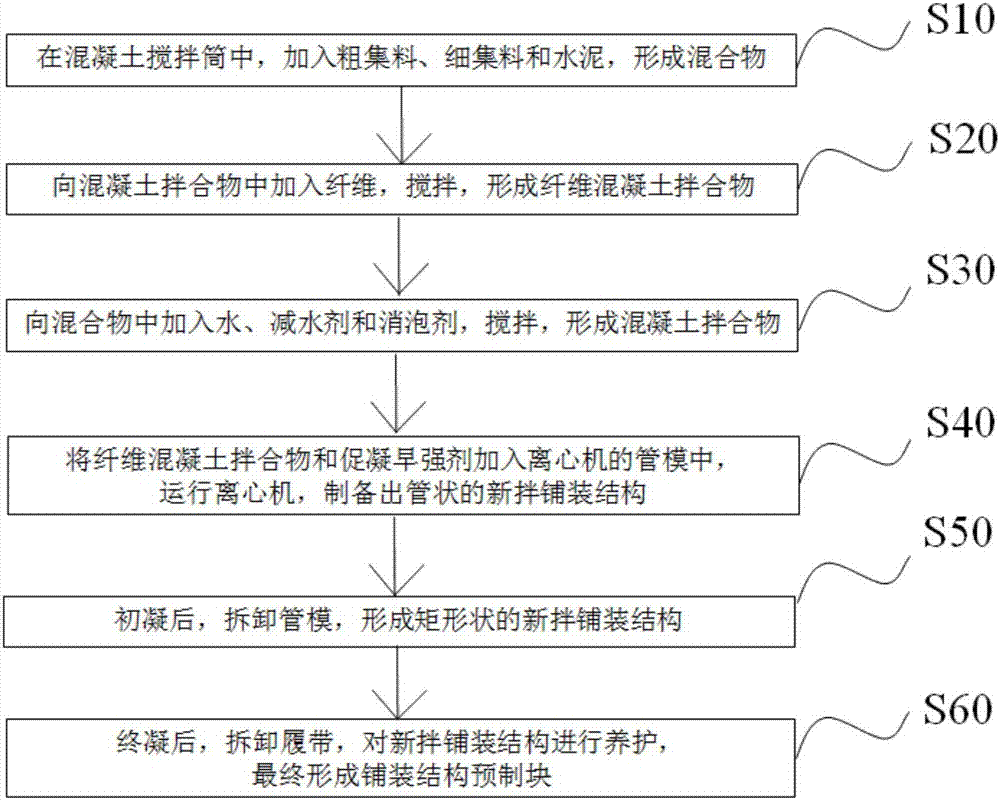
本發(fā)明屬于道路材料領(lǐng)域,具體來說,涉及一種道路路面或機場道面鋪裝結(jié)構(gòu)的制備方法。
背景技術(shù):
:道路路面、機場道面常采用水泥混凝土作為道路路面和機場道面材料,水泥混凝土具有其原材料來源廣泛、制作工藝簡便,應(yīng)用方便等優(yōu)點。然而水泥混凝土路面板、道面板也存在抗拉強度低、韌性差和裂縫易擴展等缺點,混凝土的抗彎拉強度比抗壓強度低得多,在輪載作用下當(dāng)彎拉應(yīng)力超過混凝土的極限抗彎拉強度時,水泥混凝土面板便會產(chǎn)生斷裂破壞,且在荷載重復(fù)作用下,由于疲勞效應(yīng)混凝土板會在低于其極限抗彎拉強度時出現(xiàn)破壞。此外,混凝土板厚度方向的溫差會使板產(chǎn)生溫度翹曲應(yīng)力,對混凝土板受力不利。水泥混凝土是脆性材料,它在斷裂時的相對拉伸變形很小,對地基變形的適應(yīng)能力不足,土基和基層的變形對混凝土板的影響很大,不均勻的基礎(chǔ)變形會造成混凝土板與基層脫空,產(chǎn)生過大的彎拉應(yīng)力。根據(jù)《公路水泥混凝土路面設(shè)計規(guī)范jtgd40-2011》,進行水泥混凝土路面設(shè)計時,取混凝土板的抗彎拉強度作為設(shè)計指標(biāo),滿足荷載疲勞應(yīng)力與溫度疲勞翹曲應(yīng)力之和不超過混凝土的抗彎拉強度。水泥混凝土機場道面設(shè)計與路面設(shè)計類似,根據(jù)板邊臨界荷位處的彎拉應(yīng)力來進行設(shè)計。由于水泥混凝土的這些特點,加上環(huán)境因素(水分等)的作用,容易造成由板底開裂向上擴展形成的裂縫,以及板底脫空現(xiàn)象,進而導(dǎo)致斷板等嚴(yán)重病害,這些缺點嚴(yán)重影響了混凝土路面(道面)面層材料的耐久性和使用壽命,因此改善水泥混凝土路面(道面)材料的性能,尤其是抗彎拉性能顯得尤為重要。實際水泥混凝土路面(道面)在車輛荷載(飛機荷載)作用下,由于水泥混凝土為脆性材料,抗壓模量高,而抗拉強度遠(yuǎn)低于抗壓強度,所以首要考慮水平拉應(yīng)力的影響。荷載作用下路面(道面)面層內(nèi)水平應(yīng)力狀況可以簡述為:上部區(qū)域受高壓應(yīng)力、中部區(qū)域為應(yīng)力過渡區(qū)域、下部區(qū)域受高拉應(yīng)力,從上至下為最大水平壓應(yīng)力到最大水平拉應(yīng)力逐漸過渡,尤其是在底部對混凝土的抗拉性能要求最高。然而普通的混凝土由于施工時為均勻拌和,可以視為均質(zhì)的材料,其各個位置的力學(xué)性能基本一致,水泥混凝土板力學(xué)性能沿著板厚方向是無變化的,這并不符合路面(道面)面層內(nèi)部的實際應(yīng)力分布的特點,尤其是抗拉強度沿厚度方向一致,在實際荷載作用下水泥混凝土板板底處產(chǎn)生的最大拉應(yīng)力易超過抗拉強度而產(chǎn)生裂縫而破壞。另外,普通水泥混凝土為脆性材料,變形能力較差,其彈性模量遠(yuǎn)高于基層(如水泥穩(wěn)定粒料),因而兩者之間的變形協(xié)調(diào)能力較差,致使混凝土板板底容易因脫空而產(chǎn)生過大的彎拉應(yīng)力,進而導(dǎo)致開裂破壞。所以,對路面(道面)面層結(jié)構(gòu)的性能改善使其力學(xué)性能能夠漸變,更為契合混凝土路面(道面)面層的實際受力狀況,并且降低混凝土路面(道面)面層底部的模量并增強其變形性能,使其與基層具有良好的變形協(xié)調(diào)能力,以滿足路面(道面)的使用要求具有重要研究意義。技術(shù)實現(xiàn)要素:技術(shù)問題:本發(fā)明實施例所要解決的技術(shù)問題是:提供一種道路路面或機場道面鋪裝結(jié)構(gòu)的制備方法,能夠制備出性能梯度分布的鋪裝結(jié)構(gòu)。