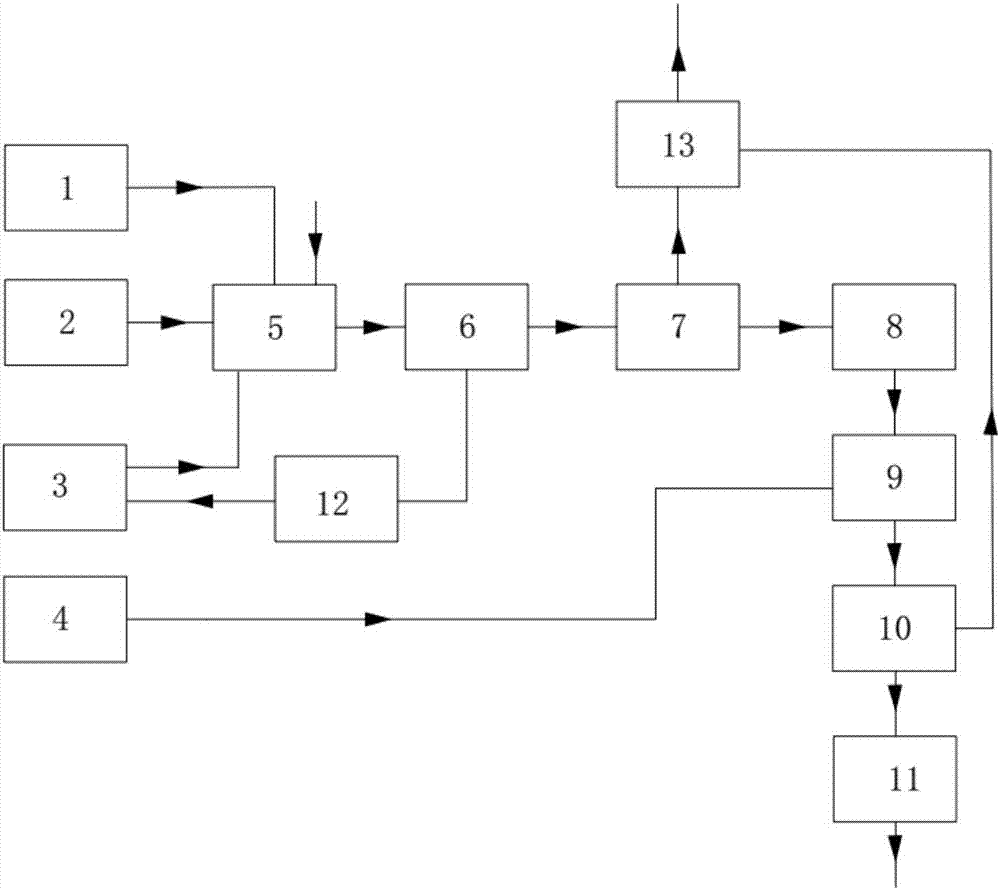
本發(fā)明涉及工業(yè)催化劑制備的工藝領域,特別涉及一種乙炔加氫催化劑的制備方法。
背景技術:
:在石油化工領域,由石油裂解制備乙烯工藝過程中,通常含有微量的乙炔,為防止乙炔對乙烯聚合反應催化劑的毒化,工業(yè)中需要進行除炔,其中乙炔催化選擇加氫是最有效的一種方法,也是近些年來研究的熱點。催化劑的反應體系也均是針對降低富乙烯環(huán)境中乙炔加氫制乙烯的工藝條件。而在煤化工技術中,以煤為原料通過電石工藝制取乙炔,已廣泛應用。以乙炔為原料,在選擇性加氫催化劑作用下,通過加氫制備乙烯產(chǎn)品,可進一步拓展煤化工路線。由于乙炔選擇加氫過程大多數(shù)反應均為放熱反應,在富乙炔加氫中,放熱量劇大,同時為迅速移熱,乙炔選擇加氫新的反應體系通常發(fā)生在漿態(tài)床,為氣(乙炔+氫氣)—液(溶劑)—固(催化劑)三相。而在之前的富乙烯除炔過程,選擇催化加氫的催化劑大多數(shù)均是在固定床內(nèi),反應體系為氣-固兩相反應。在新的三相反應體系中,催化劑的水熱穩(wěn)定性對催化劑的壽命以及催化活性和選擇性影響巨大,因此必須高度重視。同時電石法制乙炔以及凈化后,可能仍含有H2S、AsH3、PH3等雜質氣體,很容易導致催化劑中毒。然而上述問題在催化劑在相關研究均未見報道。此外,傳統(tǒng)的催化加氫都是以貴金屬Pd為主要催化劑,另外需添加Ag、Au等助劑,催化劑成本較高,而Ni在選擇催化加氫中性能雖然減少,但由于其制備成本較低而依然受到關注。即使在小試催化劑制備中,催化劑性能良好,按照小試直接放大,在工業(yè)中卻并不一定能實現(xiàn)良好的效果,催化劑性能難得到保障。技術實現(xiàn)要素:對于現(xiàn)有技術中存在的上述問題,發(fā)明人經(jīng)過大量的創(chuàng)造性工作,提出了一種乙炔加氫催化劑的制備方法,具體方法如下:包含以下步驟:步驟1,分別配置第一溶液、第二溶液、第三溶液以及第四溶液;步驟2,將第一溶液、第二溶液以及第三溶液注入水熱反應釜并設定水熱反應釜的溫度、攪拌轉速以及攪拌時間;步驟3,在水熱反應釜內(nèi)加入載體材料,控制載體材料加入速度并攪拌,載體材料完全加入后將水熱反應釜密封并在設定的溫度與壓力下持續(xù)攪拌;步驟4,將步驟3攪拌后得到的混合溶液送入連續(xù)微波干燥器迅速干燥,并將完成干燥的固態(tài)物送入旋轉煅燒爐;步驟5,在旋轉煅燒爐中煅燒固態(tài)物;步驟6,將第四溶液注入水熱反應釜,并將在步驟5煅燒后的固態(tài)物加入到水熱反應釜中進行攪拌,隨后轉移至擠壓過濾機中過濾;步驟7,將過濾后的固態(tài)物轉移到氮氣烘干箱,在氮氣氛圍下干燥得到催化劑;其中第一溶液與第二溶液分別為鎳鹽,鋅鹽,鈀鹽,銀鹽,以及其它過渡金屬或堿土金屬鹽的飽和溶液的至少一種;其中第三溶液由有機溶劑氮甲基吡咯烷酮(NMP)、二甲基酰胺(DMF)、四氫呋喃(THF)、二甲基亞砜(DMSO)、一甲胺(MMA)的至少一種與六次甲基四胺和聚乙烯吡咯烷酮(PVP)組成;其中第四溶液為硼氫化鈉(NaBH4)的堿性溶液。進一步地,步驟1中的第一至第四溶液的配置在第一到第四溶劑罐中進行。