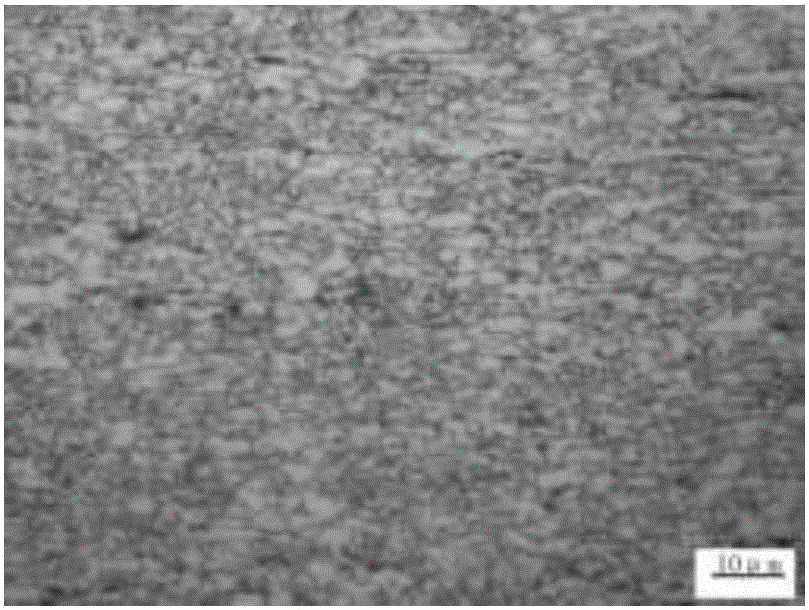
本發(fā)明涉及一種低合金高強(qiáng)度鋼技術(shù),具體說,涉及一種屈服強(qiáng)度600MPa級(jí)薄規(guī)格廂體鋼帶及其制造方法
背景技術(shù):
:隨著國內(nèi)商用汽車工業(yè)的快速發(fā)展,用戶對(duì)減輕汽車重量、降低油耗、提高汽車結(jié)構(gòu)件強(qiáng)度以及安全性能等提出了更高的要求。高強(qiáng)度,薄規(guī)格成為了廂體用鋼發(fā)展的趨勢,汽車廂體用鋼主要用來制造商用汽車的車廂等,通過加入Nb、Ti微合金元素,得到極為細(xì)小的晶粒組織和沉淀強(qiáng)化,使鋼材強(qiáng)韌性獲得極高的匹配,同時(shí)具有良好的成型性能和焊接性能。薄規(guī)格鋼帶(2.0~3.0mm)在廂體用鋼中占有較大的市場比重,市場銷量較好。中國公開號(hào)CN103614625A的專利文獻(xiàn)公開了“一種590MPa級(jí)熱軋汽車廂體用鋼板”,鋼板的化學(xué)成分按重量百分比為C:0.12~0.14%、Si:0.20~0.30%、Mn:1.40~1.60%、P:≤0.015%、S:≤0.010%、Nb:0.01~0.03%、Ti:0.07~0.10%,余量為Fe和不可避免的雜質(zhì),其屈服強(qiáng)度>450MPa,抗拉強(qiáng)度>590MPa,該專利與本專利鋼板強(qiáng)度不是同一級(jí)別,本專利屈服強(qiáng)度>620MPa,抗拉強(qiáng)度>660MPa而且該專利只闡述了實(shí)驗(yàn)室的生產(chǎn)方法。中國公開號(hào)CN104561791A的專利文獻(xiàn)公開了“800MPa級(jí)別汽車箱體用鋼及其生產(chǎn)方法”,所采用的板坯的質(zhì)量百分比含量為:C:0.08~0.12%、Si:0.20~0.40%、Mn:1.40~1.60%、P≤0.025%、S≤0.010%、V:0.040~0.060%、Ti:0.090~0.120%、Als≥0.015%、N≤0.004%,其余為Fe和不可避免的不純物。該專利與本專利鋼板強(qiáng)度不是同一級(jí)別,而且本專利不含V,合金化體系不同,成本更低。中國公開號(hào)CN104141093A的專利文獻(xiàn)公開了“屈服強(qiáng)度達(dá)700MPa的汽車廂體用帶鋼及其軋制方法”,化學(xué)成分重量百分比為:C:0.06~0.12%;Si:0.2~0.4%;V<0.005%;Mn:0.5~1.6%;Ti:0.06~0.14%;其余為鐵和其它不可避免的雜質(zhì)。本專利不含V,該專利與本專利合金化體系不同,成本更低。但在,現(xiàn)有廂體用鋼在生產(chǎn)過程中容易出現(xiàn)甩尾和板型不良的問題,生產(chǎn)困難較大。技術(shù)實(shí)現(xiàn)要素:本發(fā)明所解決的技術(shù)問題是提供一種屈服強(qiáng)度600MPa級(jí)薄規(guī)格廂體鋼帶,具有良好冷彎成型性能。