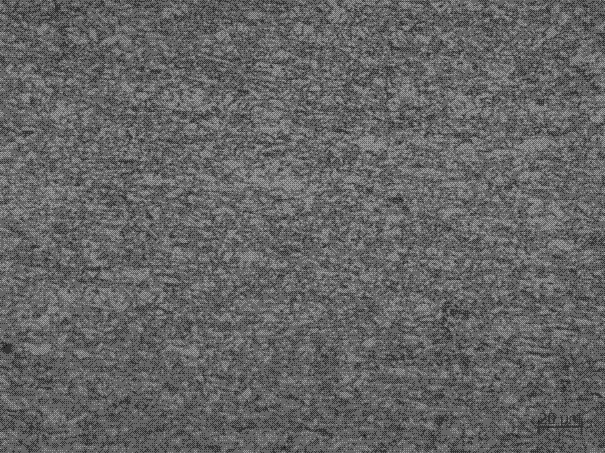
本發(fā)明涉及x100管線(xiàn)用鋼板及其制備方法,具體涉及一種高韌性的厚度在25mm以上的x100超高鋼級(jí)管線(xiàn)用鋼板及其制造方法。
背景技術(shù):
:目前世界需求的能源中化石能源還占能源結(jié)構(gòu)中的主體地位,近年來(lái)世界經(jīng)濟(jì)的急速增長(zhǎng)極大帶動(dòng)了化石能源需求的急速增長(zhǎng),這也極大地促進(jìn)了長(zhǎng)距離輸送管線(xiàn)的發(fā)展,為提高輸送效率,降低投資,長(zhǎng)距離石油天然氣輸送管線(xiàn)用鋼的發(fā)展趨勢(shì)是向高強(qiáng)度或超高鋼級(jí)發(fā)展。目前世界各國(guó)使用的管線(xiàn)鋼最高鋼級(jí)為x80鋼級(jí),為推動(dòng)管線(xiàn)鋼技術(shù)發(fā)展及從降低建設(shè)成本及提到運(yùn)營(yíng)效率考慮,上世紀(jì)后期,在加拿大等國(guó),相繼鋪設(shè)了x100鋼級(jí)管道試驗(yàn)段。降低運(yùn)營(yíng)成本,提高輸送效率的途徑主要包括擴(kuò)大管徑、提高鋼級(jí)和增加壁厚。x100管線(xiàn)鋼國(guó)內(nèi)專(zhuān)利授權(quán)或申請(qǐng)專(zhuān)利,但是涉及厚規(guī)格甚至超厚規(guī)格x100專(zhuān)利則很少。如專(zhuān)利號(hào)為cn102304667b提到的專(zhuān)利:1)該專(zhuān)利提到的最厚規(guī)格為22mm;2)該專(zhuān)利提到mn含量不高于1.80%,v含量為0.02-0.08%;3)該專(zhuān)利終冷溫度控制在90-190℃。故該專(zhuān)利涉及到的成分和工藝所獲得的x100因組織為下貝氏體,從而dwtt性能在厚規(guī)格中受到較差,據(jù)其公開(kāi)的數(shù)據(jù),最厚規(guī)格為22mm。如申請(qǐng)專(zhuān)利號(hào)為cn1033695807a提到的專(zhuān)利:1)該專(zhuān)利提到的最厚規(guī)格為20mm;2)該專(zhuān)利提到mn含量為1.80-2.1%;3)該專(zhuān)利終軋溫度在800-860℃,開(kāi)冷溫度為730-800℃,最終得到的韌性值為0℃沖擊功不高于250j。本專(zhuān)利是在申請(qǐng)專(zhuān)利號(hào)為cn201510153571.3所公開(kāi)技術(shù)方案的基礎(chǔ)上進(jìn)行的在鋼種方面的延伸,即將該技術(shù)思想延伸到x100鋼級(jí),同時(shí)在acc冷卻時(shí)通過(guò)分段梯度冷卻工藝,獲得厚規(guī)格優(yōu)異低溫韌性超高鋼級(jí)x100鋼板,厚度規(guī)格超過(guò)25mm。技術(shù)實(shí)現(xiàn)要素:石油天然氣等管道工程發(fā)展方向是高鋼級(jí)、大壁厚、低溫高韌性。同時(shí)還包括抗hic及抗sscc等性能要求,早在上世紀(jì)90年代,x100鋼級(jí)就已研發(fā)成功,但厚度一直難以突破19mm以及-15℃低溫落錘性能要求。本申請(qǐng)結(jié)合國(guó)外訂單要求,解決目前超高鋼級(jí)超厚規(guī)格,低溫落錘性能問(wèn)題,使得x100超高強(qiáng)度鋼級(jí)25.4mm及以上超厚管線(xiàn)鋼板,具有優(yōu)異低溫落錘性能,解決目前超高強(qiáng)度鋼級(jí)超厚規(guī)格鋼板的低溫韌性問(wèn)題。