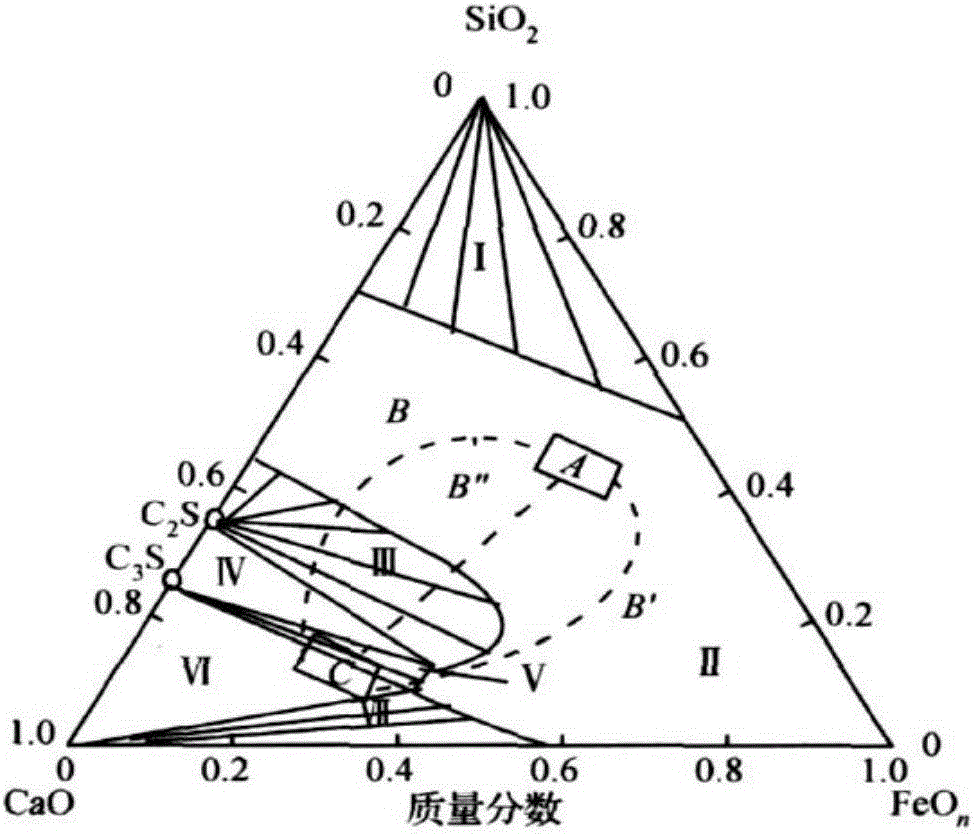
本發(fā)明屬于鋼冶煉
技術(shù)領(lǐng)域:
,涉及一種低成本鋼的冶煉工藝,尤其是涉及一種82B鋼的轉(zhuǎn)爐冶煉工藝。
背景技術(shù):
:水鋼生產(chǎn)預(yù)應(yīng)力鋼絞線用82B盤條。它是煉鋼廠冶煉出的鋼水澆鑄成方坯之后,在軋鋼廠加熱、軋制成φ10~13mm的盤條,然后在鋼絞線廠拉拔成φ5.05~5.10mm的鋼絲,最后捻制成鋼絞線。這種鋼絞線被稱為預(yù)應(yīng)力鋼絞線,它被廣范用于水壩、橋梁、立交橋、高層建筑等大型工程中。在水鋼成功開發(fā)生產(chǎn)82B盤條后,通過在冶煉工藝和軋制工藝過程中的精心操作和控制,生產(chǎn)出了鋼質(zhì)潔凈、性能優(yōu)良的82B盤條,但由于生產(chǎn)成本高、價格貴,影響了盤條的更大規(guī)模生產(chǎn)和銷售。將82B盤條鋼與普通建筑用盤條螺紋鋼進(jìn)行比較可知,前者比后者成本高的主要原因是前者的冶煉成本高,而軋制成本相差不大。為了實現(xiàn)水鋼82B盤條產(chǎn)業(yè)化,我們致力于在保證和提高鋼的質(zhì)量的前提下,通過對冶煉工藝的優(yōu)化,達(dá)到多快好省地生產(chǎn)優(yōu)質(zhì)82B鋼的目的。82B鋼冶煉成本高其中一個原因是轉(zhuǎn)爐采用雙渣冶煉導(dǎo)致鋼鐵料消耗高。吹煉進(jìn)入中、后期之后,脫磷的各種條件發(fā)生了變化,前期脫掉的磷又有可能返回到鋼水中,從而造成前功盡棄。因此在轉(zhuǎn)爐冶煉過程中,為了使鋼水的磷含量盡可能低,采用雙渣操作,即在冶煉初期,在鋼水初次脫磷后,把磷含量高的初期渣(約6噸)倒掉一半(約3噸),避免初期渣中的磷又回到鋼水中,然后再加入石灰等造渣材料造新渣,進(jìn)一步對鋼水脫磷,直到冶煉終點出鋼。在雙渣操作過程中,要倒掉初期渣約3噸,渣中全鐵(TFe)含量為18%~25%,平均為20%,每爐鋼倒初期渣消耗全鐵約600kg,這些鐵隨初期渣倒掉,被白白浪費掉,增加了鋼鐵料消耗,增加了成本。另外,沒有充分利用鐵水中的鉻元素,LF精煉結(jié)束喂硅鈣絲量太大,中間包使用壽命短,浪費了耐火材料,連鑄丟坯太多,浪費鋼坯等也是造成其生產(chǎn)成本居高不下的重要原因。這在《四川冶金》(2016年4月)第38卷第2期降低高碳鋼冶煉成本的生產(chǎn)實踐(李正嵩等)中已有說明。技術(shù)實現(xiàn)要素:為了解決上述問題,本發(fā)明提供了一種82B鋼的轉(zhuǎn)爐冶煉工藝,以低成本高效率地生產(chǎn)出優(yōu)質(zhì)82B鋼,從而達(dá)到降低82B鋼生產(chǎn)成本的效果。本發(fā)明是通過如下技術(shù)方案予以實現(xiàn)的。