技術(shù)方案如下:一種屈服強(qiáng)度600MPa級(jí)薄規(guī)格廂體鋼帶,化學(xué)成分按重量百分比包括:C:0.06~0.08%、Si:≤0.20%、Mn:1.5~1.7%、P:≤0.020%、S:≤0.010%、Alt:0.10~0.04%、Nb:0.025~0.035%、Ti:0.08~0.10%,余量為Fe和不可避免的雜質(zhì)。進(jìn)一步:Si:0.10~0.20%,Mn:1.53~1.65%,P:0.012~0.015%、S:0.006~0.009%,Nb:0.025~0.033%,Ti:0.080~0.095%,Alt:0.02~0.04。本發(fā)明所解決的另一個(gè)技術(shù)問題是提供一種屈服強(qiáng)度600MPa級(jí)薄規(guī)格廂體鋼帶的制造方法,鋼帶具有良好冷彎成型性能。技術(shù)方案如下:一種屈服強(qiáng)度600MPa級(jí)薄規(guī)格廂體鋼帶的制造方法,包括轉(zhuǎn)爐冶煉、LF精煉、連鑄、板坯加熱、機(jī)架粗軋、機(jī)架精軋、層流冷卻、卷??;轉(zhuǎn)爐冶煉過程中,轉(zhuǎn)爐底吹采用全程吹氬模式,終點(diǎn)一次命中,以減少因補(bǔ)吹導(dǎo)致鋼水增氮;LF精煉進(jìn)一步脫氧、脫硫、去除夾雜、調(diào)整成分及溫度,控制吹氬強(qiáng)度,按照前期強(qiáng)、中期較強(qiáng)、后期弱的原則制定吹氬曲線;加熱過程中,加熱溫度控制在1270℃~1290℃,加熱時(shí)間控制在180-240min,保證合金元素的充分固溶,鋼板坯溫度均勻;軋制采用兩階段控制軋制,單道次相對(duì)壓下率至少有兩道次以上大于20%;精軋時(shí)嚴(yán)格控制各道次變形量,精軋開軋溫度≥950℃,開軋厚度為37~42mm,終軋溫度865-895℃;軋后鋼帶進(jìn)入層流冷卻系統(tǒng),卷取溫度565-595℃;得到屈服強(qiáng)度600MPa級(jí)薄規(guī)格廂體鋼帶,化學(xué)成分按重量百分比包括:C:0.06~0.08%、Si:≤0.20%、Mn:1.5~1.7%、P:≤0.020%、S:≤0.010%、Alt:0.10~0.04%、Nb:0.025~0.035%、Ti:0.08~0.10%,余量為Fe和不可避免的雜質(zhì)。進(jìn)一步:連鑄過程中,連鑄機(jī)采用直弧形連鑄機(jī),采用凝固末端動(dòng)態(tài)輕壓下、動(dòng)態(tài)二冷技術(shù),通過恒溫、恒拉速工藝。進(jìn)一步:鋼帶為晶粒細(xì)小且均勻的鐵素體+貝氏體組織。進(jìn)一步:連鑄后板坯厚度為230mm,鋼帶厚度為2.5~3.0mm。與現(xiàn)有技術(shù)相比,本發(fā)明技術(shù)效果包括:通過低碳微合金化成分設(shè)計(jì),得到一種屈服強(qiáng)度≥620MPa、抗拉強(qiáng)度≥680Mpa、延伸率≥14%,且具有良好冷彎成型性能的薄規(guī)格高強(qiáng)度汽車廂體用鋼帶。本發(fā)明通過加入Nb、Ti微合金元素,得到極為細(xì)小的晶粒組織和沉淀強(qiáng)化使鋼材強(qiáng)韌性獲得極高的匹配,同時(shí)具有良好的成型性能和焊接性能??梢灶A(yù)計(jì),薄規(guī)格鋼帶(2.0~3.0mm)在廂體用鋼中占有較大的市場比重,市場銷量較好??