本發(fā)明所要解決的技術(shù)問(wèn)題是針對(duì)上述現(xiàn)有技術(shù)提供生產(chǎn)厚度超過(guò)25mm厚x100管線(xiàn)鋼板及其制造方法,為獲得超厚規(guī)格優(yōu)異低溫韌性及dwtt落錘性能,成分涉及該工藝相對(duì)比較簡(jiǎn)練,成材率較高。實(shí)際上,超高強(qiáng)度鋼級(jí)厚規(guī)格管線(xiàn)鋼的低溫韌性及落錘性能是世界公認(rèn)的難題,國(guó)內(nèi)外的研究表明,落錘性能除了鋼中的組織及環(huán)境溫度等因素以外,還與鋼板的厚度有密切的關(guān)系,且隨厚度增加,對(duì)厚度越敏感,這稱(chēng)之為厚度效應(yīng)!為解決超厚規(guī)格下的厚度效應(yīng),需要從組織上進(jìn)行設(shè)計(jì),即控制組織類(lèi)型和細(xì)化晶粒上進(jìn)行控制,同時(shí)還要考慮到其他影響落錘影響因素如應(yīng)力等。本發(fā)明解決上述問(wèn)題所采用的技術(shù)方案為:一種超厚規(guī)格高韌性x100超高鋼級(jí)管線(xiàn)鋼板,該鋼板的化學(xué)成分按質(zhì)量百分比計(jì)為c:≤0.08%、mn:1.9~2.5%,si:≤0.35%,s:≤0.0006%,p:≤0.010%,nb:0.035~0.08%、ti:≤0.012%、v:≤0.008%,alt:≤0.06%,n:≤0.0040%,o:≤0.004%,mo:≤0.40%,pb≤0.0015%,zn≤0.003%,sb≤0.0015%,sn≤0.0015%,cu:≤0.30%、ni:0.20~1.5%,cr:≤0.35%,mo+cu+ni+cr≤2.5%,ca:≤0.01%,余量為fe及不可避免的雜質(zhì)元素;所述鋼板的厚度為25mm及以上。本申請(qǐng)鋼板的最厚達(dá)到28mm,鋼板的屈服強(qiáng)度≥690mpa;抗拉強(qiáng)度≥760mpa,屈強(qiáng)比≤0.86,圓棒樣延伸率≥25%,-25℃沖擊功≥300j,-40℃沖擊功≥200j,-60℃沖擊功≥150j,-15℃落錘剪切面積≥85%,-20℃落錘剪切面積≥70%,全壁厚試樣落錘性能,若是減薄試樣落錘性能更高。鋼板的金相組織為少量細(xì)鐵素體+貝氏體組織。本發(fā)明具有性能優(yōu)異的厚規(guī)格x100管線(xiàn)用鋼板,成分設(shè)計(jì)原理是采用適量的c、mn,通過(guò)加入微量nb、v、ti等微合金化元素,同時(shí)加入少量mo、cu、ni等元素,結(jié)合特定tmcp(中間坯冷卻+acc分段梯度冷卻工藝)工藝,以便最終保證厚規(guī)格x100具有低溫高韌性,尤其是優(yōu)異的dwtt落錘性能,其主要的基本元素作用如下:c:c是鋼中最經(jīng)濟(jì)、最基本的強(qiáng)化元素,通過(guò)固溶強(qiáng)化和析出強(qiáng)化可明顯提高鋼的強(qiáng)度,但對(duì)鋼的韌性及延性以及焊接性能帶來(lái)不利影響,因此管線(xiàn)鋼的發(fā)展趨勢(shì)是不斷降低c含量,考慮到強(qiáng)度及韌性的匹配關(guān)系,將c含量控制在0.03~0.07%。:通過(guò)固溶強(qiáng)化提高鋼的強(qiáng)度,是管線(xiàn)鋼中彌補(bǔ)因c含量降低而引起強(qiáng)度損失的最主要的元素,mn同時(shí)還是擴(kuò)大γ相區(qū)的元素,可降低鋼的γ→α相變溫度,有助于獲得細(xì)小的相變產(chǎn)物,可提高鋼的韌性,降低韌脆性轉(zhuǎn)變溫度,mn也是提高鋼的淬透性元素??