技術(shù)方案:為解決上述技術(shù)問題,本發(fā)明實施例采用如下的技術(shù)方案:一種上述的道路路面或機場道面鋪裝結(jié)構(gòu)的制備方法,該制備方法包括以下步驟:s10:在混凝土攪拌筒中,加入粗集料、細(xì)集料和水泥,形成混合物;干拌混合物,使得各組分混合均勻;s20:向混合物中加入水、減水劑和消泡劑,然后攪拌,形成混凝土拌合物;s30:向步驟s20制備的混凝土拌合物中加入纖維,攪拌均勻,得到纖維混凝土拌合物;s40:將步驟s30制備的纖維混凝土拌合物和促凝早強劑加入離心機的管模中,運行離心機,使纖維混凝土拌合物沿管模內(nèi)壁均勻分布,且內(nèi)部形成空腔;然后逐步提高轉(zhuǎn)速,增大離心力,在離心機中逐漸形成鋪裝結(jié)構(gòu)的粗集料層、粗細(xì)集料過渡層、細(xì)集料層和纖維層,制備出管狀的新拌鋪裝結(jié)構(gòu);s50:管狀的新拌鋪裝結(jié)構(gòu)初凝后,拆卸管模,將管狀的新拌鋪裝結(jié)構(gòu)取出并攤平,形成矩形狀;s60:矩形狀的新拌鋪裝結(jié)構(gòu)終凝后,將履帶從新拌鋪裝結(jié)構(gòu)上拆卸,對新拌鋪裝結(jié)構(gòu)養(yǎng)護,從而制成鋪裝結(jié)構(gòu)預(yù)制塊。作為優(yōu)選例,所述的步驟s10中,攪拌筒的轉(zhuǎn)速為60~100r/min,干拌時間為2~3min。作為優(yōu)選例,所述的步驟s20中,攪拌筒的轉(zhuǎn)速為60~100r/min,攪拌時間8~10min。作為優(yōu)選例,所述的步驟s30中,攪拌筒的轉(zhuǎn)速為150~240r/min,攪拌時間為16~20min;所述的纖維的密度為1.2~1.6g/cm3,拉伸強度大于1000mpa。作為優(yōu)選例,所述的步驟s40中,在管模內(nèi)壁固定一層履帶,并在履帶的表面涂刷隔離劑;履帶內(nèi)表面設(shè)有平行于履帶寬度方向的凸起條紋,相鄰條紋間距不相等。作為優(yōu)選例,所述的步驟s40中,離心機的起始轉(zhuǎn)速為45~60r/min,運行時間為3~5min,使纖維混凝土拌合物沿管模內(nèi)壁均勻分布,且內(nèi)部形成空腔。作為優(yōu)選例,所述的步驟s40中,逐步提高轉(zhuǎn)速是指:先逐漸提升轉(zhuǎn)速至130~140r/min,并維持5~7min,在最外側(cè)形成粗集料層;然后逐漸提升轉(zhuǎn)速至160~180r/min,并維持8~10min,在粗集料層內(nèi)側(cè)逐漸形成粗細(xì)集料過渡層和細(xì)集料層;最后逐漸提升轉(zhuǎn)速至200~215r/min,并維持6~9min,在細(xì)集料層內(nèi)側(cè)形成纖維層。作為優(yōu)選例,所述的步驟s50中,初凝時間為80~90min;所述的步驟s60中,終凝時間為270~285min,所述的養(yǎng)護是對鋪裝結(jié)構(gòu)覆蓋塑料薄膜進行養(yǎng)護,養(yǎng)護時間為28天。有益效果:與現(xiàn)有技術(shù)相比,本發(fā)明實施例具有以下有益效果:第一、本發(fā)明采用離心法制備性能梯度分布的鋪裝結(jié)構(gòu),能充分實現(xiàn)材料的組成成分沿著厚度方向由一側(cè)到另一側(cè)呈梯度逐漸變化,從而實現(xiàn)該材料的力學(xué)性能沿著厚度方向漸變,主要表現(xiàn)為:在厚度方向上,抗壓強度從鋪裝結(jié)構(gòu)底面到表面逐漸增大,而抗拉強度相反,從表面到底面逐漸增大。第二、與上下表面力學(xué)性能一致的素混凝土板相比,本實施例的鋪裝結(jié)構(gòu)的力學(xué)性能沿著厚度方向漸變,更加符合混凝土路面(道面)面層在實際輪載作用下所受應(yīng)力漸變的狀況,即表面受最大水平壓應(yīng)力,底面受最大水平拉應(yīng)力,中間應(yīng)力連續(xù)過渡。鋪裝結(jié)構(gòu)的力學(xué)性能梯度分布符合層位設(shè)計要求。第三、本實施例的鋪裝結(jié)構(gòu)表面的粗集料層因為富集抗壓性能優(yōu)越的粗集料,所以具有優(yōu)良的抗壓性能和耐磨性能;中間的粗細(xì)集料過渡層及細(xì)集料層的級配密實,能使荷載作用下產(chǎn)生的應(yīng)力良好過渡;下部區(qū)域的纖維層,由于富集了大量高強纖維,所以大大提高了鋪裝結(jié)構(gòu)的抗彎拉強度和極限拉伸應(yīng)變,能有效抵抗路面(道面)底部拉應(yīng)力、應(yīng)變,抵抗疲勞開裂破壞,同時纖維的梯度分布大大節(jié)約了纖維的用量,顯著降低了成本。第四、本實施例的鋪裝結(jié)構(gòu)的纖維層中添加的高強纖維,使混合料具備良好的拉伸變形能力,并且添加促凝早強劑控制其凝結(jié)時間,利用水泥混凝土初凝時間前的良好的塑性變形能力,通過履帶將管狀的試件取出并攤平成矩形混凝土預(yù)制板。第五、本實施例的鋪裝結(jié)構(gòu)在成型時即具有優(yōu)良的抗滑構(gòu)造,滿足道路路面(機場道面)使用的抗滑要求。