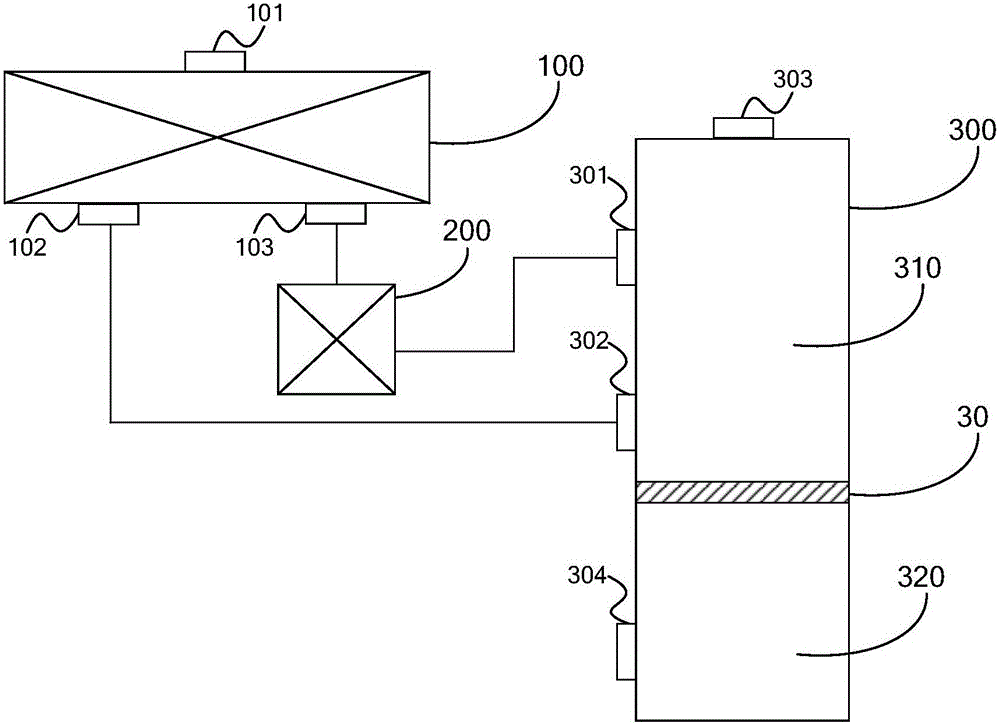
本發(fā)明涉及能源化工領域,具體而言,本發(fā)明涉及處理生物質的系統(tǒng)和方法。
背景技術:
:生物質的熱解是指在惰性氛圍下,通過高溫加熱,使生物質中大分子鍵斷裂,然后發(fā)生一系列解聚、分裂、重整等復雜反應,最終生低聚合度或者小分子化合物的過程。隨著生物質熱解氣化技術研究和應用發(fā)展,熱解焦油的影響已廣受關注,作為熱解過程中的副產(chǎn)品,焦油常溫下呈粘稠狀液態(tài),可引起輸氣管路的堵塞、腐蝕等,對熱解系統(tǒng)及裝置都非常不利。目前用于脫除或者減少熱解氣化產(chǎn)品氣中的焦油含量的方法主要包括濕法、干法、焦油電捕法以及催化裂解。其中,濕式凈化法是用水將可燃氣中的部分焦油帶走,設備主要是噴淋塔。但濕式凈化法液體回收及循環(huán)設備龐大,大量焦油隨水流失,造成能源浪費,凈化效果差。干式凈化法一般為采用多級過濾的方法來把可燃氣中的焦油過濾掉,過濾器中一般填充如活性炭類吸附性較強材料。但是干式凈化系統(tǒng)去除焦油效果并不好,焦油沉積嚴重,且存在系統(tǒng)設備復雜,操作不便及費用過高等缺點。電捕焦油對焦油灰塵粒徑要求較高,且該方法設備造價和運行費用較高。催化裂解作為一種具有潛力的焦油脫除方法,具有高效性和先進性特征,但缺少高效、廉價且適用于商業(yè)化應用的催化劑,制約了該方法的進一步開發(fā)應用。技術實現(xiàn)要素:本發(fā)明旨在至少在一定程度上解決相關技術中的技術問題之一。為此,本發(fā)明的一個目的在于提出處理生物質的系統(tǒng)和方法。該系統(tǒng)可以利用生物質自身熱解產(chǎn)生的熱解炭對熱解氣中的焦油進行催化熱裂解和吸附,從而脫除熱解氣中的焦油,實現(xiàn)熱解氣凈化,該系統(tǒng)組成簡單、易操作,對熱解氣中焦油的脫除率高達80~90%。在本發(fā)明的一個方面,本發(fā)明提出了一種處理生物質的系統(tǒng)。根據(jù)本發(fā)明的實施例,該系統(tǒng)包括:熱解爐,所述熱解爐具有生物質入口、熱解油氣出口和熱解炭出口;螺旋出料機,所述螺旋出料機與所述熱解炭出口相連;吸收塔,所述吸收塔包括由上至下布置的吸收腔室和落料倉,所述吸收腔室和落料倉通過可抽出的卸料板間隔開或者連通,所述吸收腔室的上部具有熱解炭入口,所述吸收腔室的下部具有熱解油氣入口,所述吸收腔室的頂部具有凈化熱解油氣出口,所述熱解炭入口與所述熱解炭出口相連,所述熱解油氣入口與所述熱解油氣出口相連,所述落料倉具有吸收后熱解炭出口。由此,根據(jù)本發(fā)明實施例的處理生物質的系統(tǒng)通過采用熱解爐將生物質進行熱解處理,得到混有焦油的熱解油氣和熱解炭,將熱解油氣和熱解炭分別通入吸收塔的吸收腔室內,使二者在吸收腔室內進行逆向接觸,從而利用熱解炭作為催化劑催化熱裂解熱解油氣中的焦油,同時吸附裂解后產(chǎn)生的小分子氣體,從而減少了熱解油氣冷凝時焦油的產(chǎn)生量,降低熱解油氣氣液分離的能耗。進一步地,通過抽出吸收腔室與落料倉之間的卸料板,使吸附焦油達到飽和的熱解炭落入落料倉,而經(jīng)過凈化的熱解油氣從吸收腔室頂部排出。