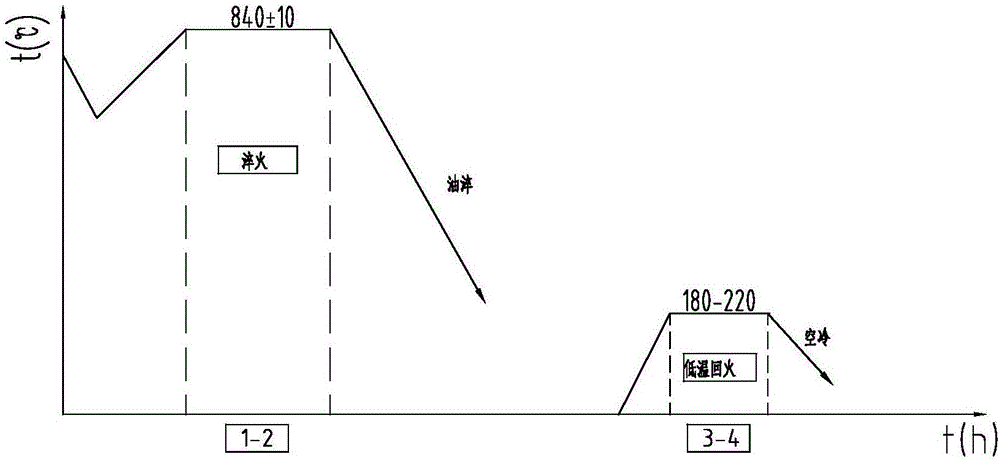
本發(fā)明涉及一種高合金滲碳鋼齒輪的淬火方法,屬于熱處理
技術(shù)領(lǐng)域:
。
背景技術(shù):
:齒輪是減速器及傳動機構(gòu)中常用的傳動零件之一,主要用來支承傳動零部件以及傳遞扭矩和承受載荷。在運轉(zhuǎn)過程中,齒輪相互嚙合的齒面之間既有滾動又有滑動,既受脈沖應(yīng)力又受交變彎曲應(yīng)力,而滲碳淬火仍是齒輪主要表面強化手段之一,因此齒輪需經(jīng)過熱處理以具有良好的硬度、耐磨性、高的彎曲疲勞強度和抗沖擊能力。近年來,隨著重載齒輪的發(fā)展,高合金滲碳鋼制齒輪能極大提高齒輪的心部韌性、表面耐磨性和疲勞強度,使得高合金滲碳鋼得到了普遍的運用,而高合金滲碳鋼的碳含量一般在0.10%~0.25之間,屬于低碳鋼,為了提高淬透性,保證心部強度,在滲碳鋼中加入各種合元素,如Ni、Cr、Mn、Mo等,同時還加入一定量的V、W、Ti等合金元素以細化晶粒,因此對齒輪的熱處理工藝方法也提出了更高的要求。目前,對于高合金滲碳鋼重載齒輪的熱處理,基本采用滲碳淬火表面強化的工藝方法,滲碳后的齒輪進行淬火處理,一般見圖2所示,將滲碳后的齒輪隨爐加熱至840±10℃保溫1~2h,出爐后熱油淬火,最后180~220℃下進行低溫回火,空冷至室溫。該方法雖能滿足一般齒輪的技術(shù)要求,但深入研究表明存在以下不足:滲碳淬火后表層馬氏體針較粗大,殘余奧氏體含量較多,齒輪表面硬度偏低,因此會降低齒輪的耐磨性、強韌性和綜合力學(xué)性能。技術(shù)實現(xiàn)要素:本發(fā)明的目的是提供一種高合金滲碳鋼齒輪的淬火方法,能有效細化齒輪表層馬氏體,減少殘余奧氏體含量,從而優(yōu)化齒輪表面的金相組織,同時提高其表面硬度、耐磨性、疲勞強度和塑韌性指標。本發(fā)明為達到上述目的的技術(shù)方案是:一種高合金滲碳鋼齒輪的淬火方法,其特征在于:包括以下步驟,⑴、第一次升溫保溫步驟:將滲碳后的齒輪隨爐升溫至860±10℃,保溫時間為2~3h;⑵、第一次降溫保溫步驟:將齒輪快速冷卻至780±10℃,保溫時間為3~4h;⑶、第二次升溫保溫步驟:再將齒輪快速升溫至840±10℃,保溫時間為2~3h;⑷、第二次降溫保溫步驟:將齒輪快速冷卻至700±10℃,保溫時間為3~4h;⑸、第三次升溫保溫步驟:再將齒輪快速升溫至820±10℃,保溫時間為2~3h;⑹、淬火冷卻步驟:將820±10℃狀態(tài)下的齒輪置入65~95℃的油液中迅速冷卻;⑺、回火步驟:將淬火后的齒輪放在回火爐內(nèi)加熱至180~220℃環(huán)境中進行低溫回火,保溫3~4h,出爐空冷至室溫。采用本發(fā)明的技術(shù)方案后,與現(xiàn)有技術(shù)相比具有以下優(yōu)點。1、本發(fā)明通過第一次升溫和降溫,先將齒輪隨爐加熱至860±10℃并保溫2~3h,先將齒輪表層的奧氏體析出碳化物轉(zhuǎn)變?yōu)閵W氏體和滲碳體,而心部的奧氏體則轉(zhuǎn)變成奧氏體和鐵素體,并通過快速冷卻保溫3~4h,使齒輪金相組織能得到很好的細化,鐵素體和滲碳體組織細小。2、本發(fā)明通過第二次升溫和降溫,先將齒輪快速升溫840±10℃并保溫2~3h,低于第一升溫溫度,能使齒輪表層極細長的碳化物極易溶解、擴散形成細小的顆粒狀碳化物,同時心部鐵素體組織則均勻化,使奧氏體中溶解的飽和碳化物更加細小,并通過快速的冷卻過程中,使齒輪表層得到均勻的珠光體和細小的顆粒狀碳化物,心部則得到均勻的珠光體和鐵素體。3、本發(fā)明經(jīng)第三次升溫保溫,使齒輪溫度保持在820±10℃,并在該狀態(tài)下的置入65~95℃的油液中迅速冷卻,使齒輪表層奧氏體中的碳含量因析出的碳化物而大大降低,淬火后形成了細針狀的馬氏體和彌散分布的細小顆粒狀碳化物,心部則形成了板條狀的馬氏體。