梢蕴嵘摦a(chǎn)品結(jié)構(gòu),帶來可觀的經(jīng)濟(jì)效益,預(yù)計(jì)每年能夠新增經(jīng)濟(jì)效益20萬元左右。附圖說明圖1本發(fā)明中實(shí)施例3鋼板的金相組織圖;圖2本發(fā)明中實(shí)施例3鋼板寬(雙)冷彎性能(d=0)示意圖。具體實(shí)施方式下面參考示例實(shí)施方式對(duì)本發(fā)明技術(shù)方案作詳細(xì)說明。然而,示例實(shí)施方式能夠以多種形式實(shí)施,且不應(yīng)被理解為限于在此闡述的實(shí)施方式;相反,提供這些實(shí)施方式使得本發(fā)明更全面和完整,并將示例實(shí)施方式的構(gòu)思全面地傳達(dá)給本領(lǐng)域的技術(shù)人員。屈服強(qiáng)度600MPa級(jí)薄規(guī)格廂體鋼帶的制造方法,采用的工藝流程具體包括:轉(zhuǎn)爐冶煉、LF精煉、連鑄、板坯加熱、機(jī)架粗軋、機(jī)架精軋、層流冷卻、卷取。步驟1:冶煉;采用經(jīng)過脫硫預(yù)處理的鐵水和優(yōu)質(zhì)廢鋼作為原料,轉(zhuǎn)爐底吹采用全程吹氬模式,終點(diǎn)一次命中,以減少因補(bǔ)吹導(dǎo)致鋼水增氮。LF(鋼包精煉爐)精煉,進(jìn)一步脫氧、脫硫、去除夾雜、調(diào)整成分及溫度,要嚴(yán)格控制吹氬強(qiáng)度,按照前期強(qiáng)、中期較強(qiáng)、后期弱的原則制定吹氬曲線,在保證脫氧、深脫硫、合金化的同時(shí),減少精煉過程的二次氧化和增氮。步驟2:連鑄;連鑄機(jī)為直弧形連鑄機(jī),采用凝固末端動(dòng)態(tài)輕壓下、優(yōu)化的動(dòng)態(tài)二冷技術(shù),通過恒溫、恒拉速工藝,減輕連鑄坯中心偏析、中心疏松、裂紋、振痕等缺陷,最終生產(chǎn)出230mm厚優(yōu)質(zhì)連鑄板坯。步驟3:加熱;在加熱爐中對(duì)鋼板坯加熱,充分保證鋼板坯加熱溫度和均熱時(shí)間。加熱溫度控制在1270℃~1290℃,加熱時(shí)間控制在180-240min,保證合金元素的充分固溶,鋼板坯溫度均勻。步驟4:軋制、冷卻、卷取。軋制采用兩階段控制軋制,即奧氏體再結(jié)晶區(qū)控制軋制(通常稱粗軋階段)和奧氏體非再結(jié)晶區(qū)控制軋制(通常稱精軋階段)。粗軋?jiān)赗1和R2粗軋機(jī)進(jìn)行,采用“3+3”道次,粗軋時(shí)加大道次變形量,單道次相對(duì)壓下率至少有兩道次以上控制在20%以上;精軋?jiān)贔1-F7精軋機(jī)進(jìn)行,精軋時(shí)嚴(yán)格控制各道次變形量,精軋開軋溫度≥950℃,開軋厚度為37~42mm,終軋溫度865-895℃;軋后鋼帶進(jìn)入層流冷卻系統(tǒng),卷取溫度565-595℃,得到晶粒細(xì)小且均勻的鐵素體+貝氏體組織。屈服強(qiáng)度600MPa級(jí)薄規(guī)格廂體鋼帶,化學(xué)成分按重量百分比為:C:0.06~0.08%、Si:≤0.20%、Mn:1.5~1.7%、P:≤0.020%、S:≤0.010%、Alt(全鋁):0.10~0.04%、Nb:0.025~0.035%、Ti:0.08~0.10%,余量為Fe和不可避免的雜質(zhì)。