由于用于取出試件的履帶內(nèi)表面設(shè)有不等間距的凸起紋理,使得到的鋪裝結(jié)構(gòu)表面在脫模成型時即具備合理的宏觀抗滑紋理,從而賦予混凝土板表面優(yōu)越的抗滑性能、散光防眩性能及排水性能,相比于普通混凝土表面抗滑紋理的二次加工方法(拉毛、刻槽等),本方法方便快捷、節(jié)省人力物力;第六,本方明制備的鋪裝結(jié)構(gòu)為預(yù)制塊,可在在室內(nèi)批量成型,質(zhì)量可控,運輸至施工現(xiàn)場后可快速鋪筑,施工快捷。附圖說明圖1是本發(fā)明實施例中鋪裝結(jié)構(gòu)攤平后的剖面圖;圖2是本發(fā)明實施例中制備方法的流程圖;圖3是本發(fā)明實施例中管模片和隔離塊的裝配圖;圖4是本發(fā)明實施例中管模的結(jié)構(gòu)圖;圖5是本發(fā)明實施例中,試件在管模中成型的結(jié)構(gòu)圖;圖6是本發(fā)明實施例中,試件從管模中取出的結(jié)構(gòu)圖;圖7是本發(fā)明實施例中,試件的抗拉強度隨深度變化的趨勢圖;圖8是本發(fā)明實施例中,試件的抗壓強度隨深度變化的趨勢圖。圖中有:粗集料層1、粗細(xì)集料過渡層2、細(xì)集料層3、纖維層4、管模片5、隔離塊6、履帶7、試件8、第一管模片501、第二管模片502、第三管模片503、鉸接螺栓504和鉸接螺栓505。具體實施方式下面結(jié)合附圖,對本發(fā)明的技術(shù)方案進行詳細(xì)的說明。如圖1所示,本發(fā)明的一個實施例提供一種道路路面或機場道面鋪裝結(jié)構(gòu),包括以下組分:粗集料、細(xì)集料、水泥、水、纖維、減水劑、促凝早強劑和消泡劑,組成比例為:按重量計,粗集料60~65份,細(xì)集料39~43份,水泥25~28份,水11~13份,減水劑0.5~0.6份,促凝早強劑0.012~0.016份,消泡劑0.05~0.06份,纖維體積占鋪裝結(jié)構(gòu)總體積的0.60%~0.85%。該鋪裝結(jié)構(gòu)包括從頂面到底面依次設(shè)置的粗集料層1、粗細(xì)集料過渡層2、細(xì)集料層3和纖維層4,其中,粗集料層1包括粗集料、細(xì)集料、纖維、水泥和水;在粗集料層1中,粗集料的體積含量介于52%~60%,細(xì)集料的體積含量介于10%~13%;粗細(xì)集料過渡層2包括粗集料、細(xì)集料、纖維、水泥和水;在粗細(xì)集料過渡層2中,粗集料的體積含量介于39%~45%,細(xì)集料的體積含量介于25%~30%;細(xì)集料層3包括細(xì)集料、纖維、水泥和水;在細(xì)集料層3中,細(xì)集料的體積含量介于50%~55%,纖維在在細(xì)集料層3的體積含量占纖維總體積含量的17%~22%;纖維層4包括纖維、細(xì)集料、水泥和水;在纖維層4中,細(xì)集料的體積含量介于36%~40%,纖維在纖維層4的體積含量占纖維總體積含量的50%~55%;粗集料和細(xì)集料組成的集料的平均粒徑沿著厚度方向從粗集料層1頂面到纖維層4底面呈梯度逐漸減??;從粗集料層1的頂面到粗細(xì)集料過渡層2的底面,粗集料的體積含量呈梯度逐漸減?。粡拇旨蠈?的頂面到細(xì)集料層3的底面,細(xì)集料的體積含量呈梯度逐漸增大;從粗集料層1的頂面到纖維層4的底面,纖維的體積含量呈梯度逐漸增大。荷載作用下混凝土板內(nèi)水平應(yīng)力狀況可以簡述為:上部區(qū)域受高壓應(yīng)力、中部區(qū)域為應(yīng)力過渡區(qū)域、下部區(qū)域受高拉應(yīng)力,從上至下為最大水平壓應(yīng)力到最大水平拉應(yīng)力逐漸過渡,尤其是在板底部位對混凝土的抗拉性能要求最高。然而普通的混凝土由于施工時為均勻拌和,可以視為均質(zhì)的材料,其各個位置的力學(xué)性能基本一致,水泥混凝土面板力學(xué)性能沿著板厚方向是無變化的,這并不符合水泥混凝土板內(nèi)部實際應(yīng)力分布的特點,尤其是抗拉強度沿厚度方向一致,在實際荷載作用下板底處產(chǎn)生的最大拉應(yīng)力易超過抗拉強度而導(dǎo)致混凝土板裂縫而破壞。