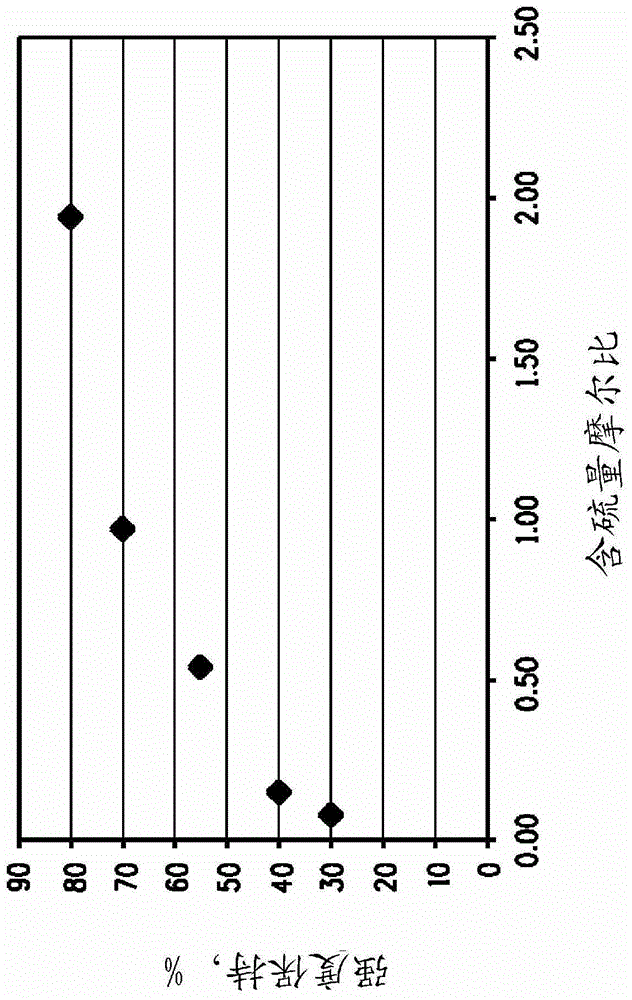
本專利申請涉及由共聚物組成的纖維和紗線,所述共聚物含有顯著量的具有咪唑官能團(tuán)具有長期水解穩(wěn)定性的單體以及制備此種纖維和紗線的方法。
背景技術(shù):在過去幾十年中聚合物化學(xué)和技術(shù)的發(fā)展啟動了高性能聚合物纖維的發(fā)展。例如,剛性棒狀和半剛性棒狀聚合物的液晶聚合物溶液可通過將液晶聚合物溶液紡絲成紡液長絲,從紡液長絲去除溶劑,洗滌和干燥纖維;并且如果需要進(jìn)一步熱處理干燥的纖維而形成為高強(qiáng)度纖維。高性能聚合物纖維的一個例子是對位芳族聚酰胺纖維例如聚(對苯二甲酰對苯二胺)(“PPD-T”或“PPTA”)。纖維強(qiáng)度通常與一種或多種聚合物參數(shù)相關(guān),包括組成、分子量、分子間相互作用、主鏈、殘余溶劑或水、大分子取向和處理過程。例如,纖維強(qiáng)度通常隨著聚合物長度(即,分子量)、聚合物取向、以及強(qiáng)分子間相互吸引作用的存在而增加。由于高分子量剛性棒狀聚合物用于形成由其可紡絲纖維的聚合物溶液(“紡液”),從而增加分子量通常導(dǎo)致增加的纖維強(qiáng)度。衍生自5(6)-氨基-2-(對氨基苯基)苯并咪唑、對苯二胺和對苯二酰二氯的纖維是本領(lǐng)域已知的。鹽酸作為聚合反應(yīng)的副產(chǎn)物產(chǎn)生。大多數(shù)由此種共聚物制成的纖維通常直接由聚合溶液紡絲而無需進(jìn)一步處理。此種共聚物是俄國制造的高強(qiáng)度纖維(例如商品名為和)的基礎(chǔ)。參見俄國專利申請2,045,586。然而,可從聚合溶液中分離所述共聚物,然后將其再溶解在另一種溶劑中,通常為硫酸,從而紡絲纖維。此前,衍生自5(6)-氨基-2-(對氨基苯基)苯并咪唑、對苯二胺和對苯二酰二氯的共聚物的纖維,在從硫酸溶液紡絲時極難有效中和是不欣賞的;這些纖維以比其它芳族聚酰胺均聚物高得多的程度保持所述硫酸。存在大量的技術(shù)教導(dǎo)表明,由芳族聚酰胺均聚物聚(對苯二甲酰對苯二胺)的硫酸溶液制成的纖維可被快速的中和/洗滌,因為均聚物不具有連接至硫酸的可估位點。5(6)-氨基-2-(對氨基苯基)苯并咪唑、對苯二胺和對苯二酰二氯的共聚物,由于咪唑官能團(tuán),據(jù)信具有多個位點實際地將硫酸連接至聚合物鏈。因此先前的用于通常均聚物纖維加工的中和/洗滌技術(shù)對這些共聚物纖維而言是不夠的。進(jìn)一步相信,共聚物纖維必須被充分地洗滌和中和以除去基本上所有的硫酸以提供具有長期水解穩(wěn)定性的纖維和/或紗線。因此,需要新的方法來洗滌和中和這些共聚物纖維。由聚合溶液直接制備共聚物纖維而制備用于彈道和其它芳族聚酰胺最終用途的合格產(chǎn)品的已知方法非常昂貴并具有非常低的投資經(jīng)濟(jì)性。因而,本領(lǐng)域需要制造方法,其中共聚物溶解在普通溶劑中,例如硫酸,其與本領(lǐng)域的已知方法相比具有改善的經(jīng)濟(jì)性并且提供了具有優(yōu)異長效物理特性的共聚物纖維。
技術(shù)實現(xiàn)要素:在一些實施例中,本發(fā)明涉及包含紗線,所述紗線包含衍生自對苯二胺、5(6)-氨基-2-(對氨基苯基)苯并咪唑和對苯二酰二氯的共聚的共聚物,其中5(6)-氨基-2-(對氨基苯基)苯并咪唑的摩爾與對苯二胺的摩爾的比率為30/70至85/15;其中紗線具有大于0.1%的含硫量;并且所述紗線具有至少0.3的有效聚合物陽離子與含硫量的摩爾比。有效聚合物陽離子與含硫量的摩爾比定義為紗線中鈉(Na)含量加兩倍鈣(Ca)含量加鉀(K)減去氯(Cl)含量的和,所述和除以硫(S)含量的值。