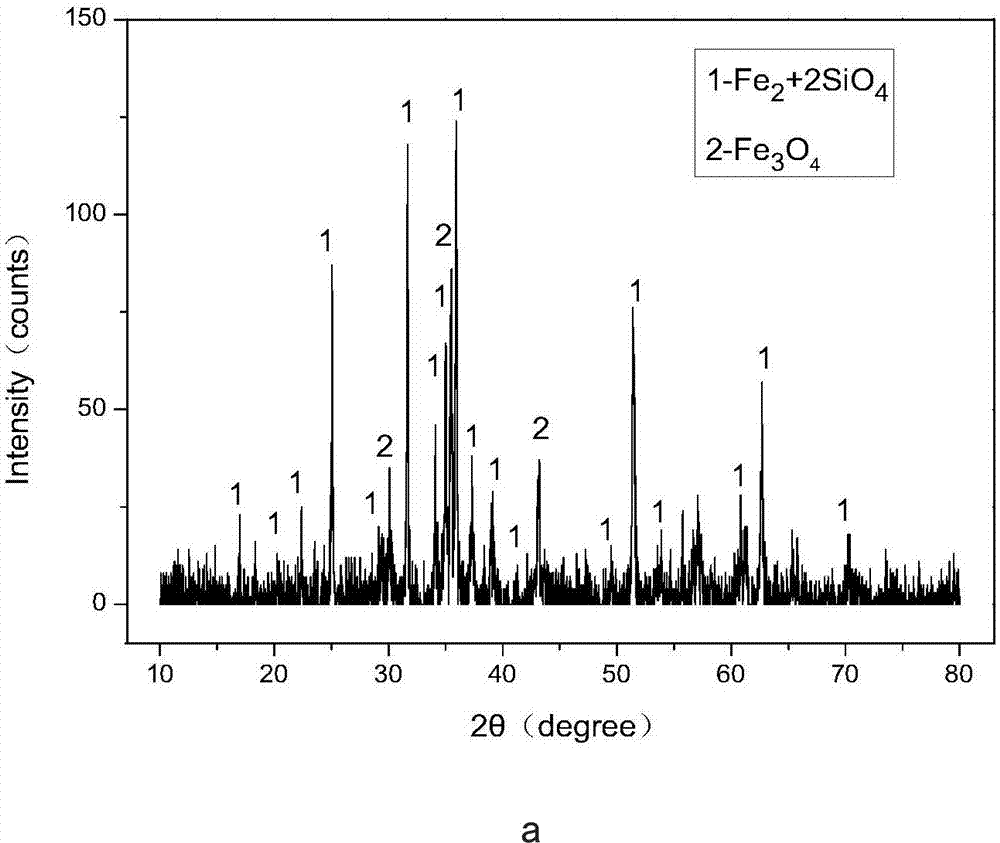
本發(fā)明屬于冶金工程與環(huán)境工程交叉領(lǐng)域,涉及一種復合添加劑分解回收銅渣中有價金屬的方法。
背景技術(shù):
:近年來我國銅產(chǎn)量迅猛增長,超越智利躍居世界第一,但同時也產(chǎn)生大量廢渣,據(jù)統(tǒng)計我國每年產(chǎn)生約300萬噸銅渣,且仍然在逐年遞增。目前這些廢渣大量堆存,不僅占用土地資源,而且還造成大量有價金屬資源的浪費;銅渣是屬于典型的feo-sio2系渣,渣中含鐵40%,遠高于冶煉鐵礦29.1%的平均品位,為一種潛在的鐵資源,但該類渣中鐵80%以上以鐵橄欖石相存在,嵌布粒度極細,硅鐵難以分開,致使該類硅鐵復合氧化物中鐵得不到合理的回收,一直作為工業(yè)不可用鐵而廢棄不用。我國雖然是世界上鋼鐵生產(chǎn)大國,但原料大多依賴國外進口,所以鐵礦資源匱乏?,F(xiàn)有研究報道中,銅渣中有價金屬的回收主要通過氧化/還原焙燒-磁選得到鐵精礦、直接還原-磁選得到鐵精礦、直接還原熔煉得到鐵合金。銅渣中鐵主要以鐵橄欖石物相存在,鐵橄欖石性質(zhì)穩(wěn)定,在1100℃以下用氧氣進行氧化焙燒或用一氧化碳/碳進行還原焙燒,但鐵橄欖石轉(zhuǎn)化為四氧化三鐵或三氧化二鐵的轉(zhuǎn)化率均不高,因此氧化/還原焙燒-磁選處理鐵橄欖石類冶金廢渣效果不理想;李燕春等(201510572205.1)在二氧化硫加氧氣的氣氛下,與氧氣氣氛焙燒相比,雖然對溫度要求低些,但是轉(zhuǎn)化效果較差,主要物相為fe2o3,磁選效果差,經(jīng)過強磁選所得鐵精礦品位為66%。楊慧芬等以褐煤為還原劑,采用直接還原-磁選方法對含鐵39.96%的水淬銅渣進行回收鐵的研究,獲得鐵回收率為81.01%的直接還原鐵粉,回收率較低。閆方興等人利用電石渣中的氧化鈣和銅渣中的二氧化硅等組分來生產(chǎn)硅鈣鐵合金,分兩段熔煉,且熔煉溫度高達1600℃以上,能耗很高。綜上所述,目前銅渣中鐵資源的回收利用缺乏環(huán)境友好、分離效果高的方法,使得渣中鐵資源得不到有效回收利用,這是冶金和環(huán)境領(lǐng)域函待解決的一個難題,迫切需要一種節(jié)能、高效、流程短的工藝方法回收銅渣中伴生的鐵資源。技術(shù)實現(xiàn)要素:本發(fā)明的目的在于提供一種利用復合添加劑分解銅渣的方法,在低二次污染和更低溫度下一步高效分解轉(zhuǎn)換成磁鐵礦。一種復合添加劑分解回收銅渣中有價金屬的方法:將氧化鈣與三氧化二鐵和銅渣按照一定的比例混合球磨,然后在一定溫度和惰性氣氛條件下焙燒,得到含有四氧化三鐵的焙燒產(chǎn)物。所述的方法:焙燒產(chǎn)物冷卻后進行破碎磁選,所得磁選產(chǎn)物為磁鐵礦。所述的方法:銅渣來源于銅冶煉廠熔煉緩冷工序。所述的方法:氧化鈣、三氧化二鐵和銅渣的質(zhì)量比為7:40:(8-12),優(yōu)選比例為7:40:10。所述的方法:氧化鈣、三氧化二鐵和銅渣混合球磨1-5小時,轉(zhuǎn)速300-500r/min,優(yōu)選球磨時間為2小時,轉(zhuǎn)速400r/min。所述的方法:所述焙燒溫度為不低于700℃,優(yōu)選700-1100℃,進一步優(yōu)選1000℃。