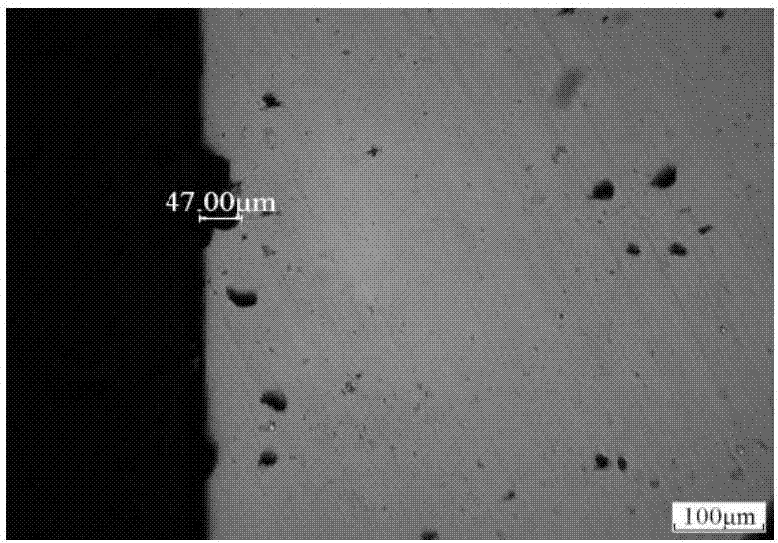
本發(fā)明涉及一種金屬材料綜合性能的提高方法,尤其是一種7000系超高強鋁合金強度、塑性以及耐腐蝕性能提高方法,具體地說是一種綜合利用過時效處理、兩道次等通道轉(zhuǎn)角擠壓(ecap)加工、熱壓縮、預(yù)回復(fù)、固溶、時效處理技術(shù)來提高超高強鋁合金綜合性能的方法。
背景技術(shù):
:al-zn-mg-cu(7000)系鋁合金以其易加工性、低密度、高比強度、優(yōu)秀的抗腐蝕性能、高導(dǎo)電率、高散熱性和通用性強等特點,在航空航天、武器裝備制造以及交通運輸?shù)刃袠I(yè)獲得非常廣泛的運用。隨著中國制造業(yè)的進一步升級,現(xiàn)代工業(yè)對高強度鋁合金的性能要求越來越高,從需求側(cè)提高了人們優(yōu)化7000系鋁合金綜合性能的熱情。但是該合金的不足之處是脆性大、塑性差、耐腐蝕性能低,如何在現(xiàn)有的科學(xué)技術(shù)的基礎(chǔ)上,尋找出一系列調(diào)控優(yōu)化鋁合金微觀組織與綜合性能的方法已經(jīng)成為研究的焦點。為了擴大7000系鋁合金的適用范圍,必須通過成分設(shè)計或者調(diào)整加工工藝來提高該系鋁合金的強度、塑性以及耐腐蝕性能。ecap加工作為強烈塑性變形(spd)的一種,主要是運用強烈剪切塑性變形的方法去調(diào)控材料內(nèi)部的組織結(jié)構(gòu),細(xì)化晶粒,從而制備塊狀超細(xì)晶金屬材料,提高材料的強度、塑性以及抗腐蝕性等性能。由于材料經(jīng)ecap加工后,其橫截面積幾乎不發(fā)生變化,因此可以對材料進行多道次ecap加工。ecap加工有多種方式,其中c方式ecap加工是指工件每道次ecap加工完成后,在下道次ecap加工前,將工件繞軸線轉(zhuǎn)動180°。bc方式ecap加工是指工件每道次ecap加工完成后,在下道次ecap加工前,將工件繞軸線轉(zhuǎn)動90°,轉(zhuǎn)動方向不做改變。過時效處理能夠降低基體材料的固溶度,便于塑性變形,而且能夠生成尺寸在1μm左右的第二相,在后續(xù)強烈塑形變形加工中可以有效抑制釘扎位錯,細(xì)化組織。熱壓縮變形加工能夠進一步增大ecap加工后材料的的塑性變形,調(diào)節(jié)材料組織結(jié)構(gòu)。預(yù)回復(fù)可以促進回復(fù),抑制后續(xù)固溶過程中產(chǎn)生的再結(jié)晶以及晶粒長大,對于調(diào)控材料組織及性能具有重要作用。結(jié)合兩道次ecap加工,并且綜合應(yīng)用過時效、熱壓縮變形加工、預(yù)回復(fù)、固溶、時效處理技術(shù)對于提高超高強鋁合金的綜合性能具有重要的實際意義。但是,迄今為止尚未有一種綜合過時效-兩道次ecap加工-熱壓縮變形加工-預(yù)回復(fù)-固溶-時效工藝來提高超高強鋁合金綜合性能的方法可供使用,在一定程度上限制了超高強鋁合金的應(yīng)用以及鋁合金制造業(yè)的發(fā)展。技術(shù)實現(xiàn)要素:本發(fā)明的目的是針對現(xiàn)有的7000系超高強鋁合金(例如al-zn-mg-cu)塑性差、抗腐蝕性能差的問題,發(fā)明一種結(jié)合兩道次ecap加工來提高超高強鋁合金綜合性能的方法。