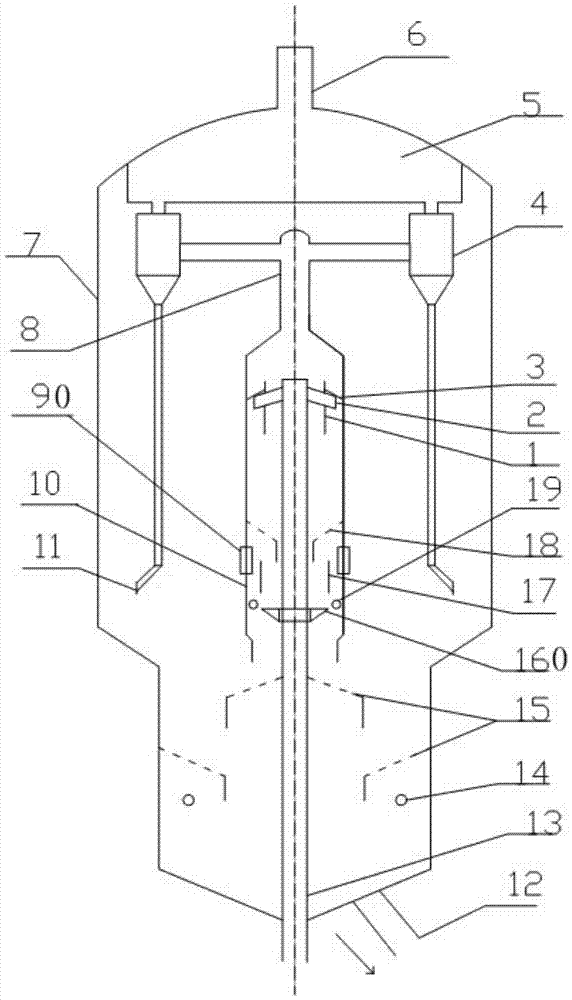
本發(fā)明涉及石油化工技術(shù)領(lǐng)域,具體涉及流化催化裂化技術(shù)領(lǐng)域,特別是流化催化裂化設(shè)備中催化裂化提升管出口氣固快速分離和帶有密相環(huán)流預(yù)汽提段的提升管出口快分系統(tǒng),即一種催化裂化提升管出口的快分設(shè)備。
背景技術(shù):煉油化工的催化裂化裝置提升管出口一般都有氣固快速分離裝置以實(shí)現(xiàn)催化劑與油氣的快速分離、油氣的快速引出,終止不必要的反應(yīng),提高目的產(chǎn)品收率,降低生產(chǎn)成本,增加效益。此外還需將快分裝置分離下來的催化劑進(jìn)行快速的預(yù)汽提以回收催化劑夾帶的部分油氣和減輕沉降器內(nèi)的結(jié)焦目前,國內(nèi)外應(yīng)用較多的帶有預(yù)汽提結(jié)構(gòu)的提升管出口快分系統(tǒng)主要有美國UOP公司開發(fā)的VDS(美國專利US5,314,611)系統(tǒng)和VSS(美國專利US4,482,451)系統(tǒng),國內(nèi)中國石油大學(xué)(北京)開發(fā)的FSC系統(tǒng)(中國專利ZL96103419.X)、VQS系統(tǒng)(中國專利ZL96103478.5、ZL96103420.3、ZL01228805.5)、CSC系統(tǒng)(中國專利ZL98102166.2、ZL98204681.2)和SVQS系統(tǒng)(中國專利ZL02159408.2)。以上技術(shù)雖然各有優(yōu)點(diǎn),但也均存在一些不足之處:例如,CSC系統(tǒng)中,油氣和催化劑的分離效率低、系統(tǒng)占用空間大、結(jié)焦嚴(yán)重。綜上所述,現(xiàn)有技術(shù)中至少存在以下問題:現(xiàn)有的催化裂化提升管出口的快分設(shè)備油氣和催化劑的分離效率低、系統(tǒng)占用空間大、結(jié)焦嚴(yán)重。
技術(shù)實(shí)現(xiàn)要素:本發(fā)明提供一種催化裂化提升管出口的快分設(shè)備,以解決現(xiàn)有的催化裂化提升管出口的快分設(shè)備油氣和催化劑的分離效率低、系統(tǒng)占用空間大、結(jié)焦嚴(yán)重的問題。為此,本發(fā)明提出一種催化裂化提升管出口的快分設(shè)備,所述催化裂化提升管出口的快分設(shè)備包括:反應(yīng)器外殼;提升管,伸入到所述反應(yīng)器外殼中;旋流快分頭,設(shè)置在所述反應(yīng)器外殼中并連接在所述提升管的頂端;氣固密相環(huán)流預(yù)汽提器,設(shè)置在所述反應(yīng)器外殼中,所述氣固密相環(huán)流預(yù)汽提器連接在所述旋流快分頭的下方,并且所述氣固密相環(huán)流預(yù)汽提器套設(shè)在所述提升管之外;從所述提升管出口的出來的油氣和催化劑首先由旋流快分頭進(jìn)行分離并將油氣快速引出,分離的催化劑再經(jīng)氣固密相環(huán)流預(yù)汽提器進(jìn)行汽提。