即:其中符號[Na]、[Ca]、[K]、[Cl]和[S]為以摩爾/千克聚合物計的這些離子的濃度。在一些實施例中,5(6)-氨基-2-(對氨基苯基)苯并咪唑的摩爾與對苯二胺的摩爾的比率為45/55至85/15。在某些實施例中,(a)對苯二胺和5(6)-氨基-2-(對氨基苯基)苯并咪唑與(b)對苯二酰二氯的摩爾比為0.9-1.1。本發(fā)明的一些方面涉及包含紗線,所述紗線包含衍生自對苯二胺、5(6)-氨基-2-(對氨基苯基)苯并咪唑和對苯二酰二氯的共聚的共聚物,其中5(6)-氨基-2-(對氨基苯基)苯并咪唑的摩爾與對苯二胺的摩爾的比率為30/70至85/15,其中所述紗線具有大于0.1%的含硫量并且至少20%的咪唑環(huán)處于游離堿狀態(tài)。在一些實施例中,至少50%的咪唑環(huán)處于游離堿狀態(tài)。在其它實施例中,至少75%的咪唑環(huán)處于游離堿狀態(tài)。在一些實施例中,5(6)-氨基-2-(對氨基苯基)苯并咪唑的摩爾與對苯二胺的摩爾的比率為45/55至85/15?!坝坞x堿”意指咪唑環(huán)上的氮非完全質(zhì)子化的;即,咪唑環(huán)不以鹽形式存在。所述紗線可具有至少1.0的有效聚合物陽離子與含硫量的摩爾比或至少1.5的有效聚合物陽離子與含硫量的摩爾比。本發(fā)明的其它方面涉及處理長絲或紗線的方法,所述長絲或紗線衍生自對苯二胺、5(6)-氨基-2-(對氨基苯基)苯并咪唑和對苯二酰二氯的共聚,其中5(6)-氨基-2-(對氨基苯基)苯并咪唑的摩爾與對苯二胺的摩爾的比率為30/70至85/15;所述長絲具有大于0.1%的含硫量,其中所述方法包括用堿性水溶液洗滌長絲足以提供具有至少0.3的有效聚合物陽離子與含硫量的摩爾比的長絲的時間。在一些實施例中,5(6)-氨基-2-(對氨基苯基)苯并咪唑的摩爾與對苯二胺的摩爾的比率為45/55至85/15。在一些實施例中,用堿性水溶液洗滌所述紗線大于60秒鐘的一段時間。在某些實施例中,在使所述紗線與堿性水溶液接觸之前和之后用水進(jìn)一步洗滌所述紗線。一些優(yōu)選的堿性水溶液包括氫氧化鈉。在一些實例中,中和溶液是含有0.01至1.25摩爾堿/升,優(yōu)選0.01至0.5摩爾堿/升的水溶液。本發(fā)明還涉及具有25gpd或更高紗線韌度的紗線。本發(fā)明還涉及制備來自長絲的紗線的方法,所述長絲包含衍生自對苯二胺、5(6)-氨基-2-(對氨基苯基)苯并咪唑和對苯二酰二氯的共聚的共聚物,具有大于0.1%的含硫量,所述方法包括以下步驟:a)紡絲并收集載酸(acid-laden)紗線;以及b)在單獨步驟中,首先洗滌載酸紗線以形成中和的紗線,接著熱處理所述紗線;其中,所述中和步驟提供了其中有效聚合物陽離子與含硫量的摩爾比為約0.3或更大的紗線。附圖說明當(dāng)結(jié)合附圖閱讀時,可進(jìn)一步理解上述發(fā)明內(nèi)容以及以下具體實施方式。為了舉例說明本發(fā)明的目的,在附圖中示出了本發(fā)明的示例性實施例;然而,本發(fā)明并不限于所公開的具體方法、組合物及裝置。在附圖中:圖1是纖維制備方法的示意圖。圖2呈現(xiàn)了纖維在水解條件下的強(qiáng)度保持%對有效陽離子與含硫量的摩爾比([Na]+2[Ca]+[K]一[Cl])/[S]的曲線圖。具體實施方式通過參見與附圖以及實例相關(guān)的以下具體實施方式可更易于理解本發(fā)明,所述附圖以及實例形成本公開的一部分。應(yīng)當(dāng)理解,本發(fā)明并不限于本文所述和/或所示的具體裝置、方法、條件或參數(shù),并且本文所用的術(shù)語僅為了以舉例的方式描述具體實施例的目的,并不旨在限制受權(quán)利要求書保護(hù)的本發(fā)明。