進一步地,步驟2中的水熱反應釜的溫度為70~90℃、攪拌轉速為20~40轉/分鐘,攪拌時間為1~2h。進一步地,步驟3中的載體材料為納米級α-Al2O3、分子篩、氧化硅、氧化鈦、堇青石中的至少一種,其中α-Al2O3的粒徑≤80nm,比表面積≤20m2/g。進一步地,步驟3中向水熱反應釜加入載體材料以10~15kg/min的速度進行。進一步地,步驟3中水熱反應釜的設定的溫度為85~95℃,設定的壓力為0.1~0.3MPa,攪拌轉速為10~20rpm,攪拌時間為6~10小時。進一步地,步驟4中的干燥溫度為210~220℃,時間為5~10min。進一步地,步驟4在連續(xù)微波干燥器的干燥過程中蒸出的氣體經(jīng)冷凝后回流至配置第三溶液的溶劑罐中以重復利用。進一步地,步驟5的煅燒過程中控制旋轉煅燒爐各段的溫度、停留時間以及轉速。進一步地,各段的溫度分別為200~260℃、300~360℃、350℃~460℃,停留時間為4~6小時,轉速為5-7rpm。進一步地,步驟6的攪拌時間為4~10小時。進一步地,步驟6中由擠壓過濾機過濾出的堿性液體以及步驟5中煅燒得到的廢氣轉移至噴淋塔中,通過調控氣液比,堿性液體可以用于處理旋轉煅燒爐中排放的有害廢氣。進一步地,通過上述調控,氣相與液相的體積比為1:3~5。進一步地,步驟7中的干燥時間為24小時,干燥溫度為120℃。進一步地,第一溶液優(yōu)選為硝酸鎳飽和溶液,第二溶液優(yōu)選為硝酸鋅飽和溶液,第三溶液優(yōu)選由氮甲基吡咯烷酮、六次甲基四胺和聚乙烯吡咯烷酮(PVP)組成,第四溶液為硼氫化鈉(NaBH4)堿性溶液,其中溶液由氫氧化鈉將pH值調節(jié)為9~10。進一步地,上述各組分的配比以重量份計分別為:載體α-Al2O3為90~110份,NMP為60~80份,硝酸鎳溶液為6~13份,硝酸鋅溶液為20~40份,六次甲基四胺為1~5份,PVP為1~3份,硼氫化鈉為20~60份,氫氧化鈉為10~20份。本發(fā)明還公開了一種上述方法制備的催化劑的應用方法,包含以下步驟:步驟1,將氫氣與乙炔組成原料氣,原料氣中含有雜質氣體;步驟2,將原料氣從反應器底部通入催化劑與有機溶劑組成溶液中;步驟3,在加熱條件下連續(xù)反應并收集氣相物質,即獲得乙烯產(chǎn)品。進一步地,步驟1中氫氣與乙炔的摩爾比為4~6:1,原料氣中含有的雜質氣體包含H2S、AsH3、PH3等,其含量共計40ppm。進一步地,步驟2中原料氣以900~1100ml/min的流速通入到溶液中。進一步地,有機溶劑可以為氮甲基吡咯烷酮(NMP)、二甲基酰胺(DMF)、四氫呋喃(THF)、二甲基亞砜(DMSO)以及一甲胺(MMA)中的一種或多種。通過本發(fā)明的方法得到的催化劑具有以下有益效果:(1)制備出的催化劑能夠較好的適用于電石法乙炔選擇加氫制乙烯時氣-液-固反應體系中,解決傳統(tǒng)制備工藝催化劑的溶劑熱不穩(wěn)定,活性組分易流失,催化劑放大后活性差等難題;(2)采用非貴金屬元素,可顯著降低催化劑價格;(3)采用化學溶劑對催化劑進行還原,避免傳統(tǒng)高溫氫氣還原,降低了能耗;(4)利用反應過程中廢堿液與煅燒產(chǎn)生的酸性氣體進行吸收,有效降低了污染廢氣的排放,安全環(huán)保,解決了傳統(tǒng)制備工藝污染問題;(5)使用該催化劑進行乙烯的制備,可以得到較高的乙炔轉化率以及乙烯收率,并且催化劑壽命與現(xiàn)有催化劑相比明顯增長。