本發(fā)明的技術(shù)方案是:一種結(jié)合兩道次ecap加工提高超高強鋁合金綜合性能的方法,其特征是它包括前處理和后處理兩個階段;所述的前處理依次為過時效、兩道次等通道轉(zhuǎn)角擠壓(ecap)加工和熱壓縮變形加工,所述的后處理為預(yù)回復(fù)、固溶、時效強化熱處理。所述的過時效處理是將超高強鋁合金加熱至400±10℃,然后保溫48±1h。所述的兩道次ecap加工是將經(jīng)過過時效處理后的超高強鋁合金先進行420±10℃×2±0.5h的保溫處理后放入ecap模具中進行一道次擠壓,并且在一道次擠壓加工后需將試樣繞軸線旋轉(zhuǎn)90°或者180°,然后再將試樣進行420±10℃×2±0.5h的保溫處理,然后放入ecap模具中進行二道次擠壓。此處的420±10℃是指溫度介于410℃~430℃之間的任一溫度,2±0.5h是指介于1.5h~2.5h之間的任意時間,下同。在進行兩道次ecap加工擠壓過程中為防止試樣開裂,需在試樣外包一層銅套對試樣進行保護。所述的熱壓縮變形加工時先將試樣加熱至420±10℃,并且保溫2±0.5h,然后進行壓下率不小于50%的熱壓處理。所述的預(yù)回復(fù)處理是將熱壓縮變形處理后的試樣進行(250±10)℃×(24±1)h+(300±10)℃×(6±1h)+(350±10)℃×(6±1)h+(400±10)℃×(6±1)h的預(yù)回復(fù)退火處理。所述的固溶處理工藝為(450±10)℃×(2±0.5)h+(460±10)℃×(2±0.5)h+(470±10)℃×(2±0.5)h,并且固溶后需要對試樣立即進行水淬處理。所述的時效處理工藝為(121±5)℃×(5±0.5)h+(153±5)℃×(16±1)h。本發(fā)明的有益效果:(1)經(jīng)本發(fā)明過時效-兩道次ecap加工-熱壓縮變形加工-預(yù)回復(fù)-固溶-時效工藝處理的合金與只進行預(yù)回復(fù)-固溶-時效工藝處理的合金,其強度大幅度提高的同時材料的塑性基本保持原有水平或者有所提高。如實施例一中材料的抗拉強度由650.5mpa上升到778.4mpa,材料的強度大約提高了19.7%,同時材料的塑性基本保持。強度提高的原理主要在于兩道次ecap加工產(chǎn)生的強烈剪切塑性變形可以累積較大的應(yīng)變,能夠有效細(xì)化晶粒,調(diào)控材料的組織結(jié)構(gòu),再結(jié)合過時效、熱壓縮變形加工以及預(yù)回復(fù)對材料組織結(jié)構(gòu)的調(diào)控作用,從而能促材料強度的大幅度提高。(2)經(jīng)本發(fā)明方法處理的合金,其抗晶間腐蝕性能和抗剝落腐蝕性能都得到顯著提高,抗腐蝕性得到了較大程度的改善。如實施例一中材料的最大晶間腐蝕深度由81.5μm減小到47.0μm,并且剝落腐蝕等級由pc上升到pb,材料的抗腐蝕性能得到了極大地改善。(3)本發(fā)明為后續(xù)提高超高強鋁合金的強度、塑性以及抗腐蝕性能提供了參考。附圖說明圖1是只經(jīng)過預(yù)回復(fù)-固溶-時效工藝處理的實施例一合金的晶間腐蝕分析圖片。圖2是經(jīng)過本發(fā)明過時效-兩道次ecap加工-熱壓縮變形加工-預(yù)回復(fù)-固溶-時效工藝處理的實施例一合金的晶間腐蝕分析圖片。