進(jìn)一步地,所述催化裂化提升管出口的快分設(shè)備還包括:分流筒和分流擋板,所述分流筒連接在所述旋流快分頭之下并且套設(shè)在所述提升管上,所述分流擋板位于所述旋流快分頭之上并且沿所述提升管的徑向斜向下延伸。進(jìn)一步地,所述氣固密相環(huán)流預(yù)汽提器還包括:容納所述氣固密相環(huán)流預(yù)汽提器的封閉罩,設(shè)置在反應(yīng)器外殼中。進(jìn)一步地,所述氣固密相環(huán)流預(yù)汽提器包括:依次連接在所述旋流快分頭之下的下料汽提擋板、環(huán)流筒、和內(nèi)環(huán)汽提蒸氣分布板,所述環(huán)流筒套設(shè)在所述提升管上。進(jìn)一步地,所述氣固密相環(huán)流預(yù)汽提器包括:依次連接在所述旋流快分頭之下的下料汽提擋板、環(huán)流筒、和內(nèi)環(huán)汽提蒸氣風(fēng)管,所述環(huán)流筒套設(shè)在所述提升管上。進(jìn)一步地,所述催化裂化提升管出口的快分設(shè)備還包括:外環(huán)汽提蒸氣風(fēng)管,設(shè)置在所述封閉罩之內(nèi),并位于所述環(huán)流筒之外。進(jìn)一步地,所述催化裂化提升管出口的快分設(shè)備還包括:連接在所述封閉罩頂部的平衡管,設(shè)置在反應(yīng)器外殼中,所述平衡管的數(shù)目為多個,對稱設(shè)置。進(jìn)一步地,所述催化裂化提升管出口的快分設(shè)備還包括:連接在各所述平衡管頂部的導(dǎo)流管,所述導(dǎo)流管豎直設(shè)置。進(jìn)一步地,所述下料汽提擋板的形狀為錐形,所述下料汽提擋板上開有多個圓孔,開孔孔徑為φ10~φ35mm,開孔率為5%~15%。進(jìn)一步地,所述下料汽提擋板下方串聯(lián)設(shè)置多個所述環(huán)流筒。本發(fā)明的目的是提供一種能實(shí)現(xiàn)油氣和催化劑的高效快速分離、油氣的快速引出及催化劑的高效預(yù)汽提快分系統(tǒng),而且還能有效降低快分系統(tǒng)的占用空間,減小沉降器的體積,降低沉降器內(nèi)的結(jié)焦場所。本發(fā)明的催化裂化提升管出口快分系統(tǒng)的上部為SVQS系統(tǒng)采用的帶分流筒和分流擋板的旋流快分頭,下部為可實(shí)現(xiàn)催化劑高效預(yù)汽提的氣固密相環(huán)流預(yù)汽提器。提升管出口的油氣和催化劑首先由旋流快分頭進(jìn)行分離并將油氣快速引出,分離的催化劑再經(jīng)氣固密相環(huán)流預(yù)汽提器進(jìn)行高效汽提。本發(fā)明,既能實(shí)現(xiàn)油氣和催化劑的高效快速分離、油氣的快速引出及催化劑的高效預(yù)汽提,又能有效降低設(shè)備的占用空間,減小沉降器體積,降低沉降器內(nèi)的結(jié)焦場所。附圖說明圖1為本發(fā)明第一實(shí)施例的催化裂化提升管出口的快分設(shè)備的內(nèi)部結(jié)構(gòu)示意圖;圖2為本發(fā)明第二實(shí)施例的催化裂化提升管出口的快分設(shè)備的內(nèi)部結(jié)構(gòu)示意圖;圖3為本發(fā)明第三實(shí)施例的催化裂化提升管出口的快分設(shè)備的內(nèi)部結(jié)構(gòu)示意圖;圖4為本發(fā)明第四實(shí)施例的催化裂化提升管出口的快分設(shè)備的內(nèi)部結(jié)構(gòu)示意圖。