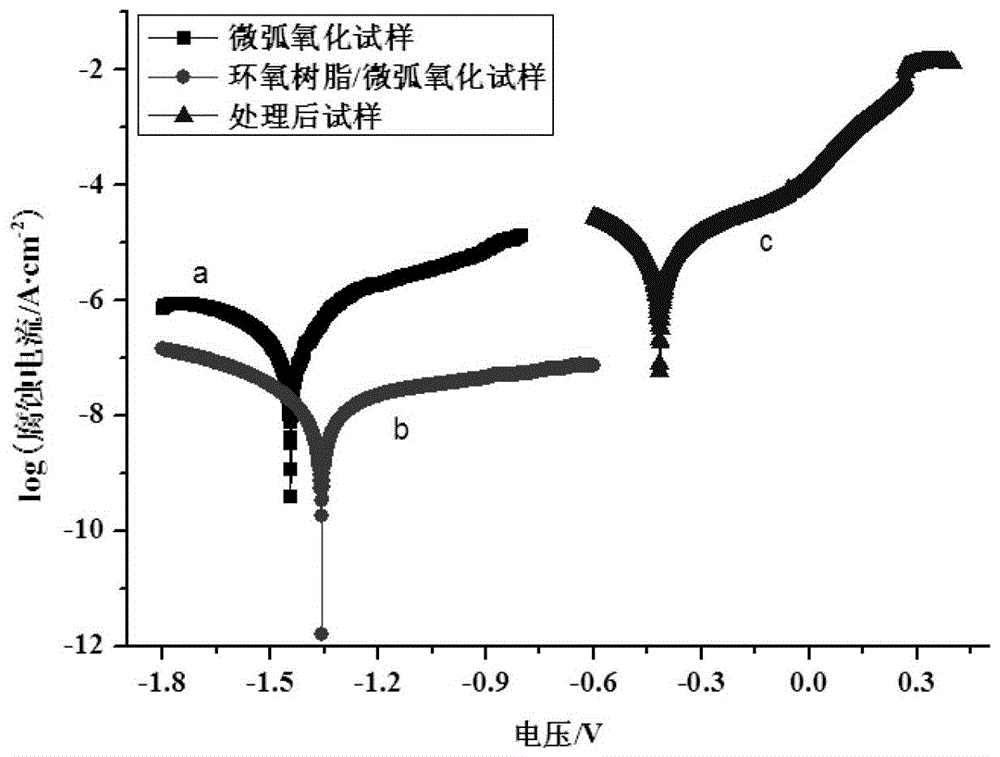
:本發(fā)明涉及到一種提高鎂合金表面耐腐蝕性能的前處理液及其處理方法。
背景技術(shù)::鎂合金是一種極輕的結(jié)構(gòu)材料,具有高的比強(qiáng)度、比剛度、減震性、可切削加工性和可回收性等特點(diǎn),被譽(yù)為21世紀(jì)的“綠色”金屬結(jié)構(gòu)材料。然而,鎂合金在潮濕的空氣或海洋大氣中均會(huì)遭受嚴(yán)重的腐蝕。因此,對(duì)其表面進(jìn)行防腐處理,提高耐腐蝕性能是鎂合金應(yīng)用需解決的一個(gè)重要問(wèn)題。目前,鎂合金表面防護(hù)處理方法主要有化學(xué)轉(zhuǎn)化、有機(jī)涂裝、陽(yáng)極氧化、微弧氧化、電鍍或化學(xué)鍍處理等方法。其中,陽(yáng)極氧化處理能顯著提高金屬的耐磨和耐蝕性能,同時(shí)還具有較強(qiáng)的吸附性,而在其基礎(chǔ)上發(fā)展起來(lái)的微弧氧化處理是一種在有色金屬表面原位生長(zhǎng)陶瓷層的新技術(shù),該陶瓷層與金屬基體結(jié)合力強(qiáng),具有較好的耐熱耐沖擊、耐磨損、耐腐蝕等特性,表面防護(hù)效果遠(yuǎn)高于傳統(tǒng)的表面處理方法。然而,無(wú)論是陽(yáng)極氧化膜還是微弧氧化膜,其表面都存在許多微孔或微裂紋,腐蝕介質(zhì)可以從這些微缺陷滲入基體,導(dǎo)致其耐蝕性下降。另外,由于其表面是一層氧化物膜,故試樣的導(dǎo)電性很差。針對(duì)鎂合金氧化膜的缺陷,主要采用沸水處理、溶膠-凝膠法、有機(jī)涂層技術(shù)、電鍍和化學(xué)鍍工藝對(duì)其進(jìn)行表面處理。沸水處理只能使孔口部分封閉變小,難以完全封閉微孔和微裂紋。溶膠-凝膠法處理工藝復(fù)雜,且較大顆粒的溶膠不易進(jìn)入膜孔。電鍍和化學(xué)鍍處理過(guò)程中,一般含有敏化工藝,其處理液中含有Sn2+離子,對(duì)環(huán)境污染嚴(yán)重,同時(shí)處理液中的酸根離子對(duì)氧化物膜腐蝕嚴(yán)重;另外,施鍍過(guò)程中,即使是堿性高pH值條件下的鍍液也能破壞表面氧化物,導(dǎo)致處理后試樣的耐蝕性大大降低。雖然國(guó)內(nèi)有許多文獻(xiàn)表明,直接在微弧氧化層表面鍍鎳能使試樣獲得很好的耐蝕性,但缺少長(zhǎng)時(shí)間的腐蝕試驗(yàn)。有機(jī)涂層技術(shù)方面,雖然試樣處理后其耐蝕性顯著提高,但其表面導(dǎo)電性能較差,且表面易被污染,使其使用受限。