附圖說明本發(fā)明的上述和/或附加的方面和優(yōu)點在與附圖結合對實施例進行的描述中將更加明顯并容易理解,其中:圖1示出了根據(jù)本發(fā)明的乙炔加氫催化劑的制備方法的流程示意圖;圖2示出了制備本發(fā)明的乙炔加氫催化劑的系統(tǒng)的示意圖。附圖標記:1第一溶劑罐;2第二溶劑罐;3第三溶劑罐;4第四溶劑罐;5水熱反應釜;6連續(xù)微波干燥器;7旋轉煅燒爐;8煅燒后的產(chǎn)品;9水熱反應釜;10擠壓過濾機;11氮氣烘干箱;12冷凝器;13噴淋塔。具體實施方式應當理解,在示例性實施例中所示的本發(fā)明的實施例僅是說明性的。雖然在本發(fā)明中僅對少數(shù)實施例進行了詳細描述,但本領域技術人員很容易領會在未實質脫離本發(fā)明主題的教導情況下,多種修改是可行的。相應地,所有這樣的修改都應當被包括在本發(fā)明的范圍內(nèi)。在不脫離本發(fā)明的主旨的情況下,可以對以下示例性實施例的設計、操作條件和參數(shù)等做出其他的替換、修改、變化和刪減。實施例一根據(jù)圖1及圖2所示,在步驟S100中,按照下表1稱取以下質量份數(shù)的各物質,第一溶劑罐1中為硝酸鎳飽和溶液(20℃硝酸鎳下飽和溶液是94.2/100g水,下同),第二溶劑罐2中為硝酸鋅飽和溶液(25℃下硝酸鋅飽和溶液為127g/100g水,下同),第三溶劑罐3中為由氮甲基吡咯烷酮(NMP)、六次甲基四胺以及聚乙烯吡咯烷酮(PVP)組成的混合溶液,第四溶劑罐4中為硼氫化鈉(NaBH4)堿性溶液,將配置好的上述各溶液備用。樣品名稱質量份數(shù)α-Al2O3100氮甲基吡咯烷酮(NMP)60硝酸鎳飽和溶液10硝酸鋅飽和溶液30六次甲基四胺2.5聚乙烯吡咯烷酮(PVP)2硼氫化鈉40去離子水40氫氧化鈉10表1在步驟S200,將第一、第二、第三溶劑罐1-3中的溶液由泵注入水熱反應釜5,設定水熱反應釜溫度70℃、轉速20~40rpm,在水熱反應釜中攪拌2h。隨后在步驟S300向水熱反應釜5中加入作為載體的納米級α-Al2O3,加料速度控制在10kg/min,并持續(xù)攪拌,此時水熱反應釜的轉速設置為10~20rpm,待載體完全加入后將水熱反應釜密閉,繼續(xù)攪拌,維持溫度85℃,壓力0.1MPa,6小時后取出。在步驟S400,將上述步驟從水熱反應釜5中取出的物質轉移至連續(xù)微波干燥器6內(nèi),控制微波干燥溫度為210℃,時間10min,使其迅速干燥。在步驟S500,干燥完成后固態(tài)物直接送入旋轉煅燒爐7。在旋轉煅燒爐7中控制三段測溫點溫度分別為250±10℃,350±10℃,450±10℃,轉速為6rpm,其中在高溫度段維持時間為5小時,自然冷卻得到煅燒后的產(chǎn)品8。在步驟S600,將第四溶劑罐4中的硼氫化鈉堿性溶液注入水熱反應釜9中,同時將煅燒后的產(chǎn)品8添加至9中,攪拌4小時后,轉移至擠壓過濾機10中過濾。