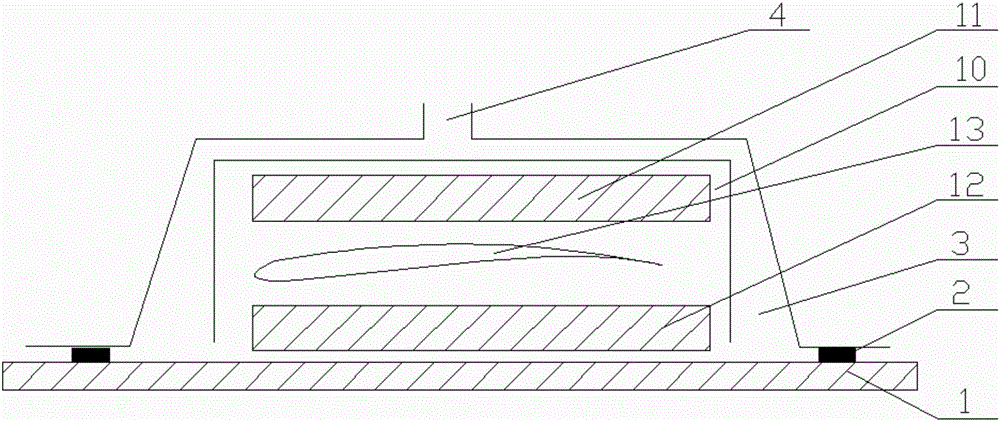
本發(fā)明屬于螺旋槳葉的制備
技術(shù)領(lǐng)域:
,涉及一種平流層飛艇用一體化復(fù)合材料螺旋槳葉的制備方法。
背景技術(shù):
:近年來,各國(guó)都在開展研究各類平流層飛行器。平流層飛艇是一種新型低成本、低能耗平流層飛行器,其大型高性能螺旋槳在控制方面起到了關(guān)鍵性作用已成為關(guān)鍵技術(shù),一般螺旋槳都采用拼接方式其強(qiáng)度與一體化螺旋槳相差近2倍之多,在同等強(qiáng)度時(shí)一般螺旋槳又比一體化螺旋槳重近1倍,存在薄壁槳葉分層,粘接氣泡等問題的出現(xiàn),需要研究一種輕質(zhì)、高效的平流層飛艇用一體化復(fù)合材料螺旋槳葉解決上述瓶頸問題。技術(shù)實(shí)現(xiàn)要素:本發(fā)明的目的是針對(duì)現(xiàn)有技術(shù)的不足,提供一種平流層飛艇用一體化復(fù)合材料螺旋槳葉的制備方法,其中,所述制備方法包括:步驟一:準(zhǔn)備制備所述螺旋槳葉的模具裝置,包括,模具裝置底板,設(shè)置于所述模具裝置底板上的模具本體,將所述模具本體封閉于所述模具裝置內(nèi)部的真空袋,所述真空袋上部具有真空嘴,所述模具本體包括外模具下模,芯模和外模具上模,所述外模具上模和所述外模具下模的相對(duì)表面設(shè)有外模具空腔,在所述外模具上模和所述外模具下模的所述空腔外側(cè)的相應(yīng)位置各設(shè)置至少一個(gè)定位裝置;步驟二:準(zhǔn)備碳纖維預(yù)浸布作為所述芯模的鋪層;步驟三:對(duì)所述外模具上模和所述外模具下模進(jìn)行清洗,并在表面噴涂脫模劑;清除芯模上的雜質(zhì),涂抹改性樹脂膠膜;步驟四:按照螺旋槳葉鋪層設(shè)計(jì)在所述芯膜外表面鋪敷所述碳纖維預(yù)浸布,形成所述螺旋槳葉的預(yù)制件;步驟五:將鋪敷完成的所述預(yù)制件放入所述外模具空腔內(nèi),并通過所述外模具上模和所述外模具下模上的所述定位裝置固定所述模具本體;步驟六:根據(jù)螺旋槳葉要求,將所述模具本體設(shè)置于所述模具裝置底板上,將所述真空袋罩在所述模具本體的外部,通過所述真空封泥將所述真空袋固定于所述模具裝置底板上,將所述模具本體封閉于所述模具裝置內(nèi)部,將所述真空嘴與真空裝置相連接,將所述模具裝置內(nèi)部抽成真空;步驟七:根據(jù)螺旋槳葉的固化要求通過加溫加壓設(shè)備對(duì)所述模具設(shè)備進(jìn)行加溫、加壓固化;步驟八:固化完成后,根據(jù)所述碳纖維預(yù)浸布固化要求進(jìn)行降溫處理,從所述加溫加壓設(shè)備中取出固化完成的所述模具裝置,冷卻至室溫;步驟九:根據(jù)螺旋槳葉的脫模要求拆除所述真空裝置,按照所述模具裝置的安裝順序的相反的順序拆除所述模具裝置,進(jìn)行脫模處理;步驟十:對(duì)脫模的螺旋槳葉的進(jìn)行打磨修邊,完成成品的制備。進(jìn)一步的,所述步驟一中的所述外模具的上模和所述外模具的下模采用鋼材料。進(jìn)一步的,所述步驟一中的所述芯模采用高性能聚甲基丙烯酰亞胺材料。