一種82B鋼的轉(zhuǎn)爐冶煉工藝,包括兌入高爐鐵水、轉(zhuǎn)爐底吹氬氣、過程加料、終點加料步驟:(1)兌入高爐鐵水:采用100噸頂?shù)讖?fù)吹轉(zhuǎn)爐,向轉(zhuǎn)爐中兌入高爐鐵水,高爐鐵水中含磷為0.104%~0.157%,在沒有測溫取樣的副槍條件下,利用上述的高磷鐵水,采用單渣操作,冶煉82B高碳鋼;(2)轉(zhuǎn)爐底吹氬氣:冶煉過程中,向轉(zhuǎn)爐底吹氬氣,從開始吹煉計算,前3分鐘,轉(zhuǎn)爐底吹氬氣總流量150m3/h,第3~7分鐘,轉(zhuǎn)爐底吹氬氣總流量180m3/h,7分鐘后,轉(zhuǎn)爐底吹氬氣總流量210m3/h;(3)過程加料:開吹點火后,先加入500~1000kg污泥球,再加入第一批渣料,3min左右起渣后,加入200kg污泥球、150kg螢石或化渣劑;之后每隔20s加入200kg污泥球,保證均勻升溫,4min以后開始加入石灰和白云石,加料應(yīng)勻速,少量多批,此時高FeO含量的有利條件促進(jìn)石灰、白云石的快速熔化,7分鐘內(nèi)加完石灰和白云石,防止出現(xiàn)返干現(xiàn)象,保證全程化渣;為防止終點壓槍過程爐渣返干回磷,壓槍前可加入100kg~200kg污泥球;(4)終點加料:終點加料時,如果第一次倒?fàn)t熔池溫度高或碳高,可補加污泥球,第一次倒?fàn)t鋼中碳大于0.40%時,補吹時嚴(yán)禁補加石灰和白云石,以防止出鋼過程爐渣返干、結(jié)塊、回磷;轉(zhuǎn)爐冶煉終點鋼水的C=0.20~0.50%、P≤0.015%。進(jìn)一步地,所述步驟(1)中,鐵水成分(以質(zhì)量百分?jǐn)?shù)計):Si≤0.60%、Mn≤0.60%、P≤0.170%、S≤0.060%;總裝入量95±0.5t。進(jìn)一步地,所述步驟(1)中,開吹前設(shè)定:前期爐渣堿度按2.0~2.8、MgO按7%~8%設(shè)定,終渣堿度按4.0~5.0、MgO按8%~9%設(shè)定,過程加料按計算機(jī)中的熱平衡計算與渣料加入量計算結(jié)果執(zhí)行。進(jìn)一步地,所述步驟(2)中,同時通過氧槍向轉(zhuǎn)爐頂吹氧氣,前3min,開吹氧氣流量設(shè)為19000m3/h;吹煉3~7分鐘,氧氣流量16000m3/h;吹煉7分鐘之后氧氣流量調(diào)至18500m3/h,直至吹煉終點;開吹點火后槍位控制在1.8m加入第一批渣料,加完第一批料后,待火焰平穩(wěn),吹煉1分鐘將槍位分兩次降到1.2m;起渣前3分鐘左右將氧氣流量調(diào)至16000m3/h,起渣后讓槍至1.4~1.7m,并開始少量多批加入污泥球;起渣后就可以提高槍位至1.6m左右,并開始加第二批石灰和白云石,7分鐘內(nèi)加完;9~10分鐘,將氧槍讓到1.9~2.0m,最大限度化渣,保證去磷效果;10分鐘時,點動提爐罩,根據(jù)火焰判斷溫度,溫度高時可補加污泥球;壓槍前必須把槍位吊到1.8~2m,讓爐渣最大限度熔化之后再壓槍;終點壓槍前可加入100~200kg污泥球以防止壓槍過程返干;壓槍時,分2~3次把槍位壓到1.3m,10秒后壓到1.2m,壓槍時間從壓到1.3m開始計算,壓槍時間控制在20秒以上,補吹時保證壓槍至1.2m的時間>10秒。