圖3是只經(jīng)過預(yù)回復(fù)-固溶-時效工藝處理的實施例二合金的晶間腐蝕分析圖片。圖4是經(jīng)過本發(fā)明過時效-兩道次ecap加工-熱壓縮變形加工-預(yù)回復(fù)-固溶-時效工藝處理的實施例二合金的晶間腐蝕分析圖片。具體實施方式下面結(jié)合附圖和實施例對本發(fā)明作進一步的說明。實施例一一種提高超高強鋁合金(al-12.18zn-3.31mg-1.43cu-0.20zr-0.0435sr)綜合性能的方法,它包括以下步驟:首先,對工件進行切割取樣,然后進行過時效處理,過時效工藝為(400±10)℃×(48±1)h,然后將試樣加熱到420±10℃(可通過對模具進行預(yù)熱加以實現(xiàn)),并且保溫2±0.5h后,再放入ecap模具中進行兩道次c方式ecap加工。在一道次ecap加工后需將試樣繞軸線旋轉(zhuǎn)180°,然后再將試樣加熱到420±10℃(可通過對模具進行預(yù)熱加以實現(xiàn)),并且保溫2±0.5h后,進行第二道次ecap加工。在擠壓過程中為防止試樣開裂,可在試樣外包一層銅套對試樣進行保護。ecap加工完成后需將試樣加熱到420±10℃,并且保溫2±0.5h,然后在液壓機上進行熱壓縮變形加工,熱壓縮變形加工的壓下率為50%,完成前處理。前處理完成后需對試樣進行預(yù)回復(fù)退火處理,預(yù)回復(fù)工藝為250±10℃×24±1h+300±10℃×6±1h+350±10℃×6±1h+400±10℃×6±1h。固溶處理采用分級固溶處理,處理工藝為450±10℃×2±0.5h+460±10℃×2±0.5h+470±10℃×2±0.5h,固溶處理完成后需立即對試樣進行水淬處理,而后進行121±5℃×5±0.5h+153±5℃×16±1h的時效處理。最后對其硬度、導(dǎo)電率、強度進行測量,對其進行xrd、ebsd分析,進行晶間腐蝕、剝落腐蝕實驗以得到各方面的性能指標(biāo),并與只進行預(yù)回復(fù)-固溶-時效處理的試樣對比。本實施例合金實測質(zhì)量分?jǐn)?shù)為。實驗結(jié)果如下:過時效-兩道次c方式ecap-熱壓縮-預(yù)回復(fù)-固溶-時效預(yù)回復(fù)-固溶-時效延伸率(%)6.77.7抗拉強度(mpa)778.4650.5硬度(hv)234.1207.2導(dǎo)電率(%iacs)30.232.7晶間腐蝕深度(μm)47.081.5剝落腐蝕等級pbpc平均晶粒尺寸(μm)18.166.9實驗結(jié)果表明“過時效-兩道次c方式ecap加工-熱壓縮-預(yù)回復(fù)-固溶-時效處理”對al-12.18zn-3.31mg-1.43cu-0.20zr-0.0435sr鋁合金的綜合性能有著較大幅度的提高。其中,材料的抗拉強度由650.5mpa上升到778.4mpa,材料的強度大約提高了19.7%,強度得到了大幅度的提高;材料的晶間腐蝕深度由81.5μm減小到47.0μm,并且剝落腐蝕等級由pc上升到pb,材料的抗腐蝕性能得到了極大地改善;材料的平均晶粒尺寸大大減小,由66.89μm減小到18.10μm,兩道次ecap加工的晶粒細(xì)化效果非常明顯,并且材料的其他性能指標(biāo)基本保持原有水平。