如包括所附權(quán)利要求的說明書中所用,單數(shù)形式“一種”、“一個”和“該/所述”包括復(fù)數(shù)形式,并且提及的具體數(shù)值至少包括該具體值,除非上下文清楚地另外指明。當(dāng)表述數(shù)值的范圍時,另一個實施例包括從一個具體值和/或到另一個具體值。類似地,當(dāng)值被表示為近似值時,應(yīng)當(dāng)理解,通過利用先行詞“大約”,特定值形成另一個實施例。所有范圍均包括或結(jié)合端值在內(nèi)。當(dāng)任何組分或任何公式中的任何變量不止一次出現(xiàn)時,其每次出現(xiàn)的定義與每次在其它地方出現(xiàn)的定義無關(guān)。僅在取代基和/或變量的組合形成穩(wěn)定化合物時,才允許此類組合。本發(fā)明涉及一種方法,其在高固體份(7%或更高)下在NMP/CaCl2或DMAC/CaCl2中進(jìn)行5(6)-氨基-2-(對氨基苯基)苯并咪唑、對苯二胺和對苯二酰二氯的聚合,分離共聚物屑粒,將分離的共聚物屑粒溶解在濃硫酸中以形成液晶溶液,并且將溶液紡絲成纖維。所謂“固體份”意指共聚物的質(zhì)量與溶液的總質(zhì)量(即共聚物加溶劑的質(zhì)量)的比率。5(6)-氨基-2-(對氨基苯基)苯并咪唑、對苯二胺和對苯二酰二氯的共聚反應(yīng)可通過本領(lǐng)域已知的方法來完成。參見,例如PCT專利申請2005/054337和美國專利申請2010/0029159。通常,一種或多種?;群鸵环N或多種芳族二胺可在酰胺極性溶劑例如N,N-二甲基甲酰胺、N,N-二甲基乙酰胺、N-甲基-2-吡咯烷酮、二甲基咪唑烷酮等中進(jìn)行反應(yīng)。在一些實施例中,N-甲基-2-吡咯烷酮是優(yōu)選的。在一些實施例中,在共聚之前或期間,以適宜的量加入無機(jī)鹽溶解劑例如氯化鋰或氯化鈣等,從而提高所得共聚酰胺在酰胺極性溶劑中的溶解度。通常,加入相對于酰胺極性溶劑3至10重量%。在獲得期望的聚合度之后,所述共聚物以未中和屑粒的形式存在。所謂“屑?!币庵杆龉簿畚餅橐姿椴牧匣蚰z的形式,當(dāng)剪切時其容易分離成可識別的分離塊狀體。所述未中和的屑粒包括共聚物,聚合溶劑,溶解劑和副產(chǎn)物水以及來自縮合反應(yīng)的酸,通常為鹽酸(HCl)。在聚合反應(yīng)完成后,然后使未中和的屑粒與堿接觸,所述堿可為堿性無機(jī)化合物,例如氫氧化鈉、氫氧化鉀、氫氧化鈣、氧化鈣、氫氧化銨等,通常以含水的形式,加入所述堿以進(jìn)行HCl副產(chǎn)物的中和反應(yīng)。如果需要,所述堿性化合物可為有機(jī)堿,例如二乙胺或三丁胺或者其它胺。通常,未中和的共聚物屑粒通過洗滌與含水堿接觸,其將酸性副產(chǎn)物轉(zhuǎn)化成鹽(如果氫氧化鈉是所述堿并且HCl是所述酸性副產(chǎn)物則為氯化鈉)并且還去除了一些聚合溶劑。如果需要,可將所述未中和的共聚物屑粒任選地用水在與堿性無機(jī)化合物接觸之前先洗滌一次或多次以除去去除過量的聚合溶劑。一旦將共聚物屑粒中的酸性副產(chǎn)物中和,可采用附加的水洗以去除鹽和聚合溶劑并降低屑粒的pH,如果需要。本發(fā)明還涉及用于形成芳族聚酰胺紗線的方法,其包括將衍生自對苯二胺、5(6)-氨基-2-(對氨基苯基)苯并咪唑和對苯二酰二氯的共聚的共聚物屑粒溶解在硫酸中以形成紡絲溶液,其中所述共聚物屑粒在形成所述紡絲溶液之前被中和;所述共聚物具有至少3dl/g的特性粘度并且具有小于0.4mol/Kg的可滴定酸。在一個優(yōu)選的實施例中,所述共聚物屑粒通過用含水堿洗滌而中和。對苯二酰二氯還稱為對苯二甲酰氯。所述共聚物優(yōu)選使用溶液紡絲紡成纖維。通常,這包括將中和的共聚物屑粒在適宜的溶劑中溶液化以形成紡絲溶液(還稱為紡絲紡液),優(yōu)選的溶劑是硫酸。