該系統(tǒng)利用生物質熱解自身產(chǎn)生的熱解炭作為催化劑對熱解油氣進行凈化,從而降低了熱解油氣凈化成本,且該系統(tǒng)組成簡單,易操作,對熱解氣中焦油的脫除率高達80~90%。另外,根據(jù)本發(fā)明上述實施例的處理生物質的系統(tǒng)還可以具有如下附加的技術特征:在本發(fā)明的一些實施例中,所述吸收腔室上部側壁上設置有第一減壓閥,所述落料倉上部側壁上設置有第二減壓閥。由此,可以有效地對所述吸收腔室和所述落料倉內的壓力進行調節(jié)。在本發(fā)明的一些實施例中,所述處理生物質的系統(tǒng)進一步包括:氣體冷凝器,所述氣體冷凝器具有凈化熱解油氣入口、熱解氣出口、油水出口,所述凈化熱解油氣入口與所述凈化熱解油氣出口相連;熱解氣罐,所述熱解氣罐與所述熱解氣出口相連;油水回收罐,所述油水回收罐與所述油水出口相連。由此,可以有效地分離所述凈化熱解油氣中剩余焦油。在本發(fā)明的一些實施例中,所述處理生物質的系統(tǒng)進一步包括:固體冷卻器,所述固體冷卻器具有吸收后熱解炭入口和熱解炭產(chǎn)品出口,所述吸收后熱解炭入口與所述吸收后熱解炭出口相連;熱解炭儲倉,所述熱解炭儲倉與所述熱解炭產(chǎn)品出口相連。由此,可以有效地將所述吸收后熱解炭進行冷凝并收集。在本發(fā)明的一些實施例中,所述吸收塔的外表面包裹有石棉類保溫層。由此,可以顯著降低熱解氣凈化過程中的熱量損失。在本發(fā)明的第二方面,本發(fā)明提出了一種采用本發(fā)明上述實施例的處理生物質的系統(tǒng)實施處理生物質的方法。根據(jù)本發(fā)明的實施例,該方法包括:將生物質供給至熱解爐內進行熱解處理,以便得到熱解油氣和熱解炭;將熱解炭從所述吸收腔室的上部加入,將所述熱解油氣從所述吸收腔室的下部通入,使所述熱解油氣與所述熱解炭在所述吸收腔室內逆向接觸,完成熱解氣的凈化,得到凈化后熱解油氣和吸收后熱解炭,吸收后熱解炭排至落料倉。由此,根據(jù)本發(fā)明實施例的處理生物質的方法通過采用熱解爐將生物質進行熱解處理,得到混有焦油的熱解油氣和熱解炭,將熱解炭送入吸收塔的吸收腔室,使熱解炭與熱解油氣接觸,利用熱解炭吸附熱解油氣中的焦油,從而實現(xiàn)了熱解氣的凈化,在吸收腔室內,從吸收腔室下部通入的熱解油氣因密度較低而向上運動,與從吸收腔室上部加入的熱解炭逆向接觸,由此熱解油氣與熱解炭之間具有較高的接觸效率,在熱解炭的作用下,焦油被充分裂解和吸附。該方法利用生物質熱解產(chǎn)生的熱解炭對熱解氣進行凈化,操作簡單,成本較低,對熱解氣中焦油的脫除率高達80~90%。另外,根據(jù)本發(fā)明上述實施例的處理生物質的方法還可以具有如下附加的技術特征:在本發(fā)明的一些實施例中,所述處理生物質的方法進一步包括:利用氣體冷凝器對所述凈化后熱解油氣進行氣液分離處理,以便得到熱解氣和油水混合物。在本發(fā)明的一些實施例中,所述處理生物質的方法進一步包括:利用固體冷卻器對所述吸收后熱解炭進行固液分離處理,以便得到熱解炭產(chǎn)品。在本發(fā)明的一些實施例中,所述熱解處理的溫度為700~900攝氏度。由此,可以顯著提高所述熱解處理的效率。