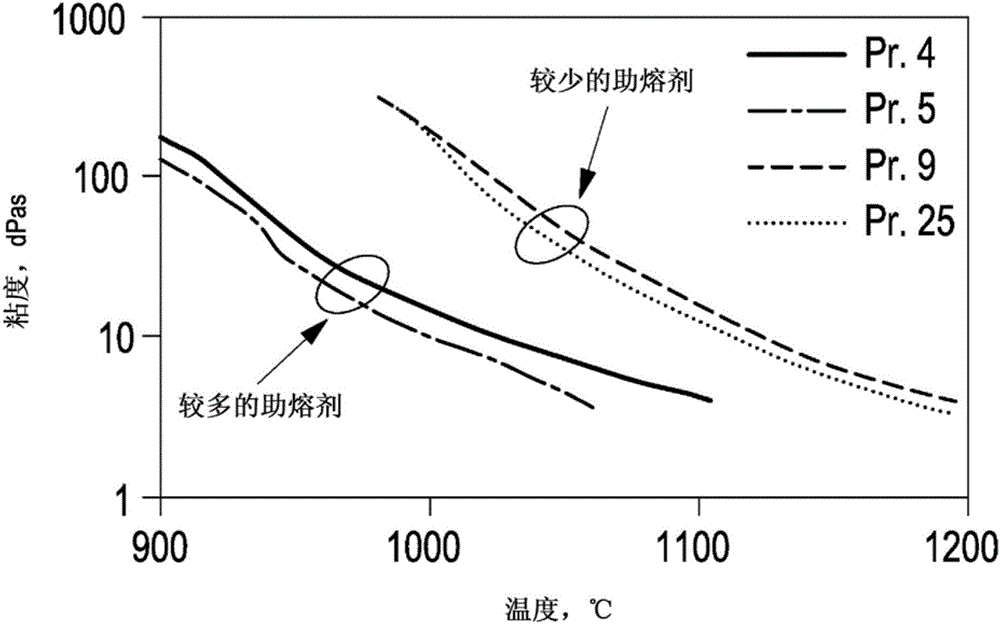
本發(fā)明涉及一種鑄造粉末、鑄造熔渣以及用于鋼鑄造的方法。
背景技術(shù):
:在鋼的鑄造過程中持續(xù)地在位于鑄模(通常也稱為硬模)中的、已熔化的鋼的表面上產(chǎn)生鑄造粉末。在此,鋼通過加熱熔化并且形成熔渣層,該熔渣層連續(xù)地流入鑄模和凝固的鋼外殼之間的縫隙中并且由此被消耗。鑄造粉末或由其導(dǎo)致的熔渣的重要的目的是在鑄模和可凝固的外殼之間的潤滑、控制待固化的鋼的散熱、脫氧產(chǎn)物的吸收、防止氧化還原以及熔化的鋼的隔熱。對于鋼的連鑄而言典型的鑄造粉末建立在硅酸鈣基礎(chǔ)上并且通常含有顯著量的二氧化硅(SiO2)以及其他易于還原的組分,例如氧化錳(MnO)和氧化鐵(FeO),從而在鋁合金鋼的鑄造過程中,鑄造熔渣中的氧化鋁含量由于鋼中的鋁(Al)與二氧化硅以及與鑄造熔渣中的氧化錳和氧化鐵之間的化學(xué)反應(yīng)而急劇增加:在Al鎮(zhèn)靜鋼的鑄造過程中,典型的氧化鋁(Al2O3,也稱為釩土)的含量為約2-4重量%。隨著鋼中鋁含量的增加,鑄造熔渣中Al2O3含量也增加。例如,在Al含量為約1.2-1.5重量%的TRIP鋼的制造過程中,鑄造熔渣中的Al2O3濃度升高到約35-40重量%。鑄造熔渣的SiO2含量相應(yīng)地減小,因為由鋁還原了二氧化硅。一般由此改變了鑄造熔渣的特性。例如,由于Al2O3的含量和與之相關(guān)的二氧化硅的比例的下降使鑄造熔渣的堿性、粘性以及結(jié)晶趨勢增加,這導(dǎo)致其潤滑作用的減弱。一般來說,非晶固化的鑄造熔渣具有比以結(jié)晶固化的鑄造熔渣更好的潤滑作用。在現(xiàn)有技術(shù)中,通常使用基于硅酸鈣的熔渣系統(tǒng)。只要鋼的鋁含量不是過高,即,特別是<重量%,這些基于硅酸鈣的熔渣系統(tǒng)通常主要是以非晶方式固化。然而,在熔體中的更高的Al含量的情況下,基于硅酸鈣的熔渣系統(tǒng)主要是以結(jié)晶的方式固化。在同時具有高錳含量(例如具有Mn含量≥15重量%且Al含量≥1重量%)的鋁合金鋼的鑄造過程中,由此額外地使鑄造過程變得困難,即,這些鋼的液相線溫度由于高的Mn含量而比例如TRIP鋼的液相線溫度低約100℃。這意味著對于具有高Al-Mn含量的鋼而言,鑄造熔渣的熔化溫度和結(jié)晶溫度必然同樣地比其他高Al含量的鋼低約100℃。否則鑄造熔渣可能在鑄模的下半部完全結(jié)晶,從而失去其潤滑作用。由于在Al合金鋼的鑄造過程中鑄造熔渣特性的上述變化,這類鑄造熔渣通常僅能夠不充分地或者完全不再能滿足其任務(wù)。因此,特別是具有高含量的鋁或高含量的鋁和錳的鋼不再能夠通過現(xiàn)有技術(shù)中已知的鑄造粉末而過程可靠地制造。WO2011/090218中已知用于鋼鑄造的鑄造粉末的組成,但是該組成由于其15-30重量%的高SiO2含量特別不適合在具有高含量鋁的鋼的鑄造過程中使用。相應(yīng)地也適用于WO2007/148939中已知的鑄造粉末以及其在鋼鑄造中的應(yīng)用。JP57184563A公開了一種用于具有相對較低的Si02含量的熔化金屬的涂層的粉末。但是由該粉末得到的熔渣由于其化學(xué)組成而不能確保必要的功能特性,比如潤滑作用和熱傳遞,特別是對于Al-Mn鋼而言。根據(jù)經(jīng)驗,由JP57184563中已知的鑄造粉末所產(chǎn)生的熔渣具有過高的結(jié)晶溫度以及在過程相關(guān)的范圍內(nèi)具有過高的粘性。