備選擇性加氫脫硫催化劑,不同的是,控制Co在載體上的負(fù)載量約為4%,Mo在載體上的負(fù)載量約為10%,并且載體上負(fù)載的Co與Mo的質(zhì)量比為0.4:1。2、汽油脫硫以濟(jì)南的催化汽油為原料(其組成見(jiàn)表2),對(duì)該汽油原料進(jìn)行脫硫的工藝流程如下。2.1汽油原料切割將上述汽油原料切割為輕餾分和重餾分,其中輕、重餾分的切割溫度為110℃,即:輕餾分為<110℃的餾分,重餾分為>110℃的餾分。2.2液液萃取采用實(shí)施例1的方法,對(duì)輕餾分進(jìn)行液液萃取,得到含有烯烴的輕餾分萃余油和含有硫化物及芳烴的輕餾分萃取油;其中,不同的是:在液液萃取時(shí),有機(jī)溶劑為四甘醇,C5烷烴為正戊烷;控制抽提塔塔頂溫度為80℃,塔底溫度為60℃,塔頂絕對(duì)壓力為0.2MPa,有機(jī)溶劑與輕餾分進(jìn)料比為2.0,C5烷烴與輕餾分進(jìn)料比為0.2。在對(duì)輕餾分萃余物進(jìn)行水洗時(shí),控制水的用量(基于輕餾分萃余物的量)為4%左右。在對(duì)輕餾分萃取物中的有機(jī)溶劑和C5烷烴進(jìn)行分離時(shí),控制抽提蒸餾塔絕對(duì)壓力為0.2MPa,抽提蒸餾塔塔底溫度為180℃;控制回收塔絕對(duì)壓力為0.025MPa,回收塔塔底溫度為150℃。2.3萃取蒸餾采用實(shí)施例1的方法,對(duì)重餾分進(jìn)行萃取蒸餾,得到含有烯烴的重餾分萃余油和含有硫化物及芳烴的重餾分萃取油;其中,不同的是:在萃取蒸餾時(shí),有機(jī)溶劑為由環(huán)丁砜和四甘醇混合而成的復(fù)合溶劑,復(fù)合溶劑中環(huán)丁砜與四甘醇的體積比為8.5:1.5;萃取蒸餾塔理論塔板數(shù)為35,并且控制萃取蒸餾塔塔頂溫度為100℃左右,塔底溫度為180℃左右,塔頂絕對(duì)壓力為0.3MPa左右,有機(jī)溶劑與重餾分的進(jìn)料比為2.0左右,回流比為2.0左右,此時(shí)萃取蒸餾塔中烯烴與芳烴的分離度達(dá)到90%左右;在對(duì)重餾分萃余物進(jìn)行水洗時(shí),控制水的用量為4%左右。在對(duì)重餾分萃取物中的有機(jī)溶劑進(jìn)行分離時(shí),溶劑回收塔的理論塔板數(shù)為25,塔頂溫度為80℃左右,塔底溫度為185℃左右,塔頂絕對(duì)壓力為0.06MPa左右,蒸汽與重餾分萃取物的進(jìn)料比為0.3:100左右;回流比為2.0左右,溶劑回收塔塔底的有機(jī)溶劑含水量為0.8-0.9%。2.4選擇性加氫脫硫?qū)⑸鲜鲚p餾分萃取油和重餾分萃取油合并后,與氫氣在上述選擇性加氫脫硫催化劑的作用下進(jìn)行選擇性加氫脫硫;其中,控制反應(yīng)溫度300℃、反應(yīng)壓力2.5MPa、體積空速2.0h-1、氫油體積比為400,得到脫硫餾分。2.5混合將上述輕餾分萃余油、重餾分萃余油和脫硫餾分混合,得到脫硫汽油,其收率為96%,組成見(jiàn)表2。實(shí)施例5本實(shí)施例在實(shí)施例4的基礎(chǔ)上進(jìn)行改進(jìn),其中不同的是:對(duì)實(shí)施例4的輕餾分萃余油進(jìn)行吸附脫硫,得到輕餾分吸附脫硫油和輕餾分富硫油;并且對(duì)實(shí)施例4的重餾分萃余油進(jìn)行吸附脫硫,得到重餾分吸附脫硫油和重餾分富硫油。隨后,將輕餾分富硫油、重餾分富硫油與實(shí)施例4的輕餾分萃取油和重餾分萃取油合并后進(jìn)行選擇性加氫脫硫,得到脫硫餾分。利用脫硫吸附劑進(jìn)行上述吸附脫硫,脫硫吸附劑由分別經(jīng)堿處理的Y型分子篩和活性炭作為復(fù)合載體負(fù)載活性金屬成分而得到,其中,活性金屬為Zn和Fe,Zn在復(fù)合載體上的負(fù)載量約為10%,F(xiàn)e在復(fù)合載體上的負(fù)載量約為10%,復(fù)合載體上負(fù)載的Zn與Fe的質(zhì)量比為1:1。