進(jìn)一步的,所述步驟一中的所述模具裝置底板采用鋁材料。進(jìn)一步的,所述步驟三采用丙酮清洗。進(jìn)一步的,所述步驟三中的脫模劑采用美國(guó)PMR脫模劑。進(jìn)一步的,所述步驟三中的改性樹脂膠膜采用型號(hào)為JCH47。進(jìn)一步的,所述步驟七中的所述加溫加壓設(shè)備為高溫釜。進(jìn)一步的,所述步驟七中的所述加溫溫度范圍為125℃±10℃。進(jìn)一步的,所述步驟七中的所述加壓的壓力范圍為8-14個(gè)大氣壓。本發(fā)明的有益效果為:1、本發(fā)明為平流層飛行器的螺旋槳制作提供了一種新的方法,本方法工藝相對(duì)簡(jiǎn)單,成品質(zhì)量較好,成品強(qiáng)度較高、重量輕,制作效率較高。2、本發(fā)明采用芯模填充技術(shù),有效的提高了螺旋槳的承載能力;3、本發(fā)明采用芯模填充技術(shù),增強(qiáng)體纖維絲連續(xù)保證了一體化成型,提高了螺旋槳的整體質(zhì)量4、本發(fā)明采用了真空技術(shù),通過真空排出制作時(shí)存在的氣泡,有效的提高了成品率;5、本發(fā)明采用了熱壓技術(shù),通過對(duì)模具整體進(jìn)行加壓,保證了螺旋槳葉固化時(shí)所受壓力一致,避免了因受力不均導(dǎo)致的變形或有氣泡的情況。6、本發(fā)明方法制作的平流層飛艇用一體化復(fù)合材料螺旋槳葉提高了平流層飛行器的機(jī)動(dòng)性能,保證整體剛度和穩(wěn)定性的同時(shí)降低了自身重量,提高了螺旋槳的工作效率。附圖說明圖1是本發(fā)明的一體化復(fù)合材料螺旋槳葉的制備方法的流程圖。圖2是本發(fā)明的一體化復(fù)合材料螺旋槳葉的制備裝置正視圖。圖3是本發(fā)明的一體化復(fù)合材料螺旋槳葉的制備裝置的模具本體結(jié)構(gòu)的的示意圖。圖4是本發(fā)明的一體化復(fù)合材料螺旋槳葉的制備裝置的外模具上模的立體圖。圖5是本發(fā)明的一體化復(fù)合材料螺旋槳葉的制備裝置的預(yù)制件的立體圖。圖6是本發(fā)明的一體化復(fù)合材料螺旋槳葉的制備裝置的預(yù)制件的A-A剖面圖。圖中:1-模具裝置底板,2-真空封泥,3-真空袋,4-真空嘴,10-模具本體,11-外模具上模,12-外模具下模,13-預(yù)制件,14-定位裝置,15-外模具空腔,16-碳纖維預(yù)浸布,17-芯模。具體實(shí)施方式下面結(jié)合附圖和具體實(shí)施方式,對(duì)本發(fā)明作進(jìn)一步的說明。實(shí)施例一本發(fā)明的所述螺旋槳葉的制備方法,如圖1所示,包括:步驟一:準(zhǔn)備制備所述螺旋槳葉的模具裝置,如圖2所示,所述模具裝置包括,模具裝置底板1,設(shè)置于所述模具裝置底板1上的模具本體10,將所述模具本體10封閉于所述模具裝置內(nèi)部的真空袋3,所述真空袋3上部具有真空嘴4,如圖3和圖4所示,所述模具本體10包括外模具下模12,芯模17和外模具上模11,所述外模具上模11和所述外模具下模12的相對(duì)表面設(shè)有外模具空腔15,在所述外模具上模11和所述外模具下模12的所述空腔15外側(cè)的相應(yīng)位置各設(shè)置至少