在本發(fā)明的一些實施例中,進入所述吸收腔室的熱解炭的溫度為700~800攝氏度,進入所述吸收腔室的熱解油氣的溫度為600~800攝氏度。由此,可以顯著提高熱解炭對熱解氣的凈化效率。在本發(fā)明的一些實施例中,所述熱解油氣與所述熱解炭接觸并發(fā)生裂解和凈化的溫度為600~800攝氏度。由此,可以進一步提高熱解炭對熱解氣的凈化效率。本發(fā)明的附加方面和優(yōu)點將在下面的描述中部分給出,部分將從下面的描述中變得明顯,或通過本發(fā)明的實踐了解到。附圖說明本發(fā)明的上述和/或附加的方面和優(yōu)點從結合下面附圖對實施例的描述中將變得明顯和容易理解,其中:圖1是根據(jù)本發(fā)明一個實施例的處理生物質的系統(tǒng)結構示意圖;圖2是根據(jù)本發(fā)明再一個實施例的處理生物質的系統(tǒng)結構示意圖;圖3是根據(jù)本發(fā)明一個實施例的處理生物質的方法流程示意圖;圖4是根據(jù)本發(fā)明再一個實施例的處理生物質的方法流程示意圖;圖5是根據(jù)本發(fā)明又一個實施例的處理生物質的系統(tǒng)結構示意圖。具體實施方式下面詳細描述本發(fā)明的實施例,所述實施例的示例在附圖中示出,其中自始至終相同或類似的標號表示相同或類似的元件或具有相同或類似功能的元件。下面通過參考附圖描述的實施例是示例性的,旨在用于解釋本發(fā)明,而不能理解為對本發(fā)明的限制。在本發(fā)明的描述中,需要理解的是,術語“上”、“下”、“頂”、“底”等指示的方位或位置關系為基于附圖所示的方位或位置關系,僅是為了便于描述本發(fā)明和簡化描述,而不是指示或暗示所指的裝置或元件必須具有特定的方位、以特定的方位構造和操作,因此不能理解為對本發(fā)明的限制。此外,術語“第一”、“第二”僅用于描述目的,而不能理解為指示或暗示相對重要性或者隱含指明所指示的技術特征的數(shù)量。由此,限定有“第一”、“第二”的特征可以明示或者隱含地包括至少一個該特征。在本發(fā)明中,除非另有明確的規(guī)定和限定,術語“相連”應做廣義理解,例如,可以是固定連接,也可以是可拆卸連接,或成一體;可以是機械連接,也可以是電連接;可以是直接相連,也可以通過中間媒介間接相連,可以是兩個元件內部的連通或兩個元件的相互作用關系,除非另有明確的限定。對于本領域的普通技術人員而言,可以根據(jù)具體情況理解上述術語在本發(fā)明中的具體含義。在本發(fā)明的一個方面,本發(fā)明提出了一種處理生物質的系統(tǒng)。根據(jù)本發(fā)明的實施例,該系統(tǒng)包括:熱解爐100、螺旋出料機200和吸收塔300。其中,熱解爐100具有生物質入口101、熱解油氣出口102和熱解炭出口103;螺旋出料機200與熱解炭出口103相連;吸收塔300包括由上至下布置的吸收腔室310和落料倉320,收腔室310和落料倉320通過可抽出的卸料板30間隔開或者連通,吸收腔室310的上部具有熱解炭入口301,吸收腔室310的下部具有熱解油氣入口302,吸收腔室310的頂部具有凈化熱解油氣出口303,熱解炭入口301與熱解炭出口103相連,熱解油氣入口302與熱解油氣出口102相連,落料倉320具有吸收后熱解炭出口304。