發(fā)明人已經(jīng)發(fā)現(xiàn),當(dāng)將此種中和的屑粒與硫酸在溶液化步驟中混合時,使用本文所述的已經(jīng)被中和的共聚物屑粒顯著地降低了紡絲紡液中氣泡的形成。如果共聚物屑粒是沒有被中和的,則共聚物中的鹽酸副產(chǎn)物將會在與硫酸接觸時揮發(fā)并且在紡絲紡液中形成氣泡。由于紡絲紡液的溶液粘度相對較高,在溶液化期間形成的任何此類氣泡趨于保留在紡絲紡液中,并且紡成長絲。當(dāng)在硫酸中溶液化時,中和的共聚物屑粒提供了基本上無氣泡并且因此更均勻的紡絲溶液,據(jù)信它能提供更均勻的優(yōu)異的共聚物長絲和纖維。含有本文所述的共聚物的紡絲紡液可使用任意數(shù)目的方法紡成紡液長絲;然而,濕法紡絲和“氣隙”紡絲是最有名的。用于這些紡絲方法中的噴絲頭和浴的一般構(gòu)造是本領(lǐng)域熟知的,美國專利3,227,793、3,414,645、3,767,756和5,667,743中的附圖說明了對于高強(qiáng)度聚合物的此種紡絲方法。在“氣隙”紡絲中,噴絲頭通常先將纖維擠出進(jìn)入氣體例如空氣中,并且是形成長絲的一種優(yōu)選方法。據(jù)信除了用中和的共聚物屑粒制備紡絲紡液以外,為了最佳的纖維特性,由酸溶劑紡絲纖維的制造方法不僅附加包括從紡液長絲中萃取酸溶劑的步驟,而且還包括進(jìn)一步除去和/或中和與纖維中的共聚物相關(guān)聯(lián)或者附著在其上的任何殘余的酸。據(jù)信如果此操作失效將會導(dǎo)致纖維中的共聚物更多潛在的降解并且接著隨著時間降低纖維的機(jī)械性能。圖1中顯示了制備共聚物紗線的一種方法。紡液2,包含共聚物和硫酸,通常含有對于聚合物而言足夠高的聚合物濃度,從而在擠出和凝固之后形成可接受的長絲6。當(dāng)所述聚合物是溶致液晶時,紡液2中的聚合物濃度優(yōu)選足夠高以提供液晶紡液。聚合物的濃度優(yōu)選為至少約7重量%,更優(yōu)選至少約10重量%并且最優(yōu)選至少約14重量%。聚合物紡液溶液2可含有添加劑例如抗氧化劑、潤滑劑、紫外線遮蔽劑、著色劑等,其通??杀粨饺?。聚合物紡液溶液2通常通過模頭或噴絲頭4擠出或紡絲以制備或形成紡液長絲6。噴絲頭4優(yōu)選含有多個孔。噴絲頭中孔的數(shù)目以及它們的排列并不是至關(guān)重要的,但是由于經(jīng)濟(jì)原因,期望最大化孔的數(shù)目。噴絲頭4可含有多達(dá)100或1000個或者更多個孔,它們可布置成圓形或網(wǎng)格,或者任何其它期望的布置方式。噴絲頭4可使用不被紡液溶液2嚴(yán)重降解的任何材料構(gòu)成。圖1的紡絲方法采用了“氣隙”紡絲(有時還稱為“干噴”濕紡絲)。紡液2排出噴絲頭4并且在非常短的持續(xù)時間內(nèi)進(jìn)入噴絲頭4和凝固浴10之間的間隙8(通常稱作“氣隙”,雖然它不需要包含空氣)。間隙8可包含不引起凝固或不與紡液發(fā)生不利反應(yīng)的任何流體,例如空氣、氮氣、氬氣、氦氣或二氧化碳。紡液長絲6橫跨氣隙8前進(jìn),并且被立即引入液體凝固浴中。作為另外一種選擇,所述纖維可被“濕紡絲”(未示出)。在濕紡中,噴絲頭通常將纖維直接擠出進(jìn)入凝固浴的液體,并且通常將噴絲頭浸沒或定位在凝固浴表面的下面。任一紡絲方法都可用于提供用于本發(fā)明方法的纖維。在本發(fā)明的一些實施例中,氣隙紡絲是優(yōu)選的。長絲6是在含有水或水和硫酸的混合物的凝固浴10中“凝固的”。如果同時擠出多根長絲,則它們可在凝固步驟之前、期間或之后被結(jié)合成復(fù)絲。如本文所用,術(shù)語“凝固”并不一定意味著紡液長絲6是流動的液體并且轉(zhuǎn)變成固相??蓪⒓徱洪L絲6置于足夠低的溫度下,使得其在進(jìn)入凝固浴10之前基本上不流動。