附圖標(biāo)號說明:1分流筒2旋流快分頭3分流擋板4頂旋5沉降器頂部集氣室6反應(yīng)器引出管7反應(yīng)器外殼8導(dǎo)流管9平衡管10封閉罩11翼閥12待生斜管13提升管14汽提蒸氣風(fēng)管15擋板16內(nèi)環(huán)汽提蒸氣風(fēng)管17環(huán)流筒18下料汽提擋板19外環(huán)汽提蒸氣風(fēng)管90槽孔160內(nèi)環(huán)汽提蒸氣分布板具體實(shí)施方式為了對本發(fā)明的技術(shù)特征、目的和效果有更加清楚的理解,現(xiàn)對照附圖說明本發(fā)明。圖1、圖2、圖3和圖4提供了四種實(shí)施例的催化裂化提升管出口的快分設(shè)備(簡稱快分設(shè)備),這四種實(shí)施例的快分設(shè)備的總體設(shè)計(jì)原理和工作原理相同,只是在具體部件的設(shè)置上有所不同。如圖1至圖4所示,本發(fā)明的催化裂化提升管出口的快分設(shè)備都包括:反應(yīng)器外殼7,具有中空的腔體,容納快分設(shè)備中的各種部件;提升管13,從反應(yīng)器外殼7的底部伸入到所述反應(yīng)器外殼7中;旋流快分頭2,設(shè)置在所述反應(yīng)器外殼7中并連接在所述提升管13的頂端;氣固密相環(huán)流預(yù)汽提器,設(shè)置在所述反應(yīng)器外殼7中,所述氣固密相環(huán)流預(yù)汽提器連接在所述旋流快分頭的下方,并且所述氣固密相環(huán)流預(yù)汽提器套設(shè)在所述提升管13之外;從所述提升管13出口的出來的油氣和催化劑首先由旋流快分頭2進(jìn)行分離并將油氣快速引出,分離的催化劑再經(jīng)氣固密相環(huán)流預(yù)汽提器進(jìn)行汽提。進(jìn)一步地,如圖1至圖4所示,所述催化裂化提升管出口的快分設(shè)備還包括:分流筒1和分流擋板3,所述分流筒1連接在所述旋流快分頭2之下并且套設(shè)在所述提升管13上,所述分流擋板1位于所述旋流快分頭2之上并且沿所述提升管的徑向斜向下延伸。也就是,本發(fā)明的催化裂化提升管出口快分系統(tǒng)的上部為SVQS系統(tǒng)采用的帶分流筒和分流擋板的旋流快分頭,這樣,能實(shí)現(xiàn)油氣和催化劑的高效快速分離,能有效降低設(shè)備的占用空間,減小沉降器體積,降低沉降器內(nèi)的結(jié)焦場所。進(jìn)一步地,如圖1至圖4所示,所述氣固密相環(huán)流預(yù)汽提器還包括:容納所述氣固密相環(huán)流預(yù)汽提器的封閉罩10,設(shè)置在反應(yīng)器外殼7中,以實(shí)現(xiàn)油氣和催化劑的高效快速分離。氣固密相環(huán)流預(yù)汽提器為可實(shí)現(xiàn)催化劑高效預(yù)汽提的氣固密相環(huán)流預(yù)汽提器。進(jìn)一步地,如圖2至圖3所示,所述氣固密相環(huán)流預(yù)汽提器包括:依次連接在所述旋流快分頭之下的下料汽提擋板18、環(huán)流筒17、和內(nèi)環(huán)汽提蒸氣分布板160,所述環(huán)流筒17套設(shè)在所述提升管13上。