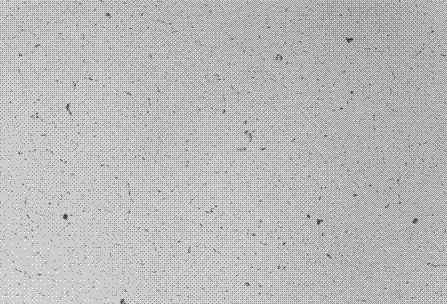
本發(fā)明涉及鋁合金制備
技術(shù)領(lǐng)域:
,尤其涉及一種高速動車用al-mg-si合金型材制備方法。
背景技術(shù):
:al-mg-si合金型材強度適中、容易折彎、焊接性能優(yōu)良,廣泛應(yīng)用于軌道交通領(lǐng)域。軌道交通列車運行速度快,對材料的性能要求相對較高,其力學(xué)性能要求均是按照t6狀態(tài)要求,而由于擠壓型材離線淬火設(shè)備較為復(fù)雜,且價格昂貴,目前很少有鋁型材企業(yè)配備擠壓型材離線淬火設(shè)備,因此,目前工業(yè)生產(chǎn)方式一般都是用t5狀態(tài)代替t6狀態(tài),t5狀態(tài)力學(xué)性能雖然一般也能達到t6狀態(tài)最低要求,但較t6狀態(tài)平均要低20-30mpa,力學(xué)性能的降低會導(dǎo)致列車結(jié)構(gòu)安全性降低。目前工業(yè)化生產(chǎn)普遍采用單級時效工藝,即生產(chǎn)工藝路線一般為:擠壓—在線淬火—單級高溫人工時效,無法有效的控制該al-mg-si合金時效過程中析出相的形態(tài)、大小和分布,因此,在t5狀態(tài)下固溶不夠充分時,無法獲得高的強度,從而達不到高速動車的使用要求。技術(shù)實現(xiàn)要素:針對以上不足,本發(fā)明提供一種能夠讓高速動車用al-mg-si型材強度在t5狀態(tài)下達到或略高于普通t6水平的型材制備方法。為達到上述目的,本發(fā)明采用如下技術(shù)方案:一種高速動車用al-mg-si合金型材制備方法,包括有以下步驟:(一)擠壓:鑄造的鋁合金鑄錠為al-mg-si合金鑄錠,所述al-mg-si合金鑄錠的組分及重量百分比為:si:0.4-0.8%,mg:0.8-1.2%,cu:0.15-0.4%,fe≤0.7%,以及含有下述一種或一種以上的元素:cr≤0.3%、mn≤0.15%、zn≤0.25%、ti≤0.1%、v≤0.05%、sc≤0.15%、ag≤0.2%,其余為al及不可避免的雜質(zhì);待所述al-mg-si合金鑄錠以及模具加熱完成,擠壓筒到溫之后上模進行擠壓,擠壓速度控制在1-5m/min;(二)在線淬火:型材淬火區(qū)入口溫度為480-530℃,通過風(fēng)冷或者水冷的方式使型材冷卻,冷卻速度為1-10℃/s;(三)單級低溫人工時效:時效溫度為40-70℃,保溫時間為4-40h;(四)冷卻停放:低溫人工時效后,型材出爐冷卻至室溫,并停放2-48h;(五)雙級高溫人工時效:第一級時效溫度為100-150℃,保溫時間為2-48h;第二級時效溫度為120-200℃,保溫時間為1-24h。優(yōu)選的是,所述al-mg-si合金鑄錠的組分及重量百分比為:si:0.4-0.6%,mg:0.8-1%,cu:0.15-0.3%,fe≤0.6%,以及含有下述一種或一種以上的元素:cr≤0.2%、mn≤0.1%、zn≤0.2%、ti≤0.1%、v≤0.05%、sc≤0.15%、ag≤0.2%,其余為al及不可避免的雜質(zhì)。優(yōu)選的是,所述al-mg-si合金鑄錠的組分及重量百分比為:si:0.6-0.8%,mg:1-1.2%,cu:0.3-0.4%,fe≤0.6%,以及含有下述一種或一種以上的元素:cr≤0.2%、mn≤0.1%、zn≤0.2%、ti≤0.1%、v≤0.05%、sc≤0.15%、ag≤0.2%,其余為al及不可避免的雜質(zhì)。