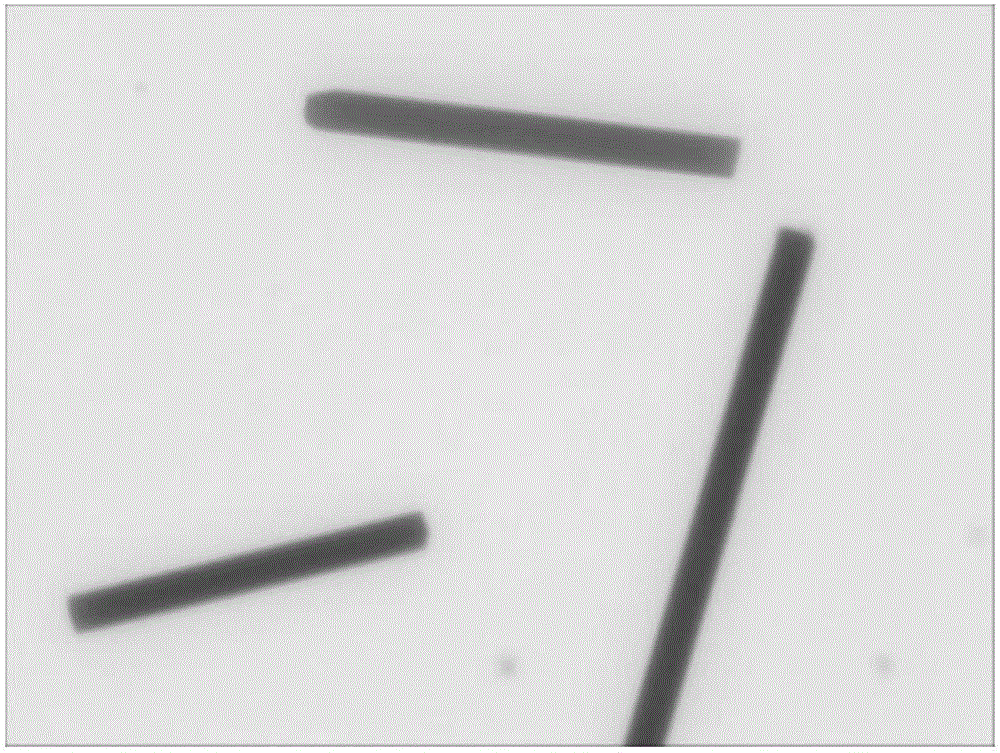
本發(fā)明涉及一種汽車及機(jī)械傳動(dòng)制動(dòng)領(lǐng)域內(nèi)使用的摩擦材料,具體涉及一種有機(jī)纖維增強(qiáng)型摩擦材料及其制備方法。
背景技術(shù):
:摩擦材料屬于一種復(fù)合材料,有骨架纖維、粘接劑、性能調(diào)節(jié)劑、填料組成,增強(qiáng)纖維是摩擦材料類復(fù)合材料必需的骨架原料,按所用纖維分三大類摩擦材料:石棉基摩擦材料、半金屬基摩擦材料、無石棉非金屬基摩擦材料。但石棉纖維可能致癌、半金屬基摩擦材料有易生銹、易傷摩擦對(duì)偶的缺點(diǎn)。以玻纖、人造巖棉、硅酸鹽礦物纖維為主要增強(qiáng)纖維的無石棉非金屬摩擦材料,是目前制動(dòng)用摩擦材料行業(yè)內(nèi)全球通用技術(shù)。而以玻纖、人造巖棉、硅酸鹽礦物纖維為增強(qiáng)纖維的無石棉非金屬摩擦材料雖然材料強(qiáng)度高、熱穩(wěn)定性好,但存在著易引起皮膚過敏、產(chǎn)生騷癢的現(xiàn)象,部分敏感人群甚至出現(xiàn)紅腫、發(fā)炎的嚴(yán)重問題。NAO類摩擦材料雖用部分有機(jī)纖維,但為滿足材料增強(qiáng)效果和熱穩(wěn)定需求,也在其中采用部分陶瓷類纖維,故同樣存在著引起皮膚過敏的問題。隨著人們對(duì)環(huán)保要求越來越高,這一問題正變得突出,因此,如何以合適的、不會(huì)刺激皮膚過敏的原料復(fù)合來制造摩擦材料,同時(shí)保持合適的強(qiáng)度、摩擦性能和熱穩(wěn)定性是研發(fā)環(huán)境友好型摩擦材料的關(guān)鍵。技術(shù)實(shí)現(xiàn)要素:本發(fā)明的目的是提供一種有機(jī)纖維增強(qiáng)型摩擦材料,該摩擦材料不會(huì)刺激皮膚過敏,同時(shí)能保證足夠的強(qiáng)度、耐磨性能和熱穩(wěn)定性能,且環(huán)境友好、不易生銹,適合推廣應(yīng)用。為實(shí)現(xiàn)上述目的,本發(fā)明采用的技術(shù)方案為:一種有機(jī)纖維增強(qiáng)型摩擦材料,各組分所占質(zhì)量百分比包括:芳綸2-4%,預(yù)氧絲3-6%,膠粉4-8%,樹脂8-14%,氧化鋁3-6%,石墨5-10%,調(diào)節(jié)劑5-10%,填料50-60%。上述方案中,所述預(yù)氧絲經(jīng)常規(guī)的硅烷偶聯(lián)劑浸潤(rùn)處理和剪切備用,其長(zhǎng)度為1-2mm,直徑為10-20μm。上述方案中,所述預(yù)氧絲為聚丙烯腈預(yù)氧絲;聚丙烯腈預(yù)氧絲由聚丙烯腈在空氣介質(zhì)下經(jīng)預(yù)氧化而制成;屬于用有機(jī)纖維加工生產(chǎn)碳纖維的初級(jí)產(chǎn)品,相對(duì)聚丙烯腈有更高的耐熱性。上述方案中,采用的纖維全部為有機(jī)柔性纖維,不含玻纖、人造巖棉、陶瓷纖維、類無機(jī)剛性纖維和金屬纖維。本發(fā)明通過研究發(fā)現(xiàn),現(xiàn)有摩擦材料在制造、使用過程中導(dǎo)致人員皮膚過敏的原因在于玻纖類纖維(如玻璃纖維、人造巖棉、硅酸鹽礦物纖維等),其纖維直徑一般在12um左右,呈剛性(見圖1),生產(chǎn)和使用過程產(chǎn)生的含纖維揚(yáng)塵粘附到皮膚上,極易透過毛孔刺入皮膚,從而引起皮膚保護(hù)性應(yīng)激反應(yīng)。