采用內(nèi)環(huán)汽提蒸氣分布板160,有利于合理增大環(huán)流預(yù)汽提器內(nèi)氣固環(huán)流的空間,提高汽提效果。進(jìn)一步地,如圖1和圖4所示,所述氣固密相環(huán)流預(yù)汽提器包括:依次連接在所述旋流快分頭之下的下料汽提擋板18、環(huán)流筒17、和內(nèi)環(huán)汽提蒸氣風(fēng)管16,所述環(huán)流筒17套設(shè)在所述提升管13上。采用內(nèi)環(huán)汽提蒸氣風(fēng)管16,便于制作安裝。如圖2所示,所述催化裂化提升管出口的快分設(shè)備還包括:外環(huán)汽提蒸氣風(fēng)管19,設(shè)置在所述封閉罩10之內(nèi),并位于所述環(huán)流筒17之外,提高汽提效果。進(jìn)一步地,如圖1至圖4所示,所述催化裂化提升管出口的快分設(shè)備還包括:汽提蒸氣風(fēng)管14,設(shè)置在所述封閉罩10之外,并位于所述氣固密相環(huán)流預(yù)汽提器之下。進(jìn)一步地,如圖1至圖4所示,所述催化裂化提升管出口的快分設(shè)備還包括:連接在所述封閉罩10頂部的平衡管9,設(shè)置在反應(yīng)器外殼中,所述平衡管9的數(shù)目為多個,對稱設(shè)置,以利于油氣和催化劑的高效快速和均衡的分離。例如,平衡管9的數(shù)目為兩個,對稱設(shè)置在提升管13的兩側(cè)。進(jìn)一步地,所述催化裂化提升管出口的快分設(shè)備還包括:連接在各所述平衡管9頂部的導(dǎo)流管8,所述導(dǎo)流管8豎直設(shè)置。導(dǎo)流管8連接封閉罩10。進(jìn)一步地,如圖1、圖2和圖3所示,所述下料汽提擋板18的形狀為錐形,錐形下料板的作用:1、對旋流快分分離的催化劑進(jìn)行初步汽提,同時將初步汽提后的催化劑引入環(huán)流預(yù)汽提段的中心區(qū)域。2、具有整流作用,即將封閉罩內(nèi)催化劑的旋流流動轉(zhuǎn)化為順重力流動,從而利于進(jìn)行汽提過程。所述下料汽提擋板上開有多個圓孔,開孔孔徑為φ10~φ35mm,開孔率為5%~15%。在該開孔范圍內(nèi),系統(tǒng)的壓降最小、催化劑的汽提效率最高,同時能使系統(tǒng)下料順暢并進(jìn)入環(huán)流預(yù)汽提段的中心區(qū)域。進(jìn)一步地,所述下料汽提擋板下方串聯(lián)設(shè)置多個所述環(huán)流筒,以提高快速分離效果。進(jìn)一步地,旋流快分頭的旋流臂外側(cè)距封閉罩內(nèi)壁5~50mm,其頂部環(huán)形分流擋板與封閉罩內(nèi)壁的間隙2~5mm,分流筒與提升管外壁形成的環(huán)形截面積與分流筒和封閉罩內(nèi)壁形成的環(huán)隙截面積之比為1~2,分流筒高度與提升管外徑之比為4.4。這樣,可消除旋流快分頭噴出口附近的短路流,利于分離效率的提高。進(jìn)而,旋流快分頭2的旋流臂穿過分流筒,沿周向均勻布置3~5個,旋流臂向下彎曲成一定弧度,向下彎曲的角度為0~45°,旋流臂噴出口截面一般為高寬比在1~5之間的矩形、噴出口截面也可以為圓形或其它形狀。