實(shí)施例1原料鐵水經(jīng)過鐵水深脫硫,轉(zhuǎn)爐頂?shù)状禑?,鋼包吹氬,LF爐外精煉及連鑄工藝得到表1所示化學(xué)成分重量百分比的230mm厚板坯。板坯加熱溫度1275℃,加熱時(shí)間185min,粗軋?jiān)赗1和R2粗軋機(jī)進(jìn)行,采用“3+3”道次,粗軋時(shí)加大道次變形量,單道次相對(duì)壓下率至少有兩道次以上控制在20%以上;精軋?jiān)贔1-F7精軋機(jī)進(jìn)行,精軋時(shí)嚴(yán)格控制各道次變形量,精軋開軋溫度1008℃,開軋厚度為38mm,終軋溫度888℃,成品鋼帶厚度2.5mm。軋后鋼帶進(jìn)入層流冷卻系統(tǒng),卷取溫度平均值589℃,最后即可得到所述鋼帶。實(shí)施例2實(shí)施方式同實(shí)施例1,其中加熱溫度為1271℃,保溫188分鐘,精軋開軋溫度1003℃,開軋厚度為39mm,終軋溫度890℃,成品鋼帶厚度2.75mm。軋后鋼帶進(jìn)入層流冷卻系統(tǒng),卷取溫度平均值588℃,最后即可得到所述鋼帶。實(shí)施例3實(shí)施方式同實(shí)施例1,其中加熱溫度為1270℃,保溫185分鐘;精軋開軋溫度989℃,開軋厚度為41mm,終軋溫度884℃,成品鋼帶厚度3.0mm。軋后鋼帶進(jìn)入層流冷卻系統(tǒng),卷取溫度平均值586℃,最后即可得到所述鋼帶。表1本發(fā)明實(shí)施例1~3的化學(xué)成分(wt%)實(shí)施例CSiMnPSNbTiAlt10.060.201.530.0120.0090.0250.0800.0220.070.161.600.0150.0080.0310.0840.0330.080.101.650.0130.0060.0330.0950.04對(duì)本發(fā)明實(shí)施例1~3的鋼板進(jìn)行力學(xué)性能檢驗(yàn),檢驗(yàn)結(jié)果見表2。表2本發(fā)明實(shí)施例1~3的鋼板的力學(xué)性能由表2可看出,采用本發(fā)明生產(chǎn)的高強(qiáng)度薄規(guī)格(2.0~3.0mm)汽車廂體用鋼帶強(qiáng)度和延伸率完全符合標(biāo)準(zhǔn)要求,且余量較大。如圖1所示,是本發(fā)明中實(shí)施例3鋼板的金相組織圖;如圖2所示,是本發(fā)明中實(shí)施例3鋼板寬(雙)冷彎性能(d=0)示意圖。鋼帶的晶粒組織極為細(xì)小,鋼帶的寬冷彎和雙冷彎試驗(yàn)表明本發(fā)明鋼帶具有優(yōu)良的冷彎成型性能,完全滿足用戶的加工使用要求。本發(fā)明所用的術(shù)語是說明和示例性、而非限制性的術(shù)語。由于本發(fā)明能夠以多種形式具體實(shí)施而不脫離發(fā)明的精神或?qū)嵸|(zhì),所以應(yīng)當(dāng)理解,上述實(shí)施例不限于任何前述的細(xì)節(jié),而應(yīng)在隨附權(quán)利要求所限定的精神和范圍內(nèi)廣泛地解釋,因此落入權(quán)利要求或其等效范圍內(nèi)的全部變化和改型都應(yīng)為隨附權(quán)利要求所涵蓋。當(dāng)前第1頁1 2 3