進(jìn)一步地,所述步驟(4)中,采用高拉碳補吹法,第一次倒?fàn)t,鋼水的目標(biāo)溫度為1580~1600℃,目標(biāo)C含量0.20%~0.50%,目標(biāo)P含量≤0.015%;出鋼溫度為1600~1620℃,出鋼P含量≤0.015%。進(jìn)一步地,第一次加入污泥球時,如爐渣泡沫化太嚴(yán)重則加入石灰或白云石,同時將轉(zhuǎn)爐底吹氬氣的流量上調(diào)至180m3/min。進(jìn)一步地,加第二批石灰和白云石時,若出現(xiàn)返干現(xiàn)象,則加入200~400kg化渣劑,之后根據(jù)爐溫情況加入污泥球,控制爐溫在1400~1600℃。本發(fā)明的有益效果是:本發(fā)明所述的一種82B鋼的轉(zhuǎn)爐冶煉工藝,采用單渣操作,冶煉82B高碳鋼,使轉(zhuǎn)爐冶煉終點鋼水的C含量更高而P含量更低,克服了初期渣中的磷隨著爐溫上升而又回到鋼水中導(dǎo)致前功盡棄的問題;同時,初期渣中含有大量的金屬鐵,單渣操作不倒初期渣,一渣到底,大大減少了金屬鐵的浪費,也減少了造渣材料的消耗,從而降低了冶煉成本,提高了冶煉質(zhì)量。附圖說明圖1為本發(fā)明中單渣冶煉優(yōu)質(zhì)鋼的操作折線圖;圖2為本發(fā)明中轉(zhuǎn)爐冶煉過程中的爐渣成分變化三元圖。圖中:Ⅰ-液相+SiO2;Ⅱ-液相;Ⅲ-液相+2CaO·SiO2;Ⅳ-液相+2CaO·SiO2+3CaO·SiO2;Ⅴ-液相+3CaO·SiO2;Ⅵ-液相+3CaO·SiO2+CaO;Ⅶ-液相+CaO。具體實施方式下面結(jié)合附圖進(jìn)一步描述本發(fā)明的技術(shù)方案,但要求保護(hù)的范圍并不局限于所述。本發(fā)明所述的一種82B鋼的轉(zhuǎn)爐冶煉工藝,包括兌入高爐鐵水、轉(zhuǎn)爐底吹氬氣、過程加料、終點加料步驟:(1)兌入高爐鐵水:采用100噸頂?shù)讖?fù)吹轉(zhuǎn)爐,向轉(zhuǎn)爐中兌入高爐鐵水,其中,鐵水成分(以質(zhì)量百分?jǐn)?shù)計):Si≤0.60%、Mn≤0.60%、P≤0.170%、S≤0.060%,其余金屬料為生鐵塊、廢鋼、渣鋼等;總裝入量95±0.5t,鐵水裝入量參考表1;鐵水裝入量可根據(jù)熱量作適當(dāng)調(diào)整(保證污泥球用量1~3t),其余用廢鋼補齊。