本發(fā)明實施例的鋪裝結(jié)構(gòu),其在厚度方向上力學(xué)性能表現(xiàn)為:上部抗壓性能優(yōu)越,下部抗拉性能優(yōu)越,并且抗壓強度從底面到頂面逐漸增大,抗拉強度從頂面到底面逐漸增大,以適應(yīng)水泥混凝土板水平應(yīng)力沿板厚方向的漸變分布的規(guī)律,位于上部的粗集料層因為富集抗壓性能優(yōu)越的粗集料,所以具有優(yōu)良的抗壓性能;位于中部的粗細(xì)集料過渡層和細(xì)集料層的級配密實,能實現(xiàn)荷載作用產(chǎn)生的應(yīng)力良好過渡;位于下部的纖維層,由于富集了大量高強纖維,所以大大提高了混凝土板的抗彎拉強度和板底部位的極限拉伸應(yīng)變,能有效抵抗混凝土面板下的拉應(yīng)力、應(yīng)變,抵抗疲勞開裂破壞。如圖2所示,本發(fā)明的另一實施例提供上述道路路面或機場道面鋪裝結(jié)構(gòu)的制備方法,該制備方法包括以下步驟:s10:在混凝土攪拌筒中,加入粗集料、細(xì)集料和水泥,形成混合物;干拌混合物,使得各組分混合均勻。所述的粗集料和細(xì)集料的級配進行了設(shè)計和控制,粗集料采用的級配范圍是:方篩孔尺寸(mm)31.5、26.5、19、16、9.5、4.75和2.36,對應(yīng)的累計篩余量(%)分別為2~3、25~30、45~55、60~70、80~85、93~97和97~98;細(xì)集料采用的級配范圍是:方篩孔尺寸(mm)4.75、2.36、1.18、0.6、0.3和0.15,對應(yīng)的累計篩余量(%)分別為2~5、15~21、42~48、62~67、79~83和94~97。干拌時攪拌筒的轉(zhuǎn)速為60~100r/min,干拌時間為2~3min。s20:向混合物中加入水、減水劑和消泡劑,然后攪拌,形成混凝土拌合物。攪拌筒的轉(zhuǎn)速為60~100r/min,攪拌時間8~10min。s30:向步驟20制備的混凝土拌合物中加入纖維,攪拌均勻,得到纖維混凝土拌合物。攪拌筒的轉(zhuǎn)速為150~240r/min,攪拌時間為16~20min;所述的纖維的密度為1.2~1.6g/cm3,拉伸強度大于1000mpa。s40:將步驟30制備的纖維混凝土拌合物和促凝早強劑加入離心機的管模中,運行離心機,使纖維混凝土拌合物沿管模內(nèi)壁均勻分布,且內(nèi)部形成空腔;然后逐步提高轉(zhuǎn)速,增大離心力,在離心機中逐漸形成鋪裝結(jié)構(gòu)的粗集料層(1)、粗細(xì)集料過渡層(2)、細(xì)集料層(3)和纖維層(4),制備出管狀的新拌鋪裝結(jié)構(gòu)。加入拌合物前,在管模內(nèi)壁固定一層履帶,并在履帶的表面涂刷隔離劑;履帶內(nèi)表面設(shè)有平行于履帶寬度方向的凸起條紋,相鄰條紋間距不相等,用于形成良好的表面抗滑紋理。凸起條紋的截面為矩形,寬度為3~5mm,高度為4~6mm。由于橫向等間距刻槽路面易產(chǎn)生峰值噪聲,刺激人耳,所以履帶表面的凸起紋理按不等間距布置,提升抗滑性能的同時能有效降低噪音的產(chǎn)生。離心機的起始轉(zhuǎn)速為45~60r/min,運行時間為3~5min,使纖維混凝土拌合物沿管模內(nèi)壁均勻分布,且內(nèi)部形成空腔。在步驟s40中,提高轉(zhuǎn)速是指:先逐漸提升轉(zhuǎn)速至130~140r/min,并維持5~7min,在最外側(cè)形成粗集料層;然后逐漸提升轉(zhuǎn)速至160~180r/min,并維持8~10min,在粗集料層內(nèi)側(cè)逐漸形成粗細(xì)集料過渡層和細(xì)集料層;最后逐漸提升轉(zhuǎn)速至200~215r/min,并維持6~9min,在細(xì)集料層內(nèi)側(cè)形成纖維層,從而得到新拌鋪裝結(jié)構(gòu)。s50:管狀的新拌鋪裝結(jié)構(gòu)初凝后,拆卸管模,將管狀的新拌鋪裝結(jié)構(gòu)取出并攤平,形成矩形狀的新拌鋪裝結(jié)構(gòu)。初凝時間為80~90min;s60:矩形狀的新拌鋪裝結(jié)構(gòu)終凝后,終凝時間為270~285minmin,將履帶從新拌鋪裝結(jié)構(gòu)上拆卸,對新拌鋪裝結(jié)構(gòu)養(yǎng)護,從而制成鋪裝結(jié)構(gòu)預(yù)制塊。養(yǎng)護是對新拌鋪裝結(jié)構(gòu)覆蓋塑料薄膜進行養(yǎng)護,養(yǎng)護時間為28天。本發(fā)明實施例通過結(jié)構(gòu)、材料的設(shè)計和轉(zhuǎn)速的控制,使離心法可用于制備路面(道面)鋪裝結(jié)構(gòu)。另外,通過添加促凝早強劑對混凝土材料的硬化性能的控制和改良材料組分所帶來的變形性能的提高,使離心法制備的幾何形狀為管狀的新拌鋪裝結(jié)構(gòu)能夠攤鋪展平,制備出幾何形狀為矩形的鋪裝結(jié)構(gòu)預(yù)制塊。