一個(gè)定位裝置14,所述外模具上模11和所述外模具下模12采用鋼材料,所述芯模17采用高性能聚甲基丙烯酰亞胺,所述模具裝置底板1采用鋁材料;步驟二:根據(jù)如表1所示的鋪層要求,準(zhǔn)備碳纖維預(yù)浸布16作為所述芯模17的鋪層;表1序號(hào)規(guī)格角度數(shù)量12200*32030°222200*32090°131800*280150°241500*2800°15700*3200°46500*280150°27500*30090°28500*30030°19700*1800°210100*800°211100*8090°212100*80150°213100*8030°2步驟三:對(duì)所述外模具上模11和所述外模具下模12進(jìn)行清洗,所述清洗劑優(yōu)選丙酮,并在表面噴涂脫模劑,所述脫模劑優(yōu)選美國(guó)PMR脫模劑,清除所述芯模13上的雜質(zhì),涂抹改性樹脂膠膜,所述改性樹脂膠膜優(yōu)選型號(hào)為JCH47;步驟四:按照螺旋槳葉鋪層設(shè)計(jì)在所述芯膜17外表面鋪敷所述碳纖維預(yù)浸布16,使得所述芯模17和所述碳纖維預(yù)浸布16形成一體化復(fù)合材料螺旋槳葉的預(yù)制件13,如圖5和圖6所示;步驟五:將鋪敷完成的所述預(yù)制件13放入所述外模具空腔15內(nèi),并通過所述外模具上模11和所述外模具下模12上的所述定位裝置14固定所述模具本體10,如圖3所示;步驟六:根據(jù)螺旋槳葉要求,將所述模具本體10設(shè)置于所述模具裝置底板1上,將所述真空袋3罩在所述模具本體10的外部,通過所述真空封泥4將所述真空袋3固定于所述模具裝置底板1上,將所述模具本體10封閉于所述模具裝置內(nèi)部,將所述真空嘴4與真空裝置相連接,將所述模具裝置內(nèi)部抽成真空,如圖2所示;步驟七:根據(jù)所述螺旋槳葉的固化要求,通過加溫加壓設(shè)備對(duì)所述模具裝置進(jìn)行加溫、加壓固化;所述加溫加壓設(shè)備采用高溫釜,設(shè)置好高壓釜加熱、加壓固化程序,加熱、加壓程序根據(jù)所述碳纖維預(yù)浸布16的固化工藝參數(shù)進(jìn)行設(shè)置,然后進(jìn)行加熱、加壓固化。加溫溫度為125℃±10℃,加壓的壓力范圍為8-14個(gè)大氣壓;步驟八:固化完成后,根據(jù)所述碳纖維預(yù)浸布16固化要求進(jìn)行降溫處理,從所述加溫加壓設(shè)備中取出固化完成的所述模具裝置,冷卻至室溫;步驟九:根據(jù)所述螺旋槳葉的脫模要求拆除所述真空裝置,按照所述模具裝置的安裝順序的相反的順序拆除所述模具裝置,進(jìn)行脫模處理;從高壓釜取出固化完成的模具,冷卻至室溫,將所述真空袋3打開,取下所述上模具11,取出復(fù)合材料螺旋槳葉;步驟十:對(duì)脫模的螺旋槳葉的進(jìn)行打磨修邊,完成成品的制備。本發(fā)明并不限于上述實(shí)施方式,在不背離本發(fā)明實(shí)質(zhì)內(nèi)容的情況下,本領(lǐng)域技術(shù)人員可以想到的任何變形、改進(jìn)、替換均落入本發(fā)明的保護(hù)范圍。當(dāng)前第1頁(yè)1 2 3