高爐鐵水中含磷為0.104%~0.157%,在沒有測溫取樣的副槍條件下,利用上述的高磷鐵水,采用單渣操作,冶煉82B高碳鋼;表1不同鐵水[Si]對應(yīng)的鐵水裝入量鐵水[Si]%<0.30.3~0.50.5~0.6鐵水量(t)88~9084~8882~86開吹前設(shè)定:前期爐渣堿度按2.0~2.8、MgO按7%~8%設(shè)定,終渣堿度按4.0~5.0、MgO按8%~9%設(shè)定,過程加料按計算機(jī)中的熱平衡計算與渣料加入量計算結(jié)果執(zhí)行。如圖1所示,開吹氧氣流量設(shè)為19000m3/h,吹煉3~7分鐘,氧氣流量16000m3/h,吹煉7分鐘之后氧氣流量調(diào)至18500m3/h直至吹煉終點;開吹點火后槍位控制在1.8m加入第一批渣料,加完第一批料后,待火焰平穩(wěn),吹煉1分鐘將槍位分兩次降到1.2m;3分鐘左右(起渣前)將氧氣流量調(diào)至16000m3/h,起渣后讓槍至1.4~1.7m,并開始少量多批加入污泥球,如爐渣泡沫化太嚴(yán)重則加入石灰或白云石,同時將轉(zhuǎn)爐底吹氬氣的流量上調(diào)至180m3/min;起渣后就可以提高槍位至1.6m左右,并開始加第二批石灰和白云石,7分鐘內(nèi)加完,如有返干現(xiàn)象,可加入200~400kg化渣劑,之后根據(jù)爐溫情況加入污泥球;9~10分鐘,將氧槍讓到1.9~2.0m,最大限度化渣,保證去磷效果;10分鐘時,點動提爐罩,根據(jù)火焰判斷溫度,溫度高時可補加污泥球;壓槍前必須把槍位吊到1.8~2m,讓爐渣最大限度熔化之后再壓槍;終點壓槍前可加入100~200kg污泥球以防止壓槍過程返干;壓槍時,分2~3次把槍位壓到1.3m,10秒后壓到1.2m,壓槍時間從壓到1.3m開始計算,壓槍時間控制在20秒以上,補吹時保證壓槍至1.2m的時間>10秒。(2)轉(zhuǎn)爐底吹氬氣:冶煉過程中,向轉(zhuǎn)爐底吹氬氣,從開始吹煉計算,前3分鐘,轉(zhuǎn)爐底吹氬氣總流量150m3/h,第3~7分鐘,轉(zhuǎn)爐底吹氬氣總流量180m3/h,7分鐘后,轉(zhuǎn)爐底吹氬氣總流量210m3/h;(3)過程加料:開吹點火后,先加入500~1000kg污泥球,再加入第一批渣料,3min左右起渣后,加入200kg污泥球、150kg螢石或化渣劑;之后每隔20s加入200kg污泥球,保證均勻升溫,4min以后開始加入石灰和白云石,加料應(yīng)勻速,少量多批,此時高FeO含量的有利條件促進(jìn)石灰、白云石的快速熔化,7分鐘內(nèi)加完石灰和白云石,防止出現(xiàn)返干現(xiàn)象,保證全程化渣;為防止終點壓槍過程爐渣返干回磷,壓槍前可加入100kg~200kg污泥球;(4)終點加料:采用高拉碳補吹法,第一次倒?fàn)t,鋼水的目標(biāo)溫度為1580~1600℃,目標(biāo)C含量0.20%~0.50%,目標(biāo)P含量≤0.015%;出鋼溫度為1600~1620℃,出鋼P含量≤0.015%;終點加料時,如果第一次倒?fàn)t熔池溫度高或碳高,可補加污泥球,第一次倒?fàn)t鋼中碳大于0.40%時,補吹時嚴(yán)禁補加石灰和白云石,以防止出鋼過程爐渣返干、結(jié)塊、回磷;轉(zhuǎn)爐冶煉終點鋼水的C=0.20~0.50%、P≤0.015%。