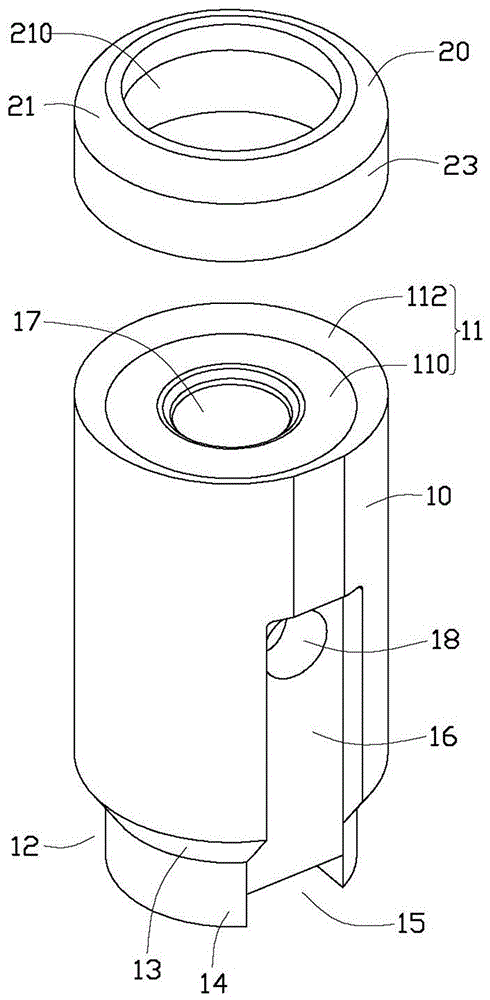
本發(fā)明涉及一種軸承裝置。
背景技術(shù):目前,軸承廣泛應(yīng)用于各種設(shè)備中,尤其是動壓軸承在電子裝置中使用得更加普遍,如硬盤驅(qū)動器(HDD)、光盤驅(qū)動器(CD-ROM)、數(shù)字化視頻光盤機(DVD)、微型光盤機(MiniDisc)、磁光盤機(MO)及散熱風(fēng)扇等領(lǐng)域,這些裝置中馬達(dá)的軸承尺寸小,對軸承的回轉(zhuǎn)精度及壽命的要求高。動壓軸承是在轉(zhuǎn)軸與軸承之間的微小間隙內(nèi)形成一層流體(可為氣體或液體)潤滑油膜,潤滑油通過流經(jīng)不同斷面積的剪力作用而產(chǎn)生一動壓效果,使得該動壓軸承以高剛性對轉(zhuǎn)軸進(jìn)行支承及潤滑,從而使得轉(zhuǎn)軸與軸承不直接接觸,可減少磨損、降低噪音。在動壓軸承中,其承載油膜的形成方式有幾何形狀楔效應(yīng)、擠壓效應(yīng)、表面伸縮效應(yīng)、密度楔效應(yīng)、黏度楔效應(yīng)及膨脹效應(yīng),目前最主要以幾何形狀楔效應(yīng)為主。然而如何保油和注油仍是動壓軸承所面臨的問題。轉(zhuǎn)軸與軸承間的潤滑油在動壓效果引起的各種作用(如毛細(xì)管作用、泵作用)下傾向沿著軸向朝軸承的端部泄露而逸散于大氣中,從而使得該動壓軸承因潤滑油不足而無法正常工作,最后導(dǎo)致該動壓軸承失效;同時,在組裝轉(zhuǎn)軸時,當(dāng)轉(zhuǎn)軸被擠入該動壓軸承內(nèi)孔時,該內(nèi)孔中空氣被壓縮時會產(chǎn)生一巨大反作用力,使得注油及裝配轉(zhuǎn)軸變得困難。業(yè)界通常通過在動壓軸承的內(nèi)周面上開設(shè)儲油槽來解決潤滑油的儲存和泄露問題,然而由于軸承的微型化趨勢使得軸承內(nèi)徑相對地縮小,軸承的中空部分相對狹小,因此在形成該儲油槽時非常地困難,難以提高產(chǎn)品的量產(chǎn)性及穩(wěn)定性。
技術(shù)實現(xiàn)要素:有鑒于此,有必要提供一種可具有較好保油效果的軸承裝置。一種軸承裝置,包括一軸承本體,該軸承本體內(nèi)設(shè)有一用于收容一轉(zhuǎn)軸的軸孔,該轉(zhuǎn)軸與軸承本體之間設(shè)有潤滑流體,該軸承本體的側(cè)面向內(nèi)凹進(jìn)形成一導(dǎo)油槽,所述導(dǎo)油槽由軸承本體的中部向下延伸至軸承本體的底端,該導(dǎo)油槽內(nèi)設(shè)有一與軸孔連通的通孔,所述轉(zhuǎn)軸旋轉(zhuǎn)帶動潤滑流體由軸孔上升而使轉(zhuǎn)軸與軸承本體之間建立動壓,所述轉(zhuǎn)軸與軸承本體之間的部分潤滑流體透過通孔并通過導(dǎo)油槽的導(dǎo)引流到軸承本體的底端,再回流至軸孔的底端而往復(fù)循環(huán)。與現(xiàn)有技術(shù)相比,該軸承裝置的轉(zhuǎn)軸旋轉(zhuǎn)帶動潤滑流體由軸孔上升而使轉(zhuǎn)軸與軸承本體之間建立動壓,所述轉(zhuǎn)軸與軸承本體之間的部分潤滑流體透過通孔并通過導(dǎo)油槽的導(dǎo)引流到軸承本體的底端,再回流至軸孔的底端而往復(fù)循環(huán),從而達(dá)成轉(zhuǎn)軸與軸承本體之間的建立動壓的目的及潤滑流體回流的效果,防止?jié)櫥黧w由軸承裝置的頂端飛濺出去。