技術(shù)實現(xiàn)要素:因此,本發(fā)明的目的在于提供一種鑄造粉末以及鑄造熔渣,該鑄造粉末以及鑄造熔渣實現(xiàn)了制造具有≥1重量%的高鋁含量和一定情況下≥15重量%的高錳含量和一定情況下≥0.2重量%的鈦的鋼。本發(fā)明的另一個目的在于,提供一種在使用該鑄造粉末或該鑄造熔渣的條件下用于鋼鑄造的方法、特別是用于鋼連鑄的方法。該目的通過說明書和權(quán)利要求書的內(nèi)容得以實現(xiàn)。在第一個方面,本發(fā)明涉及包含以下成分的鑄造熔渣:30-50重量%的CaO;20-45重量%的Al2O3;7-15重量%的F_(氟離子);5-15重量%的Na2O;3-6.5重量%的SiO2;2-5%重量%的Li2O。該鑄造熔渣由鑄造粉末產(chǎn)生,該鑄造粉末含有基本上以預(yù)熔化的鋁酸鈣形式的成分CaO和Al2O3。在本發(fā)明的意義層面上,基本上預(yù)熔化意味著鋁酸鈣有>50%、優(yōu)選>60%、更優(yōu)選>70%、特別優(yōu)選>80%、最優(yōu)選>90%到最大100%預(yù)熔化。此外,該鑄造粉末還包括含氟化物的成分,優(yōu)選為CaF2、SiO2,在一定情況下也可以以CaSiO3、Na2O的形式,在一定情況下也可以以Na2CO3、Li2O的形式,在一定情況下也可以以Li2CO3以及可能額外的Al2O3的形式。在此,該鑄造粉末也可以含有例如在加熱過程中產(chǎn)氣(比如水或CO2)的揮發(fā)性成分。在另一個方面,本發(fā)明因此涉及一種鑄造粉末,該鑄造粉末在不計算揮發(fā)性組分的情況下包括以下組分:40-60重量%的預(yù)熔化的鋁酸鈣;10-30重量%的含氟化物的成分、優(yōu)選CaF2;3-6.5重量%的SiO2;5-15重量%的Na2O;2-5.5重量%的Li2O;≤10.5重量%的Al2O3;≤15重量%的碳。對于實現(xiàn)期望的鑄造熔渣組成以及實現(xiàn)所需的鑄造熔渣特性(比如其粘性)而言,重要的是,在預(yù)熔化的鋁酸鈣中CaO相對于Al2O3的比例在約40/60(2:3)至約50/50(1:1)的范圍內(nèi)。在預(yù)熔化的鋁酸鈣中CaO相對于Al2O3的比例不應(yīng)明顯地小于0.6或明顯地大于1.0,因為否則的話鋁酸鈣的液相線溫度變得過高而且使作為鑄造粉末的組分的鋁酸鈣熔化并由此僅不充分地熔化該鑄造粉末。該比例為優(yōu)選0.6至1.1、更優(yōu)選0.65至1.05、特別優(yōu)選0.7至1或0.7至0.9。另外還重要的是,鋁酸鈣以預(yù)熔化的形式存在于鑄造粉末中。鋁酸鈣的優(yōu)選的組成近似于共晶成分,該共晶成分促使鑄造粉末的更快熔化以及由該鑄造粉末獲得的鑄造熔渣的更低結(jié)晶趨勢,這使過程可靠性得到了提高。使用預(yù)熔化的鋁酸鈣的另一個原因在于,CaO添加易于操作。燒石灰(CaO)的加入由此妨礙鑄造粉末的制造,即,燒石灰吸濕性強并由此可以通過吸濕而改變其重量。這樣可能導(dǎo)致鑄造粉末組成或鑄造熔渣組成中的CaO/AL2O3比例的偏移并使其特性劣化。硅有助于非晶狀態(tài)的穩(wěn)定并促進(jìn)鑄造熔渣的非晶固化。鑄造粉末中的SiO2含量不應(yīng)小于3重量%,因為否則的話所得鑄造熔渣的非晶比重小于60%。鑄造粉末中的SiO2含量不應(yīng)大于6.5重量%,因為否則的話額外的SiO2含量可能與鋼熔體中所含的鋁反應(yīng)。游離氧可以結(jié)合鋁,因此熔渣可以額外地吸收Al2O3。熔渣系統(tǒng)將不再是化學(xué)穩(wěn)定的,即,無法得到所追求的CaO與Al2O3的最佳比例。