紤]到檢驗(yàn)過(guò)程中發(fā)現(xiàn)mn偏析對(duì)落錘性能產(chǎn)生不利影響,同時(shí)兼顧到強(qiáng)度要求,本發(fā)明中mn含量設(shè)計(jì)在1.90~2.5%范圍,為緩解因mn較高所帶來(lái)的中心偏析,連鑄時(shí)采用輕壓下。:是現(xiàn)代微合金化鋼特別是管線(xiàn)鋼中最主要的微合金化元素之一,對(duì)晶粒細(xì)化的作用非常明顯。通過(guò)nb的固溶拖曳及熱軋過(guò)程中的nb(c,n)應(yīng)變誘導(dǎo)析出可阻礙形變奧氏體的回復(fù)、再結(jié)晶,經(jīng)tmcp使未再結(jié)晶區(qū)軋制的形變奧氏體在相變時(shí)轉(zhuǎn)變?yōu)榧?xì)小相變產(chǎn)物,以使鋼具有高強(qiáng)度和高韌性,本發(fā)明主要是通過(guò)c與nb含量的關(guān)系來(lái)確定nb含量范圍,v:具有較高的析出強(qiáng)化和較弱的晶粒細(xì)化作用,在nb、v、ti三種微合金化元素中復(fù)合使用時(shí),v主要起析出強(qiáng)化作用。:是強(qiáng)的固n元素,ti/n的化學(xué)計(jì)量比為3.42,利用0.02%左右的ti就可固定鋼中60ppm以下的n,在板坯連鑄過(guò)程中即可形成tin析出相,這種細(xì)小的析出相可有效阻止板坯在加熱過(guò)程中奧氏體晶粒的長(zhǎng)大,有助于提高nb在奧氏體中的固溶度,同時(shí)可改善焊接熱影響區(qū)的沖擊韌性,是管線(xiàn)鋼中不可缺少的元素,但過(guò)高的ti會(huì)形成大的tin質(zhì)點(diǎn),影響落錘性能,因此本申請(qǐng)專(zhuān)利將ti控制在0.008-0.015%之間。:可推遲γ→α相變時(shí)先析出鐵素體相的形成,促進(jìn)針狀鐵素體形成的主要元素,對(duì)控制相變起到重要作用,同時(shí)也是提高鋼的淬透性元素。在一定的冷卻速度和終冷溫度下通過(guò)添加一定mo即可獲得明顯的針狀鐵素體或貝氏體組織。、p:是管線(xiàn)鋼中不可避免的雜質(zhì)元素,希望越低越好,通過(guò)超低硫及ca處理改變硫化物形態(tài)可使管線(xiàn)鋼具有很高的沖擊韌性。、ni:可通過(guò)固溶強(qiáng)化提高鋼的強(qiáng)度,ni的加入一方面可提高鋼的韌性,同時(shí)改善cu在鋼中易引起的熱脆性。:cr的加入可提高鋼的淬透性,且相對(duì)經(jīng)濟(jì)。pb,zn,sb,sn:這些殘余元素很容易在晶界聚集,弱化晶界間的結(jié)合力,從而影響落錘性能,因此需要控制pb≤0.0015%,zn≤0.003%,sb≤0.0015%,sn≤0.0015%。上述厚規(guī)格優(yōu)異低溫韌性x100管線(xiàn)鋼板的制備流程:配比備料→進(jìn)行轉(zhuǎn)爐或電爐冶煉→爐外精煉→連鑄→板坯再加熱→特定tmcp工藝(中間坯冷卻+acc分段梯度冷卻工藝)+冷卻后堆冷→矯直。具體工藝為首先將冶煉原料依次經(jīng)kr鐵水預(yù)處理、轉(zhuǎn)爐冶煉、lf精煉、rh真空精煉和連鑄,制造出滿(mǎn)足化學(xué)成分要求、厚度為不小于350mm的連鑄坯;將連鑄坯再加熱,溫度不高于1200℃,進(jìn)行特定tmcp工藝+水冷+堆冷+矯直。連鑄時(shí)采用輕壓下以便改善因mn較高造成的芯部偏析。