附圖說明圖1為本發(fā)明軸承裝置第一實施例的立體組裝圖。圖2為圖1所示的軸承裝置的立體分解圖。圖3為圖2所示的軸承裝置的倒置圖。圖4為本發(fā)明軸承裝置具體應(yīng)用時的縱向剖面示意圖。圖5為本發(fā)明軸承裝置具體應(yīng)用時的另一角度的縱向剖面示意圖。圖6為本發(fā)明軸承裝置具體應(yīng)用時的第二實施例的縱向剖面示意圖。主要元件符號說明軸承裝置100軸承本體10上蓋20凹槽11環(huán)槽12導(dǎo)引面13擋壁14開口15導(dǎo)油槽16軸孔17通孔18頂壁21側(cè)壁23導(dǎo)引部25平面110斜面112穿孔210組裝面230軸套30轉(zhuǎn)軸40第一儲油空間50第二儲油空間60如下具體實施方式將結(jié)合上述附圖進(jìn)一步說明本發(fā)明。具體實施方式如圖1所示,該軸承裝置100包括一軸承本體10及設(shè)于該軸承本體10上的一上蓋20。請同時參閱圖2,所述軸承本體10為圓柱狀,其由銅或鐵等金屬粉末射出成型而成。該軸承本體10內(nèi)形成一由其頂面貫穿至底面的軸孔17。該軸承本體10的頂面向內(nèi)凹進(jìn)形成一凹槽11。所述凹槽11包括一平面110及由該平面110的周緣向上延伸形成的斜面112。所述平面110為圓環(huán)形。所述斜面112為環(huán)狀,并由所述平面110的外緣傾斜向上延伸而成。該軸承本體10的底端設(shè)有一圍繞軸承本體10底端的環(huán)槽12。所述軸承本體10于環(huán)槽12的頂端形成一導(dǎo)引面13。所述導(dǎo)引面13由上向下呈漸縮狀延伸。請同時參閱圖3,該軸承本體10的底面周緣的相對兩側(cè)分別向下延伸各形成一擋壁14,并于兩擋壁14的邊端之間分別形成一開口15。該軸承本體10的側(cè)面于靠近其底端位置的相對兩側(cè)分別向內(nèi)凹進(jìn)形成一導(dǎo)油槽16。每一導(dǎo)油槽16對應(yīng)設(shè)于開口15的上方,由軸承本體10的中部向下延伸至貫穿該軸承本體10的底端,并分別與開口15連通。該軸承本體10于右側(cè)的導(dǎo)油槽16內(nèi)形成一與軸孔17連通的通孔18。所述通孔18為圓形,其設(shè)于右側(cè)的導(dǎo)油槽16的頂端。該上蓋20包括一頂壁21及由該頂壁21的周緣向下延伸的圓筒狀的側(cè)壁23。該頂壁21為圓形板狀,其中部設(shè)有一穿孔210。該側(cè)壁23由頂壁21的周緣向下垂直延伸而成,其底端形成一與軸承本體10的斜面112對應(yīng)的組裝面230。該組裝面230的外緣由所述側(cè)壁23向外呈漸縮狀延伸。組裝時,所述上蓋20通過組裝面230預(yù)組裝至軸承本體10的斜面112上,再通過燒結(jié)將上蓋20與軸承本體10固定在一起。