環(huán)流筒與提升管外壁間的內(nèi)環(huán)截面積與環(huán)流筒與封閉罩間的外環(huán)截面積的比值為0.25~0.5,內(nèi)環(huán)下部設(shè)置汽提蒸氣分布板或汽提蒸氣分布管,外環(huán)下部可設(shè)置汽提蒸氣分布管也可不設(shè)置汽提蒸氣分布管。封閉罩的頂部采用錐形縮口,錐形縮口上端與導(dǎo)流管聯(lián)接,導(dǎo)流管上可設(shè)置多根平衡管。汽提段汽提置換出的油氣及汽提蒸汽既可由沉降器(反應(yīng)器外殼)中與導(dǎo)流管相連的多根平衡管引出,也可由沿封閉罩筒壁周向開設(shè)的多個槽孔引出,封閉罩筒壁上槽孔的軸向高度與平衡管下端端面的軸向高度相同,二者均位于環(huán)流筒上端面與錐形下料汽提擋板之間。旋流快分頭噴出口與環(huán)流筒上端面間的距離為1.0m~10m。在該距離范圍內(nèi),既可保證旋流快分的分離效率,又可減少油氣的停留時間、降低二次裂化反應(yīng)。下面再詳細(xì)介紹一下各實(shí)施例的結(jié)構(gòu)和工作原理。實(shí)施例一如圖1所示,提升管13出口的油氣和催化劑顆粒由帶有分流筒1和分流擋板3旋流快分頭2的旋流臂噴出后在封閉罩10內(nèi)快速旋轉(zhuǎn)對油劑二相進(jìn)行快速分離,分離下來的催化劑顆粒沿封閉罩邊壁旋轉(zhuǎn)向下流動,經(jīng)錐形下料汽提擋板18進(jìn)入密相環(huán)流預(yù)汽提器的環(huán)流筒17與提升管外壁間的內(nèi)環(huán),在內(nèi)環(huán)汽提蒸氣風(fēng)管16的作用下,環(huán)流筒內(nèi)外環(huán)間所產(chǎn)生的密度差實(shí)現(xiàn)催化劑顆粒的密相環(huán)流預(yù)汽提,預(yù)汽提后的催化劑顆粒進(jìn)入下部的汽提段,在盤環(huán)形擋板15和汽提蒸氣風(fēng)管14的作用下繼續(xù)汽提。汽提蒸氣風(fēng)管14位于內(nèi)環(huán)汽提蒸氣風(fēng)管16之下。旋流快分頭2分離出的大量油氣、少量的細(xì)催化劑顆粒以及來自預(yù)汽提器的汽提蒸汽和汽提置換出的油氣在分流擋板的作用下沿分流筒與提升管間的環(huán)形通道向上流動經(jīng)導(dǎo)流管8進(jìn)入頂旋4(沉降器頂部旋風(fēng)分離器)。由頂旋分離出的油氣進(jìn)入沉降器頂部集氣室5,被分離下來的細(xì)催化劑顆粒沿頂旋料腿經(jīng)翼閥11進(jìn)入汽提段進(jìn)行汽提,汽提段汽提置換出的油氣和汽提蒸氣依次經(jīng)過位于沉降器稀相空間的平衡管9、導(dǎo)流管8、頂旋后進(jìn)入集氣室,氣體從反應(yīng)器引出管6引出,汽提后的催化劑顆粒經(jīng)待生斜管12進(jìn)入再生器進(jìn)行再生。這樣,不僅實(shí)現(xiàn)了油氣和催化劑的高效快速分離、油氣的快速引出及催化劑的高效預(yù)汽提,而且還降低了快分系統(tǒng)的占用空間,減小了沉降器的體積和結(jié)焦空間。實(shí)施例二如圖2所示,實(shí)施例二的實(shí)施工藝流程與實(shí)施例一類似。