同時(shí),本發(fā)明通過研究發(fā)現(xiàn)有機(jī)纖維具有很好的柔性,不會(huì)刺入皮膚,但其熱穩(wěn)定性差,400℃溫度下的燒蝕量約為85%,其高溫摩擦性能下降過快。目前也有采用有機(jī)纖維高溫石墨化加工而成的碳纖維的技術(shù)方案,雖能解決材料的耐熱性能,但失去了有機(jī)纖維的柔性(見圖2),同樣存在剛性過高刺入皮膚導(dǎo)致過敏的問題。本發(fā)明采用的預(yù)氧絲(聚丙烯腈纖維高溫碳化而成的預(yù)氧絲),只對(duì)有機(jī)纖維表面進(jìn)行碳化,大幅提高了纖維的耐熱性(400度燒蝕量約20%);同時(shí)其內(nèi)核仍為有機(jī)纖維,保持了有機(jī)纖維的柔性,不會(huì)刺入皮膚引起過敏,可有效平衡皮膚刺激性和熱穩(wěn)定性。上述方案中,所述調(diào)節(jié)劑為金屬硫化物,但不僅僅局限為金屬硫化物;用于穩(wěn)定摩擦材料的熱穩(wěn)定性能。上述方案中,所述調(diào)節(jié)劑可選用硫化鉬、硫化銅、硫化錫、硫化鐵、硫化亞鐵銅、硫化銻等中的一種或幾種。優(yōu)選的,所述金屬硫化物采用硫化銅、硫化銻和硫化鉬進(jìn)行組合而成:硫化銅的熔點(diǎn)為220℃,硫化銻的熔點(diǎn)為550℃,在摩擦高溫條件下起到無機(jī)粘接劑的效用,可有效平衡有機(jī)纖維的熱分解而導(dǎo)致的摩擦磨損性能下降的問題,同時(shí)硫化鉬作為高溫潤(rùn)滑劑,可有效改善摩擦材料的高溫磨損性能。上述方案中,所述填料為硫酸鋇、碳酸鈣中的一種或兩種。上述方案中,采用的氧化鋁用于調(diào)節(jié)摩擦材料的磨損性能;石墨用于調(diào)節(jié)摩擦材料的磨損性能。上述方案中,樹脂作為粘接劑,優(yōu)選采用硼酸改性的硼改性酚醛樹脂(硼酸改性酚醛樹脂),其耐氧化性能好,TGA(熱重分析)測(cè)試其600℃殘?zhí)悸蕿?0-65%,比普通酚醛樹脂高約50%,適合于本發(fā)明采用的全有機(jī)纖維體系。上述方案中膠粉作為增韌劑,優(yōu)選采用耐熱性高的丁腈膠粉。上述一種有機(jī)纖維增強(qiáng)型摩擦材料的制備方法,包括以下步驟:1)按配方要求稱取各原料,各組分所占質(zhì)量百分比包括:芳綸2-4%,預(yù)氧絲3-6%,膠粉4-8%,樹脂8-14%,氧化鋁3-6%,石墨5-10%,調(diào)節(jié)劑5-10%,填料42-60%。2)將稱取的原料投入犁耙式混料機(jī)中混合均勻,得混合原料;3)將混合原料置于模具中進(jìn)行熱壓成型;4)將步驟3)所得成型產(chǎn)品置于烘箱中進(jìn)行年深度交聯(lián)固化處理,冷卻得所述有機(jī)纖維增強(qiáng)型摩擦材料。上述方案中,所述熱壓成型工藝條件為:壓力為190-210kg/cm2,溫度為150-160℃,保壓時(shí)間為4-6min。上述方案中,所述深度交聯(lián)固化處理工藝為:由室溫加熱至145-150℃保溫50-60min,繼續(xù)升溫至155-160℃保溫50-60min,再升溫至175-180℃保溫5-6h;最后自然冷卻至室溫。