本發(fā)明的淬火溫度低于常規(guī)淬火溫度,能在保證表面獲得細針狀馬氏體,因此具有高硬度的同時,減少淬火應(yīng)力,降低淬火變形。本發(fā)明通過合理設(shè)計整個工藝流程以及各流程中溫度、保溫時間、冷卻方式的選擇達到優(yōu)化高合金滲碳鋼齒輪的熱處理性能的目的,能有效細化晶粒,細化馬氏體針,降低表層殘余奧氏體含量,使高合金滲碳鋼齒輪力學(xué)性能得到大幅改善,塑韌性指標明顯提高,同時,高合金滲碳鋼齒輪鋼表面的耐磨性能也大幅提高,從而也提高了齒輪的疲勞強度和抗蝕性,提高齒輪的綜合力學(xué)性能。附圖說明下面結(jié)合附圖對本發(fā)明的實施例作進一步的詳細描述。圖1是本發(fā)明高合金滲碳鋼齒輪的淬火方法示意圖。圖2是現(xiàn)有高合金滲碳鋼齒輪淬火過程示意圖。具體實施方式見圖1所示,本發(fā)明的高合金滲碳鋼齒輪的淬火方法,包括以下步驟。⑴、第一次升溫保溫步驟:將滲碳后的齒輪隨爐升溫至860±10℃,保溫時間為2~3h,通過將齒輪加熱至860±10℃并保溫一段時間,使齒輪表層的奧氏體析出碳化物而轉(zhuǎn)變成奧氏體和滲碳體,心部的奧氏體則轉(zhuǎn)變成奧氏體和鐵素體。⑵、第一次降溫保溫步驟:將齒輪快速冷卻至780±10℃,保溫時間為3~4h,本發(fā)明齒輪快速冷卻的速度為≥1200℃/h,如冷卻的速度為1260℃/h,將齒輪從860±10℃降至780±10℃,通過快速冷卻,由于齒輪金相組織能得到很好的細化,使鐵素體和滲碳體組織細小。⑶、第二次升溫保溫步驟:再將齒輪快速升溫至840±10℃,保溫時間為2~3h,第二次升溫保溫步驟中,齒輪以≥900℃/h進行升溫,通過再次升溫至840±10℃并進行保溫,使齒輪表層極細長的碳化物極易溶解、擴散形成細小的顆粒狀碳化物,而心部鐵素體組織則均勻化,使奧氏體中溶解的飽和碳化物更加細小。⑷、第二次降溫保溫步驟:將齒輪快速冷卻至700±10℃,保溫時間為3~4h,本發(fā)明齒輪快速冷卻的速度為≥1200℃/h,如可在1260℃/h,通過再次冷卻,使齒輪表層得到均勻的珠光體和細小的顆粒狀碳化物,心部則得到均勻的珠光體和鐵素體。⑸、第三次升溫保溫步驟:再將齒輪快速升溫至820±10℃,保溫時間為2~3h,齒輪以≥900℃/h進行升溫,將齒輪加熱至淬火溫度。⑹、淬火冷卻步驟:將820±10℃狀態(tài)下的齒輪置入65~95℃的油液中迅速冷卻,在保證表面獲得細針狀馬氏體因此具有高硬度的同時,由于降低了淬火溫度,故能減少淬火應(yīng)力,降低淬火變形。⑺、回火步驟:將淬火后的齒輪放在回火爐內(nèi)加熱至180~220℃環(huán)境中進行低溫回火,保溫3~4h,出爐空冷至室溫,低溫回火的次數(shù)為兩次,以降低淬火應(yīng)力,并保持高硬度和高耐磨性。本發(fā)明在淬火完畢后,還可進行清洗步驟,清洗去除零部件表面油漬,且清洗液溫度控制在50~60℃,將齒輪放置在清洗液中清洗去除零部件表面油漬。本發(fā)明對采用12Cr2Ni4A制成的齒輪進行淬火,具體淬火工藝參數(shù)見表1所示,表1采用本發(fā)明淬火方法制得的樣件按標準TB/T2254-1991進行檢測,具體檢測數(shù)據(jù)見表2所示。表2項目實施例1實施例2實施例3實施例4實施例5實施例6馬氏體級別1級1級1級1級1級1級殘余奧氏體級別1級1級1級1級1級1級表面硬度61HRC60.5HRC60.5HRC61HRC61.5HRC61HRC從表2中可以看出,采用本發(fā)明的高合金滲碳鋼齒輪的淬火方法能有效細化表層馬氏體,減少殘余奧氏體含量,從而優(yōu)化齒輪表面的金相組織,同時提高其表面硬度、耐磨性、疲勞強度和塑韌性指標。當前第1頁1 2 3