鑄造粉末中的含氟化物的成分、Na2O和Li2O影響固化溫度以及由此獲得的鑄造熔渣的結(jié)晶行為。含氟化物的成分的含量應(yīng)當(dāng)不小于10重量%,Na2O的含量應(yīng)不小于5重量%而Li2O的含量應(yīng)不小于2重量%,因為否則的話可能使固化溫度升高并且使以結(jié)晶形式固化的熔渣比重增加。在這種情況下Li2O的影響大于Na2O的影響,因此Li2O必須以較少的量加入。然而,與Na2O相比,Li2O是非常昂貴的,因此出于成本的原因,Li2O的作用盡可能用Na2O補償。含氟化物的成分的含量應(yīng)不大于30重量%,Na20的含量應(yīng)不大于15重量%而Li2O的含量應(yīng)不大于5.5重量%,因為否則的話可能使固化溫度過低并且鑄造熔渣可能變成過度的稀液狀。稀液狀的鑄造爐渣在鋼表面上流走,由此不再能夠在鋼連鑄外殼和硬模壁之間的整個接觸面上提供熔渣的潤滑作用。這可能導(dǎo)致仍較薄的連鑄件外殼的斷裂并且由于連鑄件斷裂而導(dǎo)致生產(chǎn)損失。此外,不完全形成的爐渣膜導(dǎo)致不均勻的散熱條件,這又導(dǎo)致了連鑄件外殼中的熱應(yīng)力并且因此可能同樣導(dǎo)致連鑄件斷裂。除了在預(yù)熔化的鋁酸鈣中結(jié)合的Al2O3之外,還可以將Al2O3添加到鑄造粉末中。將額外的Al2O3添加到鑄造粉末中,以便在含鈣的組分、特別是CaF2的含量相對較高的情況下,使CaO與Al2O3的比例保持在約0.6至約1.0的目標(biāo)最佳范圍內(nèi),因為添加含鈣的組分、特別是CaF2使通過鋁酸鈣而引入的CaO與Al2O3的初始比例偏移。額外的Al2O3的比重不應(yīng)超過10.5重量%,從而不會使CaO與Al2O3的比例過于強烈地對Al2O3有利地偏移,這又會對鑄造熔渣的形成和功能性產(chǎn)生不利影響。在添加額外的Al2O3的情況下,在鑄造粉末中CaO與Al2O3的比例為0.7至0.9被證明是特別有利的。為了加速鑄造粉末的熔化,可以將碳加入鑄造粉末中。鑄造粉末中的碳含量應(yīng)不大于15重量%,從而避免鋼熔體的碳化。優(yōu)選鑄造粉末可以以4-10重量%、特別優(yōu)選5-7重量%的量含有碳。在此可以使用常見的、技術(shù)人員已知的形式的碳,例如作為碳黑、石墨或焦炭粉。技術(shù)人員應(yīng)理解,按照本發(fā)明的鑄造粉末不必嚴(yán)格是粉末狀的,而是可以至少部分或甚至完全以其他形式存在,例如作為顆?;蛘咭钥招那虻男问剑诒匾獣r甚至以液態(tài)的形式。按照本發(fā)明的鑄造熔渣應(yīng)該在固化的過程中具有基本上非晶結(jié)構(gòu),即,鑄造熔渣中非晶比重應(yīng)為至少60%,優(yōu)選至少70%,更優(yōu)選至少80%。具有至少90%的非晶比重的熔渣具有特別好的特性。較高的非晶比重對于獲得良好的潤滑特性和均勻的熱傳導(dǎo)而言是重要的。在制造具有≥1重量%的Al含量的鋼的情況下,按照本發(fā)明的鑄造熔渣是特別有利的,因為該鑄造熔渣即使在具有≥1重量%的Al含量的鋼中也是化學(xué)穩(wěn)定的?;瘜W(xué)穩(wěn)定是指,熔渣在鑄造過程中不會與溶解在鋼熔體中的鋁反應(yīng)并且其化學(xué)組成幾乎保持不變。這提高了過程可靠性以及產(chǎn)品質(zhì)量。即使在額外地具有例如≥15重量%的高M(jìn)n含量的鋼中,在使用按照本發(fā)明的鑄造熔渣的條件下仍可以實現(xiàn)高的過程可靠性。