在步驟S700,將過濾后的固體物質轉移至氮氣烘干箱11中,控制氮氣流速1L/min,在氮氣氛圍下干燥24小時后即得催化劑產(chǎn)品,密閉保存即可。由連續(xù)微波干燥器6蒸出的氣體經(jīng)冷凝器12冷凝后回流至第三溶劑罐3中以重復使用。而由擠壓過濾機10過濾出的堿性液體轉移至噴淋塔13中,通過將氣液體積比控制為1:3,可以有效處理旋轉煅燒爐7中由煅燒產(chǎn)生的有害廢氣,實現(xiàn)廢氣和廢液達標排放。在對本實施例1所得的催化劑進行應用測試時,將氫氣和乙炔以摩爾比4:1組成原料氣,原料氣中含有H2S、AsH3、PH3等雜質氣體共計40ppm。以流速1000ml/min從反應器底部通入液相溶劑NMP120g以及本實施例1所得催化劑8g組成的溶液,操作壓力為0.15MPa,在140℃條件下連續(xù)反應,收集氣相物質,即為所得產(chǎn)物及副產(chǎn)物。經(jīng)分析,所制備的催化劑的乙炔轉化率可達99%以上,乙烯收率94%以上,催化劑循環(huán)壽命400小時。實施例二同樣根據(jù)圖1及圖2所示,在步驟S100中,按照下表2稱取以下質量份數(shù)的各物質,第一溶劑罐1中為硝酸鎳飽和溶液,第二溶劑罐2中為硝酸鋅飽和溶液,第三溶劑罐3中為由氮甲基吡咯烷酮(NMP)、六次甲基四胺以及聚乙烯吡咯烷酮(PVP)組成的混合溶液,第四溶劑罐4中為硼氫化鈉(NaBH4)堿性溶液,將配置好的上述各溶液備用。樣品名稱質量份數(shù)α-Al2O3100氮甲基吡咯烷酮(NMP)70硝酸鎳飽和溶液10硝酸鋅飽和溶液30六次甲基四胺2.5聚乙烯吡咯烷酮(PVP)2硼氫化鈉40去離子水40氫氧化鈉10表2在步驟S200,將第一、第二、第三溶劑罐1-3中的溶液由泵注入水熱反應釜5,設定水熱反應釜溫度90℃、轉速20~40rpm,在水熱反應釜中攪拌1h。隨后在步驟S300向水熱反應釜5中加入作為載體的納米級α-Al2O3,加料速度控制在15kg/min,并持續(xù)攪拌,此時水熱反應釜的轉速設置為10~20rpm,待載體完全加入后將水熱反應釜密閉,繼續(xù)攪拌,維持溫度95℃,壓力0.3MPa,10小時后取出。在步驟S400,將上述步驟從水熱反應釜5中取出的物質轉移至連續(xù)微波干燥器6內(nèi),控制微波干燥溫度為220℃,時間5min,使其迅速干燥。在步驟S500,干燥完成后固態(tài)物直接送入旋轉煅燒爐7。在旋轉煅燒爐7中控制三段測溫點溫度分別為210±10℃,310±10℃,360±10℃,轉速為7rpm,其中在高溫度段維持時間為6小時,自然冷卻得到煅燒后的產(chǎn)品8。在步驟S600,將第四溶劑罐4中的硼氫化鈉堿性溶液注入水熱反應釜9中,同時將煅燒后的產(chǎn)品8添加至9中,攪拌10小時后,轉移至擠壓過濾機10中過濾。在步驟S700,將過濾后的固體物質轉移至氮氣烘干箱11中,控制氮氣流速1L/min,在氮氣氛圍下干燥24小時后即得催化劑產(chǎn)品,密閉保存即可。由連續(xù)微波干燥器6蒸出的氣體經(jīng)冷凝器12冷凝后回流至第三溶劑罐3中以重復使用。而由擠壓過濾機10過濾出的堿性液體轉移至噴淋塔13中,通過將氣液體積比控制為1:3,可以有效處理旋轉煅燒爐7中由煅燒產(chǎn)生的有害廢氣,實現(xiàn)廢氣和廢液達標排放。