同時對混凝土離心裝置作特殊設(shè)計,即在內(nèi)壁附上特殊設(shè)計的履帶,既方便管狀鋪裝結(jié)構(gòu)從離心機中取出并攤鋪展平,又可通過對履帶表面作特殊的紋理設(shè)計賦予鋪裝結(jié)構(gòu)表面優(yōu)越的抗滑性能。為了提高離心機內(nèi)管狀新拌鋪裝結(jié)構(gòu)的拉伸變形能力以及制備出的鋪裝結(jié)構(gòu)預(yù)制塊的抗彎拉強度,通過改良它的材料組分——添加纖維賦予其高延性。由于纖維具有的超高韌性,能夠很好地解決傳統(tǒng)混凝土材料易脆性、弱拉伸性、裂縫寬度無法控制等種種缺陷。加入適量高強纖維離心制備管狀鋪裝結(jié)構(gòu)時利用離心力的作用,可以使纖維呈梯度分布,在管狀混凝土內(nèi)側(cè)區(qū)域富集,在最內(nèi)側(cè)形成一個纖維含量達到總纖維含量50%以上的纖維層,纖維層具有較高的抗拉強度、優(yōu)越的拉伸變形能力和控制裂縫開展的能力,大幅改善了鋪裝結(jié)構(gòu)預(yù)制塊的抵抗底部拉應(yīng)力和拉應(yīng)變的能力,從而抵抗開裂破壞,大幅提高路面(道面)面層的使用壽命,同時纖維集中分布底部區(qū)域大大節(jié)約了纖維的用量,顯著降低了造價。本發(fā)明制備的鋪裝結(jié)構(gòu)預(yù)制塊在成型時即表面具有優(yōu)越的抗滑性能、散光防眩性能、耐磨性能及排水性能,而無需二次加工處理,直接制備、方便快捷。水泥混凝土面板具有抗滑的要求,傳統(tǒng)的素混凝土面板進行抗滑構(gòu)造處理時一般采用拉毛法、壓槽法、刻槽法、露石法等方法,存在需要二次加工、消耗人力成本、施工質(zhì)量要求高的缺點。其中壓槽和拉槽都是在新澆混凝土表面上通過一定的附加外力完成的,所制作的溝槽存在明顯的不均勻現(xiàn)象。同時,由于拉壓槽時對表面砂漿的推擠作用,紋理深度不均勻,還易出現(xiàn)局部翻砂現(xiàn)象,影響混凝土表面平整度;而刻槽法和露石法需要專用設(shè)備和材料,所需成本高。本發(fā)明實施例在履帶內(nèi)表面設(shè)有平行于履帶寬度方向的凸起條紋,凸起條紋的截面為矩形,寬度為3~5mm,高度為4~6mm,使鋪裝結(jié)構(gòu)在成型時即具備良好的表面抗滑紋理而無需二次加工。同時,由于橫向等間距刻槽路面易產(chǎn)生峰值噪聲,刺激人耳,所以履帶表面的凸起紋理按不等間距布置,如間距依次為:19、25、23、25、19、22、25、22、17、25、26、32、28、22、25、20、25,單位:mm,提升抗滑性能的同時能有效降低噪音的產(chǎn)生。本實施例的制備方法利用離心力作用使拌合物密實,并使材料組成成分沿厚度方向梯度逐漸變化,從而使其力學(xué)性能也沿厚度方向梯度逐漸變化,并且內(nèi)部沒有明顯的界面,各個功能梯度層位的力學(xué)性能契合實際情況下路面(道面)面層所受應(yīng)力漸變的情況?;炷涟韬衔镏兴?、粗集料、細(xì)集料、纖維等各種組分在離心機中在作圓周運動時所產(chǎn)生的離心力,是和材料的質(zhì)量、角速度的二次方、旋轉(zhuǎn)半徑成正比的,計算式為:f=mω2r=ρvω2r式中:f表示材料受到的離心力;m表示材料的質(zhì)量;ω表示材料作圓周運動的角速度;r表示材料的旋轉(zhuǎn)半徑;ρ表示材料密度;v表示材料體積。由于拌合物中水泥、粗集料、細(xì)集料、纖維等多種材料的體積、密度不同,即使旋轉(zhuǎn)速度和旋轉(zhuǎn)半徑相同,各自的離心力也相差很大。在流動度較大的混凝土拌合物中,根據(jù)膠漿理論,可以分為三級,粗分散系:以粗集料為分散相,懸浮在纖維砂漿介質(zhì)中,細(xì)分散系:以細(xì)集料為分散相,懸浮在纖維水泥漿介質(zhì)中,微分散系:以纖維為分散相,懸浮在水泥漿介質(zhì)中,而水泥顆粒是懸浮在水內(nèi)。離心機鋼??焖傩D(zhuǎn)時,水泥膠漿混合物中的各種成分由于體積和密度不同,所受離心力的相差懸殊,在旋轉(zhuǎn)過程中相互之間就會發(fā)生相對位移,總體表現(xiàn)為:粒徑和密度越大的成分所受離心力越大,傾向于向外移動,而粒徑和密度越小的成分所受離心力越小,則傾向于相對向內(nèi)移動。離心過程中各種成分之間的嵌擠和摩阻作用以及細(xì)料對空隙的填充作用,最終與離心作用力達到平衡后,則得到平均粒徑由外而內(nèi)逐漸減小的密實型鋪裝結(jié)構(gòu)。