所述的方法:所述焙燒的時間60-180min,優(yōu)選時間為120min。所述的方法;所述惰性氣氛條件為氮氣和/或氬氣。本發(fā)明反應過程中發(fā)生的主要化學反應式為:cao+fe2sio4+2fe2o3=casio3+2fe3o4相對現(xiàn)有技術(shù),本發(fā)明的技術(shù)方案帶來的有益效果:1、本發(fā)明的分解回收銅渣中有價金屬的方法,可使銅渣磁選率達到86%,渣中鐵的回收率達到95%以上。2、本發(fā)明的方法所需溫度較低,且無廢氣產(chǎn)生,有利于環(huán)境保護。3、本發(fā)明的方法可實現(xiàn)銅渣約40%的減量化,大大提高了銅渣二次資源化利用。附圖說明圖1為本發(fā)明方法的工藝流程圖;圖2為銅渣分解前后的xrd對比圖,a為銅渣分解前的xrd圖,b為銅渣分解后的xrd圖;圖3為磁選精礦的xrd圖;圖4為銅渣分解前后的sem對比圖,a為銅渣分解前的sem圖,b為銅渣分解后的sem對比圖。具體實施方式下面結(jié)合具體實施例對本發(fā)明做進一步詳細說明,此處所描述的具體實施例僅用于解釋本發(fā)明,并不用于限制本發(fā)明。實施例1以湖南某銅冶煉廠的熔煉緩冷銅渣為原料,其化學成分如下表所示:feosicaznalcus43.3123.5316.144.383.642.501.771.32將氧化鈣、三氧化二鐵和銅渣按照質(zhì)量比為7:40:10稱取試樣,放入星形球磨機中,球磨時間為2h,轉(zhuǎn)速為400r/min,將球磨混合料裝入氣氛管式爐中,通入惰性氣體在1000℃條件下進行高溫固相反應120min,冷卻后進行磁選,所得產(chǎn)物為磁鐵礦,銅渣磁選率為86%,渣中鐵的回收率為95%。實施例2將氧化鈣、三氧化二鐵和銅渣按照質(zhì)量比為7:40:12稱取試樣,放入星形球磨機中球磨時間為3h,轉(zhuǎn)速為500r/min,將球磨混合料裝入氣氛管式爐中,通入惰性氣體在1100℃條件下進行高溫固相反應90min,冷卻后進行磁選,所得產(chǎn)物為磁鐵礦,銅渣磁選率為84%,渣中鐵的回收率為92%。實施例3將氧化鈣、三氧化二鐵和銅渣按照質(zhì)量比為7:40:8稱取試樣,放入星形球磨機中球磨時間為1h,轉(zhuǎn)速為300r/min,將球磨混合料裝入氣氛管式爐中,通入惰性氣體在900℃條件下進行高溫固相反應120min,冷卻后進行磁選,所得產(chǎn)物為磁鐵礦,銅渣磁選率為85%,渣中鐵的回收率為94.3%。實施例4將氧化鈣、三氧化二鐵和銅渣按照質(zhì)量比為7:40:9稱取試樣,放入星形球磨機中球磨時間為1.5h,轉(zhuǎn)速為350r/min,將球磨混合料裝入氣氛管式爐中,通入惰性氣體在700℃條件下進行高溫固相反應160min,冷卻后進行磁選,所得產(chǎn)物為磁鐵礦,銅渣磁選率為82%,渣中鐵的回收率為88.8%。實施例5將氧化鈣、三氧化二鐵和銅渣按照質(zhì)量比為7:40:11稱取試樣,放入星形球磨機中球磨時間為2h,轉(zhuǎn)速為450r/min,將球磨混合料裝入氣氛管式爐中,通入惰性氣體在800℃條件下進行高溫固相反應180min,冷卻后進行磁選,所得產(chǎn)物為磁鐵礦,銅渣磁選率為83%,渣中鐵的回收率為90%。當前第1頁12