具有≥15重量%的Mn含量的鋼比較低Mn含量的鋼具有明顯更低的液相線溫度。對于具有≥15重量%的Mn含量的鋼而言典型的液相線溫度為1400-1430℃。具有≥1重量%的Al含量和額外地具有例如≥0.2重量%的高的鈦含量的鋼在過程中具有這樣的問題,即,不僅Al作為化學(xué)活性元素存在,而且Ti也以較高的含量作為化學(xué)活性元素存在。用于制造這類鋼所使用的鑄造熔渣必須相對于AL和Ti具有良好的化學(xué)穩(wěn)定性。在按照本發(fā)明的鑄造熔渣正是這樣。鈦是一種化學(xué)活性元素并且能夠通過其結(jié)合連接在Si和Mn上的氧而從熔渣中吸取Si或Mn。在增高的二氧化鈦含量的情況下,可形成鈦鈣氧化化合物(TiO2-CaO),其促進(jìn)鑄渣的結(jié)晶固化。為了防止這個問題,有利的是在按照本發(fā)明的鑄造粉末中不添加例如氧化錳和氧化鐵的相應(yīng)組分。因此,這些組分不是有意添加的,而是可能作為不期望的伴生元素存在于按照本發(fā)明的鑄造粉末中并因此存在于本發(fā)明的鑄造熔渣中。按照本發(fā)明的鑄造熔渣組成可以進(jìn)一步包含堿金屬氧化物,堿土金屬氧化物或過渡金屬氧化物。因此,按照本發(fā)明的鑄造熔渣組成可以包含以下組分中的一種或多種:≤5.0重量%的TiO2;≤5.0重量%的MgO;≤3.0重量%的MnO;≤2.0重量%的FeO。因此,所述的優(yōu)選鑄造熔渣組成可以額外地包含以下組分中的一種或多種:≤5.0重量%的TiO2;≤5.0重量%的MgO;≤3.0重量%的MnO;≤1.0重量%的Fe2O3;≤1.0重量%的FeO。Ti02可以添加到按照本發(fā)明的鑄造粉末中。然而,在鑄造粉末中Ti02的含量不應(yīng)該大于5.0重量%,因為高于該數(shù)值的Ti02比重將與鋼熔體中存在的鋁反應(yīng)。游離氧將結(jié)合鋁,從而使熔渣可能額外地吸收Al203。該熔渣系統(tǒng)將不再是化學(xué)穩(wěn)定的,即,不再能提供CaO與Al203的目標(biāo)最佳比例。此外,在Ti02比重>5重量%時,元素形式的鈦可以轉(zhuǎn)移到鋼熔體中并且不期望地改變其化學(xué)組成。在鑄造粉末中可以含有作為伴生元素的MgO、MnO、Fe203、FeO,但不是為了調(diào)整鑄造熔渣的性能而有意地加入。在優(yōu)選的實施方式中,按照本發(fā)明的鑄造熔渣包括以下成分:33-48重量%的CaO;23-43重量%的Al2O3;7-13重量%的Fˉ(氟離子);3-6.5重量%的SiO2;7-12重量%的Na2O;2-5重量%的Li2O;≤3重量%的TiO2;≤1.5重量%的MgO;≤1.0重量%的MnO;≤1重量%的FeO。所述的優(yōu)選的鑄造粉末組成在不計算揮發(fā)性組分的條件下包括以下組分:40-60重量%的預(yù)熔化的鋁酸鈣;15-30重量%的含氟化物的組分,優(yōu)選CaF2;3-6重量%的SiO2;7-12重量%的Na2O;2-5.5重量%的Li2O;≤10.5重量%的Al2O3;≤15重量%的碳;≤3.0重量%的TiO2;≤1.0重量%的MgO;≤1.0重量%的MnO;≤1.0重量%的Fe2O3;≤1.0重量%的FeO。針對以上給出的鑄造熔渣和鑄造粉末的組成而給定的重量說明是分別相對于鑄造熔渣組成或鑄造粉末組成的成分的總量而言的。以按照本發(fā)明的鑄造熔渣和鑄造粉末組成的氟離子或者含氟化物的組分可以分別以常見的氟化物的形式而加入,例如堿金屬的氟化物、堿土金屬的氟化物或者過渡金屬的氟化物,特別是以從CaF2、MgF2、NaF、LiF的組合中選出的氟化物和這些氟化物中的至少兩個或更多個組成的混合物的形式。