技術(shù)實(shí)現(xiàn)要素::針對(duì)現(xiàn)有技術(shù)存在的問(wèn)題,本發(fā)明的目的在于結(jié)合微弧氧化膜或陽(yáng)極氧化膜、有機(jī)涂層技術(shù)和化學(xué)鍍鎳工藝的優(yōu)點(diǎn),提供一種提高鎂合金表面耐腐蝕性能的前處理液及其處理方法。一種提高鎂合金表面耐腐蝕性能的前處理液,在-10~35℃下將去離子水和氨丙基三乙氧基硅烷加入無(wú)水乙醇溶劑中,去離子水、氨丙基三乙氧基硅烷體積比為1:1,分別占溶液總體積的1~10%,室溫下水解5~120min。利用所述的前處理液對(duì)鎂合金進(jìn)行處理的方法,將涂有高分子有機(jī)涂層的微弧氧化或陽(yáng)極氧化的鎂合金經(jīng)除油和粗化處理后放入所述的前處理液中10s~10min,取出后吹干,在80~120℃條件下固化10~120min,然后再經(jīng)過(guò)活化和還原處理后放入化學(xué)鍍鎳液中進(jìn)行鍍鎳處理,制得提高鎂合金表面耐腐蝕性能且表面導(dǎo)電的復(fù)合涂層。所述的高分子有機(jī)涂層包括熱塑性樹(shù)脂或熱固性樹(shù)脂。本發(fā)明方法可使有機(jī)涂層填充到鎂合金氧化膜孔洞中使其封閉,并在氧化膜表面形成一層致密的有機(jī)涂層,顯著提高鎂合金的耐腐蝕性能。同時(shí),采用化學(xué)鍍的方法在有機(jī)涂層表面鍍敷一層鎳-磷合金,可使試樣表面具有金屬特性,具有較好的導(dǎo)電性。附圖說(shuō)明:圖1為微弧氧化AZ31鎂合金經(jīng)本發(fā)明處理后的表面形貌圖;圖2為AZ31鎂合金在3.5%氯化鈉溶液中的極化曲線圖,a為微弧氧化樣品,b為涂有環(huán)氧樹(shù)脂涂層的微弧氧化樣品,c為本發(fā)明處理后樣品;圖3為微弧氧化AZ31鎂合金在3.5%氯化鈉溶液中的交流阻抗譜;圖4為涂有環(huán)氧樹(shù)脂的微弧氧化AZ31鎂合金在3.5%氯化鈉溶液中的交流阻抗譜;圖5為微弧氧化AZ31鎂合金經(jīng)本發(fā)明處理后在3.5%氯化鈉溶液中的交流阻抗譜;圖6為微弧氧化AZ31鎂合金本發(fā)明處理前后的室溫浸泡腐蝕照片;具體實(shí)施方式:以下結(jié)合實(shí)施例旨在進(jìn)一步說(shuō)明本發(fā)明,而非限制本發(fā)明。實(shí)施例11.在室溫下將環(huán)氧樹(shù)脂涂料和相應(yīng)的固化劑及稀釋劑混合均勻,其中,環(huán)氧樹(shù)脂涂料、固化劑和稀釋劑的體積比為5:1:2。2.