優(yōu)選的是,所述al-mg-si合金鑄錠的組分及重量百分比為:si:0.5-0.6%,mg:0.9-1%,cu:0.2-0.3%,fe≤0.7%,以及含有下述一種或一種以上的元素:cr≤0.1%、mn≤0.1%、zn≤0.2%、ti≤0.1%、v≤0.05%、sc≤0.15%、ag≤0.2%,其余為al及不可避免的雜質(zhì)。優(yōu)選的是,步驟(一)擠壓中,所述al-mg-si合金鑄錠加熱完成溫度為480-520℃,所述模具加熱完成溫度為490-510℃,所述待擠壓筒到溫溫度為440-460℃。優(yōu)選的是,步驟(二)在線淬火中,型材冷卻速度為1-5℃/s。優(yōu)選的是,步驟(三)單級低溫人工時效中,時效溫度為55-60℃,保溫時間為8-20h。優(yōu)選的是,步驟(三)單級低溫人工時效中,時效溫度為60-70℃,保溫時間為8-15h。優(yōu)選的是,步驟(五)雙級高溫人工時效中,第一級時效溫度為110-130℃,保溫時間為12-22h;第二級時效溫度為150-180℃,保溫時間為5-10h。優(yōu)選的是,步驟(五)雙級高溫人工時效中,第一級時效溫度為130-150℃,保溫時間為12-22h;第二級時效溫度為180-200℃,保溫時間為1-10h。與現(xiàn)有技術(shù)相比,本發(fā)明的有益效果是:本發(fā)明提出的一種高速動車用al-mg-si合金型材制備方法,適用的al-mg-si合金鑄錠的組分及重量百分比為:si:0.4-0.8%,mg:0.8-1.2%,cu:0.15-0.4%,fe≤0.7%,以及含有下述一種或一種以上的元素:cr≤0.3%、mn≤0.15、zn≤0.25%、ti≤0.1%、v≤0.05%、sc≤0.15%、ag≤0.2%,其余為al及不可避免的雜質(zhì);本發(fā)明將目前工業(yè)化生產(chǎn)普遍采用的單級時效工藝由原來的:擠壓—在線淬火—單級高溫人工時效,調(diào)整為:擠壓—在線淬火—單級低溫人工時效—冷卻停放—雙級高溫人工時效,配合特定的合金組分,通過三級時效處理,使得第二相充分彌散析出,最大化的發(fā)揮第二相強化效果,從而提高該合金t5狀態(tài)的力學(xué)性能,使其強度達到或略高于普通t6狀態(tài),從而達到高速動車的使用要求。本發(fā)明中,al-mg-si合金時效過程中第二相轉(zhuǎn)化過程如下:gp區(qū)—針狀mg2si非平衡相—棒狀mg2si非平衡相—片狀平衡mg2si相。gp區(qū)是溶質(zhì)原子聚集區(qū),是鋁合金時效強化的根本原因,鋁合金型材在在線淬火后,進行單級低溫人工時效,有利于形成更多彌散的溶質(zhì)原子聚集區(qū)(gp區(qū)),從而使得在后續(xù)的雙級高溫時效過程中,第二相形核長大時有更多的gp區(qū)作為核心依附,使第二相長大后更為細小均勻,從而強化效果更為明顯。附圖說明為了更清楚地說明本發(fā)明實施例的技術(shù)方案,以下將對實施例描述中所需要使用的附圖作簡單地介紹。圖1為本發(fā)明實施例1提供的一種高速動車用al-mg-si合金型材制備方法的工藝流程圖;圖2為按本發(fā)明實施例1的工藝方法所獲型材的金相組織圖像;圖3為按現(xiàn)有技術(shù)的工藝方法所獲型材的金相組織圖像。