在對本實施例2所得的催化劑進行應用測試時,將氫氣和乙炔以摩爾比6:1組成原料氣,原料氣中含有H2S、AsH3、PH3等雜質氣體共計40ppm。以流速1000ml/min從反應器底部通入液相溶劑DMF120g以及本實施例2所得催化劑8g組成的溶液中,操作壓力為0.15MPa,在140℃條件下連續(xù)反應,收集氣相物質,即為所得產(chǎn)物及副產(chǎn)物。經(jīng)分析,所制備的催化劑的乙炔轉化率可達99%以上,乙烯收率94%以上,催化劑循環(huán)壽命420小時。實施例三同樣根據(jù)圖1及圖2所示,在步驟S100中,按照下表3稱取以下質量份數(shù)的各物質,第一溶劑罐1中為硝酸鎳飽和溶液,第二溶劑罐2中為硝酸鋅飽和溶液,第三溶劑罐3中為由氮甲基吡咯烷酮(NMP)、六次甲基四胺以及聚乙烯吡咯烷酮(PVP)組成的混合溶液,第四溶劑罐4中為硼氫化鈉(NaBH4)堿性溶液,將配置好的上述各溶液備用。樣品名稱質量份數(shù)α-Al2O390氮甲基吡咯烷酮(NMP)80硝酸鎳飽和溶液6硝酸鋅飽和溶液20六次甲基四胺1聚乙烯吡咯烷酮(PVP)1硼氫化鈉20去離子水40氫氧化鈉10表3在步驟S200,將第一、第二、第三溶劑罐1-3中的溶液由泵注入水熱反應釜5,設定水熱反應釜溫度90℃、轉速20~40rpm,在水熱反應釜中攪拌1h。隨后在步驟S300向水熱反應釜5中加入作為載體的納米級α-Al2O3,加料速度控制在15kg/min,并持續(xù)攪拌,此時水熱反應釜的轉速設置為10~20rpm,待載體完全加入后將水熱反應釜密閉,繼續(xù)攪拌,維持溫度95℃,壓力0.3MPa,10小時后取出。在步驟S400,將上述步驟從水熱反應釜5中取出的物質轉移至連續(xù)微波干燥器6內(nèi),控制微波干燥溫度為220℃,時間5min,使其迅速干燥。在步驟S500,干燥完成后固態(tài)物直接送入旋轉煅燒爐7。在旋轉煅燒爐7中控制三段測溫點溫度分別為240±10℃,320±10℃,390±10℃,轉速為5rpm,其中在高溫度段維持時間為9小時,自然冷卻得到煅燒后的產(chǎn)品8。在步驟S600,將第四溶劑罐4中的硼氫化鈉堿性溶液注入水熱反應釜9中,同時將煅燒后的產(chǎn)品8添加至9中,攪拌10小時后,轉移至擠壓過濾機10中過濾。在步驟S700,將過濾后的固體物質轉移至氮氣烘干箱11中,控制氮氣流速1L/min,在氮氣氛圍下干燥24小時后即得催化劑產(chǎn)品,密閉保存即可。由連續(xù)微波干燥器6蒸出的氣體經(jīng)冷凝器12冷凝后回流至第三溶劑罐3中以重復使用。而由擠壓過濾機10過濾出的堿性液體轉移至噴淋塔13中,通過將氣液體積比控制為1:4,可以有效處理旋轉煅燒爐7中由煅燒產(chǎn)生的有害廢氣,實現(xiàn)廢氣和廢液達標排放。在對本實施例3所得的催化劑進行應用測試時,將氫氣和乙炔以摩爾比6:1組成原料氣,原料氣中含有H2S、AsH3、PH3等雜質氣體共計40ppm。以流速1100ml/min從反應器底部通入液相溶劑DMF140g以及本實施例3所得催化劑9g組成的溶液中,操作壓力為0.15MPa,在140℃條件下連續(xù)反應,收集氣相物質,即為所得產(chǎn)物及副產(chǎn)物。