該脫硫吸附劑的硫容為0.481,壽命長(zhǎng)達(dá)7-8h,吸附脫硫效率達(dá)到100%。將上述脫硫吸附劑填裝于固定床反應(yīng)器中,在溫度為30℃以及常壓條件下,以0.3mL/min的流速分別對(duì)輕餾分萃余油和重餾分萃余油進(jìn)行吸附脫硫,得到輕餾分吸附脫硫油和重餾分吸附脫硫油;在吸附脫硫后,采用180℃的水蒸氣吹掃吸附脫硫后的脫硫吸附劑1h進(jìn)行洗滌,分別收取輕餾分富硫油和重餾分富硫油,將該輕餾分富硫油和重餾分富硫油與實(shí)施例4的輕餾分萃取油和重餾分萃取油合并后進(jìn)行選擇性加氫脫硫,得到脫硫餾分。將輕餾分吸附脫硫油、重餾分吸附脫硫油和脫硫餾分混合,得到脫硫汽油,其收率為96%,組成見(jiàn)表2。對(duì)照例1除不進(jìn)行實(shí)施例1的萃取蒸餾,而直接將實(shí)施例1的輕餾分萃取油與重餾分合并后進(jìn)行選擇性加氫脫硫,得到脫硫餾分;將輕餾分萃余油和脫硫餾分混合,得到脫硫汽油(組成見(jiàn)表1),其收率為94%,脫硫汽油含硫量為8.5ppm,辛烷值損失達(dá)到2個(gè)單位。表1脫硫前后汽油的組成對(duì)照例2除不進(jìn)行實(shí)施例4的萃取蒸餾,而直接將實(shí)施例4的輕餾分萃取油和重餾分合并后進(jìn)行選擇性加氫脫硫,得到脫硫餾分;將輕餾分萃余油和脫硫餾分混合,得到脫硫汽油(組成見(jiàn)表2),其收率為94%,脫硫汽油含硫量為9.3ppm,辛烷值損失達(dá)到2個(gè)單位。表2脫硫前后汽油的組成對(duì)照例3除不進(jìn)行實(shí)施例1的汽油切割,而直接采用實(shí)施例1方法對(duì)實(shí)施例1的汽油原料進(jìn)行萃取蒸餾,得到萃取油和萃余油,隨后采用實(shí)施例1方法對(duì)萃取油進(jìn)行選擇性加氫脫硫,得到脫硫汽油;將萃余油與脫硫汽油混合,得到脫硫汽油,其收率為94%,脫硫汽油含硫量為8.9ppm,辛烷值損失達(dá)到1.4個(gè)單位。由上述結(jié)果可知:1、采用本發(fā)明各實(shí)施例方法對(duì)汽油原料進(jìn)行脫硫時(shí),脫硫汽油中含硫量達(dá)到10ppm以下,辛烷值降低<1個(gè)單位,產(chǎn)品收率>95%(實(shí)施例3除外);而對(duì)照例1和對(duì)照例2方法不進(jìn)行本發(fā)明的萃取蒸餾,而直接對(duì)重餾分進(jìn)行選擇性加氫脫硫,此時(shí)辛烷值損失達(dá)到2個(gè)單位;對(duì)照例3方法不進(jìn)行汽油切割而直接對(duì)汽油原料全餾分進(jìn)行萃取蒸餾,辛烷值損失達(dá)到1.4個(gè)單位。2、本發(fā)明各實(shí)施例的萃取蒸餾可使重餾分中的烯烴與芳烴高度分離,分離度可達(dá)80%以上,甚至90%以上;并且,烯烴與芳烴的分離還有利于避免在后續(xù)吸附脫硫過(guò)程中所引起的競(jìng)爭(zhēng)吸附,吸附脫硫效率可高達(dá)100%,吸附劑的使用壽命大大延長(zhǎng)。最后應(yīng)說(shuō)明的是:以上各實(shí)施例僅用以說(shuō)明本發(fā)明的技術(shù)方案,而非對(duì)其限制;盡管參照前述各實(shí)施例對(duì)本發(fā)明進(jìn)行了詳細(xì)的說(shuō)明,本領(lǐng)域的普通技術(shù)人員應(yīng)當(dāng)理解:其依然可以對(duì)前述各實(shí)施例所記載的技術(shù)方案進(jìn)行修改,或者對(duì)其中部分或者全部技術(shù)特征進(jìn)行等同替換;而這些修改或者替換,并不使相應(yīng)技術(shù)方案的本質(zhì)脫離本發(fā)明各實(shí)施例技術(shù)方案的范圍。