下面參考圖1和圖2對根據(jù)本發(fā)明實施例的處理生物質的系統(tǒng)進行詳細描述:根據(jù)本發(fā)明的實施例,熱解爐100具有生物質入口101、熱解油氣出口102和熱解炭出口103,熱解爐100適于對生物質進行熱解處理,以便得到熱解油氣和熱解炭。根據(jù)本發(fā)明的實施例,生物質的主要成分包括水分、揮發(fā)分、灰分以及固定碳,具有較高的能源利用價值。通過將生物質在惰性氛圍下高溫加熱,可以得到熱解油氣和熱解炭,熱解油氣中混有焦油,有待進一步進行凈化處理。根據(jù)本發(fā)明的實施例,螺旋出料機200與熱解炭出口103相連,螺旋出料機200適于將生物質熱解得到的熱解炭供給至吸收塔300。根據(jù)本發(fā)明的實施例,吸收塔300包括由上至下布置的吸收腔室310和落料倉320,收腔室310和落料倉320通過可抽出的卸料板30間隔開或者連通,吸收腔室310的上部具有熱解炭入口301,吸收腔室310的下部具有熱解油氣入口302,吸收腔室310的頂部具有凈化熱解油氣出口303,熱解炭入口301與熱解炭出口103相連,熱解油氣入口302與熱解油氣出口102相連,落料倉320具有吸收后熱解炭出口304,吸收塔300適于使熱解油氣與熱解炭接觸,以便完成的熱解氣的凈化。根據(jù)本發(fā)明的實施例,吸收塔300的外表面包裹有石棉類保溫層。由此,可以顯著降低熱解油氣凈化過程中的熱量損失。根據(jù)本發(fā)明的實施例,熱解炭從吸收腔室310上部的熱解炭入口301進入吸收腔室,熱解油氣從吸收腔室310下部的熱解油氣入口302進入吸收腔室,在吸收腔室中,密度較低的熱解油氣向上運動,與熱解炭逆向接觸,高溫的熱解炭催化熱解氣中的大分子碳氫化合物發(fā)生二次裂解,裂解為輕質小分子氣體,如CO、CH4或H2,同時,熱解炭具有發(fā)達的孔隙結構和大比表面積等特征,還可以對焦油產(chǎn)生吸附作用。由此利用熱解炭對熱解氣中焦油的進行催化熱裂解和吸附,可使得焦油的脫除率高達80~90%。根據(jù)本發(fā)明的實施例,熱解炭與熱解油氣在吸收腔室310內接觸10~20min后,抽出吸收腔室和落料倉320之間的卸料板30,使吸收腔室310中已吸附焦油飽和的熱解炭在自身重力作用下落至落料倉320,與此同時,通過螺旋出料機200將新熱解炭及時補充到吸收腔室310中,待吸收腔室310中的熱解炭更新完畢后,將卸料板30關閉,通過新熱解炭對熱解油氣進行下一輪凈化。參考圖2,根據(jù)本發(fā)明實施例的處理生物質的系統(tǒng)進一步包括:第一減壓閥31、第二減壓閥32。根據(jù)本發(fā)明的實施例,吸收腔室310上部側壁上設置有第一減壓閥31,落料倉320上部側壁上設置有第二減壓閥32。由此,可以及時有效地對吸收腔室310和落料倉320中的壓力進行平衡。參考圖2,根據(jù)本發(fā)明實施例的處理生物質的系統(tǒng)進一步包括:氣體冷凝器400、熱解氣罐500和油水回收罐600。根據(jù)本發(fā)明的實施例,氣體冷凝器400具有凈化熱解油氣入口401、熱解氣出口402和油水出口403,凈化熱解油氣入口401與凈化熱解油氣出口303相連,氣體冷凝器400適于對凈化后的熱解油氣進行氣液分離處理,以便得到熱解氣和油水混合物。