特定tmcp工藝包括兩階段軋制和中間坯冷卻:第一階段為再結(jié)晶區(qū)軋制,終軋溫度控制在≤1150℃,再結(jié)晶區(qū)軋制時(shí)控制連續(xù)兩至三道次的單道次壓下率不低于20%,再結(jié)晶區(qū)軋制的總壓縮比為不低于70%;中間坯冷卻是通過(guò)mildcooling冷卻系統(tǒng)對(duì)中間坯快速冷卻至第二階段的非再結(jié)晶區(qū)開(kāi)軋溫度,冷卻方式是在mildcooling箱體內(nèi)采用來(lái)回?cái)[動(dòng)的方式進(jìn)行冷卻,冷速速度為8-14℃/s,保證再結(jié)晶區(qū)軋制變形后奧氏體晶粒不再長(zhǎng)大,中間坯表面與心部溫差較小。第二階段為非再結(jié)晶區(qū)軋制,開(kāi)軋溫度不高于900℃,終軋溫度控制在相變臨界溫度附近ac3+15℃范圍內(nèi)。軋后以水冷方式冷卻鋼板,冷卻工藝采用分段梯度冷卻工藝,開(kāi)始冷卻溫度控制為不高于770℃,終止冷卻溫度控制為400℃以下,冷卻速度為8~35℃/s;冷卻后矯直,最后直接冷卻到室溫即得鋼板成品。acc分段梯度冷卻工藝是將acc各冷卻單元冷卻水量設(shè)置:前1-5段的冷卻水量最大,對(duì)應(yīng)的冷卻速度為25-35℃/s,后6-16段acc冷卻單元冷卻水量依次遞減,對(duì)應(yīng)的冷卻速度變化是8-20℃/s。終軋溫度結(jié)束后,通過(guò)分段梯度冷卻工藝,結(jié)合cct曲線(xiàn),在前1-6acc冷卻段,將鋼板表面溫度冷卻到ac3線(xiàn)以下10℃范圍內(nèi),一方面可以通過(guò)快冷卻速度,使得鋼板獲得較大的過(guò)冷度,從而為獲得更多相變形核,最終在鋼板近表面會(huì)獲得更細(xì)小相變后晶粒,但同時(shí)由于鋼板較厚,而鋼板內(nèi)部主要是傳熱冷卻,鋼板表明和心部會(huì)存在溫差,從而心部和近表面組織存在差異。另一方面,為在同樣獲平均冷卻速度和終冷溫度縮短時(shí)間。一旦溫度達(dá)到ar3線(xiàn)附近后,采用較低冷卻速度,可以減緩因高碳當(dāng)量下,相變時(shí)產(chǎn)生相變應(yīng)力和溫度應(yīng)力敏感性。從而獲得鋼板組織近表面組織相對(duì)較小且鐵素體含量相對(duì)較多的組織,而其余部位雖大部分為貝氏體組織,但因殘余應(yīng)力相對(duì)較小,最終仍具有低溫高韌性。與現(xiàn)有技術(shù)相比,本發(fā)明的特點(diǎn)在于:1)采用特定的成分,生產(chǎn)25mm以上厚規(guī)格x100,并與后續(xù)特定tmcp工藝結(jié)合,獲得了優(yōu)異的低溫韌性。2)該發(fā)明改良的tmcp工藝(含采用mildcooling冷卻系統(tǒng)進(jìn)行中間坯冷卻+分段梯度冷卻),有助于降低產(chǎn)品的合金成本,提高成材率。在tmcp工藝過(guò)程通過(guò)mildcooling冷卻系統(tǒng)對(duì)中間坯快速冷卻,保證第一階段再結(jié)晶區(qū)變形后奧氏體晶粒不再長(zhǎng)大,提高超厚規(guī)格管線(xiàn)鋼板生產(chǎn)效率。3)通過(guò)采用ar3附近精軋后再快速冷卻工藝到ar3附近,一方面通過(guò)增加形變存儲(chǔ)能和增大過(guò)冷度,為相變提供更大動(dòng)力,從而可進(jìn)一步細(xì)化晶粒,為獲得優(yōu)異低溫韌性,特別是超高強(qiáng)度鋼級(jí)低溫落錘性能提供保證。附圖說(shuō)明圖1為本發(fā)明acc分段梯度冷卻與常規(guī)冷卻的對(duì)比圖;圖2為本發(fā)明鋼板近表面至近厚度1/4組織;圖3為本發(fā)明鋼板近厚度1/4處至心部組織。