然而,凝固浴10確實能保證或完成長絲的凝固,即聚合物從紡液溶液2轉(zhuǎn)化為基本上固態(tài)的聚合物長絲12。凝固步驟期間去除的溶劑(即硫酸)的量將取決于凝固浴中長絲6的停留時間、浴10的溫度以及其中溶劑的濃度。例如,在約23℃的溫度下使用18重量%共聚物/硫酸溶液,約一秒的停留時間將去除存在于長絲6中約30%的溶劑。凝固浴之后,可使所述纖維與一個或多個洗滌浴或箱14接觸。洗滌可通過將所述纖維浸入浴中或者通過用水溶液噴霧所述纖維來完成。洗滌箱通常包括含有一個或多個輥的封閉箱,其中紗線在退出所述箱之前多次環(huán)繞并穿越所述輥行進(jìn)。當(dāng)紗線12環(huán)繞輥行進(jìn)時,會對其噴霧洗滌流體。洗滌流體連續(xù)收集在箱的底部,并從此處排出。一種或多種洗滌流體的溫度優(yōu)選地大于30℃。也可以蒸氣形式(蒸汽)來施用洗滌流體,但以液體形式使用更為方便。優(yōu)選地,使用多個洗滌浴或箱。紗線12在任何一個洗滌浴或箱14中的停留時間將取決于期望的紗線12中的殘留的硫濃度。在連續(xù)方法中,在優(yōu)選的多個洗滌浴和/或箱中的整個洗滌方法的持續(xù)時間優(yōu)選地不大于約10分鐘,更優(yōu)選地大于約5秒鐘。在一些實施例中,整個洗滌方法的持續(xù)時間為20秒或更長;在一些實施例中,整個洗滌在400秒或更短時間內(nèi)完成。在間歇方法中,整個洗滌方法的持續(xù)時間可以大約小時計,多達(dá)12至24小時或更長。中和紗線中的硫酸可在浴或箱16中進(jìn)行。在一些實施例中,中和浴或箱可跟隨一個或多個洗滌浴或箱。洗滌可通過將纖維浸入浴中或者通過用水溶液噴霧所述纖維來完成。中和可在一個浴或箱或者在多個浴或箱中進(jìn)行。在一些實施例中,優(yōu)選用于中和硫酸雜質(zhì)的堿包括NaOH;KOH;Na2CO3;NaHCO3;NH4OH;Ca(OH)2;K2CO3;KHCO3、或三烷基胺(優(yōu)選為三丁胺);其它胺;或它們的混合物。在一個實施例中,堿是水溶性的。在一些優(yōu)選的實例中,中和溶液是含有0.01至1.25摩爾堿/升,優(yōu)選0.01至0.5摩爾堿/升的水溶液。陽離子的量也取決于暴露于堿的時間和溫度以及洗滌方法。在一些優(yōu)選的實施例中,所述堿是NaOH或Ca(OH)2。用堿處理纖維之后,所述方法可任選地包括以下步驟:使紗線與含有水或酸的洗滌溶液接觸以去除所有或基本上所有過量的堿。這種洗滌溶液可被施用于一個或多個洗滌浴或箱18中。洗滌和中和之后,纖維或紗線12可在干燥器20中干燥以除去水和其它液體??墒褂靡粋€或多個干燥器。在某些實施例中,所述干燥器可為烘箱,其使用加熱的空氣干燥所述纖維。在其它實施例中,可使用加熱輥來加熱所述纖維。在干燥器中將所述纖維加熱到至少約20℃但小于約100℃的溫度直到纖維的含水量為20重量%或更低。在一些實施例中,將所述纖維加熱到85℃或更低。在一些實施例中,在那些條件下將所述纖維加熱直到纖維的含水量為所述纖維的14重量%或更低。發(fā)明人已經(jīng)發(fā)現(xiàn)低溫干燥是改善纖維強(qiáng)度的優(yōu)選途徑。具體地,發(fā)明人已經(jīng)發(fā)現(xiàn),當(dāng)未干燥紗線經(jīng)歷的第一干燥步驟是在溫和的溫度下進(jìn)行(即,加熱輥、烘箱中的加熱氣氛等)而不是在商業(yè)規(guī)模上干燥高強(qiáng)度纖維的連續(xù)方法中所使用的通常溫度下進(jìn)行時,可獲得最佳的纖維強(qiáng)度特性。據(jù)信,共聚物纖維比PPD-T均聚物具有更強(qiáng)的對水的親和力;這種親和力降低了干燥期間水?dāng)U散出聚合物的速率,并且接著如果將未干燥紗線直接暴露于典型的高干燥溫度下(通常用于產(chǎn)生大的熱驅(qū)動力并且降低干燥時間),則將會對纖維造成不可挽回的損傷,導(dǎo)致纖維強(qiáng)度降低。