根據(jù)本發(fā)明的實施例,通過利用生物質自身熱解產(chǎn)生的熱解炭對熱解油氣進行凈化處理,可以有效脫除熱解油氣中的80~90%的焦油。進而可以有效降低氣體冷凝器400分離熱解油氣中焦油的能耗,提高分離效率。具體地,氣體冷凝器400可以將熱解油氣冷卻至20~30攝氏度,從而使熱解油氣中的油水冷凝為液態(tài),使熱解氣與油水分離。根據(jù)本發(fā)明的實施例,熱解氣罐500與熱解氣出口402相連,且適于將經(jīng)過氣液分離處理的潔凈熱解氣進行儲存。根據(jù)本發(fā)明的實施例,油水回收罐600與油水出口403相連,且適于將從熱解油氣中冷凝得到的油水進行回收。參考圖2,根據(jù)本發(fā)明實施例的處理生物質的系統(tǒng)進一步包括:固體冷卻器700和熱解炭儲倉800。根據(jù)本發(fā)明的實施例,固體冷卻器700具有吸收后熱解炭入口701和熱解炭產(chǎn)品出口702,吸收后熱解炭入口701與吸收后熱解炭出口304相連,固體冷卻器700適于對落料倉320中收集得到的吸收焦油后的熱解炭進行冷凝處理,以便得到熱解炭產(chǎn)品。根據(jù)本發(fā)明的實施例,熱解炭儲倉800與熱解炭產(chǎn)品出口702相連,且適于對經(jīng)過冷凝處理得到的熱解炭進行儲存。由此,根據(jù)本發(fā)明實施例的處理生物質的系統(tǒng)通過采用熱解爐將生物質進行熱解處理,得到混有焦油的熱解油氣和熱解炭,將熱解油氣和熱解炭分別通入吸收塔的吸收腔室內,使二者在吸收腔室內進行逆向接觸,從而利用熱解炭作為催化劑催化熱裂解熱解油氣中的焦油,同時吸附裂解后產(chǎn)生的小分子氣體,從而減少了熱解油氣冷凝時焦油的產(chǎn)生量,降低熱解油氣氣液分離的能耗。進一步地,通過抽出吸收腔室與落料倉之間的卸料板,使吸附焦油達到飽和的熱解炭落入落料倉,而經(jīng)過凈化的熱解油氣從吸收腔室頂部排出。該系統(tǒng)利用生物質熱解自身產(chǎn)生的熱解炭作為催化劑對熱解油氣進行凈化,從而降低了熱解油氣凈化成本,且該系統(tǒng)組成簡單,易操作,對熱解氣中焦油的脫除率高達80~90%。在本發(fā)明的第二方面,本發(fā)明提出了一種采用本發(fā)明上述實施例的處理生物質的系統(tǒng)實施處理生物質的方法。根據(jù)本發(fā)明的實施例,該方法包括:將生物質供給至熱解爐內進行熱解處理,以便得到熱解油氣和熱解炭;將熱解炭從所述吸收腔室的上部加入,將所述熱解油氣從所述吸收腔室的下部通入,使所述熱解油氣與所述熱解炭在所述吸收腔室內逆向接觸,完成熱解氣的凈化,得到凈化后熱解油氣和吸收后熱解炭,吸收后熱解炭排至落料倉。下面對根據(jù)本發(fā)明實施例的處理生物質的方法進行詳細描述,參考圖3和圖4,該方法包括:S100:熱解處理該步驟中,將生物質供給至熱解爐內進行熱解處理,以便得到熱解油氣和熱解炭。根據(jù)本發(fā)明的實施例,生物質的主要成分包括水分、揮發(fā)分、灰分以及固定碳,具有較高的能源利用價值。