本發(fā)明采用預(yù)氧絲作為增強(qiáng)骨架材料,由于纖維表面光滑無分枝,與一起復(fù)合的粘接劑、調(diào)節(jié)劑等功能性組分的吸附性不好,不易使復(fù)合材料混拌均勻,工藝穩(wěn)定性差,因此研究引入少量芳綸纖維進(jìn)行輔助,芳綸纖維有很好的分枝和比表面積,可以輔助增強(qiáng)復(fù)合摩擦材料的混拌均勻性及原料分布的穩(wěn)定性。本發(fā)明提供了一種全新的摩擦材料配方體系,采用的增強(qiáng)纖維全部為有機(jī)纖維,利用芳綸纖維和預(yù)氧絲的特性,同時(shí)配合其他功能性組分制備所述摩擦材料;優(yōu)選引入硫化銅作為調(diào)節(jié)劑,利用硫化銅的220℃低熔點(diǎn)特性,在200-300℃下所發(fā)生的化學(xué)反應(yīng)起到無機(jī)粘接劑效用,可有效補(bǔ)償有機(jī)纖維熱分解所導(dǎo)致的摩擦材料性能下降的短板,同時(shí)優(yōu)選硼酸改性的硼改性酚醛樹脂,其耐氧化性能好,600℃殘?zhí)剂勘绕胀ǚ尤渲呒s50%;本發(fā)明得到的有機(jī)纖維增強(qiáng)型摩擦材料,完全不同于現(xiàn)有的無石棉摩擦材料、半金屬摩擦材料或NAO類摩擦材料,不存在纖維引起的皮膚過敏問題,同時(shí)具有優(yōu)良的熱摩擦性能,解決了困撓摩擦材料行業(yè)多年的難題;可達(dá)到摩擦材料所需的各項(xiàng)性能要求,具有摩擦磨損性能優(yōu)良、環(huán)境友好、不生銹的多重特點(diǎn)。本發(fā)明的有益效果為:1)本發(fā)明所述摩擦材料在生產(chǎn)和使用過程中,克服了無石棉摩擦材料等摩擦材料易引起皮膚過敏的問題,符合健康、環(huán)保的發(fā)展理念。2)本發(fā)明摩擦材料經(jīng)實(shí)車驗(yàn)證,具有工藝和產(chǎn)品性能穩(wěn)定的特點(diǎn),可適用于各種工況包括山區(qū)高溫工作環(huán)境。3)本發(fā)明摩擦材料不存在半金屬材質(zhì)摩擦材料易生銹的問題。附圖說明圖1為市售玻璃纖維的顯微形態(tài)照片。圖2為高溫石墨化加工而成的碳纖維的顯微形態(tài)照片。圖3為本發(fā)明實(shí)施例1~3采用的預(yù)氧絲的500倍顯微照片。圖4為本發(fā)明實(shí)施例1~3采用的芳綸的500倍顯微照片。具體實(shí)施方式為了更好地理解本發(fā)明,下面結(jié)合實(shí)例進(jìn)一步闡明本發(fā)明的內(nèi)容,但本發(fā)明不僅僅局限于下面的實(shí)施例。以下實(shí)施例中,采用的預(yù)氧絲的長(zhǎng)度為1-2mm,直徑為10-20μm,其顯微照片見圖3;它由聚丙烯腈在空氣介質(zhì)下經(jīng)預(yù)氧化而制成聚丙烯腈預(yù)氧絲,再浸潤(rùn)于硅烷偶聯(lián)劑后經(jīng)剪切而成;由南京緯達(dá)復(fù)合材料有限公司提供。采用的芳綸由杜邦公司提供,其顯微照片見圖4。采用的硼改性酚醛樹脂經(jīng)TGA(熱重分析)測(cè)試其600℃殘?zhí)悸蕿?0-65%,比普通酚醛樹脂高約50%;由濟(jì)南圣泉海沃斯化工有限公司提供。