實施例以首鋼水城鋼鐵集團(tuán)公司煉鋼廠采用本技術(shù)方案冶煉低成本82B鋼的轉(zhuǎn)爐冶煉工藝實踐為例,進(jìn)一步對本技術(shù)方案進(jìn)行說明。本發(fā)明所述的一種82B鋼的轉(zhuǎn)爐冶煉工藝,包括如下步驟:(1)兌入高爐鐵水對鐵水、廢鋼的準(zhǔn)備、來源及用量作如下規(guī)定:①從煉鐵廠來的大罐鐵水必須先倒入混鐵爐進(jìn)行成分、溫度的混勻,再將混鐵爐中的鐵水倒入轉(zhuǎn)爐兌鐵罐,然后將鐵水兌入轉(zhuǎn)爐;②每當(dāng)大罐鐵水倒入混鐵爐后,混鐵爐工人必須及時測溫并取樣分析,之后將鐵水溫度和鐵水成分分析結(jié)果報告爐前工人;③鐵水必須稱量準(zhǔn)確方可進(jìn)入轉(zhuǎn)爐;④廢鋼必須按要求進(jìn)行搭配,實際重量在目標(biāo)重量±0.5t以內(nèi),稱量要準(zhǔn)確。采用100噸頂?shù)讖?fù)吹轉(zhuǎn)爐,利用P=0.104~0.157%的高磷鐵水,單渣操作,冶煉82B高碳鋼,控制轉(zhuǎn)爐冶煉終點鋼水的C含量為0.20~0.50%,從而有效地去除鋼水中的磷,使P含量≤0.015%。這樣既可以有效地去除鋼水中的磷,又可以減少鐵水中Cr的氧化(可使鋼水中的殘余Cr含量最高達(dá)到0.10%),從而減少增碳劑、合金用量。裝料時,兌入鐵水88噸,生鐵塊3噸,廢鋼2.5噸,渣鋼2噸;在轉(zhuǎn)爐裝料過程中,入爐料主要是鐵水、廢鋼、生鐵塊和含鐵資源(渣鋼、污泥球、冷固球),由于各種資源價格不一樣,通過優(yōu)化調(diào)整,充分利用廉價含鐵資源替代廢鋼資源,可實現(xiàn)經(jīng)濟(jì)效益最大化。根據(jù)水鋼的鐵水、廢鋼、石灰等原料及輔料條件,通過熱平衡計算和現(xiàn)場跟蹤驗證,建立了水鋼100t轉(zhuǎn)爐冶煉82B高碳鋼的熱平衡加料參考表表2和100t轉(zhuǎn)爐溫度控制及調(diào)整參考數(shù)據(jù)表表3;爐前工根據(jù)原料的變化情況,參照表2和表3,就可對每爐鋼的熱量情況作出一個近似估計,在吹煉過程中進(jìn)行及時調(diào)整,通過跟蹤和校正,此熱平衡計算結(jié)果與實際操作情況非常接近,對操作具有相當(dāng)大的指導(dǎo)作用。表2100t轉(zhuǎn)爐熱平衡加料參考表表3100t轉(zhuǎn)爐溫度控制及調(diào)整參考數(shù)據(jù)表(2)向轉(zhuǎn)爐底吹氬氣:從開始吹煉計算,前3分鐘內(nèi),底吹透氣磚(共6塊磚)總流量150m3/h,每塊透氣磚流量25m3/h;3~7分鐘,底吹總流量180m3/h;7分鐘以后,底吹總流量210m3/h。