具體梯度形成的原理為:形成空腔后初步提高轉(zhuǎn)速,粗集料顆粒由于體積最大,所受的離心力最大,因此開始逐步外移,移向管模模壁,與少部分細(xì)集料、水泥和纖維達到穩(wěn)定后組成緊密的骨架密實結(jié)構(gòu),從而在離心機最外側(cè)形成一個成分以粗集料為主的粗集料層;接著提高離心機的轉(zhuǎn)速即增大離心力,粗集料層(粗集料為主,含少量細(xì)集料)由于骨架嵌擠、內(nèi)摩阻力較大,其組分相對穩(wěn)定,而其余的細(xì)集料則進一步發(fā)生相對位移,在粗集料層內(nèi)側(cè)與剩余的粗集料混合形成粗細(xì)集料過渡層,并逐漸密實穩(wěn)定;隨著離心時間的延長,又有部分細(xì)集料在離心作用下與水泥纖維混合密實,逐漸達到穩(wěn)定,在粗細(xì)集料過渡層內(nèi)側(cè)形成一層成分以細(xì)集料為主的細(xì)集料層;纖維的密度最低,且較水略大,所受離心作用要小于集料,所以在整個離心過程中會逐步相對向內(nèi)側(cè)移動,最終在內(nèi)側(cè)聚集大量的纖維,增大離心力后與剩余的細(xì)集料和水泥達到密實穩(wěn)定,在最內(nèi)側(cè)形成纖維含量較高的纖維層。最終得到集料的平均粒徑和體積含量沿厚度方向逐漸過渡,且表面抗滑、耐磨和抗壓性能優(yōu)良及底層抗拉性能優(yōu)越的鋪裝結(jié)構(gòu)預(yù)制塊。在離心機中旋轉(zhuǎn)成型時,轉(zhuǎn)速控制及其作用如下:(1)起始轉(zhuǎn)速為45~60r/min,時間為3~5min,使拌合物沿模板內(nèi)壁均勻分布,內(nèi)部形成空腔;(2)接著逐漸將轉(zhuǎn)速提升至130~140r/min,并維持5~7min,使粗分散系中的分散相——粗集料從水泥漿介質(zhì)中逐漸分離外移,組成緊密的粗集料骨架,粗集料的體積含量介于52%~60%,同時細(xì)集料、水泥和纖維填充粗集料的骨架空隙,形成骨架密實結(jié)構(gòu),在最外側(cè)形成主要成分為粗集料的粗集料層。同時在離心過程中部分細(xì)料(細(xì)集料、水泥和纖維)向內(nèi)側(cè)移動;(3)然后逐漸將轉(zhuǎn)速提升至160~180r/min,并維持8~10min,離心力的增大使剩余的粗集料繼續(xù)向外側(cè)移動,在粗集料層內(nèi)側(cè)聚集,與部分細(xì)集料混合形成粗細(xì)集料過渡層,其中粗集料的體積含量介于39%~45%,細(xì)集料的體積含量介于25%~30%;旋轉(zhuǎn)過程中細(xì)分散系中的分散相——細(xì)集料從水泥漿介質(zhì)中進一步分離相對內(nèi)移,隨著離心時間的延長,細(xì)集料在粗細(xì)集料過渡層內(nèi)側(cè)聚集并與水泥和纖維混合達到密實穩(wěn)定,形成以細(xì)集料為主要成分的細(xì)集料層,其中細(xì)集料的體積含量介于50%~55%。粗細(xì)集料過渡層和細(xì)集料層為懸浮密實結(jié)構(gòu),同時纖維的體積含量逐漸增大,能實現(xiàn)壓應(yīng)力和拉應(yīng)力的良好過渡。同時在離心過程中部分水泥和纖維繼續(xù)相對向內(nèi)側(cè)移動;(4)最后逐漸將轉(zhuǎn)速在提升至200~215r/min,并維持6~9min,使微分散系中的分散相——纖維從水泥漿介質(zhì)中進一步分離相對內(nèi)移,并與剩余的細(xì)集料和水泥混合逐漸達到密實穩(wěn)定,形成纖維含量較高的纖維層,并成型密實的梯度分布水泥混凝土鋪裝結(jié)構(gòu)。纖維層中纖維的含量占總纖維含量的50%~55%,占本層的體積含量達到3%左右,較高的纖維含量賦予了鋪裝結(jié)構(gòu)底層良好的抗拉性能和耐疲勞性能,有效抵抗疲勞開裂破壞。如圖3至圖5所示,上述制備方法中采用的管模,包括至少3個管模片5、隔離塊6和履帶7,相鄰管模片5之間活動連接,且隔離塊6位于兩個管模片5之間,隔離塊6分別與相鄰的管模片5固定連接,管模片5和隔離塊6形成一環(huán)形體;履帶7固定連接在管模片5的內(nèi)壁上,離心機中隔離塊6內(nèi)表面與履帶7內(nèi)表面之間的距離大于管狀的新拌鋪裝結(jié)構(gòu)的厚度。