在一些實施例中,將所述纖維至少加熱到約30℃;在一些實施例中,將所述纖維至少加熱到約40℃。干燥器停留時間少于10分鐘并且優(yōu)選少于180秒鐘。所述干燥器可提供氮氣或其它非反應(yīng)性氣氛。所述干燥步驟通常在大氣壓下進(jìn)行。然而,如果需要,所述步驟可在減壓下進(jìn)行。在一個實施例中,所述紗線在至少0.1gpd的張力下,優(yōu)選在2gpd或更大的張力下干燥。干燥步驟之后,將所述纖維優(yōu)選進(jìn)一步加熱到至少350℃的溫度,例如在熱定型裝置22中進(jìn)行??墒褂靡环N或多種裝置。例如,此類方法可在氮氣吹掃的管爐22中進(jìn)行以增加韌度和/或減少長絲中分子的機(jī)械應(yīng)變。在一些實施例中,將所述纖維或紗線加熱到至少400℃的溫度。在一個實施例中,將所述紗線進(jìn)一步地在1gpd或更小的張力下,使用僅足夠牽引紗線通過加熱裝置的張力加熱。在一些實施例中,所述加熱是多步方法。例如,在第一步中,將所述纖維或紗線在200至360℃的溫度下在至少0.2cN/dtex的張力下加熱,接著進(jìn)行第二加熱步驟,其中將所述纖維或紗線在370至500℃的溫度下在小于1cN/dtex的張力下加熱。最后,將紗線12在卷繞裝置24上纏繞包裝。輥、插腳、導(dǎo)引和/或機(jī)械化裝置26被適宜地定位以將所述紗線通過所述方法傳輸。此類裝置是本領(lǐng)域熟知的并且可使用任何適宜的裝置。聚合物的分子量通常根據(jù)一種或多種稀釋溶液粘度測量而監(jiān)測或者與其相關(guān)聯(lián)。因此,相對粘度(“Vrel”或“ηrel”或“nrel”)和特性粘度(“Vinh”或“ηinh”或“ninh”)的稀釋溶液測量通常用于監(jiān)測聚合物的分子量。根據(jù)以下表達(dá)式,稀釋聚合物溶液的相對粘度和特性粘度是相關(guān)聯(lián)的Vinh=ln(Vrel)/C,其中,ln是自然對數(shù)函數(shù)并且C是聚合物溶液的濃度。Vrel是無單位比值,因此Vinh以濃度倒數(shù)單位表達(dá),通常作為分升/克(“dl/g”)。本發(fā)明還進(jìn)一步部分地涉及織物,其包括本發(fā)明的長絲或紗線,以及制品,其包括本發(fā)明的織物。為了本文的目的,“織物”意指任何機(jī)織、針織或非織造結(jié)構(gòu)。所謂“機(jī)織”意指任何織物編織,例如平織、四經(jīng)破緞紋織、方平織、緞面編織、斜紋編織等。所謂“針織”意指通過將一個或多個經(jīng)線、纖維或復(fù)絲紗線相互環(huán)連或相互交叉而制備的結(jié)構(gòu)。所謂“非織造”意指纖維網(wǎng)絡(luò),包括單向纖維(如果在基質(zhì)樹脂中含有),氈等?!袄w維”是指相對柔韌的、具有高的長寬比的物質(zhì)單元,其中所述寬度跨越垂直于其長度的橫截面區(qū)域。在本文中,術(shù)語“纖維”與術(shù)語“長絲”互換使用。本文所述的長絲橫截面可為任何形狀,但是通常為圓形或菜豆形。紡絲到卷裝中線軸上的纖維稱作連續(xù)纖維。纖維可被切割成短長度,稱作短纖維。纖維可被切割成更小的長度,稱作絮狀物。本文使用的術(shù)語“紗線”包括長絲的絲束,還稱為復(fù)絲紗線;或包括多根纖維的繩;或紡絲的短纖紗。紗線可被纏結(jié)和/或加捻。測試方法如通過強(qiáng)度保持測量的促進(jìn)水解穩(wěn)定性使用以下方法進(jìn)行。制備待評價樣品的兩個25米絞絲。一個絞絲吊掛于高壓釜中并用飽和蒸汽在150℃下處理24小時。