具體實施方式下面將結(jié)合本發(fā)明實施例中的附圖,對本發(fā)明實施例中的技術(shù)方案進行清楚、完整地描述。顯然,所描述的實施例僅僅是本發(fā)明一部分實施例,而不是全部的實施例。基于本發(fā)明中的實施例,本領(lǐng)域普通技術(shù)人員在沒有作出創(chuàng)造性勞動前提下所獲得的所有其他實施例,都屬于本發(fā)明保護的范圍。實施例1請參照圖1,本實施例提供一種高速動車用al-mg-si合金型材制備方法,包括有以下步驟:(一)擠壓(s1):使用山西太原重型機械集團有限公司制造的7500mn單動短行程擠壓機,擠壓筒直徑460mm;鑄造的鋁合金鑄錠為al-mg-si合金鑄錠,所述al-mg-si合金鑄錠的組分及重量百分比為:si:0.6%,mg:1%,cu:0.3%,fe:0.6%,cr:0.2%,mn:0.1%,zn:0.2%,ti:0.1%,v:0.05%,sc:0.15%,ag:0.1%,其余為al及不可避免的雜質(zhì);鑄錠車皮后直徑448mm,鑄錠長度1000mm;將al-mg-si合金鑄錠分區(qū)加熱,頭部溫度510℃,中部溫度500℃,尾部溫度490℃,模具加熱到500℃,待擠壓筒溫度控制在450±10℃之后,將al-mg-si合金鑄錠上模進行擠壓,擠壓速度控制在3m/min;擠壓型材截面規(guī)格300*420mm,壁厚3-12mm;(二)在線淬火(s2):型材淬火區(qū)入口溫度為500℃,使用意大利奧馬弗在線淬火系統(tǒng)進行冷卻,通過水冷的方式使型材冷卻,水冷參數(shù)設(shè)置為65,冷卻速度為5℃/s;(三)單級低溫人工時效(s3):時效溫度為55℃,保溫時間為20h;(四)冷卻停放(s4):低溫人工時效后,型材出爐冷卻至室溫,并停放24h;(五)雙級高溫人工時效(s5):第一級時效溫度為130℃,升溫速度2℃/min,保溫時間為12h;第二級時效溫度為150℃,升溫速度2℃,保溫時間為10h。實施例2本實施例提供一種高速動車用al-mg-si合金型材制備方法,包括有以下步驟:(一)擠壓:使用山西太原重型機械集團有限公司制造的7500mn單動短行程擠壓機,擠壓筒直徑460mm;鑄造的鋁合金鑄錠為al-mg-si合金鑄錠,所述al-mg-si合金鑄錠的組分及重量百分比為:si:0.4%,mg:0.8%,cu:0.15%,fe:0.5%,cr:0.1%,mn:0.05%,zn:01%,ti:0.1%,v:0.05%,sc:0.15%,ag:0.1%,其余為al及不可避免的雜質(zhì);鑄錠車皮后直徑448mm,鑄錠長度1200mm;將al-mg-si合金鑄錠分區(qū)加熱,頭部溫度520℃,中部溫度500℃,尾部溫度480℃,模具加熱到490℃,待擠壓筒溫度控制在450±10℃之后,將al-mg-si合金鑄錠上模進行擠壓,擠壓速度控制在1m/min;擠壓型材截面規(guī)格200*1900mm,壁厚3-5mm;(二)在線淬火:型材淬火區(qū)入口溫度為480℃,用意大利奧馬弗在線淬火系統(tǒng)進行冷卻,通過風(fēng)冷的方式使型材冷卻,風(fēng)冷參數(shù)全部設(shè)置為99,冷卻速度為1℃/s;(三)單級低溫人工時效:時效溫度為40℃,保溫時間為40h;(四)冷卻停放:低溫人工時效后,型材出爐冷卻至室溫,并停放2h;(五)雙級高溫人工時效:第一級時效溫度為100℃,保溫時間為48h;第二級時效溫度為120℃,保溫時間為24h。