吹煉的前3分鐘熔池溫度低,此階段升溫化渣是主要任務(wù),適當(dāng)降低轉(zhuǎn)爐底吹氬氣流量,有助于熔池表面升溫和FeO的聚集,從而加速活性石灰的熔化。最佳脫磷溫度范圍是1400~1500℃。冶煉優(yōu)質(zhì)鋼時,廢鋼比小,前期熔池溫度上升較快,在3min后就進(jìn)入1400℃以上的最佳脫磷溫度區(qū)域,此時碳氧反應(yīng)加劇,渣中FeO被快速消耗,為了創(chuàng)造熔池溫度在1400~1500℃以及渣中FeO在14~25%的最佳脫磷條件,在熔池溫度達(dá)到1400℃以后,以每隔20秒加入200kg的加料速度加入含F(xiàn)eO的冷卻劑,具體參見步驟(3)。為了控制噴濺和延長前期爐渣FeO高、爐溫低的最佳脫磷時間,此時可調(diào)低氧氣流量和增加轉(zhuǎn)爐底吹氬氣量。在最初的Si氧化期,應(yīng)提高槍位,同時降低供氧流量,延長冶煉在低溫區(qū),即1400℃~1500℃的持續(xù)時間。(3)開吹前設(shè)定:前期爐渣堿度按2.0%~2.8%、MgO按7%~8%設(shè)定,終渣堿度按4.0%~5.0%、MgO按8%~9%設(shè)定,過程加料按計算機(jī)中的熱平衡計算與渣料加入量計算結(jié)果執(zhí)行。開吹點火后,先加入500~1000kg污泥球,再加入第一批渣料,3分鐘左右起渣后,加入200kg污泥球、150kg螢石或化渣劑,之后每隔20秒加入200kg污泥球,保證均勻升溫,4分鐘以后即可開始加入石灰和白云石,此時高FeO含量的有利條件促進(jìn)石灰、白云石的快速熔化,加料要勻速,少量多批,前7分鐘內(nèi)加完石灰和白云石,防止出現(xiàn)返干現(xiàn)象,保證全程化渣;為防止終點壓槍過程爐渣返干回磷,壓槍前可加入100kg~200kg污泥球。含鐵資源中污泥球的鐵含量高、堿度高、MgO含量高、有豐富的FeO,堿度高可以減少轉(zhuǎn)爐石灰的用量,MgO含量高對轉(zhuǎn)爐護(hù)爐有利,豐富的FeO含量有利于轉(zhuǎn)爐前期快速成渣,對脫磷非常有利。(4)終點加料時,如果第一次倒?fàn)t熔池溫度高或碳高,可補加污泥球,第一次倒?fàn)t鋼中碳大于0.40%時,補吹時嚴(yán)禁補加石灰和白云石,以防止出鋼過程爐渣返干、結(jié)塊、回磷;為避免熔池快速升溫,鐵皮、礦石、螢石要分批錯開加入,這樣既保證爐渣活躍,又避免爐渣返干、回磷。步驟(2)進(jìn)行的同時,通過氧槍,向轉(zhuǎn)爐頂吹氧氣,前3min,開吹氧氣流量設(shè)為19000m3/h,吹煉3~7分鐘,氧氣流量16000m3/h,吹煉7分鐘之后氧氣流量調(diào)至18500m3/h,直至吹煉終點。