通過將生物質在惰性氛圍下高溫加熱,可以得到熱解油氣和熱解炭,熱解油氣中混有焦油,有待進一步進行凈化處理。根據(jù)本發(fā)明的實施例,熱解處理的溫度并不受特別限制,本領域技術人員可以根據(jù)實際需要進行選擇,根據(jù)本發(fā)明的具體實施例,熱解處理的溫度可以為700~900攝氏度。發(fā)明人通過大量實驗發(fā)現(xiàn),如果熱解溫度過低,則無法有效地將生物質熱解為小分子氣體化合物,且得到的熱解產(chǎn)物中焦油含量較大,難以利用;而如果熱解溫度過高,則會使能耗增大。S200:凈化處理該步驟中,將熱解炭從吸收腔室的上部加入,將熱解油氣從吸收腔室的下部通入,使熱解油氣與熱解炭在吸收腔室內逆向接觸,完成熱解氣的凈化,得到凈化后熱解油氣和吸收后熱解炭。具體地,根據(jù)本發(fā)明的實施例,可以采用螺旋出料機將熱解炭供給至吸收腔室。在吸收腔室中,密度較低的熱解油氣向上運動,與熱解炭逆向接觸,高溫的熱解炭催化熱解氣中的大分子碳氫化合物發(fā)生二次裂解,裂解為輕質小分子氣體,如CO、CH4或H2,同時,熱解炭具有發(fā)達的孔隙結構和大比表面積等特征,還可以對焦油產(chǎn)生吸附作用。由此利用熱解炭對熱解氣中焦油的進行催化熱裂解和吸附,可使得焦油的脫除率高達80~90%。根據(jù)本發(fā)明的具體實施例,吸收腔室內的熱解炭的溫度可以為700~800攝氏度,進入吸收腔室的熱解油氣的溫度可以為600~800攝氏度。發(fā)明人發(fā)現(xiàn),將溫度略高的熱解炭與熱解油氣逆向接觸,熱解炭可以發(fā)揮催化作用,有效地催化熱裂解熱解油氣中的焦油,從而有效脫除熱解油氣中的大部分焦油,達到凈化熱解氣的目的。根據(jù)本發(fā)明的具體實施例,熱解油氣與熱解炭接觸并發(fā)生裂解和凈化的溫度為600~800攝氏度。由此,可以使熱解炭對熱解油氣中焦油的吸附效率和裂解效率最佳。根據(jù)本發(fā)明的實施例,熱解炭與熱解油氣在吸收腔室內接觸10~20min后,抽出吸收腔室和落料倉之間的卸料板,使吸收腔室中已吸附焦油飽和的熱解炭在自身重力作用下落至落料倉,與此同時,通過螺旋出料機將新熱解炭及時補充道吸收腔室中,待吸收腔室中的熱解炭更新完畢后,將卸料板關閉,通過新熱解炭對熱解油氣進行下一輪凈化。根據(jù)本發(fā)明的實施例,吸收腔室上部側壁上設置有第一減壓閥,落料倉上部側壁上設置有第二減壓閥。由此,可以及時有效地對吸收腔室和落料倉中的壓力進行平衡。S310:氣液分離處理該步驟中,利用氣體冷凝器對S300中得到的凈化后熱解油氣進行氣液分離處理,以便得到熱解氣和油水混合物。根據(jù)本發(fā)明的實施例,通過利用生物質自身熱解產(chǎn)生的熱解炭對熱解油氣進行凈化處理,可以有效脫除熱解油氣中的80~90%的焦油。進而可以有效降低氣體冷凝器400分離熱解油氣中焦油的能耗,提高分離效率。具體地,氣體冷凝器400可以將熱解油氣冷卻至20~30攝氏度,從而使熱解油氣中的油水冷凝為液態(tài),使熱解氣與油水分離,進一步地,可以將熱解氣送入熱解氣罐儲存,將油水混合物送入油水回收罐儲存。