實(shí)施例1~3一種有機(jī)纖維增強(qiáng)型摩擦材料,其制備方法包括以下步驟:1)按表1所述配比要求稱取各原料;2)將稱取的原料投入犁耙式混料機(jī)中混合均勻,得混合原料;3)將混合原料置于模具中進(jìn)行熱壓成型;壓力為200kg/cm2,溫度為150℃,保壓時(shí)間為5分鐘。4)將步驟3)所得成型產(chǎn)品置于烘箱中,由室溫加熱至150℃保溫1h,繼續(xù)升溫至160℃保溫1h,再升溫至180℃保溫6h;最后自然冷卻至室溫取出,得所述有機(jī)纖維增強(qiáng)型摩擦材料。對(duì)比例中采用聚丙烯腈纖維和紡綸制備摩擦材料,采用的原料配比見表1,制備方法同實(shí)施例1~3。表1實(shí)施例1~3所述有機(jī)纖維增強(qiáng)型摩擦材料和對(duì)比例的原料配比組成(質(zhì)量百分比)實(shí)施例1實(shí)施例2實(shí)施例3對(duì)比例硼改性酚醛樹脂8101413丁腈膠粉8544芳綸4222預(yù)氧絲3640聚丙烯腈纖維0004硫化鉬1300硫化銅7266硫化銻2022氧化鋁3466石墨51077硫酸鋇24382324碳酸鈣35203232總計(jì)100100100100將實(shí)施例1~3制備的有機(jī)纖維增強(qiáng)型摩擦材料和對(duì)比例所得摩擦材料分別應(yīng)用于制動(dòng)系統(tǒng),采用汽車制動(dòng)襯片GB5763-2008標(biāo)準(zhǔn)進(jìn)行測(cè)試,結(jié)果如表2所示。其中現(xiàn)通用技術(shù)是指典型的汽車廠原裝無石棉摩制動(dòng)摩擦材料性能。表2實(shí)施例1~3所得有機(jī)纖維增強(qiáng)型摩擦材料和對(duì)比例的性能測(cè)試結(jié)果測(cè)試結(jié)果表明本實(shí)施例制備的摩擦材料具有較好的摩擦磨損性能、熱衰退性能和強(qiáng)度,性能同典型的汽車廠原裝摩擦片相當(dāng),高溫摩擦磨損性能明顯優(yōu)于對(duì)比例中的聚丙烯腈纖維所制的材料,非常適合用于制動(dòng)用摩擦材料。皮膚刺激性試驗(yàn)采用實(shí)施例1~3所述摩擦材料的原料進(jìn)行皮膚刺激性測(cè)試,具體步驟如下:從生產(chǎn)車間隨機(jī)確定操作工10人,5男5女,職能部門員工10人,5男5女,共計(jì)20人參與試驗(yàn)。20人分別裸手(手上皮膚無任何護(hù)具)插入已按配比混好材料的料桶,攪動(dòng)3周(圓周),5小時(shí)后查詢參試人員手上皮膚感覺。調(diào)查結(jié)果如下表3:表3實(shí)施例1~3所得有機(jī)纖維增強(qiáng)型摩擦材料的皮膚刺激性測(cè)試結(jié)果由表3可以看出,本發(fā)明采用的原料體系無人出現(xiàn)皮膚刺激過敏現(xiàn)象,而現(xiàn)有通用技術(shù)和配方則高達(dá)91%人員出現(xiàn)受刺激反饋,其中34%的人員出現(xiàn)較明顯的過敏反饋。證明本發(fā)明可有效解決對(duì)皮膚刺激的問題。以上所述僅為本發(fā)明的優(yōu)選實(shí)施方式,應(yīng)當(dāng)指出,對(duì)于本領(lǐng)域的普通技術(shù)人員來說,在不脫離本發(fā)明創(chuàng)造構(gòu)思的前提下,做出若干改進(jìn)和變換,這些都屬于本發(fā)明的保護(hù)范圍。當(dāng)前第1頁1 2 3