在按照本發(fā)明的鑄造熔渣和鑄造粉末的各個特別優(yōu)選的實施方式中,氟離子或者含氟化物的成分份額來自CaF2(也稱為氟石)。已發(fā)現(xiàn)特別有利的是含有鋁酸鈣(CaO-AL203)和CaF2成分的鑄造粉末的組成,從而改善由其產(chǎn)生的鑄造熔渣的特性的穩(wěn)定性并因此特別是還改善Al合金鋼的制造的過程可靠性。這種CaO-AL203-CaF2三元混合物的成分不與鋼中所含在的鋁進(jìn)行任何反應(yīng),從而確保了鑄造粉末的化學(xué)穩(wěn)定性以及由其產(chǎn)生的鑄造熔渣在鑄造過程中恒定的特性。投入使用的鑄造粉末的精確的組成可以變化并且另外與現(xiàn)有的條件相適應(yīng),例如與鋼的組成或者與鑄造方法的類型相適應(yīng)。另外,原則上還存在這樣的可能性,即,將三氧化硼(B203)用作為鑄造粉末添加劑。存在于粉末或熔渣中的三氧化硼可以通過存在于鋼中的鋁按照以下的反應(yīng)方程而還原:還原后的硼可以作為不期望的伴生元素而引入到熔體中。為了防止這樣,在此處描述的鑄造粉末組成和鑄造熔渣組成中優(yōu)選免去了硼。為了優(yōu)化功能特性、例如在鋼和硬模之間鑄造縫隙中的潤滑特性,可以使鑄造熔渣的組成與待鑄的鋼種的液相線溫度相適應(yīng)。這例如通過調(diào)整鑄造粉末中的助熔劑(比如氧化鈉(Na20)和/或氧化鋰(Li20))的限定含量和/或含氟化物的成分的含量而完成。例如,在具有例如1500-1530℃的較高液相線溫度的鋼種的鑄造過程中,可以在鑄造熔渣中設(shè)置Na20含量為5-11重量%,Li20含量為約2-3重量%,F(xiàn)-含量為8-10.5重量%,Na20、Li20和F-的總和優(yōu)選<25重量%。為了防止熔渣的粘度變得過低,Na20、Li20和F-的總量應(yīng)當(dāng)<25重量%。在另一方面,本發(fā)明因此還涉及一種用于具有高液相線溫度的鋼的鑄造熔渣組成,其具有以下成分:30-50重量%的CaO;20-45重量%的Al2O3;8-10.5重量%的Fˉ(氟離子);3-6.5重量%的SiO2;5-11重量%的Na2O;2-3重量%的Li2O;≤3重量%的TiO2;≤5重量%的MgO;≤3重量%的MnO;≤2重量%的FeO。所屬的鑄造粉末組成在不計算揮發(fā)組分的情況下包括:40-60重量%的預(yù)熔化的鋁酸鈣;10-30重量%的含氟化物的組分,優(yōu)選以CaF2的形式;3-6.5重量%的SiO2;5-11重量%的Na2O;2-3重量%的Li2O;≤10.5重量%的Al2O3;≤15重量%的碳;≤3.0重量%的TiO2;≤5.0重量%的MgO;≤3.0重量%的MnO;≤1.0重量%的Fe2O3;≤1.0重量%的FeO。在一個優(yōu)選的實施方式中,用于具有高液相線溫度的鋼的鑄造熔渣組成包括以下成分:33-48重量%的CaO;23-43重量%的Al2O3;8-10.5重量%的Fˉ(氟離子);3-5重量%的SiO2;5-11重量%的Na2O;2-3重量%的Li2O;≤3重量%的TiO2;≤1.5重量%的MgO;≤1.0重量%的MnO;≤1.0重量%的FeO。所屬的優(yōu)選的鑄造粉末組成在不計算揮發(fā)組分的情況下包括:40-60重量%的預(yù)熔化的鋁酸鈣;10-25重量%的含氟化物的組分,優(yōu)選以CaF2的形式;3-5重量%的SiO2;5-11重量%的Na2O;2-3重量%的Li2O;≤8重量%的Al2O3;≤5重量%的碳;≤3.0重量%的TiO2;≤1.0重量%的MgO;≤1.0重量%的MnO;≤1.0重量%的Fe2O3;≤1.0重量%的FeO。