實(shí)施例二與實(shí)施例一主要存在兩方面不同,一是實(shí)施例二采用在封閉罩10上設(shè)置的多個槽孔90代替了實(shí)施例一中沉降器內(nèi)設(shè)置的平衡管9,槽孔90的軸向位置在錐形下料汽提擋板18與環(huán)流筒17之間,這樣,結(jié)構(gòu)更簡單,空間更緊湊,更有利于降低沉降器內(nèi)的結(jié)焦。汽提段汽提置換出的油氣和汽提蒸氣由槽孔進(jìn)入封閉罩,再依次經(jīng)錐形下料汽提擋板和分流筒后進(jìn)入導(dǎo)流管。二是實(shí)施例二在環(huán)流預(yù)汽提器的外環(huán)設(shè)置了外環(huán)汽提蒸氣風(fēng)管,并且用內(nèi)環(huán)汽提蒸氣分布板160替代了實(shí)施例一中設(shè)置的內(nèi)環(huán)汽提蒸氣風(fēng)管16。實(shí)施例三如圖3所示,實(shí)施例三的實(shí)施工藝流程與實(shí)施例二類似,二者不同的是:實(shí)施例三沒有在封閉罩之內(nèi)、以及環(huán)流預(yù)汽提器的外環(huán)設(shè)置外環(huán)汽提蒸氣風(fēng)管19,結(jié)構(gòu)相對比較簡單。為了能達(dá)到比較順暢的密相環(huán)流流動,發(fā)明人經(jīng)過長期的實(shí)驗(yàn)以及計(jì)算得出密相環(huán)流預(yù)汽提器的內(nèi)環(huán)截面積與外環(huán)截面積(環(huán)流筒與提升管外壁間的內(nèi)環(huán)截面積與環(huán)流筒與封閉罩間的外環(huán)截面積)的比值在0.3~0.4之間(這樣可使催化劑形成順暢的密相環(huán)流流動,同時提高密相環(huán)流的操作彈性)。實(shí)施例四如圖4所示,實(shí)施例四的實(shí)施工藝流程與實(shí)施例三類似,二者主要存在兩方面差異:一是實(shí)施例四沒有設(shè)置錐形的下料汽提擋板18,也就是,氣固密相環(huán)流預(yù)汽提器包括:依次連接在所述旋流快分頭之下的環(huán)流筒17、和內(nèi)環(huán)汽提蒸氣風(fēng)管16,所述環(huán)流筒17套設(shè)在所述提升管13上,結(jié)構(gòu)進(jìn)一步簡化,封閉罩10內(nèi)分離下來的催化劑顆粒直接進(jìn)入環(huán)流預(yù)汽提段的外環(huán)進(jìn)行預(yù)汽提;二是實(shí)施例四采用內(nèi)環(huán)汽提蒸氣風(fēng)管16取代實(shí)施例三中的內(nèi)環(huán)分布板(內(nèi)環(huán)汽提蒸氣分布板),這樣有利于合理增大環(huán)流預(yù)汽提器內(nèi)氣固環(huán)流的空間,提高汽提效果。本發(fā)明能實(shí)現(xiàn)油氣和催化劑的高效快速分離、油氣的快速引出及催化劑的高效預(yù)汽提,又能有效降低設(shè)備的占用空間,減小沉降器體積,降低沉降器內(nèi)的結(jié)焦場所。以上所述僅為本發(fā)明示意性的具體實(shí)施方式,并非用以限定本發(fā)明的范圍。為本發(fā)明的各組成部分在不沖突的條件下可以相互組合,任何本領(lǐng)域的技術(shù)人員,在不脫離本發(fā)明的構(gòu)思和原則的前提下所作出的等同變化與修改,均應(yīng)屬于本發(fā)明保護(hù)的范圍。