以3個管模片5的離心機為例,管模片包括第一管模片501、第二管模片502和第三管模片503,其安裝過程如下:(1)首先將管模片之間的鉸接螺栓504和鉸接螺栓505旋松,將第一管模片501和第三管模片503展開,然后通過螺栓將履帶7固定在第二管模片502上;(2)接著將第一管模片501和第三管模片503合攏,并繼續(xù)將履帶7固定在第一管模片501和第三管模片503上,使履帶與管模壁緊密貼合,從而得到帶有缺口的圓環(huán)形管模;(3)將隔離塊6組裝到管模的缺口上,組裝分為兩步:第一步是將履帶7的兩個端部裝入隔離塊6兩側(cè)的預(yù)留槽將其固定;第二步是將隔離塊6與管模片之間的固定螺栓旋緊,以固定隔離塊6,從而得到用于成型試件8的管模。使用管模時,從離心機管模兩側(cè)加入混凝土拌合物原料,最后用封蓋封閉管模兩端,即可開始離心旋轉(zhuǎn),成型試件8。當(dāng)試件8成型后,從離心機上取出管模,首先拆卸固定履帶7的螺栓,然后將三個管模片之間的鉸接螺栓旋松,并拆卸連接隔離塊6與管模片的螺栓,解除隔離塊對履帶兩個端部的鎖定,移除隔離塊,將履帶的兩個端部夾住,然后將第一管模片501和第三管模片503同時逐漸向兩側(cè)展開,展開的同時將履帶7展開、提起并攤平,將試件8展平后,終凝后拆除履帶,在標(biāo)準(zhǔn)條件(溫度為20±2℃,相對濕度為95%)下養(yǎng)護28天。下面例舉一實例。一種路面或道面鋪裝結(jié)構(gòu),采用的原材料包括:玄武巖碎石(即粗集料,其級配范圍見表1)、石英砂(即細(xì)集料,其級配范圍見表2)、硅酸鹽水泥(42.5r)、pva纖維(長度20mm,直徑50μm,密度1.3g/cm3,拉伸強度1200mpa)、水、聚羧酸高效減水劑、促凝早強劑及消泡劑。表1粗集料級配范圍方篩孔尺寸(mm)31.526.519169.54.752.36累計篩余量(%)2.527.5506582.59597.5表2細(xì)集料級配范圍方篩孔尺寸(mm)4.752.361.180.60.30.15累計篩余量(%)31845658195各組分的質(zhì)量比為:粗集料∶細(xì)集料∶硅酸鹽水泥∶水∶聚羧酸高效減水劑∶促凝早強劑∶消泡劑=3∶1.5∶1∶0.6∶0.01∶0.0008∶0.002;纖維體積占混合料總體積的0.75%。制備路面和道面鋪裝結(jié)構(gòu)的步驟如下:步驟10:在混凝土攪拌筒中,加入粗集料、細(xì)集料和水泥,形成混合物;以90r/min的速率攪拌3分鐘,使得各組分混合均勻。步驟20:向混合物中加入水、減水劑和消泡劑,然后以90r/min攪拌8分鐘,形成混凝土拌合物。步驟30:向步驟20制備的漿體中加入pva纖維,以180r/min攪拌16分鐘,形成纖維混凝土拌合物。步驟40:將步驟30制備的纖維混凝土拌合物和促凝早強劑加入離心機的管模中,以起始轉(zhuǎn)速為50r/min運行離心機,運行時間為3~5min,使纖維混凝土拌合物沿管模內(nèi)壁均勻分布,且內(nèi)部形成空腔;然后逐漸將轉(zhuǎn)速提升至140r/min,并維持6min,然后逐漸將轉(zhuǎn)速提升至170r/min,并維持9min;最后逐漸將轉(zhuǎn)速提升至210r/min,并維持8min,制備出管狀的新拌鋪裝結(jié)構(gòu)。步驟50:管狀的新拌鋪裝結(jié)構(gòu)初凝后,拆卸管模,將管狀的新拌鋪裝結(jié)構(gòu)取出并攤平,形成矩形狀的新拌鋪裝結(jié)構(gòu);步驟60:管狀的新拌鋪裝結(jié)構(gòu)終凝后,將履帶從新拌鋪裝結(jié)構(gòu)上拆卸,對新拌鋪裝結(jié)構(gòu)養(yǎng)護,從而制成鋪裝結(jié)構(gòu)預(yù)制塊。對比例1:采用上述實例1的材料,按同樣的配比,但不含pva纖維,以現(xiàn)有的普通攪拌方法即均勻拌合方法,澆筑一塊等厚度的混凝土板。對比例2采用上述實例1的材料,按同樣的配比,含pva纖維,以現(xiàn)有的普通攪拌方法即均勻拌合方法,澆筑一塊等厚度的混凝土板。將實例1、對比例1和對比例2得到的樣品放置于同一養(yǎng)護室,在溫度為20±2℃,相對濕度為95%的條件下,養(yǎng)護28天。下面對實例1、對比例1和對比例2制備的三塊樣品進行抗壓強度和抗彎拉強度試驗。養(yǎng)護結(jié)束后,將三塊樣品切割成小梁試件(每塊3個,共9個)、立方體試件(每塊3個,共9個),分別進行四點彎曲試驗、抗壓強度試驗,取平均值進行計算和比較。試件要保留厚度方向上所有層位,試件實際尺寸見表3。試驗結(jié)果如表4所示。