然后將兩個絞絲在75°F(23.0℃)和55%相對濕度的條件下調(diào)理最少24小時。將各絞絲的樣品在手動加捻機(jī)上加捻至33.7捻度系數(shù)(捻度系數(shù)=轉(zhuǎn)/米x平方根(分特)/100)并根據(jù)描述于ASTMD885中的方法測量斷裂強(qiáng)度。百分比強(qiáng)度保持是通過蒸汽處理紗線的強(qiáng)度除以未處理紗線的強(qiáng)度并乘以100計算的。根據(jù)ASTMD885確定紗線韌度,其是纖維的最大或者斷裂應(yīng)力,表達(dá)為每單元橫截面積上的力,以giga-Pascals(GPa)的形式,或者為每單位質(zhì)量每長度上的力,以克/丹尼爾或克/分特的形式。使用溶液在0.5g/dl的聚合物濃度(C)下并且在25℃的溫度下確定特性粘度,在所述溶液中聚合物被溶解在濃硫酸中,濃度為96重量%。然后以ln(tpoly/tsolv)/C計算特性粘度,其中tpoly是聚合物溶液的滴落時間,并且tsolv是純?nèi)軇┑牡温鋾r間。通過以下方法獲得纖維的含水量,即將纖維樣品第一次稱重,將樣品在300℃的烘箱中放置20分鐘,然后立即對樣品再次稱重。然后通過從初始樣品重量中減去干燥樣品重量然后除以干燥樣品重量乘以100來計算含水量。硫、鈣、鈉、鉀和氯的XRF分析如下進(jìn)行確定。樣品制備:將所述芳族聚酰胺材料通過SPEXX-按壓機(jī)在10T的壓力下用1分鐘壓成13mm直徑的片劑。XRF測量:該測量用PanalyticalAxiosAdvancedX-射線熒光光度計和用于13mm片劑的不銹鋼樣品夾持器進(jìn)行。施用以下裝置設(shè)置:X-射線管:銠檢測器:Ca、K、Cl、Na、S的流通式計數(shù)器過濾器:無準(zhǔn)直器掩模:10mm介質(zhì):真空所述裝置的設(shè)置為如下:定量的原則是基于Na-Kα-、S-Kα-、CI-Kα-、K-Kα-和Ca-Kα-熒光強(qiáng)度與給出校準(zhǔn)線的已知濃度的線性關(guān)系,其中所述校準(zhǔn)線用于確定未知濃度。經(jīng)由滴定的紗線中的酸濃度如下確定。稱出約10克的紗線樣品。將250ml的蒸餾水和紗線加入不銹鋼燒杯中。將150ml的1當(dāng)量濃度NaOH溶液加入燒杯中。(加入的NaOH溶液(ml)≡A)(NaOH溶液的當(dāng)量≡B)。覆蓋燒杯并置于罩內(nèi)的熱板上,使其沸騰15分鐘。然后使液體和紗線冷卻至室溫。將紗線從液體中移除并置于配衡鋁盤中,立即一起稱量紗線樣品和鋁盤的重量。(濕紗線+鍋重量(g)≡C)(鍋重量(g)≡D)然后稱量燒杯中剩余液體的重量。(液體重量≡E)然后將濕紗線樣品在真空爐中干燥過夜,然后將干燥的紗線與鍋一起稱重。(干燥紗線+鍋重量≡F)然后將燒杯中的10克剩余液體置于具有攪拌棒的燒瓶中攪拌。然后向燒瓶中加入三滴溴百里酚藍(lán)指示劑。然后用0.05當(dāng)量濃度的HCl滴定樣品。向樣品中緩慢加入HCl直到指示劑顏色由藍(lán)變綠/黃。(0.05NHCl滴定劑的量≡G)(HCl溶液的當(dāng)量濃度≡H)然后由以下等式計算紗線中酸的百分比:實例給出了許多以下實例以示出本發(fā)明的多種實施例,并且其不應(yīng)被理解為以任何方式限制本發(fā)明的實施例。所有份數(shù)和百分比均按重量計,除非另外指明??偸龉簿畚锿ㄟ^將單體對苯二胺(PPD)、5(6)-氨基-2-(對氨基苯基)苯并咪唑(DAPBI)和對苯二酰二氯(TCL)共聚而制備。DAPBI/PPD/TLC共聚物具有70/30的DAPBI/PPD摩爾比并以20%固體溶解于硫酸中,用類似于對位芳族聚酰胺均聚物使用的干噴濕紡方法紡絲。參見美國專利3,767,756。