經(jīng)分析,所制備的催化劑的乙炔轉化率可達99%以上,乙烯收率96%以上,催化劑循環(huán)壽命400小時。實施例四同樣根據(jù)圖1及圖2所示,在步驟S100中,按照下表4稱取以下質量份數(shù)的各物質,第一溶劑罐1中為硝酸鎳飽和溶液,第二溶劑罐2中為硝酸鋅飽和溶液,第三溶劑罐3中為由氮甲基吡咯烷酮(NMP)、六次甲基四胺以及聚乙烯吡咯烷酮(PVP)組成的混合溶液,第四溶劑罐4中為硼氫化鈉(NaBH4)堿性溶液,將配置好的上述各溶液備用。樣品名稱質量份數(shù)α-Al2O3110氮甲基吡咯烷酮(NMP)70硝酸鎳飽和溶液13硝酸鋅飽和溶液40六次甲基四胺5聚乙烯吡咯烷酮(PVP)2硼氫化鈉60去離子水40氫氧化鈉20表4在步驟S200,將第一、第二、第三溶劑罐1-3中的溶液由泵注入水熱反應釜5,設定水熱反應釜溫度90℃、轉速20~40rpm,在水熱反應釜中攪拌1h。隨后在步驟S300向水熱反應釜5中加入作為載體的納米級α-Al2O3,加料速度控制在15kg/min,并持續(xù)攪拌,此時水熱反應釜的轉速設置為10~20rpm,待載體完全加入后將水熱反應釜密閉,繼續(xù)攪拌,維持溫度95℃,壓力0.3MPa,10小時后取出。在步驟S400,將上述步驟從水熱反應釜5中取出的物質轉移至連續(xù)微波干燥器6內(nèi),控制微波干燥溫度為220℃,時間5min,使其迅速干燥。在步驟S500,干燥完成后固態(tài)物直接送入旋轉煅燒爐7。在旋轉煅燒爐7中控制三段測溫點溫度分別為210±10℃,310±10℃,360±10℃,轉速為7rpm,其中在高溫度段維持時間為4小時,自然冷卻得到煅燒后的產(chǎn)品8。在步驟S600,將第四溶劑罐4中的硼氫化鈉堿性溶液注入水熱反應釜9中,同時將煅燒后的產(chǎn)品8添加至9中,攪拌10小時后,轉移至擠壓過濾機10中過濾。在步驟S700,將過濾后的固體物質轉移至氮氣烘干箱11中,控制氮氣流速1L/min,在氮氣氛圍下干燥24小時后即得催化劑產(chǎn)品,密閉保存即可。由連續(xù)微波干燥器6蒸出的氣體經(jīng)冷凝器12冷凝后回流至第三溶劑罐3中以重復使用。而由擠壓過濾機10過濾出的堿性液體轉移至噴淋塔13中,通過將氣液體積比控制為1:5,可以有效處理旋轉煅燒爐7中由煅燒產(chǎn)生的有害廢氣,實現(xiàn)廢氣和廢液達標排放。在對本實施例4所得的催化劑進行應用測試時,將氫氣和乙炔以摩爾比6:1組成原料氣,原料氣中含有H2S、AsH3、PH3等雜質氣體共計40ppm。以流速1000ml/min從反應器底部通入液相溶劑DMF120g以及本實施例4所得催化劑8g組成的溶液中,操作壓力為0.15MPa,在140℃條件下連續(xù)反應,收集氣相物質,即為所得產(chǎn)物及副產(chǎn)物。經(jīng)分析,所制備的催化劑的乙炔轉化率可達99%以上,乙烯收率96%以上,催化劑循環(huán)壽命440小時。以上僅為本發(fā)明的較佳實施例,并非用來限定本發(fā)明的實施范圍;如果不脫離本發(fā)明的精神和范圍,對本發(fā)明進行修改或者等同替換,均應涵蓋在本發(fā)明權利要求的保護范圍當中。當前第1頁1 2 3