對于具有較低液相線溫度(例如1400-1430℃)的鋼,可以特別考慮具有9-15重量%的Na20含量,4-5重量%的Li20含量和12.5-15重量%的F-含量的鑄造熔渣,其中,Na20、Li20和F-的總和優(yōu)選≥25重量%。在此,對于具有相對高的助熔劑含量的情況,測得的粘度向低溫偏移大約100℃(圖2)。在另一方面,本發(fā)明因此還涉及一種用于具有較低液相線溫度的鋼的鑄造熔渣組成,其含有以下成分:30-50重量%的CaO;20-45重量%的Al2O3;12.5-15重量%的Fˉ(氟離子);3-6.5重量%的SiO2;9-15重量%的Na2O;4-5重量%的Li2O;≤3重量%的TiO2;≤5重量%的MgO;≤3重量%的MnO;≤2重量%的FeO。所屬的鑄造粉末在不計算揮發(fā)組分的情況下包括以下成分:40-60重量%的預(yù)熔化的鋁酸鈣;15-30重量%的含氟化物的組分,優(yōu)選以CaF2的形式;3-6.5重量%的SiO2;9-15重量%的Na2O;3-5重量%的Li2O;≤10重量%的Al2O3;≤15重量%的碳;≤3重量%的TiO2;≤5重量%的MgO;≤3重量%的MnO;≤1重量%的Fe2O3;≤1重量%的FeO。在一個優(yōu)選的實施方式中,用于具有較低液相線溫度的鋼的根據(jù)本發(fā)明的鑄造熔渣組成包括以下成分:33-48重量%的CaO;23-43重量%的Al2O3;12.5-15重量%的Fˉ(氟離子);3-5重量%的SiO2;11-15重量%的Na2O;3-5重量%的Li2O;≤3重量%的TiO2;≤1.5重量%的MgO;≤1重量%的MnO;≤1重量%的FeO。所屬的優(yōu)選的鑄造粉末組成在不計算揮發(fā)組分的情況下包括:40-60重量%的預(yù)熔化的鋁酸鈣;15-30重量%的含氟化物的組分,優(yōu)選以CaF2的形式;3-5重量%的SiO2;11-15重量%的Na2O;3-5重量%的Li2O;≤10重量%的Al2O3;≤15重量%的碳;≤3.0重量%的TiO2;≤1.5重量%的MgO;≤1.0重量%的MnO;≤1.0重量%的Fe2O3;≤1.0重量%的FeO。鑄造熔渣的另一個重要的特性是其熱傳導(dǎo)性。在鑄造間隙內(nèi),這種熱傳導(dǎo)性決定了從鋼到硬模的熱傳遞。熱導(dǎo)率主要受到鑄造熔渣的結(jié)晶行為的影響。在此重要的是,鑄造熔渣是非晶固化還是結(jié)晶固化?;诠杷徕}的典型的鑄造熔渣主要是非晶固化或在快速冷卻的過程中形成非晶組分和結(jié)晶組分。鑄造熔渣的非晶部分有利于潤滑特性并確保更強的熱傳遞。在包晶固化的鋼的鑄造過程中,為了防止縱向裂紋而期望較低的熱傳遞。如果鑄造熔渣的非晶/結(jié)晶比例和與之相關(guān)的鑄造熔渣的熱導(dǎo)率與鋼種相適應(yīng),則可以通過具有相對高的結(jié)晶比重的鑄造熔渣來實現(xiàn)這種較低的熱傳遞。通過助熔劑(Na20、Li20、F-)的含量實現(xiàn)了這種適應(yīng)。較高的助熔劑的比重同時導(dǎo)致鑄造熔渣中較高的非晶比重。最高6.5重量%的Si02的加入避免了在鑄造熔渣中過高的非晶比重。因此,在本發(fā)明的優(yōu)選的實施方式中,在上述組成中,成分Si02的含量≤6重量%、優(yōu)選≤5.5重量%、特別優(yōu)選≤5重量%。