開吹點火后槍位控制在1.8m加入第一批渣料,加完第一批料后,待火焰平穩(wěn),吹煉1分鐘將槍位分兩次降到1.2m;3分鐘左右(起渣前)將氧氣流量調(diào)至16000m3/h,起渣后將槍位調(diào)整至1.4~1.7m,并開始少量多批加入污泥球,如爐渣泡沫化太嚴(yán)重則加入石灰或白云石,同時將轉(zhuǎn)爐底吹氬氣每塊磚的流量上調(diào)至30m3/min;起渣后就可以提高槍位至1.6m左右,并開始加第二批石灰和白云石,前7分鐘內(nèi)加完,如有返干現(xiàn)象,可加入200~400kg化渣劑,之后根據(jù)爐溫情況加入污泥球;9~10分鐘,將氧槍位進(jìn)一步提高到1.9~2.0m,最大限度化渣,保證去磷效果;10分鐘時,點動提爐罩,根據(jù)火焰判斷溫度,溫度高時可補加污泥球。壓槍前必須把槍位吊到1.8~2.0m,讓爐渣最大限度熔化之后再壓槍。終點壓槍前可加入100~200kg污泥球以防止壓槍過程返干;壓槍時,分2~3次把槍位壓到1.3m,10秒后壓到1.2m,壓槍時間從壓到1.3m開始計算,壓槍時間控制在20秒以上。補吹時保證壓槍至1.2m的時間>10秒。在轉(zhuǎn)爐采用高拉碳出鋼后,鋼水的氧化性降低,可減少Si-Ca-Ba復(fù)合脫氧劑的使用量。在轉(zhuǎn)爐出鋼過程中,將Si-Mn合金的用量增加200kg/爐,以降低鋼水氧含量,減少鋼中夾雜物,為LF爐精煉工序造還原渣、減少鈣處理喂絲量創(chuàng)造良好條件,又減少了LF爐精煉過程中高碳錳鐵的加入量,節(jié)約了成本。在保證轉(zhuǎn)爐良好的脫磷和高拉碳的前提下,使出鋼溫度達(dá)到1600~1620℃,使鋼水進(jìn)LF爐精煉站的溫度從1490~1520℃提高到1510~1530℃,以減少精煉爐耗電量。轉(zhuǎn)爐冶煉工序完成后,進(jìn)入LF爐精煉工序。單渣方案的使用情況單渣方案用在水鋼100噸轉(zhuǎn)爐冶煉82B鋼200爐,其鐵水成分和溫度見表4,過程控制情況見表5,終點爐渣成分見表6。從表4可見,鐵水P含量為0.104~0.157%,平均0.13%,用這樣的高磷鐵水單渣操作成功地冶煉82B優(yōu)質(zhì)鋼。從表5可見,單渣冶煉優(yōu)質(zhì)鋼的鋼鐵料消耗為1044~1049kg/t,平均1047kg/t,比雙渣冶煉降低了7kg/t,石灰消耗為24.6~34.7kg/t,平均29.4kg/t,比雙渣冶煉降低了3kg/t。出鋼時C含量為0.20~0.30%,平均0.25%,出鋼時P含量為0.011~0.015%,平均0.013%,實現(xiàn)了低成本冶煉82B優(yōu)質(zhì)鋼。經(jīng)過大量的研究和現(xiàn)場生產(chǎn)試驗,使每噸82B鋼的冶煉成本降低了200元以上。