請同時參閱圖4及圖5,具體應(yīng)用時,所述軸承裝置100設(shè)置于一軸套30內(nèi),一轉(zhuǎn)軸40穿設(shè)于軸承裝置100的軸孔17內(nèi),并通過所述上蓋20的穿孔210延伸至上蓋20的外側(cè)。所述軸套30包括一底板32及由該底板32的周緣向上延伸形成的一圓筒狀的套筒34。所述軸承本體10的底端抵靠于底板32上,并于所述兩擋壁14的內(nèi)側(cè)與軸承本體10的底面之間合圍成第一儲油空間50,于所述兩擋壁14及環(huán)槽12的外側(cè)與套筒34之間合圍成第二儲油空間60。所述第一儲油空間50、第二儲油空間60及所述軸承本體10與轉(zhuǎn)軸40之間充滿潤滑流體。所述上蓋20擋設(shè)于套筒34的頂端。使用時,所述轉(zhuǎn)軸40轉(zhuǎn)動擠壓潤滑流體,從而于軸承本體10與轉(zhuǎn)軸40之間建立動壓,防止二者之間直接接觸。在所述轉(zhuǎn)軸40轉(zhuǎn)動的過程中,所述第一儲油空間50內(nèi)的潤滑流體上升至轉(zhuǎn)軸40與軸承本體10之間的間隙內(nèi),該轉(zhuǎn)軸40與軸承本體10之間的部分的潤滑流體會透過通孔18并通過導(dǎo)油槽16的導(dǎo)引流到第二儲油空間60內(nèi),再由開口15回流至第一儲油空間50內(nèi),從而達(dá)成轉(zhuǎn)軸40與軸承本體10之間的建立動壓的目的及潤滑流體回流的效果,防止?jié)櫥黧w由軸承裝置100的頂端飛濺出去。所述軸承本體10底端的導(dǎo)引面13擋設(shè)于第二儲油空間60的頂端,可以防止第二儲油空間60內(nèi)的潤滑流體溢至軸承本體10與套筒34的間隙內(nèi),且所述導(dǎo)引面13由上向下的漸縮狀設(shè)計,可以導(dǎo)引流至第二儲油空間60頂端的潤滑流體向下流動,從而加速第一儲油空間50與第二儲油空間60內(nèi)潤滑流體的循環(huán)。所述上蓋20可防止上升到軸承本體10頂端的潤滑流體飛濺至軸承裝置100的外側(cè),從而起到保油的效果。圖6為本發(fā)明軸承裝置具體應(yīng)用時的第二實施例的剖面圖。本實施例與前一實施例的不同之處在于:所述上蓋20于穿孔210的內(nèi)周緣向下延伸形成一導(dǎo)引部25。所述導(dǎo)引部25可單獨通過金屬粉末射出成型后,再通過燒結(jié)的方式與上蓋20相連接。所述導(dǎo)引部25可將上升到軸承本體10頂端的潤滑流體向下導(dǎo)引,從而進(jìn)一步防止上升到軸承本體10頂端的潤滑流體由上蓋20的穿孔210飛濺至軸承裝置100的外側(cè)。具體實施時,所述導(dǎo)油槽16的個數(shù)不限于上述實施例的情況,其可為兩個也可為一個或多個,所述通孔18個數(shù)也不限于上述實施例的情況,其可只設(shè)于一個導(dǎo)油槽16內(nèi),也可于每個導(dǎo)油槽16內(nèi)分別設(shè)有通孔18??梢岳斫獾氖?,對于本領(lǐng)域的普通技術(shù)人員來說,可以根據(jù)本發(fā)明的技術(shù)構(gòu)思做出其它各種像應(yīng)的改變與變形,而所有這些改變與變形都應(yīng)屬于本發(fā)明權(quán)利要求的保護(hù)范圍。