添加較小的Ti02含量實現(xiàn)了在上述鑄造粉末組成中進(jìn)一步降低Si02含量。Ti02同樣有利于鑄造熔渣的非晶比重的形成并另外相對于與鋼中所存在的Al的反應(yīng)而言在熱力學(xué)上比Si02更加穩(wěn)定。在降低Si02的同時加入Ti02的情況下,使鑄造熔渣的粘度保持不變(圖3)。在另一方面,本發(fā)明因此還涉及一種鑄造熔渣組成,其含有以下成分:30-50重量%的CaO;20-45重量%的Al2O3;8-15重量%的Fˉ(氟離子);3-5重量%的SiO2;5-15重量%的Na2O;2-5重量%的Li2O;1.5-5重量%的TiO2;≤5重量%的MgO;≤3重量%的MnO;≤2重量%的FeO。所屬的鑄造粉末的組成在不計算揮發(fā)組分的情況下包括以下成分:40-60重量%的預(yù)熔化的鋁酸鈣;10-30重量%的含氟化物的組分,優(yōu)選以CaF2的形式;3-5重量%的SiO2;5-15重量%的Na2O;2-5重量%的Li2O;≤10重量%的Al2O3;≤15重量%的碳;1.5-5重量%的TiO2;≤5重量%的MgO;≤3重量%的MnO;≤1重量%的Fe2O3;≤1重量%的FeO。在一個優(yōu)選的實施方式中,按照本發(fā)明的鑄造熔渣組成包括以下成分:33-48重量%的CaO;23-43重量%的Al2O3;8-13重量%的Fˉ(氟離子);3-4重量%的SiO2;8-13重量%的Na2O;3-5重量%的Li2O;1.5-3重量%的TiO2;≤1.5重量%的MgO;≤1重量%的MnO;≤1重量%的FeO。所屬的優(yōu)選的鑄造粉末具有這樣的組成,即,其在不計算揮發(fā)組分的情況下包括以下成分:50-60重量%的預(yù)熔化的鋁酸鈣;15-25重量%的含氟化物的組分,優(yōu)選以CaF2的形式;3-4重量%的SiO2;8-13重量%的Na2O;3-5重量%的Li2O;≤10重量%的Al2O3;≤15重量%的碳;1.5-3重量%的TiO2;≤1.5重量%的MgO;≤1.0重量%的MnO;≤1重量%的Fe2O3;≤1重量%的FeO。按照本發(fā)明的鑄造熔渣的特征特別是在于,其對于鋼中的鋁部分不表現(xiàn)出或僅表現(xiàn)出很小的反應(yīng)性,從而拓寬了可鑄鋼種的范圍并且還可以可靠地制造具有較高含量的鋁或較高含量的鋁和錳的鋼。在使用含有該鑄造粉末的鋼產(chǎn)品的情況下這最后還促使質(zhì)量的改善。本發(fā)明的另一個方面涉及一種在使用上述鑄造粉末的條件下用于鋼鑄造的方法。結(jié)合以上按照本發(fā)明的鑄造粉末所描述的所有優(yōu)選的實施方式相應(yīng)地也適用于按照本發(fā)明的鋼鑄造的方法并在此不再復(fù)述。優(yōu)選用于鋼鑄造的方法按照一個連續(xù)的方法、特別是按照連鑄法進(jìn)行。在一個優(yōu)選的實施方式中,本發(fā)明涉及一種按照本發(fā)明的方法,該方法用于鑄造具有≥1重量%、優(yōu)選≥1.5重量%、特別優(yōu)選≥3.0重量%、最優(yōu)選≥5.0重量%的鋁含量的鋼。在另一個優(yōu)選的實施方式中,本發(fā)明涉及一種按照本發(fā)明的方法,該方法用于鑄造具有≥15重量%、優(yōu)選≥17.5重量%、特別優(yōu)選≥20重量%的錳含量的鋼。在另一個優(yōu)選的實施方式中,本發(fā)明涉及一種按照本發(fā)明的方法,該方法用于鑄造具有≥0.2重量%、優(yōu)選≥0.5重量%的鈦含量的鋼。