未經(jīng)本發(fā)明處理的實施例一合金的晶間腐蝕圖片如圖1所示,經(jīng)過本發(fā)明處理的實施例一合金的晶間腐蝕圖片如圖2所示。實施例二一種提高超高強鋁合金(al-12.18~12.51zn-2.85~3.31mg-1.43~2.83cu-0.18~0.20zr-0.0435~0.0598sr)綜合性能的方法,它包括以下步驟:將質(zhì)量分?jǐn)?shù)為的超高強鋁合金切割取樣后進行過時效處理,過時效工藝為400±10℃×48±1h,然后將試樣放入ecap模具中進行兩道次bc方式ecap加工。在一道次ecap加工后需將試樣繞軸線旋轉(zhuǎn)90°,然后再進行第二道次ecap加工。在二道次ecap加工前需將試樣進行420±10℃×2±0.5h的保溫處理,并對模具進行預(yù)熱。在擠壓過程中為防止試樣開裂,需在試樣外包一層銅套對試樣進行保護。ecap加工完成后需將試樣加熱到420±10℃,并且保溫2±0.5h,然后在液壓機上進行熱壓縮變形加工,熱壓縮變形加工的壓下率為55%。前處理完成后需對試樣進行預(yù)回復(fù)退火處理,預(yù)回復(fù)工藝為250℃×24h+300℃×6h+350℃×6h+400℃×6h。固溶處理采用分級固溶處理,處理工藝為450℃×2h+460℃×2h+470℃×2h,固溶處理完成后需立即對試樣進行水淬處理,而后進行121℃×5h+153℃×16h的時效處理。最后對其硬度、導(dǎo)電率、強度進行測量,對其進行xrd、ebsd分析,進行晶間腐蝕、剝落腐蝕實驗以得到各方面的性能指標(biāo),并與只進行預(yù)回復(fù)-固溶-時效處理的試樣對比。本實施例合金實測質(zhì)量分?jǐn)?shù)為al-12.51zn-2.85mg-2.83cu-0.18zr-0.0598sr。實驗結(jié)果如下:過時效-兩道次bc方式ecap-熱壓縮-預(yù)回復(fù)-固溶-時效預(yù)回復(fù)-固溶-時效延伸率(%)6.76.3抗拉強度(mpa)688.2603.9硬度(hv)215.7218.2導(dǎo)電率(%iacs)32.330.2晶間腐蝕深度(μm)42.765.3剝落腐蝕等級pbea平均晶粒尺寸(μm)9.111.3實驗結(jié)果表明“過時效-兩道次bc方式ecap加工-熱壓縮-預(yù)回復(fù)-固溶-時效處理”對al-12.18zn-3.31mg-1.43cu-0.20zr-0.0435sr合金的綜合性能有著較大幅度的提高。其中,材料的抗拉強度由603.9mpa上升到688.2mpa,強度大約提高了14%,材料的強度有了較大的提高;材料的延伸率由6.3%上升到6.7%,提高了大約6%,材料的塑性有了一定的改善;材料的晶間腐蝕深度由65.3μm減小到42.7μm,剝落腐蝕等級由ea上升到pb,材料的抗腐蝕能力有了大幅度的提高,并且材料的其他性能指標(biāo)基本保持原有水平。未經(jīng)本發(fā)明處理的實施例二合金的晶間腐蝕圖片如圖3所示,經(jīng)過本發(fā)明處理的實施例二合金的晶間腐蝕圖片如圖4所示。本發(fā)明未涉及部分(如ecap加工用模具等)均與現(xiàn)有技術(shù)相同或可采用現(xiàn)有技術(shù)加以實現(xiàn)。當(dāng)前第1頁12