處理方法:將微弧氧化處理過(guò)的AZ31鎂合金用丙酮進(jìn)行超聲波清洗,吹干,將預(yù)處理過(guò)后的樣品浸入環(huán)氧樹(shù)脂溶液,2min后取出晾干,在室溫下固化24h;將固化好的試樣經(jīng)除油(氫氧化鈉20g/L,碳酸鈉30g/L,磷酸鈉30g/L,60℃,30min)和粗化(氫氧化鈉12~15mol/L,65~75℃,30min)處理后放入本發(fā)明的處理液中,該處理液的配制過(guò)程為:在-10~35℃下將去離子水和氨丙基三乙氧基硅烷加入無(wú)水乙醇溶劑中,去離子水、氨丙基三乙氧基硅烷體積比為1:1,分別占溶液總體積的5%,室溫下水解5~120min。體積比為5%的氨丙基三乙氧基硅烷溶液中1min,取出后吹干,在100℃條件下固化30min,然后再經(jīng)過(guò)活化和還原處理后放入化學(xué)鍍鎳液中進(jìn)行鍍鎳處理20min后取出,用去離子水清洗干凈并吹干。將經(jīng)過(guò)上述工藝處理的AZ31鎂合金樣品進(jìn)行以下實(shí)驗(yàn):1.掃描電鏡形貌:如圖1所示,微弧氧化AZ31鎂合金樣品經(jīng)本發(fā)明處理后,表面由許多菜花狀的鎳胞組成,鎳胞間結(jié)合緊密,看不出明顯的缺陷。2.動(dòng)電位極化曲線測(cè)試:如圖2所示,涂覆環(huán)氧樹(shù)脂后,試樣的自腐蝕電流密度降低一個(gè)數(shù)量級(jí),腐蝕電位降低87mV,本發(fā)明處理后,樣品腐蝕電位正移了1028mV。3.電化學(xué)交流阻抗譜:如圖3、圖4和圖5所示,AZ31鎂合金在經(jīng)本發(fā)明處理后,阻抗值下降的速率明顯降低,微弧氧化樣品在經(jīng)過(guò)96h浸泡后阻抗值下降至102Ωcm2,涂有環(huán)氧樹(shù)脂的微弧氧化樣品浸泡1032h后阻抗值降至103Ωcm2,而經(jīng)本發(fā)明處理后樣品浸泡1368h后阻抗值仍然處于103Ωcm2以上。4.室溫鹽水浸泡實(shí)驗(yàn):如圖6所示,未處理的微弧氧化樣品在浸泡144h后,表面便堆積了大量的腐蝕產(chǎn)物,并有若干腐蝕點(diǎn)出現(xiàn),浸泡至240h時(shí),試樣腐蝕進(jìn)一步加劇,腐蝕產(chǎn)物比之前更多,原先的腐蝕點(diǎn)處已被腐蝕介質(zhì)腐蝕穿;涂覆環(huán)氧樹(shù)脂后,試樣浸泡816h才出現(xiàn)腐蝕點(diǎn),浸泡1032h后腐蝕點(diǎn)變大;與之相比,本發(fā)明處理后的樣品在浸泡初期幾乎沒(méi)有任何變化,只是鍍層表面顏色稍微變暗,浸泡至1224h時(shí),有少許氣泡從試樣表面冒出,表面出現(xiàn)一個(gè)肉眼可見(jiàn)的鼓泡,且當(dāng)浸泡進(jìn)行到1368h時(shí),腐蝕點(diǎn)的數(shù)量也沒(méi)有增加。