實施例3本實施例提供一種高速動車用al-mg-si合金型材制備方法,包括有以下步驟:(一)擠壓:使用山西太原重型機械集團有限公司制造的7500mn單動短行程擠壓機,擠壓筒直徑460mm;鑄造的鋁合金鑄錠為al-mg-si合金鑄錠,所述al-mg-si合金鑄錠的組分及重量百分比為:si:0.8%,mg:1.2%,cu:0.4%,fe:0.7%,cr:0.3%,mn:0.15%,zn:0.25%,ti:0.1%,v:0.05%,sc:0.15%,ag:0.2%,其余為al及不可避免的雜質(zhì);將al-mg-si合金鑄錠分區(qū)加熱,頭部溫度510℃,中部溫度500℃,尾部溫度490℃,模具加熱到500℃,待擠壓筒溫度控制在450±10℃之后,將al-mg-si合金鑄錠上模進行擠壓,擠壓速度控制在5m/min;擠壓型材截面規(guī)格340*290mm,壁厚6-10mm;(二)在線淬火:型材淬火區(qū)入口溫度為480℃,用意大利奧馬弗在線淬火系統(tǒng)進行冷卻,通過水冷的方式使型材冷卻,水冷參數(shù)設(shè)置為80,冷卻速度為10℃/s;(三)單級低溫人工時效:時效溫度為70℃,保溫時間為4h;(四)冷卻停放:低溫人工時效后,型材出爐冷卻至室溫,并停放48h;(五)雙級高溫人工時效:第一級時效溫度為150℃,保溫時間為2h;第二級時效溫度為200℃,保溫時間為1h。實施例4本實施例提供一種高速動車用al-mg-si合金型材制備方法,包括有以下步驟:(一)擠壓:使用山西太原重型機械集團有限公司制造的7500mn單動短行程擠壓機,擠壓筒直徑460mm;鑄造的鋁合金鑄錠為al-mg-si合金鑄錠,所述al-mg-si合金鑄錠的組分及重量百分比為:si:0.5%,mg:0.9%,cu:0.2%,fe:0.7%,cr:0.3%,mn:0.15%,zn:0.25%,ti:0.1%,sc:0.15%,其余為al及不可避免的雜質(zhì);將al-mg-si合金鑄錠分區(qū)加熱,頭部溫度510℃,中部溫度500℃,尾部溫度490℃,模具加熱到500℃,待擠壓筒溫度控制在450±10℃之后,,將al-mg-si合金鑄錠上模進行擠壓,擠壓速度控制在3m/min;擠壓型材截面規(guī)格420*240mm,壁厚10-15mm;(二)在線淬火:型材淬火區(qū)入口溫度為520℃,用意大利奧馬弗在線淬火系統(tǒng)進行冷卻,通過水冷的方式使型材冷卻,水冷參數(shù)設(shè)置為90,冷卻速度為5℃/s;(三)單級低溫人工時效:時效溫度為60℃,保溫時間為8h;(四)冷卻停放:低溫人工時效后,型材出爐冷卻至室溫,并停放24h;(五)雙級高溫人工時效:第一級時效溫度為110℃,保溫時間為22h;第二級時效溫度為180℃,保溫時間為5h。實施例5本實施例提供一種高速動車用al-mg-si合金型材制備方法,包括有以下步驟:(一)擠壓:使用山西太原重型機械集團有限公司制造的7500mn單動短行程擠壓機,擠壓筒直徑460mm;鑄造的鋁合金鑄錠為al-mg-si合金鑄錠,所述al-mg-si合金鑄錠的組分及重量百分比為:si:0.5%,mg:0.9%,cu:0.2%,fe:0.7%,cr:0.3%,mn:0.1%,zn:0.2%,ti:0.1%,sc:0.15%,其余為al及不可避免的雜質(zhì);將al-mg-si合金鑄錠分區(qū)加熱,頭部溫度510℃,中部溫度500℃,尾部溫度490℃,模具加熱到500℃,待擠壓筒溫度控制在450±10℃之后,,將al-mg