具體實(shí)施方式以下結(jié)合實(shí)施例對(duì)本發(fā)明作進(jìn)一步詳細(xì)描述。超低溫落錘性能優(yōu)異的厚規(guī)格x100管線(xiàn)鋼板的制造流程為:配比備料→進(jìn)行轉(zhuǎn)爐或電爐冶煉→爐外精煉→連鑄→板坯再加熱→特定tmcp工藝+冷卻后堆冷→矯直。具體工藝步驟如下:將冶煉原料依次經(jīng)kr鐵水預(yù)處理、轉(zhuǎn)爐冶煉、lf精煉、rh真空精煉和連鑄,連鑄時(shí)采用輕壓下工藝,目的在于改善因mn含量較高造成的芯部偏析。制造出滿(mǎn)足化學(xué)成分要求、厚度350mm的連鑄坯;將連鑄坯再加熱至1180~1200℃,進(jìn)行特定tmcp工藝+acc梯度冷卻工藝+堆冷+矯直。特定tmcp工藝包括兩階段軋制和中間坯冷卻:第一階段為再結(jié)晶區(qū)軋制,終軋溫度控制在不高于1150℃,再結(jié)晶區(qū)軋制時(shí)控制連續(xù)兩至三道次的單道次壓下率不低于20%;中間坯冷卻是通過(guò)mildcooling冷卻系統(tǒng)對(duì)中間坯快速冷卻至第二階段的非再結(jié)晶區(qū)開(kāi)軋溫度,冷卻方式為是在mildcooling箱體內(nèi)采用來(lái)回?cái)[動(dòng)式進(jìn)行冷卻,冷速速度為6-12℃/s,保證再結(jié)晶區(qū)軋制變形后奧氏體晶粒不再長(zhǎng)大,中間坯表面與心部溫差較小;第二階段為非再結(jié)晶區(qū)軋制,開(kāi)軋溫度不高于900℃,終軋溫度控制在相變臨界溫度ar3附近。軋后以水冷方式冷卻鋼板,開(kāi)始冷卻溫度控制為不高于770℃,終止冷卻溫度控制為不高于400℃,冷卻速度為8~35℃/s;水冷結(jié)束后矯直,最后直接冷卻到室溫即得鋼板成品。即acc各冷卻單元冷卻水量設(shè)置為不同:前1-5段的冷卻水量最大,對(duì)應(yīng)的冷卻速度為25-35℃/s,后6-16段acc冷卻單元冷卻水量依次遞減,對(duì)應(yīng)的冷卻速度變化是8-20℃/s。各實(shí)施例所涉及鋼板的具體化學(xué)成分見(jiàn)表1,具體tmcp工藝參數(shù)見(jiàn)表2,主要力學(xué)性能見(jiàn)表3。表1實(shí)施例cmnsispnbtivaltmo+cu+ni+crbca1≤0.08≤2.0≤0.350.00050.01≤0.08≤0.015≤0.007≤0.06≤1.8-≤0.012≤0.08≤2.0≤0.350.00050.01≤0.08≤0.015≤0.007≤0.06≤1.8-≤0.013≤0.08≤2.0≤0.350.00050.01≤0.08≤0.015≤0.007≤0.06≤1.8-≤0.01表2實(shí)施例再加熱溫度℃再結(jié)晶區(qū)軋制,終軋溫度℃再結(jié)晶區(qū)軋制累計(jì)變形率%開(kāi)始非再結(jié)晶區(qū)軋制溫度℃終止非再結(jié)晶區(qū)軋制溫度水冷冷速℃/s終冷溫度℃1≤1200≤1150≤55≤900臨界相變溫度10-35≤400堆冷+矯直2≤1200≤1150≤55≤900臨界相變溫度10-35≤400堆冷+矯直3≤1200≤1150≤55≤900臨界相變溫度10-35≤400堆冷+矯直表3除上述實(shí)施例外,本發(fā)明還包括有其他實(shí)施方式,凡采用等同變換或者等效替換方式形成的技術(shù)方案,均應(yīng)落入本發(fā)明權(quán)利要求的保護(hù)范圍之內(nèi)。當(dāng)前第1頁(yè)12