在一個優(yōu)選的實施方式中,本發(fā)明涉及一種按照本發(fā)明的方法,該方法用于鑄造具有≥1重量%、優(yōu)選≥1.5重量%、特別優(yōu)選≥3.0重量%、最優(yōu)選≥5.0重量%的鋁含量和一定情況下具有≥15重量%、優(yōu)選≥17.5重量%、特別優(yōu)選≥20重量%的錳含量和在一定情況下具有≥0.2重量%、優(yōu)選≥0.5重量%的鈦含量的鋼。附圖說明圖1示出了成分的CaO、Al203和CaF2有利的組成。圖2示出了對于不同的助熔劑含量,使用Fa.的高溫旋轉(zhuǎn)粘度計測量的一些鑄造熔渣的粘度與溫度的相關(guān)性。圖3示出了在減少Si02比重和提高Ti02比重的條件下測得的一些鑄造熔渣的粘度(Pr.9和Pr.25具有約5重量%的Si02;Pr.42和Pr.44具有約4重量%的Si02和約2重量%的Ti02)。以下借助例子說明本發(fā)明。這些說明僅是示例性的而并不限制一般的發(fā)明構(gòu)思。具體實施方式研究了表1所示組成的各種鑄造粉末。含C的樣品5、19、32、40和44在600℃下預(yù)煅燒8小時并在氬氣環(huán)境下在1500℃熔化。不含C的樣品不進(jìn)行預(yù)煅燒,而是直接在氬氣環(huán)境下在1500℃下熔化。在熔化之后,將樣品各自在1500℃下保持15分鐘并隨后為了在室溫下在空氣中進(jìn)行冷卻而澆鑄在具有室溫的鋼基材上。冷卻后的樣品具有最大15mm、在樣品表面上不同的厚度。對于隨后的研究,選擇固化的爐渣層為5至7mm厚的位置。在這些位置上,借助光學(xué)顯微鏡確定在樣品橫截面中的非晶固化比重和/或結(jié)晶固化比重。表2中給出了所產(chǎn)生的熔渣的化學(xué)組成和非晶比重。通過X射線熒光法在樣品上分別三重的方式測定鑄造粉末和鑄造熔渣的化學(xué)組成。氟離子的含量通過根據(jù)DIN51723和DIN51727的加氫熱解測定,隨后根據(jù)DINENISO10304的離子色譜法測定。在相應(yīng)的樣品制備之后通過按照DINENISO11885的ICPOS測量來測定Na20濃度。此外,使具有樣品31、40和48的組成的鑄造粉末樣品與所選的熔體接觸并在氬氣環(huán)境下在1450℃-1550℃下保持15分鐘(參見表3)。然后分開地澆鑄熔渣和熔體并分別進(jìn)行分析。通過差熱分析(DTA)測定相關(guān)的液相線溫度。可調(diào)整的鑄造熔渣組成和非晶鑄造熔渣的比重與表2中的樣品31、40和48的結(jié)果相同。因此能夠證明,先前研究的鑄造熔渣系統(tǒng)即使在與鋼熔體接觸的情況下也是代表性。在表1中給出的按照本發(fā)明的鑄造粉末的組成因此以突出的方式適用于制造所追求的鑄造熔渣。表1:在不考慮揮發(fā)性組分的條件下以重量%表示的鑄造粉末的組成,和在預(yù)熔化的鋁酸鈣中CaO相對于Al203的比例(無量綱)表2:以重量%(標(biāo)準(zhǔn)化)表示的實驗室熔渣的組成以及非晶固化的比重盡管沒有主動地向所屬的鑄造粉末加入二氧化硅,在熔渣樣品26中存在0.7重量%的二氧化硅。對此的原因在于,在熔爐和鉗鍋所使用的耐火材料中存在少量的二氧化硅,其在試驗期間擴散到熔化的鑄造熔渣中。表3:在接觸試驗內(nèi)所使用的鋼熔體的例子(基于鐵的鋼以及以重量%計的重要合金元素,以℃計的液相線溫度Tliq)鋼種Tliq.CMnAlTi試驗熔渣的組成鋼115020.221.671.46-Pr.40(表2)鋼214200.4018.801.20-Pr.31(表2)鋼315160.05-5.000.5Pr.48(表2)當(dāng)前第1頁1 2 3