-si合金鑄錠上模進行擠壓,擠壓速度控制在3m/min;擠壓型材截面規(guī)格420*240mm,壁厚10-15mm;(二)在線淬火:型材淬火區(qū)入口溫度為520℃,用意大利奧馬弗在線淬火系統(tǒng)進行冷卻,通過水冷的方式使型材冷卻,水冷參數(shù)設(shè)置為90,冷卻速度為5℃/s;(三)單級低溫人工時效:時效溫度為55℃,保溫時間為15h;(四)冷卻停放:低溫人工時效后,型材出爐冷卻至室溫,并停放24h;(五)雙級高溫人工時效:第一級時效溫度為110℃,保溫時間為22h;第二級時效溫度為180℃,保溫時間為5h。下面對按本發(fā)明實施例1的工藝方法所獲型材以及按現(xiàn)有技術(shù)的工藝方法所獲型材的金相組織圖像、最終力學(xué)性能進行測試、比較。圖2為按本發(fā)明實施例1的工藝方法所獲型材的金相組織圖像,圖3為按現(xiàn)有技術(shù)的工藝方法所獲型材的金相組織圖像,圖2和圖3均為200倍金相顯微鏡下觀察獲得。從圖2和圖3中可以看出,按本發(fā)明實施例1的工藝方法所獲型材的金相組織,第二相長大后更為細小均勻,從而強化效果更為明顯;按現(xiàn)有技術(shù)的工藝方法所獲型材的金相組織,第二相長大后更為粗大不均,從而強化效果沒有本發(fā)明的明顯。表1按本發(fā)明實施例1的工藝方法所獲型材的最終力學(xué)性能樣品編號12345平均抗拉強度(mpa)299298301301295298.8屈服強度(mpa)265265268266262265.2表2按現(xiàn)有技術(shù)的工藝方法所獲型材的最終力學(xué)性能樣品編號678910平均抗拉強度(mpa)268270272269275270.8屈服強度(mpa)225229231228234229.4表1為按本發(fā)明實施例1的工藝方法所獲型材的最終力學(xué)性能;表2為按現(xiàn)有技術(shù)的工藝方法所獲型材的最終力學(xué)性能。從表1和表2中可以看出,按本發(fā)明實施例1的工藝方法所獲型材的五個樣品的抗拉強度范圍為295-301mpa,平均抗拉強度為298.8mpa,按本發(fā)明實施例1的工藝方法所獲型材的五個樣品的屈服強度范圍為262-268mpa,平均屈服強度為265.2mpa;按現(xiàn)有技術(shù)的工藝方法所獲型材的五個樣品的抗拉強度范圍為268-275mpa,平均抗拉強度為270.8mpa,按現(xiàn)有技術(shù)的工藝方法所獲型材的五個樣品的屈服強度范圍為225-234mpa,平均屈服強度為229.4mpa;由此可知,按本發(fā)明實施例1的工藝方法所獲型材的抗拉強度和屈服強度都比按現(xiàn)有技術(shù)的工藝方法所獲型材的抗拉強度和屈服強度高,即采用本發(fā)明公開的高速動車用al-mg-si合金型材制備方法,能使得al-mg-si型材強度在t5狀態(tài)下達到或略高于普通t6水平,從而達到高速動車的使用要求。以上所述,僅為本發(fā)明的具體實施方式,但本發(fā)明的保護范圍并不局限于此,任何熟悉本
技術(shù)領(lǐng)域:
的技術(shù)人員在本發(fā)明揭露的技術(shù)范圍內(nèi),可輕易想到的變化或替換,都應(yīng)涵蓋在本發(fā)明的保護范圍之內(nèi)。因此,本發(fā)明的保護范圍應(yīng)以所述權(quán)利要求的保護范圍為準(zhǔn)。當(dāng)前第1頁12