表3試件尺寸試件小梁試件立方體試件試件尺寸(mm)195×195×750195×195×195表4抗彎拉、立方體抗壓強度試驗結(jié)果抗彎拉強度比較:表4的試驗數(shù)據(jù)表明,實例1的抗彎拉強度比未摻纖維的普通混凝土(即對比例1)高40.0%,比摻纖維的混凝土(即對比例2)高14.8%。實例1的極限撓度比對比例2高14.3%,由于對比例1中沒有纖維的增強約束作用,所以撓度則比實例1和對比例2低得多。實驗結(jié)果說明:纖維在實例1中的抗彎拉性能起到了很好的增強效果,表現(xiàn)為抗彎拉強度和韌性(變形能力)相對于素混凝土(即對比例1)得到極大提升,同時相同纖維含量下,與均勻拌合的纖維混凝土(即對比例2)相比也有一定幅度的提升。這是因為實例1可使纖維梯度分布,使其在鋪裝結(jié)構(gòu)底部受拉部位分布率最高,從而提高了抗彎拉強度以及纖維的利用率,進而起到節(jié)約纖維用量的作用,具有良好的工程效益??箟簭姸缺容^:實例1的抗壓強度值較普通方法制備的混凝土有一定的增加,約比素混凝土(即對比例2)增加6%??梢?,雖然梯度分布從一定程度上降低了粗集料的嵌擠作用,但離心作用使鋪裝結(jié)構(gòu)變得更加密實,加上纖維的約束增強作用使鋪裝結(jié)構(gòu)的抗壓強度得到一定增強。雖然抗壓強度增強并不明顯,但其抗彎性能得到很大提高,而這正是我們實際使用中需要的材料性能。對實例1的試件進行抗滑能力測定,分別測定構(gòu)造深度和擺值。試驗結(jié)果如表5所示。表5抗滑試驗結(jié)果抗滑指標(biāo)指標(biāo)值構(gòu)造深度(mm)1.02擺值68抗滑試驗結(jié)果表明:采用本發(fā)明制備的實例1由于表面具備規(guī)則紋理,所以表面具有優(yōu)越的抗滑性能,構(gòu)造深度達到1.02,遠(yuǎn)高于抗滑技術(shù)指標(biāo)值0.55,擺值(摩擦系數(shù))達68,高于抗滑技術(shù)指標(biāo)值59。對上述實例的鋪裝結(jié)構(gòu)材料的抗拉強度隨深度變化進行測試。測試方法:將實例1的鋪裝結(jié)構(gòu)試件樣品在厚度方向上不同深度范圍內(nèi)切割為6個3cm×3cm×20cm小梁試件,截取的6個深度范圍分別為:0~3cm、4~7cm、7~10cm、10.5~13.5cm,13.5~16.5cm,16.5~19.5cm,每個深度范圍各取3個小梁試件,得到6組小梁試件。分別測量6組試件的抗拉強度并取平均值代表各組試件的抗拉強度,以這6個抗拉強度值近似表示樣品在深度1.5cm、5.5cm、8.5cm、12cm、15cm、18cm處的抗拉強度。并繪制抗拉強度隨深度變化的趨勢圖。結(jié)果如圖7所示。圖7中,橫坐標(biāo)表示抗拉強度,縱坐標(biāo)表示試件的深度,以試件的頂面為基準(zhǔn)面,即試件頂面的深度為零。從該圖可以看出上述實例的鋪裝混凝土板,其抗拉強度隨高度呈現(xiàn)出梯度變化的趨勢,即抗拉強度由頂面到底面逐漸增大,證明材料抗拉性能具備梯度分布的特性。在底部的抗拉強度最大,底部小梁試件抗拉強度達到2.68mpa,相比于普通混凝土抗拉強度(約為1.75mpa)要大53%左右,有效增強了材料在實際應(yīng)用時抵抗拉應(yīng)力和拉應(yīng)變的能力。對上述實例的鋪裝結(jié)構(gòu)材料的抗壓強度隨深度變化進行測試。測試方法:將實例1的鋪裝結(jié)構(gòu)試件樣品在厚度方向上不同深度范圍內(nèi)切割為5個4cm×4cm×4cm立方體抗壓強度試件,截取的5個深度范圍分別為:0~4cm、4~8cm、8~12cm、12~16cm,15.5~19.5cm每個深度范圍各取3個立方體試件,得到5組立方體試件。分別測量5組試件的抗壓強度并取平均值代表各組試件的抗壓強度,以這5個抗拉強度值近似表示樣品在深度2cm、6cm、10cm、14cm、17.5cm處的抗壓強度。并繪制抗壓強度隨深度變化的趨勢圖。結(jié)果如圖8所示。圖8中,橫坐標(biāo)表示抗壓強度,縱坐標(biāo)表示試件的深度,以試件的頂面為基準(zhǔn)面,即試件頂面的深度為零。從該圖可以看出:上述實例的鋪裝混凝土板的抗壓強度隨高度呈現(xiàn)出梯度變化的趨勢,即抗壓強度由試件的底面到頂面逐漸增大,證明材料抗壓性能具備梯度分布的特性。頂部的抗壓強度有一定增大,抗壓強度達到51.7mpa,相比于普通混凝土頂部的抗壓強度(約為45.84mpa)要大13%左右,在保證混凝土整體抗壓性能的前提下,局部增強了頂部區(qū)域的抗壓性能,更加適應(yīng)實際情況下道路路面和機場道面的受力特征。當(dāng)前第1頁12