表4100t轉(zhuǎn)爐單渣冶煉優(yōu)質(zhì)鋼的鐵水成分和溫度數(shù)值特征C(%)Si(%)Mn(%)P(%)S(%)溫度(℃)范圍3.70~5.800.23~0.510.16~0.280.104~0.1570.022~0.0381307~1345均值4.700.360.230.130.0321322表5100t轉(zhuǎn)爐單渣冶煉優(yōu)質(zhì)鋼的過程控制情況表6100t轉(zhuǎn)爐單渣冶煉優(yōu)質(zhì)鋼的終點爐渣成分為了盡快得到具有一定性能的爐渣,需要選擇合理的成渣路線。在轉(zhuǎn)爐冶煉條件下,可以用CaO-FeO-SiO2三元相圖來研究冶煉過程中的成渣路線,其它次要組分可按性質(zhì)歸入這3個組分中,如圖2所示。轉(zhuǎn)爐吹煉初期爐渣成分大致位于圖中的A區(qū)。A區(qū)為酸性初渣區(qū),其形成的主要原因是:在開吹的頭幾分鐘內(nèi)熔池溫度比較低(約為1400℃),加入的第一批渣料中,石灰才剛剛開始溶解,硅、錳等元素優(yōu)先氧化,生成FeO、SiO2和MnO,形成了高氧化性的酸性初渣區(qū)。吹煉中期主要是脫碳,此時爐渣的氧化性有所下降。而吹煉后期為了脫磷、脫硫和保持爐渣的流動性,要求終渣具有一定的堿度和氧化性(即渣中FeO含量)。通常終渣堿度為3~5%,渣中FeO含量為15~25%,其位置大致在C區(qū)。由初渣到終渣可以有3條路線,即ABC,AB'C和AB"C。按成渣時渣中FeO含量可將AB'C稱為高氧化鐵成渣途徑,ABC稱為低氧化鐵成渣途徑。高氧化鐵成渣途徑能極大限度的避開2CaO·SiO2區(qū),爐渣流動性好,石灰熔化快,成渣快,吹煉中期爐渣不易返干,爐渣很快具有良好的脫磷、脫硫能力;低氧化鐵成渣途徑中,爐渣熔點高,石灰熔化緩慢,爐渣粘稠,吹煉中期爐渣容易返干,爐渣的脫磷、脫硫能力弱。根據(jù)上述分析,可很快選擇高氧化鐵成渣途徑進(jìn)行成渣。吹煉進(jìn)入中、后期之后,脫磷的各種條件發(fā)生了變化,前期脫掉的磷又有可能返回到鋼水中,從而造成前功盡棄。在1600℃時,爐渣中的(FeO)含量在15%左右、堿度在4.5左右時,爐渣的脫磷能力最強。從脫磷熱力學(xué)分析中可知,渣中的MnO屬弱堿性物質(zhì),它可降低渣中P2O5的活度系數(shù),從而提高磷的分配比,但由于MnO的增加會造成CaO和FeO含量的下降,反而會造成磷的分配比下降;渣中Al2O3含量對終渣脫磷能力也有影響,在堿性爐渣中Al2O3顯弱酸性,隨著渣中Al2O3含量升高,磷的分配比下降較快(比MnO對磷分配比的影響還要大),但在爐渣中配加適量的MnO和Al2O3可以提高爐渣的流動性,從而有利于脫磷。渣中MnO的含量控制在3~5%、Al2O3控制在<3%的范圍時,爐渣的脫磷能力最強,我們通過調(diào)整化渣劑中化學(xué)成分MnO與Al2O3的配比,使終渣成分達(dá)到最佳值。當(dāng)前第1頁1 2 3