紗線由九根長絲組成,每根長絲具有約3丹尼爾的標(biāo)稱線密度,長絲共聚物的特性粘度為約4.25dl/g。未洗滌紗線的硫酸含量為如通過滴定測量的約50%。然后將多個50米的樣品纏繞在單個管上以進(jìn)行進(jìn)一步的測試。實例1在~20℃下將在管上的一個未洗滌紗線樣品置于連續(xù)補充溢流的去離子水浴中12小時。然后將管上的紗線樣品與1升在水中的2.0重量%氫氧化鈉(0.5摩爾NaOH/升)接觸放置1小時。然后在~20℃下將紗線樣品置于連續(xù)補充溢流的去離子水浴中1小時。然后從紗線除去多余的液體并將其在管式烘箱中在160℃下干燥。然后在氮氣下在第一烘箱中于300℃和4.5cN/分特下熱處理所述紗線,然后在第二烘箱在450℃和0.15cN/分特下處理。關(guān)于陽離子的大約量及其計算濃度的數(shù)據(jù)在表1中。有效聚合物陽離子與含硫量的摩爾比為約1,并且預(yù)期水解強(qiáng)度保持為約70%。在表中,重量-百分比、份數(shù)-每-百萬份,和摩爾-每-千克均為紗線中的元素的。比較例A和B對于比較例A,在另一個管上的未洗滌紗線樣品上重復(fù)實例1;然而,用0.8重量%的氫氧化鈉水溶液(0.2摩爾NaOH/升)替代2.0重量%的氫氧化鈉水溶液。該降低的堿的濃度提供了對紗線的較小中和力。關(guān)于陽離子的大約量及其計算濃度的數(shù)據(jù)在表1中。有效聚合物陽離子與含硫量的摩爾比為約0.1,并且預(yù)期水解強(qiáng)度保持僅為約40%。對于比較例B,重復(fù)實例A,然而,在用0.8重量%的氫氧化鈉水溶液洗滌后,第二次水洗滌從1小時洗滌增加至8小時洗滌。關(guān)于陽離子的大約量及其計算濃度的數(shù)據(jù)在表1中。有效聚合物陽離子與含硫量的摩爾比小于比較例A(小于約0.1),并且預(yù)期水解強(qiáng)度保持僅為約30%。據(jù)信0.8重量%氫氧化鈉溶液不提供足夠的中和力,處理后的附加洗滌僅簡單地除去了氫氧化鈉,這表明了共聚物中和的緩慢動力學(xué)。表1實例2重復(fù)實例1,然而初始水洗滌從12小時減少至8小時。有效聚合物陽離子與含硫量的摩爾比為約0.5,并且預(yù)期水解強(qiáng)度保持為約55%,小于實例1,這反應(yīng)了第一次水洗滌的影響。實例3重復(fù)實例1,然而初始水洗滌從12小時增加至16小時。有效聚合物陽離子與含硫量的摩爾比為約2,并且預(yù)期水解強(qiáng)度保持為約80%,大于實例1,這反應(yīng)了第一次水洗滌的影響。實例4重復(fù)實例1,然而初始水洗滌從12小時增加至48小時并且使紗線與1.0重量%氫氧化鈉水溶液接觸2小時,相對于實例1中的與2.0重量%氫氧化鈉水溶液接觸1小時。有效聚合物陽離子與含硫量的摩爾比為約2,并且預(yù)期水解強(qiáng)度保持為約80%,大于實例1,這進(jìn)一步反應(yīng)了時間和濃度對最終結(jié)果的影響。表1和2中的結(jié)果圖示于圖2中。表2實例5在連續(xù)方法中如上所述制備紗線,然而每根紗線具有270根長絲,每根長絲具有3旦尼爾的線密度。凝固的紗線連續(xù)地在10個順序洗滌模塊中洗滌,每個洗滌模塊具有一組兩個具有螺旋推進(jìn)套的輥,每個模塊具有20個套。除了模塊8外,所有模塊用~60℃的水洗滌所述紗線。模塊8用2.0重量%的NaOH水溶液洗滌所述紗線。在每個洗滌模塊中的停留時間為約35秒鐘,總洗滌時間為約350秒鐘。然后用銷軸脫水器從紗線去除過量的液體并將紗線在烘箱中的干燥輥上于160℃下干燥。然后在氮氣下在第一烘箱中于300℃和4.5cN/分特下熱處理所述紗線,然后在第二烘箱中在450℃和0.15cN/分特下處理。有效聚合物陽離子與含硫量的摩爾比為約1,并且預(yù)期水解強(qiáng)度保持為約70%。