S320:固液分離處理該步驟中,利用固體冷卻器對S300中得到的吸收焦油后的熱解炭進行固液分離處理,除去其中的焦油等液體,以便得到熱解炭產(chǎn)品,進一步地,可以將得到的熱解炭產(chǎn)品送入熱解炭儲倉儲存。由此,根據(jù)本發(fā)明實施例的處理生物質的方法通過采用熱解爐將生物質進行熱解處理,得到混有焦油的熱解油氣和熱解炭,將熱解炭送入吸收塔的吸收腔室,使熱解炭與熱解油氣接觸,利用熱解炭吸附熱解油氣中的焦油,從而實現(xiàn)了熱解氣的凈化,在吸收腔室內,從吸收腔室下部通入的熱解油氣因密度較低而向上運動,與從吸收腔室上部加入的熱解炭逆向接觸,由此熱解油氣與熱解炭之間具有較高的接觸效率,在熱解炭的作用下,焦油被充分裂解和吸附。該方法利用生物質熱解產(chǎn)生的熱解炭對熱解氣進行凈化,操作簡單,成本較低,對熱解氣中焦油的脫除率高達80~90%。下面參考具體實施例,對本發(fā)明進行描述,需要說明的是,這些實施例僅僅是描述性的,而不以任何方式限制本發(fā)明。實施例參考圖5,對玉米秸稈進行熱解處理,其中玉米秸稈的工業(yè)分析見表1:表1玉米秸稈的工業(yè)分析(wt%)水分揮發(fā)分灰分固定碳玉米秸稈6.7%60.9%23.6%8.8%熱解爐設定的熱解溫度為800℃,熱解時間為60min。熱解產(chǎn)物主要為高溫熱解油氣和高溫熱解炭。熱解爐頂部熱解油氣出口溫度為600~800℃,熱解爐底部熱解炭出口溫度為700~800℃。將熱解炭和熱解油氣供給至吸收塔的吸收腔室,將熱解炭從吸收腔室的上部加入,將熱解油氣從吸收腔室的下部通入,待熱解炭體積達到吸附塔吸收腔室容積的2/3時,停止加入熱解炭,進而使熱解油氣與熱解炭在吸收腔室內逆向接觸,凈化進行15min后,打開吸收腔室和落料倉之間的卸料板,使已吸附飽和的熱解炭在自身重力作用下落至位于其下方的落料倉,與此同時,通過螺旋出料機將熱解爐中的新熱解炭及時補充到吸附塔吸收腔室,待吸附塔吸收腔室內熱解炭更新完畢后,停止加入熱解炭,熱解氣進入下一個吸附凈化循環(huán)。得到的經(jīng)過凈化的熱解油氣中焦油的脫除率達到80~90%。將凈化后的熱解油氣(500~600℃)進行冷凝處理,使熱解油氣降溫至20~30℃,同時熱解油氣中的油水混合物冷凝,將油水混合物送至油水回收罐。將已吸附飽和的熱解炭(500~600℃)水冷至不高于50℃,同時除去其中吸附的焦油等液體,得到的低溫熱解炭產(chǎn)品送入熱解炭儲倉。在本說明書的描述中,參考術語“一個實施例”、“一些實施例”、“示例”、“具體示例”、或“一些示例”等的描述意指結合該實施例或示例描述的具體特征、結構、材料或者特點包含于本發(fā)明的至少一個實施例或示例中。在本說明書中,對上述術語的示意性表述不必須針對的是相同的實施例或示例。而且,描述的具體特征、結構、材料或者特點可以在任一個或多個實施例或示例中以合適的方式結合。此外,在不相互矛盾的情況下,本領域的技術人員可以將本說明書中描述的不同實施例或示例以及不同實施例或示例的特征進行結合和組合。盡管上面已經(jīng)示出和描述了本發(fā)明的實施例,可以理解的是,上述實施例是示例性的,不能理解為對本發(fā)明的限制,本領域的普通技術人員在本發(fā)明的范圍內可以對上述實施例進行變化、修改、替換和變型。當前第1頁1 2 3